Introduction and Principle of Operation
The Single-Ended Primary Inductor Converter (SEPIC), a flexible and effective DC-DC converter topology, can step-up and step-down the input voltage, making it the perfect option for applications with different input voltage needs. The SEPIC converter's distinctive qualities, such as its capacity to deliver a non-inverted output voltage and uphold minimal input and output ripple, make it ideal for a variety of uses, including battery-powered and renewable energy systems as well as automotive electronics.
The SEPIC converter's fundamental working theory depends on the energy transfer between two inductors and a capacitor. Two inductors (L1 and L2) and a capacitor (C1) are connected to provide an intermediate energy storage stage in a SEPIC converter. The coupled inductors and capacitors in this configuration enable the converter to transfer energy from the input to the output. In contrast, the output voltage is controlled by the switching component (often a MOSFET) and output capacitor.
During the on-state of the switch, the energy is stored in both inductors, and the capacitor is charged. The inductors’ stored energy is transmitted to the output capacitor and the load when the switch is in the off position. The output voltage is regulated as a result of this continual energy transfer process, and depending on the duty cycle of the switch, it may be either greater or lower than the input voltage.
The SEPIC converter is a useful addition to the spectrum of existing DC-DC converter topologies because it can step-up and step-down the input voltage while maintaining a non-inverted output voltage.
Circuit Topology and Key Components
By swapping the position of diode D and inductor L2 in the Ćuk converter, the SEPIC (Single Ended Primary Inductance Converter) topology of the converter is obtained, as shown in Figure 16. This ensures that the negative pole of the power source and the negative pole of the load voltage are connected at a common point in the converter.
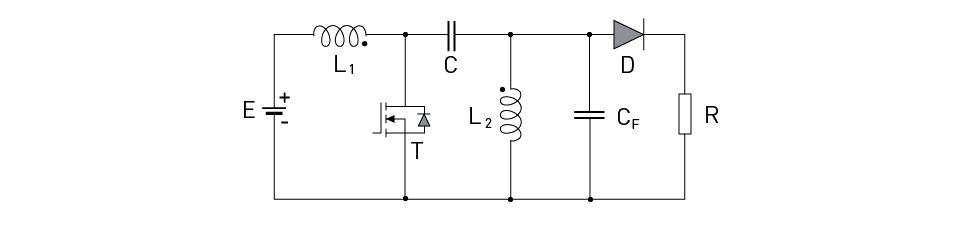
Figure 16: The SEPIC converter circuit diagram
In steady-state, the average voltage across the inductors is zero, so the average voltage across the capacitor is equal to the DC voltage source. The capacitance of the capacitor can be considered sufficiently large to neglect the AC component of the voltage across it. Figure 17 shows the equivalent circuit of the SEPIC converter during the t_ON period. During this period, the voltages across the inductors L1 and L2 are:
$$V_{L1} = -E$$ $$V_{L2} = -V_C = -E$$so that their currents linearly increase and the load is supplied with energy from the capacitor Cf.
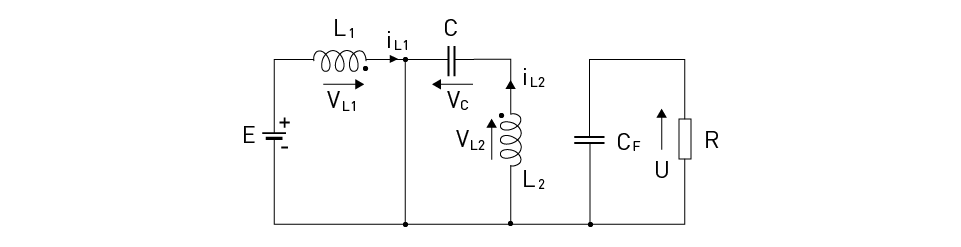
Figure 17: The SEPIC converter circuit diagram – interval tON
The equivalent circuit of the SEPIC converter in the tOFF period is shown in Figure 18. In this period, the voltages on the inductors L1 and L2 are:
$$V_{L2} = U$$ $$V_{L1} = U + V_C - E = U$$so that their currents linearly decrease and their sum flows through the diode towards the load, where a part of the energy is consumed by the load and another part is stored in the capacitor Cf.
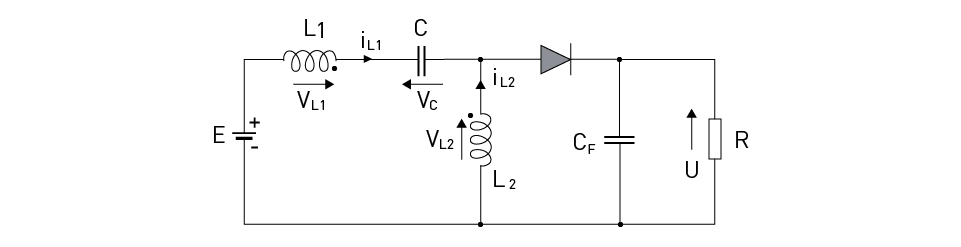
Figure 18: The SEPIC converter circuit diagram – interval tOFF
In steady state, the average voltage value on the inductor is equal to zero, so from Figure 19 it follows:
$$E \cdot T \cdot d = U \cdot T \cdot (1 - d)$$ $$U = E \cdot \frac{d}{1 - d}$$which means that this converter operates as a buck-boost converter.
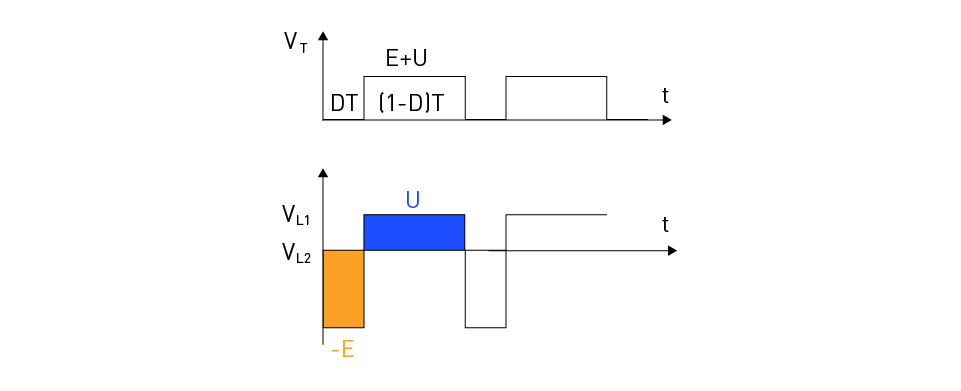
Figure 19: The SEPIC converter – the voltage across inductors L1 and L2
The SEPIC converter's unique topology is characterized by its specific arrangement of inductors, capacitors, switching elements, and diodes. The key components in a SEPIC converter are:
- Input and output capacitors (Cin and Cout): These capacitors filter the input and output voltage, minimizing voltage ripple and ensuring stable operation.
- Coupling capacitor (C1): This capacitor connects the two inductors, L1 and L2, and plays a critical role in transferring energy between the inductors during the switching process.
- Inductors (L1 and L2): These inductors store energy during the on-state of the switch and release it to the output during the off-state. They are crucial in maintaining continuous energy transfer and regulating the output voltage.
- Switching element (S): Typically a MOSFET, this component controls the energy transfer process by switching on and off at a specific duty cycle, which determines the output voltage.
- Diode (D): This component provides a path for current to flow during the off-state of the switch, ensuring energy transfer from the inductors to the output capacitor and load.
- Controller (not shown in the topology): A pulse-width modulation (PWM) controller or similar control circuitry is used to regulate the duty cycle of the switching element, maintaining a stable output voltage regardless of variations in the input voltage or load conditions.
With the crucial distinction of the coupling capacitor C1, the SEPIC converter topology can be viewed as combining buck converters with boost converters. This capacitor creates a special energy transfer path that enables the converter to perform both step-up and step-down functions without inverting the output voltage. The careful design and selection of these essential parts, which guarantees the converter's best performance and efficiency, are essential to its operation.
Continuous and Discontinuous Conduction Modes
In SEPIC converters, the inductor current flow is the primary factor determining the converter's conduction mode. There are two primary modes of operation: continuous conduction mode (CCM) and discontinuous conduction mode (DCM). The converter's mode of operation significantly impacts its performance, efficiency, and design considerations.
Continuous Conduction Mode (CCM): During the switching cycle in CCM, the current flowing through the inductors L1 and L2 never stops and never reaches zero. This mode runs when there is a high demand for the load, and the converter uses a greater duty cycle. Due to its lower output voltage ripple, decreased current stress on components, and improved transient response, CCM is typically preferred. The primary disadvantage of CCM is the complexity of the control circuitry, which must be controlled more precisely to maintain the appropriate output voltage. Additionally, when operating in CCM, the converter's efficiency tends to be lower under light loads since the switching losses are more pronounced.
Discontinuous Conduction Mode (DCM): In DCM, energy is intermittently transferred to the output because the inductor current goes to zero for a portion of the switching cycle. This mode often happens when the load demand is minimal and the converter is operating at a lower duty cycle. DCM has a few benefits, such as less complicated control circuitry and improved efficiency at light loads because of lower switching losses. However, compared to CCM, DCM also exhibits poorer transient responsiveness, higher output voltage ripple, and increased current stress on components.
In conclusion, the individual application requirements, including load circumstances, efficiency goals, and design limits, will determine whether CCM or DCM should be used. Depending on the load conditions, a SEPIC converter may occasionally be built to run in a quasi-continuous conduction mode (QCCM), which combines the benefits of both CCM and DCM. To get the best performance and efficiency while constructing a SEPIC converter, it is essential to understand the trade-offs between various conduction modes.
Design Considerations and Calculations
Designing a SEPIC converter requires careful consideration of various factors such as input voltage, output voltage, load current, switching frequency, and component selection. The following design steps outline the process for designing a SEPIC converter:
- Determine the required output voltage (V_out) and load current (I_out) based on the application requirements.
- Choose an appropriate input voltage range (V_in) within which the converter will operate.
- Select the desired switching frequency (f_sw) for the converter. Higher frequencies result in smaller inductor and capacitor sizes, reducing the overall size of the converter. However, higher frequencies also increase switching losses, which can reduce efficiency. The choice of switching frequency depends on the trade-off between size and efficiency.
- Calculate the duty cycle (D) required to achieve the desired output voltage using the following equation: $$D = \frac{V_{out}}{V_{in} + V_{out}}$$ $$\Leftrightarrow V_{out} = V_{in} \cdot \frac{d}{1 - d}$$ $$\Leftrightarrow V_{out} \cdot (1 - d) = V_{in} \cdot d$$ $$\Leftrightarrow V_{out} - V_{out} \cdot d = V_{in} \cdot d$$ $$\Leftrightarrow d = \frac{V_{out}}{V_{in} + V_{out}}$$
- Choose suitable inductance values for the coupled inductors L1 and L2. The selection should be based on the desired ripple current, the inductor's saturation current, and the converter's efficiency requirements. A common guideline is to choose the inductor value so that the peak-to-peak ripple current is 20-40% of the load current.
- Calculate the capacitance value for the input capacitor (C_in), output capacitor (C_out), and a coupling capacitor (C_c). The choice of capacitance values depends on the desired input and output voltage ripple and the converter's transient response requirements.
- Select a suitable switching element with appropriate voltage and current ratings, such as a MOSFET or IGBT. Ensure the selected device can handle the maximum current and voltage stresses experienced during operation. To improve efficiency, the switching element should also have low conduction and switching losses.
- Design the control circuitry to regulate the output voltage. Various control techniques can be employed, including voltage mode control, current mode control, and average current mode control. The choice of control technique depends on the desired performance, complexity, and stability requirements.
- Evaluate the converter's performance through simulation and prototyping. Verify that the converter meets the desired specifications, such as output voltage regulation, efficiency, and transient response. Make any necessary adjustments to the design based on the results.
Efficiency and Losses
Efficiency plays a key role in power converter design since it has a direct impact on a system's functionality, thermal management, and cost. The efficiency of SEPIC converters is determined by a variety of elements, including the converter's topology, the environment in which it operates, and the components that are used. This section discusses the primary sources of losses in SEPIC converters and provides guidelines for improving efficiency.
Conduction losses: Conduction losses primarily occur in the switching element, inductors, and diodes due to the resistive elements within these components. To minimize conduction losses, it is essential to select components with low series resistance. For example, choosing a MOSFET with low on-state resistance (R_DS(on)) and diodes with low forward voltage drops (V_F) can significantly reduce conduction losses.
Switching losses: Switching losses are a result of the switching element's movement between the on and off states, and they can cause energy to be lost as heat. The total switching is influenced by the switching frequency, voltage, transitional current stresses, and properties of the switching device. Choose a switching device with quick switching times and low capacitance to reduce switching losses, and think about enhancing the gate drive circuitry for quick transitions.
Core losses: As a result of the alternating magnetic fields produced during operation, core losses happen in the magnetic cores of inductors. The core material, operating frequency, and magnetic flux density inside the core all affect these losses. To minimize core losses, select a suitable core material with low-loss characteristics and ensure that the inductor operates within the specified range of the core material.
Capacitor losses: Equivalent series resistance (ESR) and dielectric losses within the capacitor are the main causes of capacitor losses. Select a dielectric material with low loss properties and capacitors with low ESR and high ripple current ratings to reduce these losses.
Control circuitry losses: The power used by the control IC and auxiliary parts that govern the converter's output is referred to as "control circuitry losses." Use energy-efficient control ICs to reduce the control circuitry's quiescent current consumption to reduce control circuitry losses.
Leakage inductance losses: Coupled inductors naturally have leakage inductance, and the losses that go along with them can diminish efficiency. These losses can be reduced by reducing the leakage inductance in the inductor design and using the proper compensatory strategies.
Engineers can obtain high efficiency in SEPIC converters by addressing these loss processes and enhancing the converter's design, enabling more compact, dependable, and economical power conversion solutions for varied applications.
Applications and Examples
SEPIC (Single-Ended Primary Inductor Converter) converters are versatile power conversion devices that can step-up, step-down, or maintain the input voltage, making them suitable for a wide range of applications. This section highlights some key applications and provides examples where SEPIC converters have proven advantageous.
Battery-powered systems: SEPIC converters are best suited for battery-powered devices with variable battery voltage, such as portable gadgets and electric cars. In these situations, the converter provides a constant output voltage despite a changing input voltage, improving the efficiency and dependability of the entire system.
Example: A portable medical device requires a stable 12V output from a 7.4V lithium-ion battery. As the battery discharges, its voltage may drop to 6V, but the SEPIC converter ensures that the device continues to receive a constant 12V supply.
Solar energy systems: In solar applications, such as photovoltaic (PV) panels and solar charge controllers, the input voltage can vary significantly due to changes in sunlight intensity and temperature. SEPIC converters can efficiently regulate the output voltage under these varying conditions, maximizing energy harvest and improving system efficiency.
Example: A solar-powered streetlight system uses a SEPIC converter to regulate the voltage from the PV panel to charge a battery and power an LED lamp, ensuring consistent performance under varying sunlight conditions.
Industrial and automotive systems: SEPIC converters are appropriate for industrial and automotive systems that need precise voltage regulation under a range of input voltage situations, such as unstable power networks or variable battery voltages. Additionally, they can offer galvanic isolation in delicate applications.
Example: In an electric vehicle charging station, a SEPIC converter can be used to step up the power grid's input voltage, enabling high-voltage battery packs with minimal losses and high efficiency.
LED lights: SEPIC converters are frequently employed in LED lighting applications to deliver a constant current output, ensuring steady brightness over a broad range of input voltages. They are especially helpful in this situation because they can handle both step-up and step-down voltage conversion.
Example: In an architectural lighting system, a SEPIC converter provides a constant current to a series of LEDs, ensuring uniform brightness despite variations in the input voltage from the power supply.
Communication systems: SEPIC converters can supply steady power supplies for delicate devices like transceivers, modems, and base stations in communication systems. They can efficiently manage fluctuating input voltages while maintaining a consistent output for critical system components.
Example: In a remote cellular base station, a SEPIC converter steps down the input voltage from a solar panel or a fuel cell to provide a stable power supply for the communication equipment, ensuring uninterrupted operation
直接登录
创建新帐号