如何为多相电源系统设计热平衡均流系统

每月为您发送最具参考价值的行业文章
我们会保障您的隐私
简介
未来的汽车将车轮上的视听仙境,它将配备环绕式的屏幕和数十个扬声器。即使在行驶中,车辆也可以通过超高速 5G 传输视听内容,乘客可以沉浸在令人难以置信的感官体验之中。为了实现这种内容丰富、高度连接的未来移动范式,新兴的数字驾驶舱系统对计算能力的需求也呈指数级增长。这种增长导致了对功率的更高要求。
交错式拓扑越来越受欢迎,因为这种拓扑不仅可以提供更高的负载电流,还能改善 EMC。但是,在设计这种汽车电源管理系统时,工程师必须在散热、电路板尺寸和成本之间权衡利弊。尤其重要的是,相位之间需要实现最佳电流分配,以避免某个相位的 MOSFET 过热,从而导致整个系统性能的下降。
本文提出了一种新颖的高性价比方法,通过两颗降压控制器的多相控制,实现了电池直接供电的大功率电源管理方案。该解决方案将一个简单而有效的热平衡电路与两个交错式MPQ2908A-AEC1器件(4V 至 60V 输入、电流模式、同步降压控制器)相结合,有效改善了相间电流分配,同时还巧妙解决了实现更高功率的难题。
功率级
随着新型汽车设计的功率需求不断上升,电力电子工程师也面临更多的挑战。他们需要在不增加 PCB 尺寸和成本的条件下设计出功率更高的电路,同时必须保持低于规定值的低 EMI。
多相拓扑提供了一种简单的解决方案来克服这一设计挑战。在这种拓扑中,多个电源变换器并联放置以增加整个电源单元 (PSU) 的可用负载电流,从而增加可输送的功率总量。与此同时,如果所有变换器彼此同步运行但锁定相位不同,则整个系统产生的 EMI 也会降低。最终,负载所需的电流由所有变换器分担,散热性能得到优化。
本文介绍的汽车电源管理系统即采用双相电源,它可以将新型汽车设计中常见的 48V电源降至12V,以满足许多高级驾驶辅助系统 (ADAS) 的需求。为了提供高达20A 的负载电流,该设计使用了两个 MPQ2908A-AEC1 器件。这款控制器除了具备宽输入范围并可实现48V 规格降压以外,还可以利用其SYNCO 引脚构建双相拓扑,输出 180° 异相时钟。
图 1 显示了一个初始 240W 功率级的系统框图。首先,系统中包含48V的汽车电池。它还包含反极性保护和过压保护 (OVP) 子系统,用于在出现意外事件(例如错误连接电缆)时保护系统免受损坏。最后,系统还包含用于减少传导发射的EMC 滤波器,以及用于将电压从 48V 降至 12V的双相交错式降压变换器。由于系统管理的功率相当高,因此还添加了一个频谱扩展 (FSS) 调制器以实现整个系统中的低 EMI。
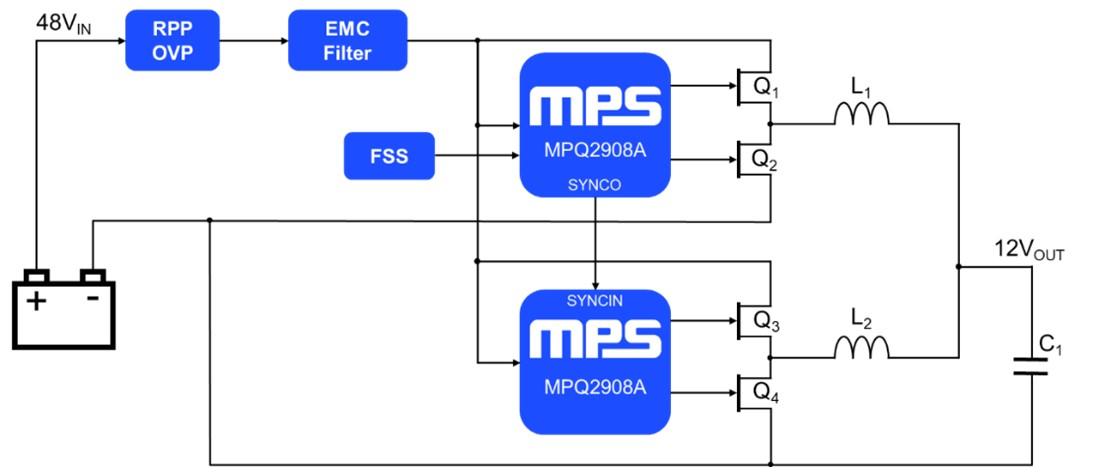
图1: 初始240W功率级
设计挑战与解决方案
汽车行业不断增长的电力需求使设计人员面临两项关键的设计挑战。首先,汽车应用的电源必须满足标准化EMC 要求,例如 CISPR 25 Class 5。这意味着 PCB 布局应涵盖所有 EMC 设计建议。此外,为确保 240W 系统能够保持在规定的 EMC 限制范围内,还需添加特定的补充解决方案,如交错式拓扑、EMC 滤波器和 FSS 调制器。
与此同时,设计方案还需要管理电路板热量。我们建议通过选择合适的电路元件来实现系统的高效率。提高效率可以减少功率损耗,从而最大限度地减少温升。设计人员尤其应谨慎选择系统中的 MOSFET 和电感。
图 2 所示为初始 240W 功率级在四种不同输入电压(24V、36V、48V 和 60V)下的效率。
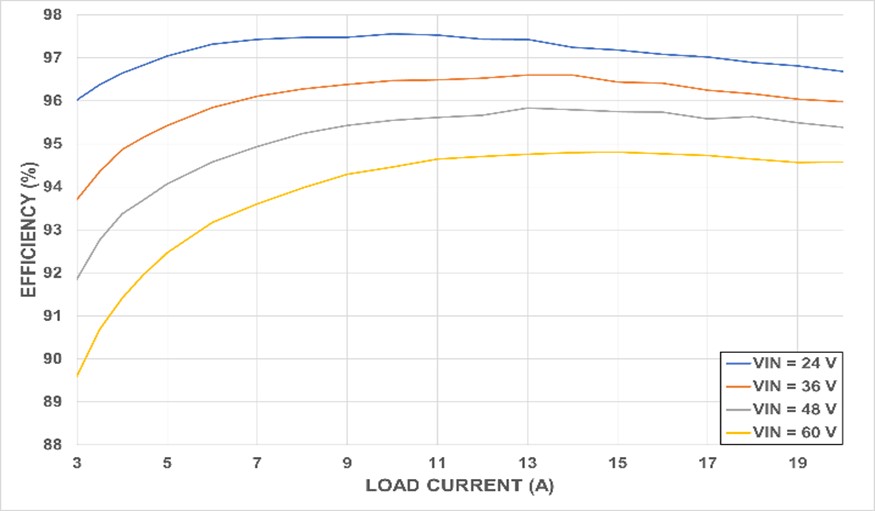
图2: 系统效率
除了选择最佳组件之外,还有其他方法也可以改善汽车电源管理系统的散热性能。例如,采用 MPQ2908A-AEC1 允许设计人员选择变换器的开关频率(fSW)。通常,fSW 应尽可能地低以减少开关损耗。较低频率可提高效率,同时避免电路板过热。在本文的示例中,fSW 设置为 225kHz。较高EMI 峰值位于 450kHz (2 x fSW) 处,这减少了开关损耗而且不会影响 EMC性能。
除了散热和 EMC 限制以外,交错式拓扑通常还需要均匀的热分布以平衡 MOSFET的退化,并防止电路板的某些部分过热。为了解决这个问题,合理布局PCB 并优化两个控制器之间的电流分配至关重要。采用最佳均流方案可以使负载电流在系统所有变换器之间均匀分配,从而使所有 MOSFET 都具有相同的温升。
假设一个系统没有考虑散热均衡。在系统负载电流为 20A 且处于稳态时,每相平均电流之间将存在 1A 的差异(如图 3 中的浅蓝色和绿色迹线所示),这将导致相位之间的温度不平衡。如果相位之间存在次优的热分布(相位温度如图 3 中的深蓝色和粉色迹线所示),则温度较高的相位会更快退化。
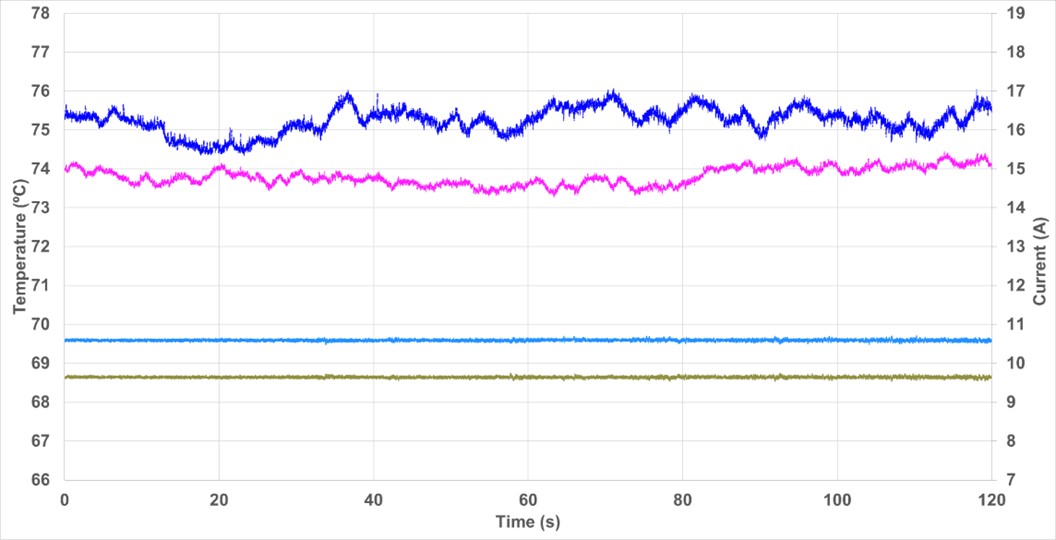
图 3:没有热平衡的系统电流分配
热平衡系统
本文提供了一种简单易行的电路设计,它通过精确的温度感测来均衡相间温度。我们将该电路与初始240W系统合并,然后检测并比较两相的温度。如图4可见,每个变换器提供的负载电流都有相应改变。
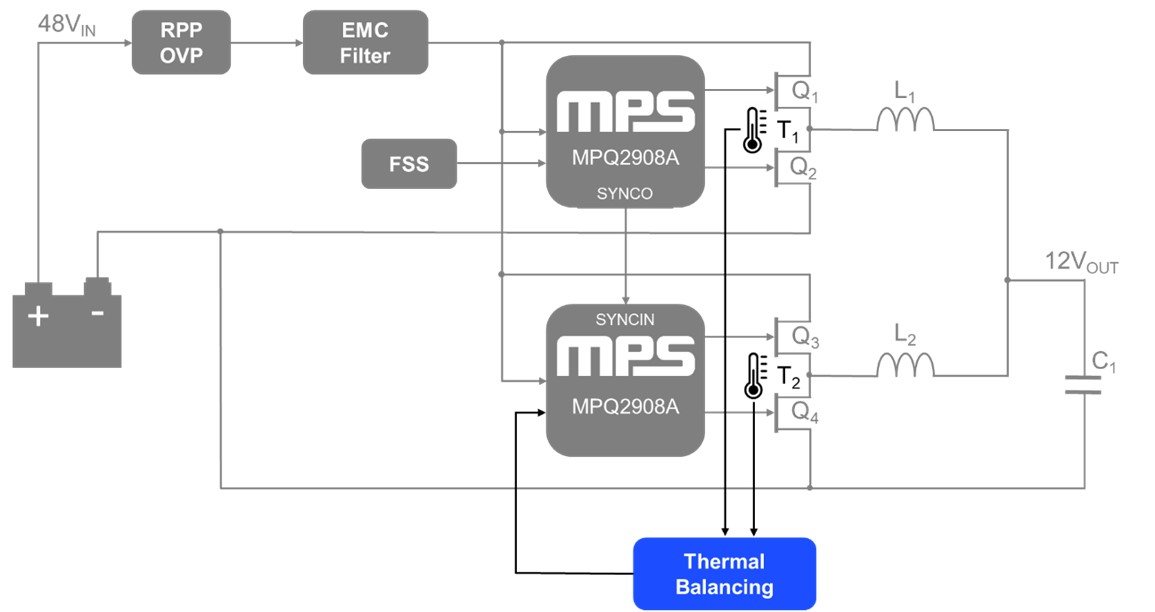
图 4:带热平衡系统的 240W 功率级
例如,如果 T1 > T2,热平衡系统会修改相 2 的补偿信号以提高其输出电压 (VOUT2)。由于总输出电流由负载决定,是不变的,所以相 2 的电流(IPHASE2) 增加而相 1 的电流 (IPHASE1) 减小。因此,相 1 的功耗和温度会降低,直到 T1 = T2。
另外,该电路还降低了 BOM 成本并最大限度地减小了 MOSFET 和电感的尺寸。如果两相之间的电流分配不均,设计人员就必须采用物理尺寸更大的电路元件,如 MOSFET 和电感,以承受电流测量容差引起的较大电流和功率。而当相间电流分配均匀时,就可以使用尺寸更小的 MOSFET 和电感,从而优化设计,并降低 BOM 成本。
在该电路中,两相的温度通过两个负温度系数 (NTC) 热敏电阻检测。然后温差被馈送到比例积分 (PI) 控制电路,由该电路将信号输出到相 2 的补偿 (COMP) 引脚。如果 T2 < T1,则相2 COMP 引脚上的电压将随电流的增加而增大(反之,当 T2 > T1时亦然)。
相1并未连接到热平衡电路上。输出电流 (ILOAD) 是两相电流的组合 (IPHASE1 + IPHASE2),它由负载设置,并与相电流分布无关,如公式 (1) 所示:
$$I_{LOAD} = I_{PHASE1} + I_{PHASE2}$$当 IPHASE2由于热平衡控制而减小,IPHASE1 会自动增大(反之亦然)。因此,尽管相 1并没有直接连接到热平衡电路上,但仍受其影响。
图 5 所示为热平衡设计原理图。
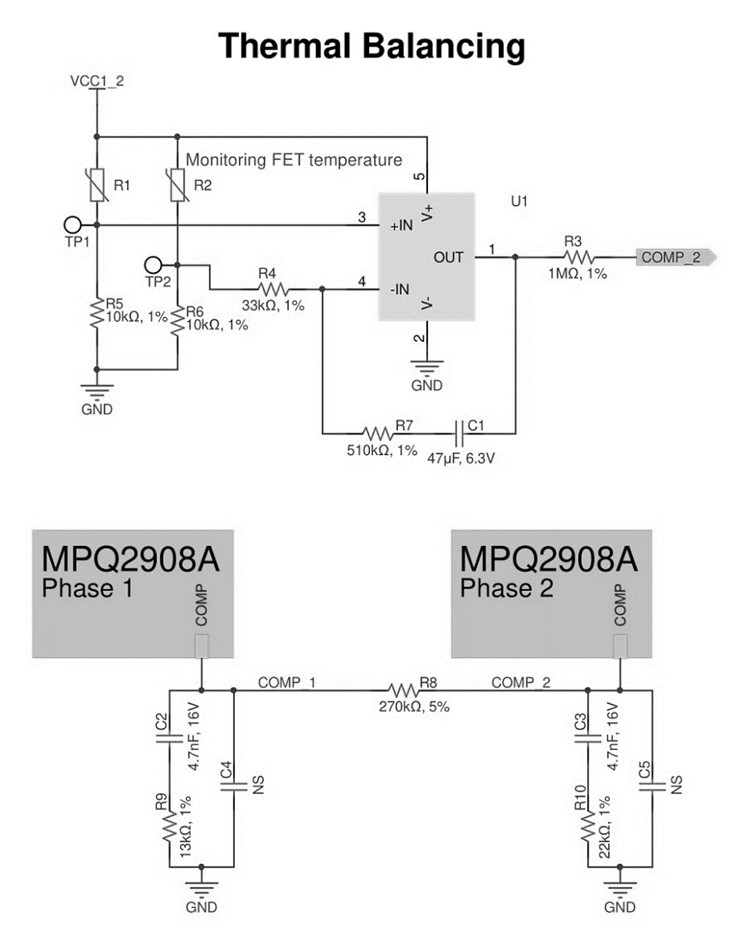
图 5:热平衡设计原理图
放置在相 1 和相 2 的 COMP 引脚之间的电阻器 (R8) 用于确保两相之间的电流差不会达到临界或危险水平。我们通过实验可确定 270kΩ 为 R8 的最佳值。
简化后的电路只需正确选择 PI 电路元件的尺寸即可实现温度控制。PI 电路传递函数(H(s))如公式(2) 所示:
$$H(S) = \frac {V_{OUT}(s)} {V_{IN}(s)} = - (\frac {R_7}{R_4} + \frac {1}{R_4 \times C_1 \times s})$$其中 C1、R4和 R7 都是 PI 补偿环路中的元件。
PI 电路的比例增益 (KP) 可通过公式 (3) 来计算:
$$K_P = \frac {R_7}{R_4}$$PI 电路的积分增益 (KI) 可通过公式 (4) 来计算:
$$K_I = \frac {1}{R_4 \times C_1}$$测试结果
采用热平衡系统可以使电流均衡和温度均衡都得到明显改善,图 3 中显示的2°C温差可降至 0.5°C 以下(如图 6 中的深蓝色和粉色迹线所示)。
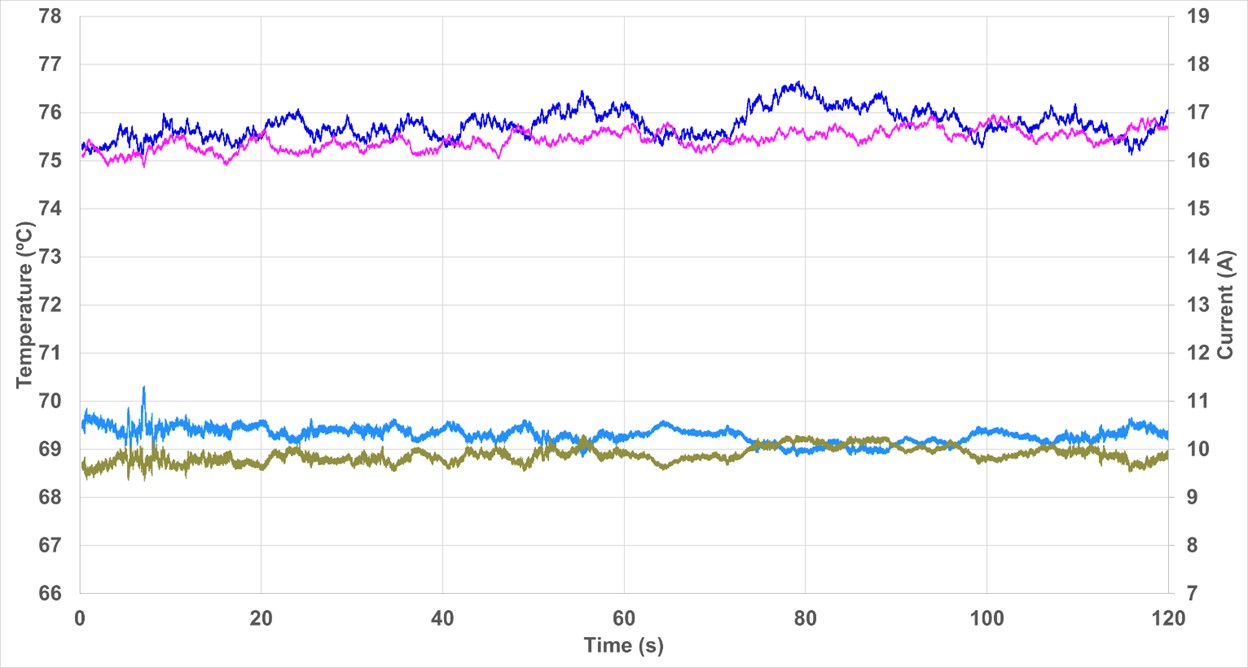
图 6:采用热平衡系统后的均流效果
结语
新型汽车设计均采用 48V 电源管理系统,以减轻车辆线束的重量以及功率损耗。为了承担更高负载,采用交错式拓扑对于提高所需功率非常重要。
采用交错式拓扑需要实现均匀的热分布,以平衡 MOSFET 的退化。本文介绍的方案结合MPQ2908A-AEC1实现了一种简单易行的热平衡电路,它改善了多相设计中的电流分配和温度分布,可满足EMC 标准,如 CISPR 25 Class 5。采用现有常用元器件,多相变换器相位之间的温差可以从 2°C 有效降低至 0.5°C。
_______________________
您感兴趣吗?点击订阅,我们将每月为您发送最具价值的资讯!
直接登录
创建新帐号