磁性角度传感器相较光学传感器的整体优势

每月为您发送最具参考价值的行业文章
我们会保障您的隐私
简介
传感器技术的进步正为智能家居、自动驾驶等应用带来新的可能性。随着自动化应用需求的增加,设计人员正在寻找创新方法,以高效、经济的方式提供精密运动控制。
传感器技术是制造业和汽车业的关键组成,它广泛应用于环境监测,如部件位置检测、液位检查、标签检测和质量控制等。在汽车领域,传感器更是运动控制组件与其他子系统之间的重要桥梁。
尽管传感器应用范围广泛,但其基础技术都一样,就是负责将物理环境(如热、光、声和运动)中的变化转换为电信号。这些信号随后被转化为二进制数据传输至计算机。
例如,在运动控制系统中,电机反馈传感器被用来执行重要任务。电机反馈传感器通常安装在电机轴或负载上,它为控制系统提供可转换为速度或位置的输入;控制系统将利用该输入数据来降低实际位置/速度与指令之间的误差。
位置传感器的选择
光学传感器和磁性传感器的重要应用之一是电机运动测量。当电机旋转时,测量其角度位置非常重要。传感器能够帮助控制器向电机驱动器发送正确的电信号,从而优化电机效率。
测量物体的接近度和位移对汽车和制造业都很重要,特别是对那些需要阀门定位、液位检测、安全控制、机器控制或过程控制的应用。
从电动工具到洗碗机,再到车库门开启器,所有现代机械都依赖精确的位置传感器。简单来说,一旦你按下一个机器按钮,就会涉及到电动机和位置传感器,而位置传感器就负责收集设备正常运行所需的数据。
不同传感器收集数据的方式也不同。对光学传感器来说,它通过计算光束的变化来收集数据。这类传感器由光源、光电探测器和不透明遮光盘组成,遮光盘上带有用于中断光路的特定结构。机器运动时,遮光盘与机器同步移动,光线会穿过或反射这些结构,从而传递出物体的相对位置信息。
用于遮断光路的遮光盘数量与精度直接相关,因此附加遮光盘可以提高精度。能够提高精度的光学传感器极具竞争力,但附加遮光盘将导致额外的成本。
磁性传感器利用了与磁铁直接相关的技术。这种传感器将敏感材料(例如砷化镓、锑化铟和硅)的磁性变化以及物理变化(例如磁场、电流或温度)转换为电信号。与光学传感器一样,磁性传感器可以检测物体的存在与否和运动。
为什么选择磁性传感器
设计师们大多都很熟悉光学角度传感器,但磁性角度传感器现已成为传感器应用领域中越来越具竞争力的理想选择。
尽管光学传感器可以提供高精度的测量,但其价格是磁性传感器的7到10倍。重型(heavy-duty)光学传感器的价格甚至高达 1000 美元(具体取决于分辨率)。而且,光学传感器的物理尺寸也比磁性传感器大。
在汽车系统中,磁性传感器广泛应用于感测位置和速度。例如,传感器可测量曲轴的角位置,以确保火花塞的正确点火角度。从防抱死制动系统的车轮速度,到安全气囊控制的汽车座椅位置,磁性传感器可以测量并传输这中间的所有数据。
与光学传感器相比,磁性传感器具有几个关键优势。例如,光学传感器需要在电机轴上安装旋转盘,磁性传感器不需要,它是完全非接触式的。此外,磁性传感器的使用寿命更长,因为其相互作用的组件更少,所以磨损更少。
如图 1所示,光学编码器需要一个发射器 PCB 和一个接收器;磁性编码器则紧凑得多,它仅需一块磁铁和一个PCB 即可运行。这种非接触式测量意味着磁性编码器的制造成本低于光学传感器,因为它们不需要轴承或机械耦合。它采用标准硅集成电路工艺制造,制造技术经过简化具有高性价比。
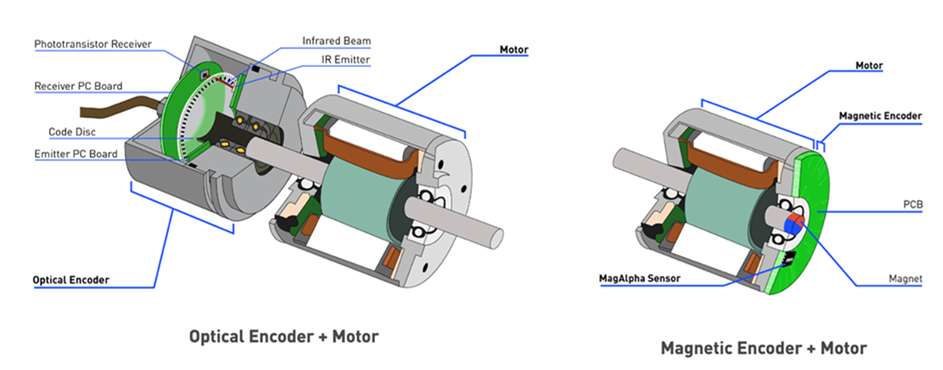
图1: 光学编码器比磁性编码器尺寸大
光学编码器是为特定外形尺寸设计的,这意味着只要电机符合外形尺寸标准,它们就可以用于许多不同的电机。磁性编码器的占用空间比光学编码器要小,但需要根据给定的电机进行定制。除此之外,磁性编码器仍然是高性价比的选择,而且可简化设计。
MPS创新的磁性传感器技术
传统的磁性角度位置传感器有时在精度和带宽方面存在不足。
MPS 率先开发出能够超越光学传感器的磁性传感器技术,它占用空间更小、成本更低。MPS 的 MagAlpha 系列磁性角度位置传感器采用创新方法测量角度。它采用专有 SpinAxisTM 霍尔测量技术,以数字格式提供瞬时角度位置。它还利用相位检测方法提供即时数据,无需进行模数转换或复杂的角度计算。
MA600是一款采用 MagAlpha 技术的先进磁性角度传感器。它配备了电机和旋转编码器,可广泛应用于精密机器人、工厂自动化、楼宇自动化和控制、动力辅助转向、汽车电子制动系统、热管理和流体管理,以及自动驾驶等领域。
MA600 可以支持各种磁场强度和空间配置。它在 75Hz 带宽下提供 15 位分辨率,在 12kHz 带宽下提供 12.5 位分辨率,性能水平可与光学传感器相媲美。MA600 采用隧道磁阻桥来检测磁场,以提高灵敏度并降低噪音。它集成了高带宽磁性位置传感器,精度极高,可媲美光学编码器。MA600 还采用了超小尺寸的 QFN-16(3mmx3mm)封装。
对于不需要这种高精度的传感器应用(例如收音机上的调谐钮),MPS提供MA800来实现低功耗的角度检测。MA800性价比高,可用于调节收音机音量等人机界面 (HMI) 解决方案。其传感器具有 8 位分辨率,可应用于各种通过按钮或旋钮来控制性能的电子设备,如白色家电、智能恒温器、键盘上的拨盘、智能扬声器、厨房炉灶和家电控制器等。
由于没有机械运动部件,MA800 比同类光学传感器更可靠。它还采用 QFN-16(3mmx3mm)封装,因此也是超小的解决方案。它是用于拨盘和按钮操作的单传感器,易于设计,并具有可配置检测阈值和20mT 至 120mT可配置场强范围。
MA302是另一款12 位分辨率的位置传感器解决方案,它适用于任意无刷直流 (BLDC) 电机应用。该器件不依赖霍尔效应技术,设计高效且减少了PCB 占用空间(见图 2)。其潜在应用包括便携式手动工具、厨房用具、水泵、电机速度和方向控制以及清洁机器人等。
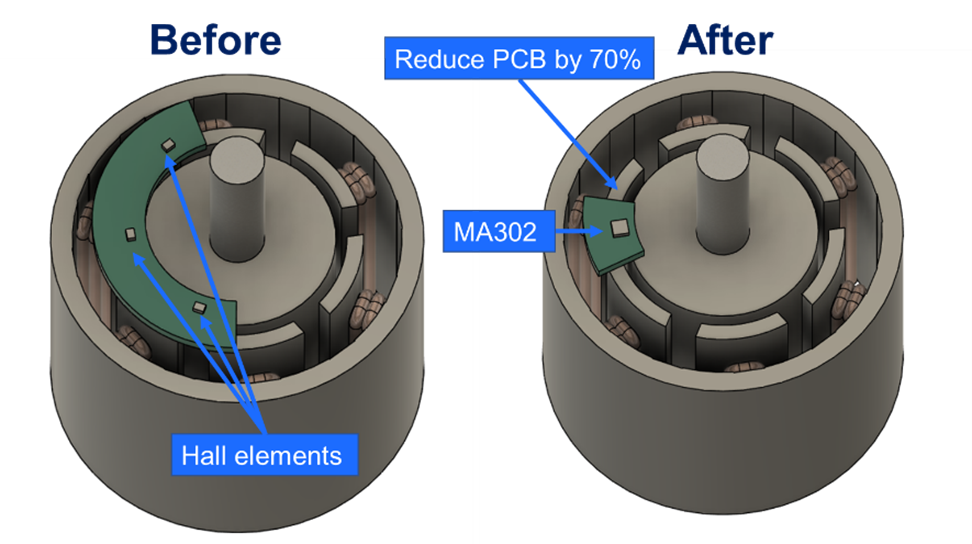
图 2:MA302 改进型磁性传感器技术减小了占位空间
功能安全在汽车领域非常重要,MPS 正在将功能安全参数纳入新传感器电源产品的开发中。即将推出的MAQ79010FS是一款采用 MagDiffTM 技术的 14 位绝对角度位置传感器。它配合全面的片上诊断功能实现功能安全备用系统,符合 ASIL 标准。该器件不受杂散磁场的影响,可为车辆提供额外的保护,帮助车辆在繁忙的高速公路上识别潜在危险,避免发生危险。
结语
传感器技术正在快速发展,磁性传感器是一种极具竞争力和吸引力的传感器。作为磁性传感器电源解决方案领域的领导者,MPS能为包括ATM 机、油泵和汽车内饰在内的各种应用提供先进的传感器产品选择。
比同类光学传感器更小、更具成本效益的MA600等产品能够帮助您提升最终产品的竞争力。与此同时,MPS 还在持续扩大其功能安全传感器产品范围,尤其针对汽车行业。如需了解MPS 在磁性传感器领域的更多成果,请访问我们的官网。
_______________________
您感兴趣吗? 点击订阅,我们将每月为您发送最具价值的资讯!
直接登录
创建新帐号