使用数字多相控制器为数据中心提供支持

每月为您发送最具参考价值的行业文章
我们会保障您的隐私
介绍
2020 年 9 月 - T服务的爆炸式增长正在推动着数据中心、网络和电信设备的重大发展。而创新需求也对处理这些日益增多的数据的服务器、存储和网络交换机产生了一定的影响。在此推动下,基础设施设备的处理能力和带宽都达到了极限。对于电源设计人员来说,他们面对的主要挑战是如何使用最少的电力高效地为数据中心设备供电,并提高它们的散热性能。而针对先进的 CPU/ASIC 和 FPGA 时,设计人员还必须平衡好功耗与散热性能。
多相解决方案改善了数据中心的效率和尺寸
随着终端系统功能的增多,处理功率也相应提高,以满足新的数据中心设计要求。这种高处理能力需求主要集中在数据中心应用中,数字中心采用高端 CPU/ASIC 和处理器来运行服务器、存储和网络设备。服务器和网络设备则通过电信设备分布至网络,然后通过 CPU/ASIC 和 FPGA 的销售点设备、台式电脑和嵌入式计算系统进行工作。
在上述示例中,CPU/ASIC 和处理器具有相似的数字处理需求,以及相似的功率分布。虽然如今处理器的尺寸不断缩小,但它们采用了更多的晶体管,因此需要更高的输出电流,范围一般在 100A 至 500A 之间,甚至更高,具体由其复杂程度决定。 该行业通过在数字负载中集成低功率状态来调整这种情况。此举使得设备能在空闲时以更低电流运行,在需要时再按全功率运行。这有利于控制整个系统的功率预算,但会给全功率端的电源设计人员带来另一项挑战。首先,数据中心电源必须对需要在不到 1 微秒的时间内实现超过 100A 的大阶跃载荷做出响应,同时还需保持很窄的输出调整率。其次,必须小心可靠地管理散热性能,才能继续保持全功率范围。
多相电压调节器模块(VRM)可以解决这些挑战。VRM 提供电源转换,一般是从 12V 输入转换至 1V(或更低)输出。 要提供如此大的负载电流,更简单的方法是设计一个多相解决方案,将负载分配给多个更小的功率级(所谓的相),而不是尝试使用单相来提供。在设计电磁和功率级,以及要从功耗的角度解决散热问题时,想要通过单相提供太多电流是一项巨大的挑战。相比通过单相提供大电流,多相解决方案则具有高效率、小尺寸和低成本等特点。这与多核 CPU 类似,该 CPU 会拆分末端负载的工作负载。
对电源数据中心的数字控制
几十年来,人们一直将模拟控制作为值得信赖的方法和电源系统解决方案。但是,在涉及大电流和高功率应用时,模拟控制存在一定的缺陷。对于高端电源解决方案,电源系统需要更加智能化并能集成到整个解决方案中,且电源解决方案和主 CPU/ASIC 之间的通信应该是一项硬性设计要求。
因此,数字控制解决方案非常适合数据中心应用。 为帮助理解,我们以 MPS 的 MP2888A 为例,这是一款数字多相控制器,可以替代传统的模拟控制器。MP2888A 是一款具有 PMBus 和 PWM-VID 接口的 10 相数字多相控制器 (参见表 1).
MP2888A | 传统的模拟控制器 | |
通信协议 | PWM-VID 和 PMBus | PWM-VID |
最大相位数量 | 10 | 最多 8 个 |
遥测 | 是 | 否 |
故障处理 | 是,寄存器设置 | 需要额外的 IC 或外部部件 |
封装 | QFN (5mmx5mm) | QFN (5mmx5mm) |
表 1: MPS 数字控制器对比传统模拟控制器
由于采用数字控制技术,仅需在封装中配置一个单独的引脚,MP2888A便可支持PWM-VID。 如果是采用模拟控制器,想要实现相同的功能,一般需要使用 4个 引脚并需要额外添加7 个以上高精度外部元器件 (参见图 1). 虽然高精度元器件提升了设备功能,但它们也增加了整体方案成本。
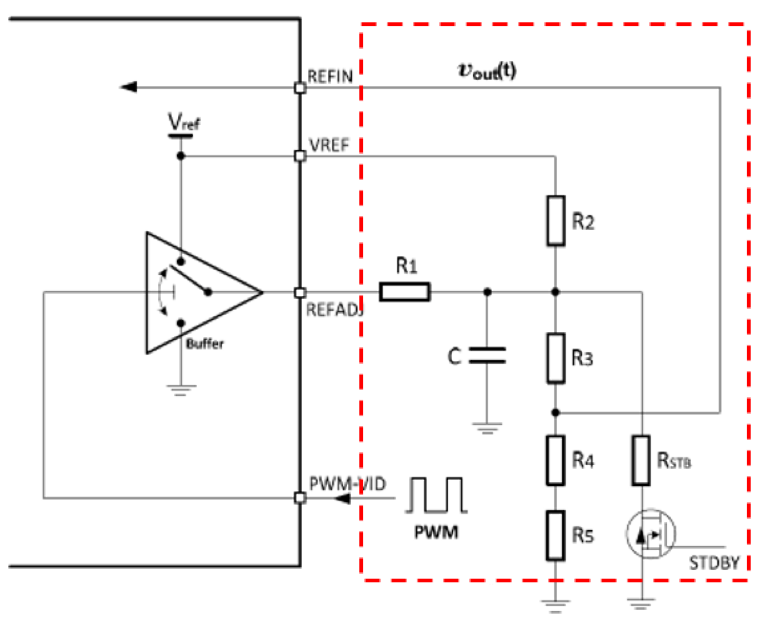
a) 支持PWM-VID 和 REFIN 的模拟控制器方案电路
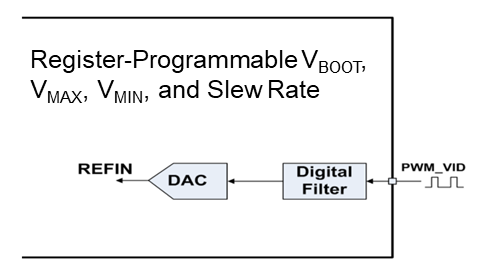
b) 支持PWM-VID 和 REFIN 的,集成可编程寄存器MP2888A方案电路
图1:支持PWM-VID(模拟控制器对比数字控制器)
传统的模拟控制器需要采用 RC 电路来构建反馈补偿环路。要优化补偿回路,需要进行多次迭代来计算外部部件的正确值从而满足多种工作条件。在测试和重新测试系统之前,工程师还必须更改这些部件。数字控制解决方案避免了潜在的重复劳动,使系统微调变得更加容易。
因为具有自动环路补偿功能,数字控制解决方案无需使用任何外部元器件,且可以通过使用 PMBus 调整寄存器设置来轻松完成微调。还可以使用一个寄存器来正确设置公差范围,由此轻松完成负载-线性校准——在超频期间,此功能非常有用,可以帮助稳定 CPU/ASIC。与数字控制器相比,模拟控制器需要使用14 个以上外部部件来进行环路补偿和负载-线性校准(参见图 2)。 模拟控制器。 (参见图2).
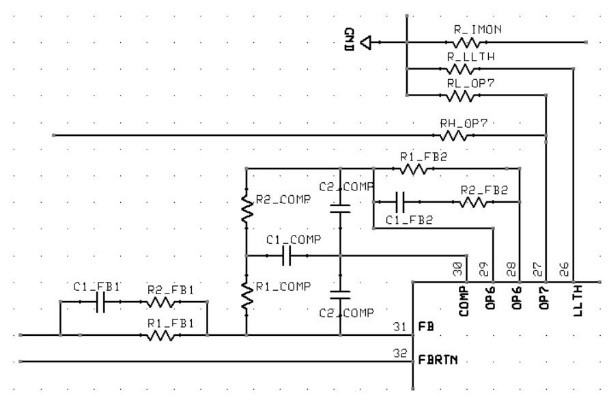
模拟控制器
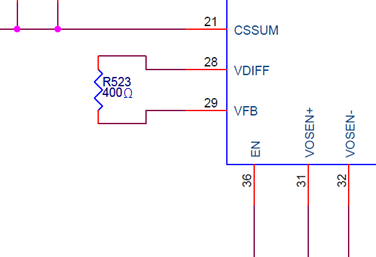
MP2888A
图 2: 负载-线性和环路补偿(模拟控制器对比数字控制器)
数字控制器可以简化系统设计。 对于工程师而言,可以帮助简化 PCB 布局设计。 图 3 为模拟控制器和数字控制器对比图。 数字控制器可以节省 36% 的占板面积,需要的传统部件数量不到原来的一半。
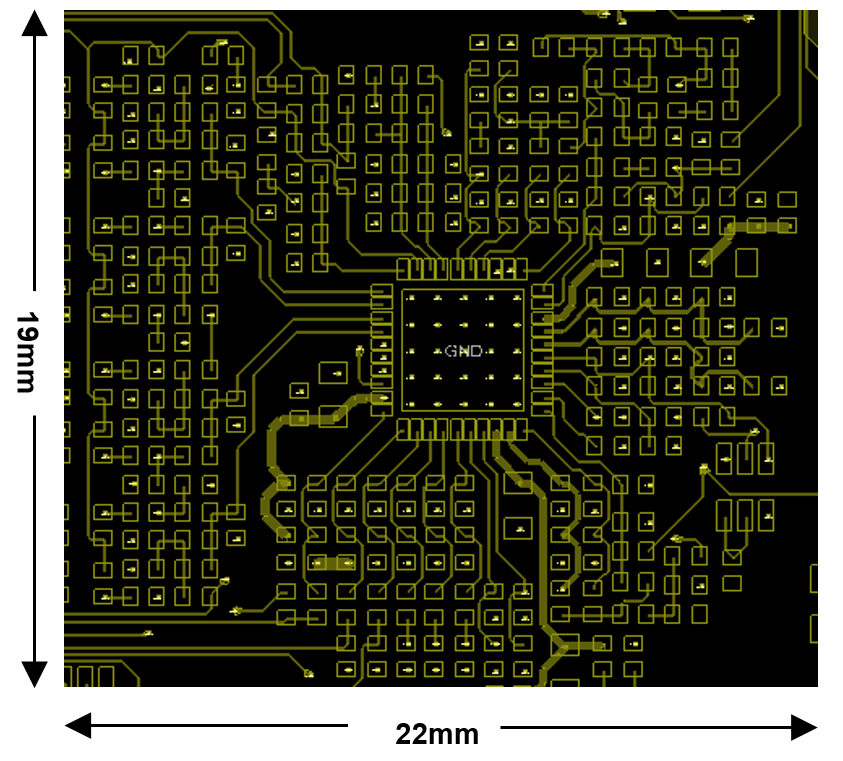
模拟控制器
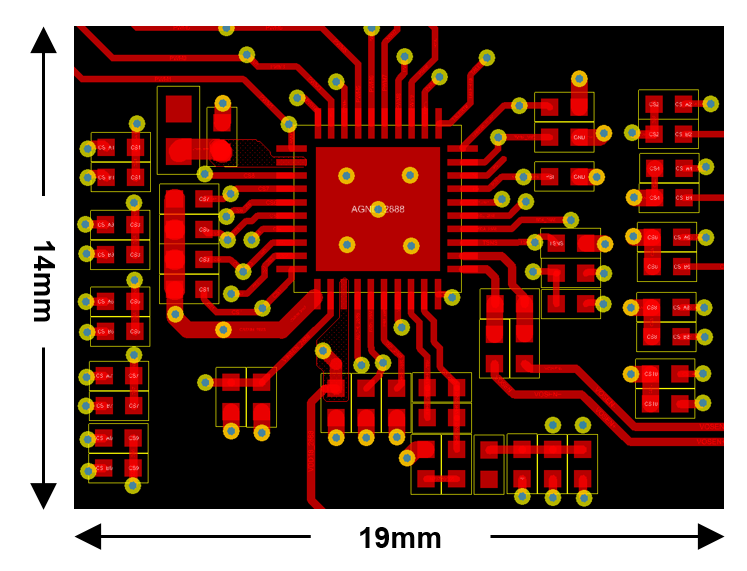
MP2888A
图 3: PCB 布局的复杂程度(模拟控制器对比数字控制器)
典型的模拟控制器使用一个 PWM 信号来驱动单个功率级。对于数据中心等高功率应用,其处理器要求至少 500A 或更高的负载电流,一般采用的方法是:
- 选择相位数量最多的控制器(例如 20 个相位)
- 使用倍相器,通过生成两个交错并联的信号(由原始信号构成)来使相位数量翻倍
但是,目前市面上尚没有 20 相模拟或数字控制器,而且倍相器会增加部件数量和成本,同时增高系统设计的复杂性。
与此相反,数字控制器(例如 MP2888A)可以通过一个通用 PWM 信号来驱动两个功率级 (参见图4).此类数字控制器无需采用倍相器,还可确保两个功率级之间的均流。因此,一个 10 相数字多相控制器堪比 20 相系统设计。
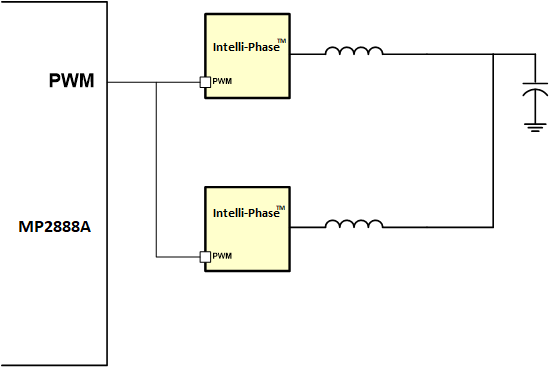
图 4: MP2888A 采用一个常用 PWM 信号来驱动两个Intelli-PhaseTM设备
结论
多相解决方案已逐步发展为数字控制方案,它能够更有效地解决大电流/功率应用挑战,例如数据中心此类应用。通过采用数字控制解决方案,可以大幅降低部件选择、环路/性能优化和布局等带来的负担。这些控制解决方案缩短了整体设计和解决系统故障所需的时间,最终加快了上市速度。
直接登录
创建新帐号