Harnessing Magnetic Position Sensors for the Future of Automotive Innovation: A Comprehensive Exploration of Selection, Application, and Quality Standards

Get valuable resources straight to your inbox - sent out once per month
We value your privacy
Introduction
As automotive technology continues to progress, magnetic position sensors play a crucial role in the design of modern vehicles. These sensors have become indispensable in detecting and measuring magnetic fields to determine the precise positions of various components within the automobile. One of the primary reasons for their widespread implementation lies in their non-contact sensing capabilities, ensuring reliable and robust performance even in harsh environmental conditions. This comprehensive guide aims to offer an in-depth exploration of the applications of magnetic position sensors in the automotive industry, shedding light on their significance, usage, and benefits. Additionally, it will provide essential guidelines for selecting the appropriate sensors and ensuring adherence to the necessary quality standards.
In-Depth Understanding of Magnetic Position Sensors
The fundamental operation of magnetic position sensors relies on the principles governing variations in magnetic fields. These sensors analyze these fluctuations to precisely monitor the movement or positioning of an object concerning a fixed reference point. In the automotive sector, several types of magnetic position sensors find widespread use, including Hall Effect sensors, Anisotropic Magneto-Resistive (AMR) sensors, Giant Magneto-Resistance (GMR) sensors, and magnetic encoder ICs. Each of these sensor types possesses distinctive attributes, making them suitable for various automotive applications.
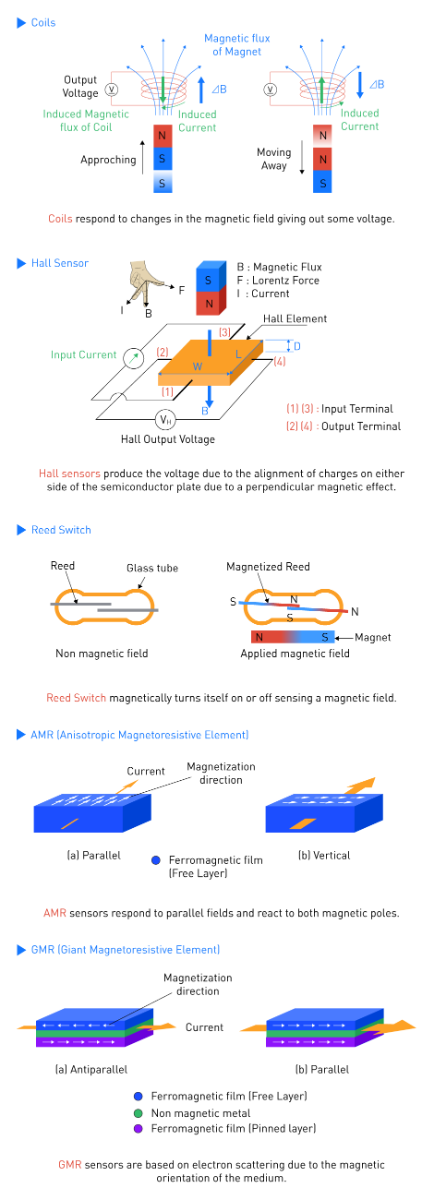
Figure 1. Different Magnetic Sensors
The operation of these sensors involves generating a voltage or resistance alteration when exposed to a magnetic field, and this transformation is then converted into positional data through processing. Due to their non-contact nature, these sensors experience minimal wear and tear, which significantly contributes to extending their operational lifespan. As a result, they are exceptionally reliable for applications demanding uninterrupted and consistent monitoring capabilities.
The Rationale for Using Magnetic Position Sensors
The implementation of magnetic position sensors in automotive applications is driven by several important reasons:
- Accuracy: Precision is a crucial factor in various vehicle functions, including throttle positioning, brake operation, and steering control. These sensors' high precision significantly contributes to ensuring the safety and optimal performance of vehicles.
- Robustness: Automotive applications benefit from the robust nature of magnetic sensors, as they can withstand environmental challenges such as dust, vibration, and extreme temperatures. This resilience enhances their suitability for use in automobiles.
- Non-contact Sensing: This capability of magnetic sensors allows them to measure positions without physical contact with the observed object. This unique feature not only ensures accuracy but also minimizes wear and tear, thereby increasing the sensors' longevity.
- Versatility: Magnetic sensors' versatility lies in their capacity to measure both linear and rotational movement. This attribute makes them highly adaptable to a wide range of applications within vehicles, further expanding their usability.
Guidelines for Choosing Magnetic Position Sensors
Selecting the right magnetic position sensor for automotive applications necessitates a thorough evaluation of several critical characteristics, which are as follows:
- Measurement Range: In order to effectively monitor the specific part's motion, the chosen sensor should have the capacity to measure the entire range of movement that the part may undergo.
- Resolution: The sensor's ability to detect the smallest incremental movements, known as resolution, is a crucial consideration. Opting for a sensor with higher resolution ensures more accurate and detailed position data.
- Repeatability and Linearity: Consistency in readings over time, known as repeatability, is essential for reliable and stable performance of the sensor. Additionally, the sensor's measurements should maintain a linear relationship with the actual movement of the part it monitors.
- Durability: Automotive environments can be challenging, exposing sensors to factors like vibrations, dust, and extreme temperatures. Therefore, selecting a durable sensor that can withstand such conditions is imperative to ensure longevity and reliable operation.
- Speed: The selected sensor must possess the capability to accurately track the maximum operating speed of the monitored part, ensuring real-time and precise position information during high-speed movements.
- Cost: Considering the cost of the sensor is vital, particularly for automotive applications that involve large-scale production. Striking a balance between performance and affordability is crucial to optimize overall project costs.
- Power Requirements: Compatibility with the power source and voltage levels available in the specific application is essential when choosing a sensor. Furthermore, opting for a sensor with low power consumption enhances energy efficiency and contributes to sustainable operation.
- Output Interference: Evaluating the type of output signal generated by the sensor is of utmost importance. Whether it is an analog voltage, analog current, PWM signal, or digital protocols like SPI or I2C, the chosen output should align with the application requirements and seamlessly integrate with the existing system architecture. A compatible output signal ensures smooth data transmission and communication with other components in the vehicle system.
Automotive Quality Specifications for ICs
In the process of selecting appropriate Integrated Circuits (ICs) for automotive applications, a comprehensive grasp of automotive quality specifications is essential. Some key aspects to consider are as follows:
- Automotive Grade Certification: One of the fundamental considerations for choosing ICs in automotive applications is ensuring they adhere to automotive quality standards. Compliance with standards such as AEC-Q100 for integrated circuits and AEC-Q200 for passive components, established by the Automotive Electronics Council (AEC), guarantees their suitability for the automotive environment.
- Operating Temperature: Automotive ICs must exhibit robust operational capability across a wide temperature range. Typically, they should be able to function reliably in temperatures ranging from -40°C to 125°C or even higher, depending on the specific application's requirements.
- Electrostatic Discharge (ESD) Protection: Given the prevalence of static discharge in automotive environments, it is crucial for automotive ICs to possess high levels of Electrostatic Discharge (ESD) protection. This protection ensures that the ICs can endure and perform flawlessly despite exposure to electrostatic discharges.
- Robustness: Ensuring the robustness of automotive ICs is paramount. They should be designed to withstand various environmental factors such as mechanical stress, thermal stress, humidity, and other challenging conditions encountered in automotive applications.
- Long-Term Reliability: Automotive ICs must demonstrate exceptional long-term reliability, as vehicles are expected to operate smoothly for extended periods, often spanning a decade or more. Reliability is essential to minimize maintenance costs and ensure consistent performance throughout the vehicle's lifespan.
- Compliance with Safety Standards: Depending on the role and function of the IC, it may be required to comply with specific automotive safety standards. For instance, ICs utilized in critical systems like braking or steering might need to adhere to ISO 26262, the functional safety standard for road vehicles. Compliance with safety standards ensures the IC's performance aligns with stringent safety requirements, contributing to overall vehicle safety.
Exploring Applications of Magnetic Position Sensors
Magnetic position sensors find wide applications in modern vehicles, which include but are not limited to:
- Steering Systems: Magnetic sensors play a key role in electronic power steering systems by providing essential data about the steering wheel's angle and rotation. This information is crucial for adjusting the power assist offered to the driver, resulting in improved control and driving comfort.
- Throttle Positioning: In modern fuel-injected engines, throttle position sensors are responsible for monitoring the position of the throttle. The data gathered from these sensors is then transmitted to the engine control unit (ECU), enabling the optimization of critical engine functions, such as fuel injection, ignition timing, and other engine operations, resulting in improved fuel efficiency and performance.
- Brake Systems: Magnetic sensors play a vital role in brake systems by detecting the position of brake pedals. This capability enables the implementation of advanced safety features such as anti-lock braking systems (ABS) and electronic stability control (ESC). By precisely monitoring brake pedal position, these sensors contribute to enhanced vehicle safety and stability during braking maneuvers.
- Transmission Systems: In automatic transmission systems, magnetic sensors are utilized to determine the position of the gear selector. This information is essential in indicating whether the vehicle is in the park, reverse, neutral, or drive modes. Accurate detection of gear positions ensures smooth and efficient gear shifting, enhancing the overall driving experience.
- Suspension Systems: Active suspension systems utilize magnetic sensors to accurately measure the relative position between the vehicle's body and its wheels. This real-time data allows the system to make continuous adjustments to the suspension, resulting in improved ride comfort and handling. By dynamically adapting to road conditions and vehicle movements, active suspension systems enhance overall driving performance and stability.
- Wheel Speed Sensors: Wheel speed sensors are crucial components of the Anti-lock Braking System (ABS). They are responsible for detecting any significant variation in wheel rotation speed compared to others, which could indicate potential wheel lock-up during braking. By monitoring wheel speeds, ABS can prevent skidding and maintain control, thereby enhancing braking performance and vehicle safety.
- Camshaft and Crankshaft Positioning: Magnetic sensors are employed to provide the Engine Control Unit (ECU) with accurate data regarding the positions of the camshaft and crankshaft. This information is essential for optimizing the timing of ignition and fuel injection, resulting in improved engine efficiency and performance. Proper synchronization of engine components, facilitated by these sensors, ensures precise combustion and reduced emissions.
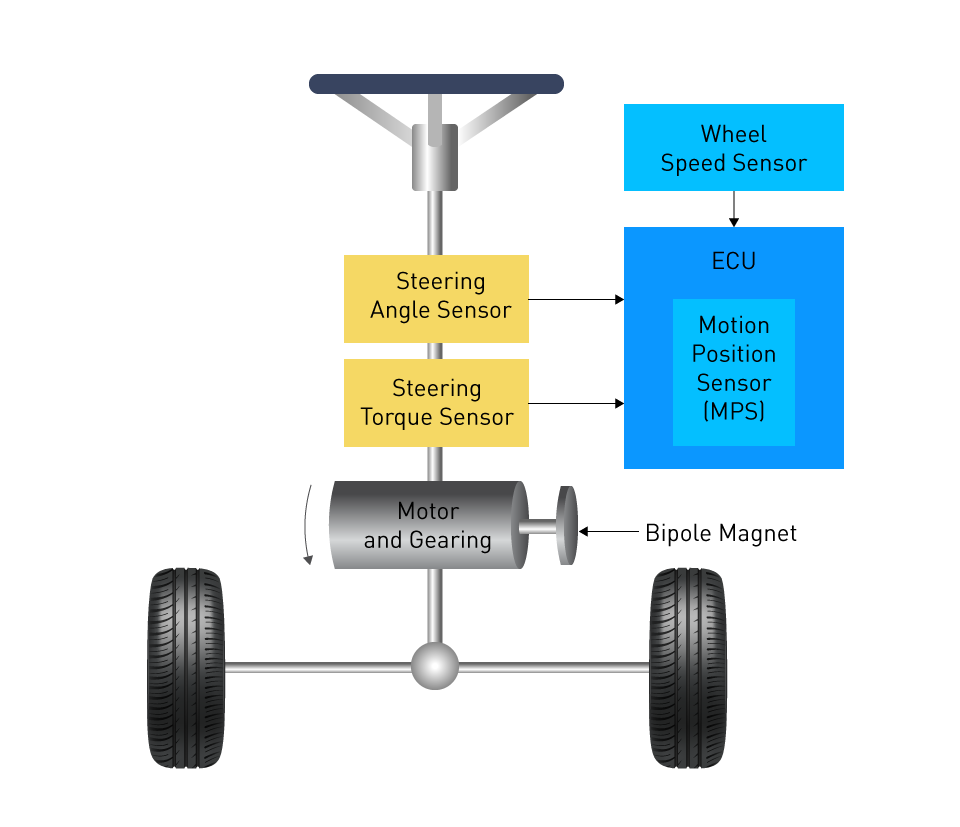
Figure 2. Steering Systems
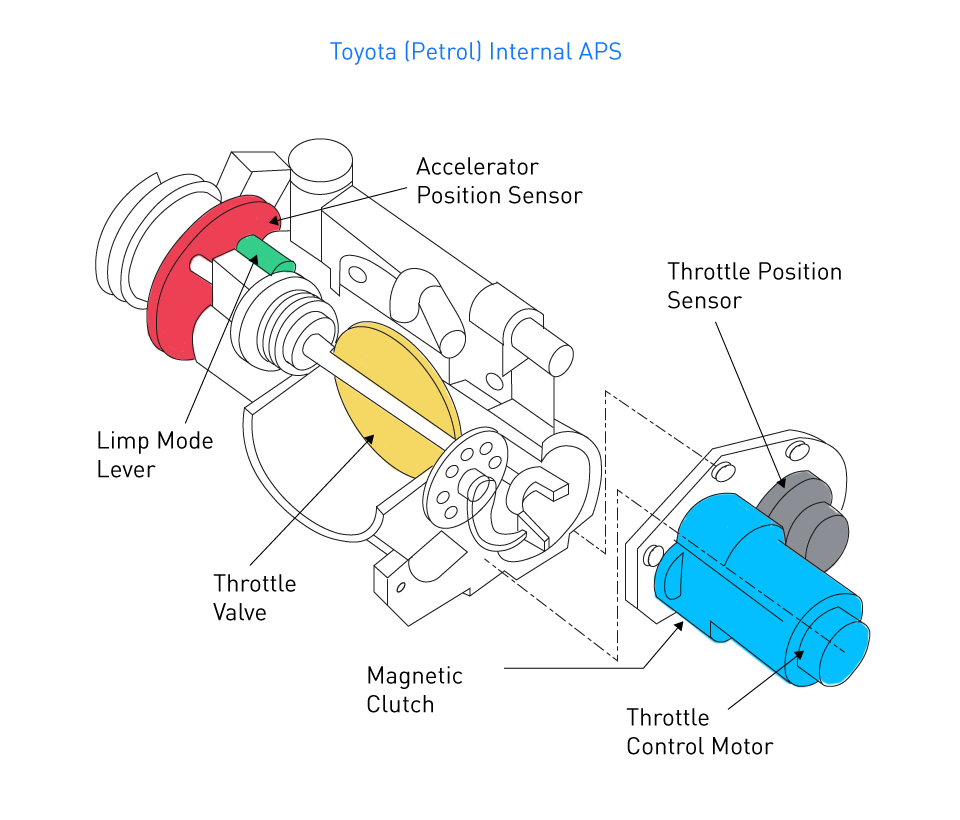
Figure 3. Throttle Systems (Toyota)
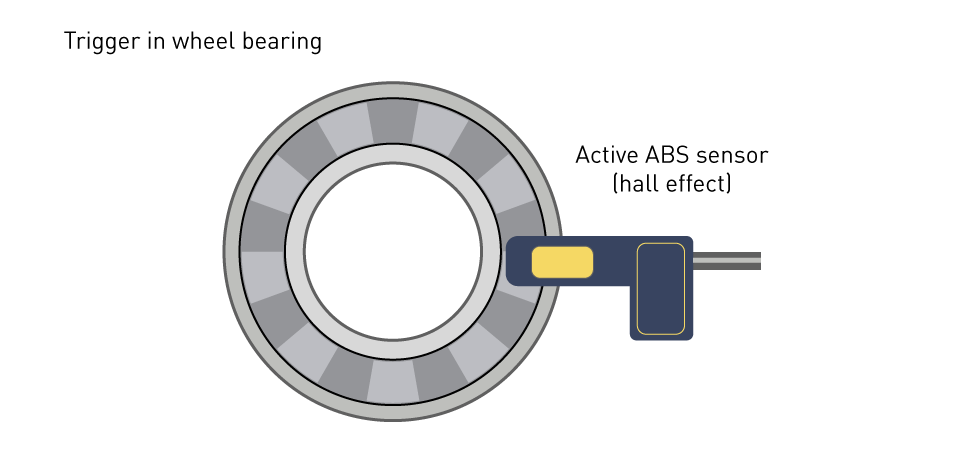
Figure 4: ABS Braking System
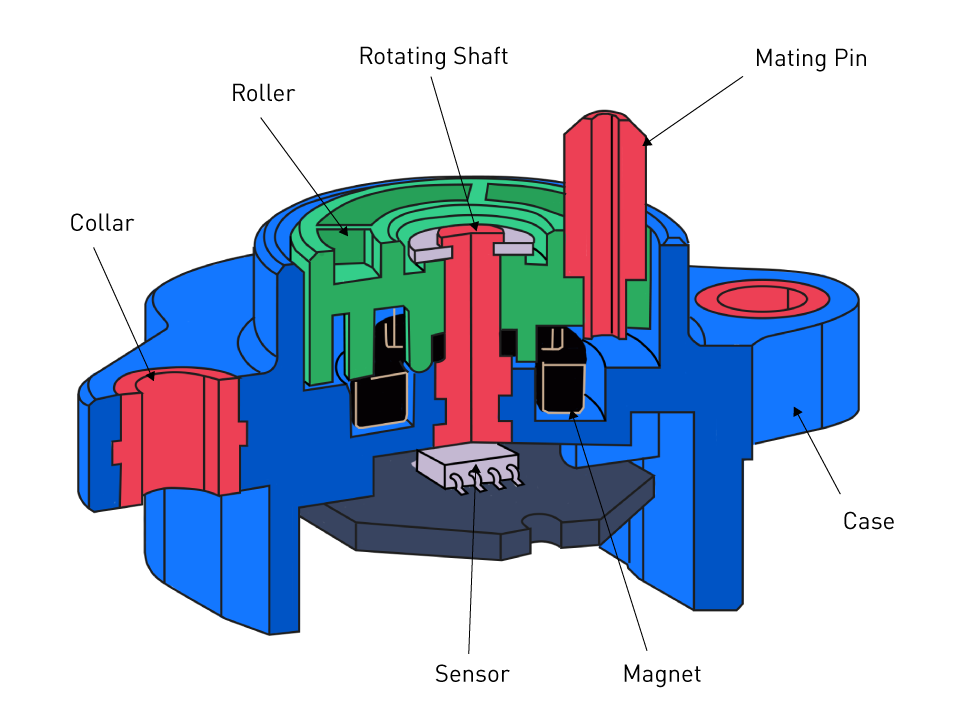
Figure 5: Gear Transmission System
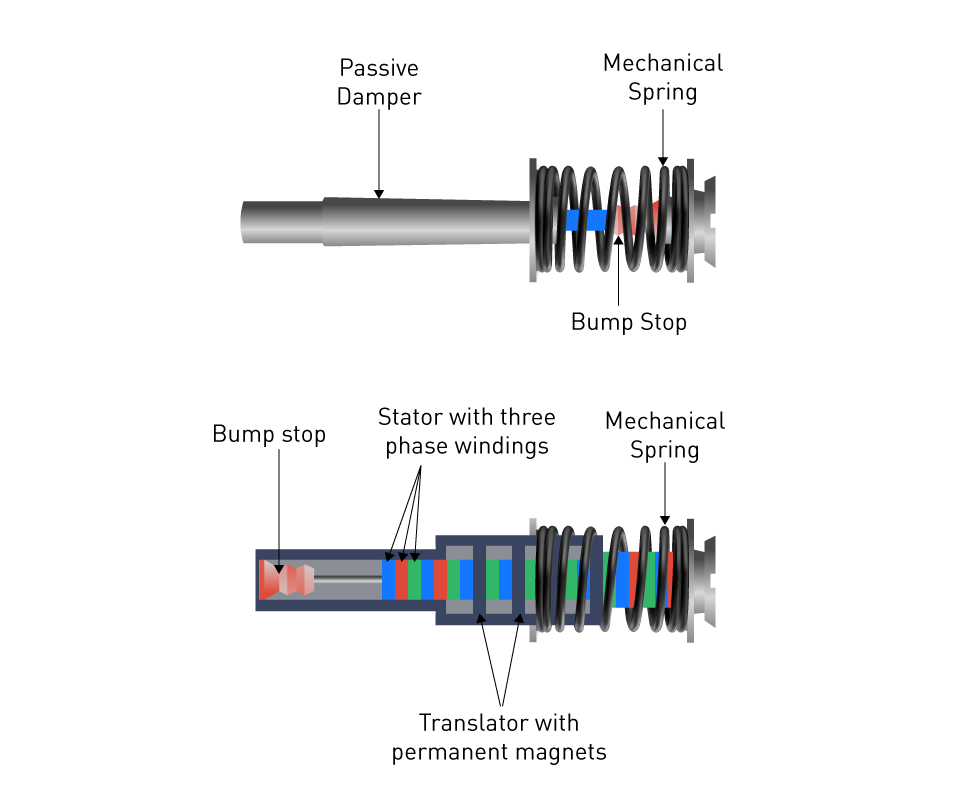
Figure 6. Suspension System of Automobiles
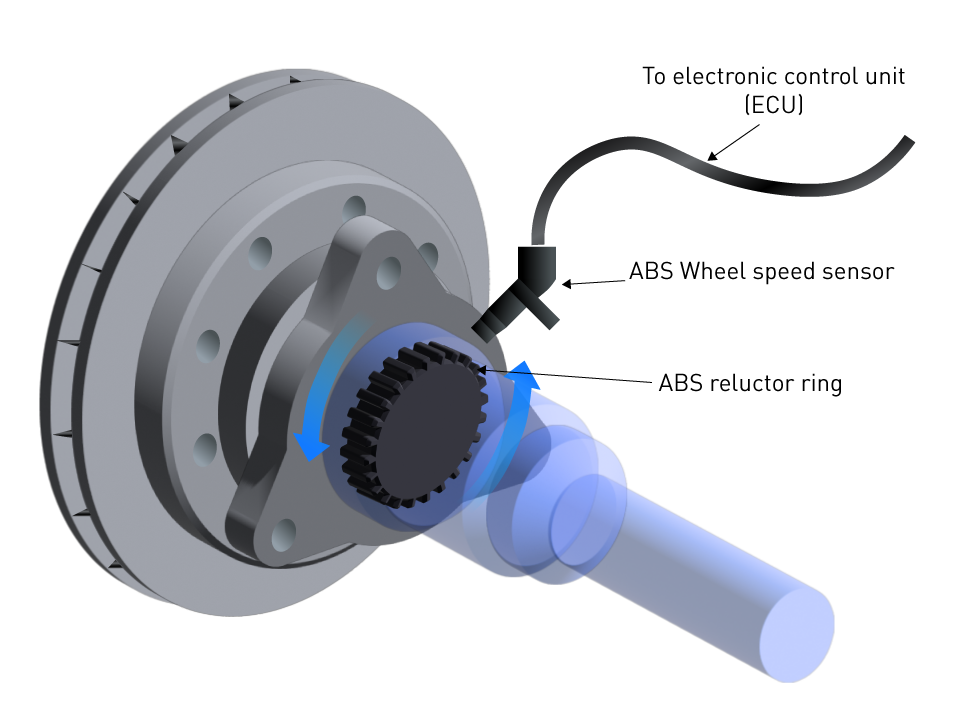
Figure 7: Wheel Speed Sensors
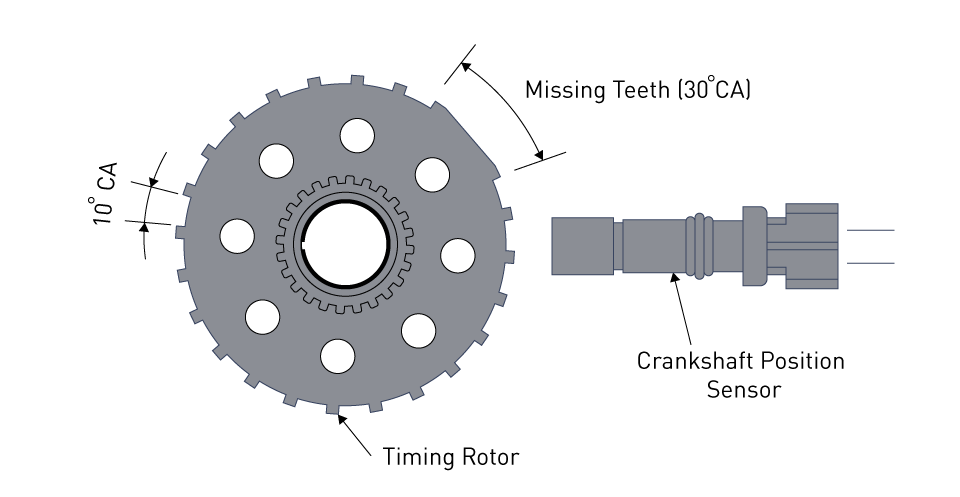
Figure 8: Crankshaft Position Sensor
The increasing significance of magnetic position sensors in the automotive sector, especially with the rise of autonomous vehicles, highlights their multifunctional, precise, and resilient characteristics. These features make them an essential aspect of the future of automotive technology, ensuring safer, more efficient, and more convenient journeys. Furthermore, thorough consideration of automotive quality specifications when selecting ICs for these sensors ensures optimal performance and dependability, ultimately leading to improved vehicle safety and efficiency.
_______________________
Did you find this interesting? Get valuable resources straight to your inbox - sent out once per month!
直接登录
创建新帐号