ADCs in Automotive Systems: Enhancing Safety and Performance

Get valuable resources straight to your inbox - sent out once per month
We value your privacy
In recent years, there has been a noticeable trend in the automobile sector toward automation and digitization. Modern automobiles are becoming more and more dependent on digital technology, from advanced driver assistance systems (ADAS) to entertainment systems. Analog-to-Digital Converters (ADCs), which are at the core of these systems, are essential for transforming actual analog signals into digital data that can be processed by the vehicle’s computer systems. The usage of ADCs in automotive systems to improve performance and safety will be discussed in this article.
Understanding ADCs in Automotive Systems
ADCs are utilized in automobile systems to transform analog signals from different sensors into digital data. These sensors might be anything from pressure and temperature sensors to radar and light sensors. The computer systems in the car may use the digital data from these sensors to process choices, manage different operations, and notify the driver.
The excellent resolution and accuracy of high-precision ADCs make them a popular choice for automotive systems. The intricacies and specifics of the analog signals may be precisely captured by these ADCs, producing high-quality digital data that can be utilized to generate judgments that are correct and trustworthy.
Types of ADCs Used in Automotive Systems
Almost all vehicle controls must, to some extent, monitor the input voltage. For instance, they all want to know how much battery voltage is used to power them. A microcontroller IC is used in every control component. For this job, microcontrollers come with built-in ADC peripherals. However, separate discrete ADC integrated circuits that can do measurements considerably more quickly and precisely may be included in the control units for high-end measurements. The microcontrollers then read these measurement results digitally using I2C and UART communication channels.
SAR ADCs
Due to their fast processing speeds and low power requirements, Successive Approximation Register (SAR) ADCs are frequently employed in automotive systems. They operate by locating the input signal's closest match using a binary search algorithm. In this case, the output value is changed depending on whether the input signal is greater or lower than a set of reference voltages when compared to the input signal. The major building blocks of a SAR ADC are shown in the following illustration:
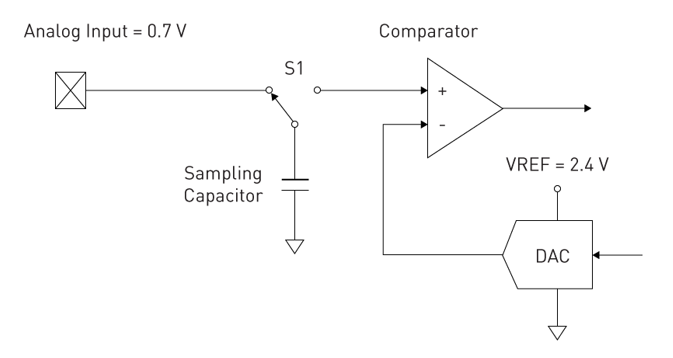
Figure 1: SAR ADC Block Diagram
Sampling capacitors are used in SAR ADCs. This capacitor is charged to the desired analog input voltage when switch S1 is turned to the left. This voltage is compared to the DAC output when S1 is turned to the right. The VREF (maximum ADC reference voltage) to 0V range of voltage levels can be supplied by a DAC (Digital Analog Comparator). The ADC is repeatedly comparing the various DAC output values to the voltage we sampled to see if they are bigger or smaller. Greater input voltage denotes a local bit value of 1, whereas lower input voltage denotes a value of 0. The analog signal input is digitalized throughout this iteration process, producing a bit stream.
SAR ADCs are especially helpful in situations when a quick response time is essential, such as in braking systems and advanced driver assistance systems (ADAS).
Delta-Sigma ADCs
When great resolution and precision are needed, automotive systems employ delta-sigma ADCs. They operate by employing a technique known as oversampling, which entails sampling the input signal at a rate far faster than the Nyquist rate. The combination of noise shaping and this oversampling enables Delta-Sigma ADCs to reach extremely high levels of precision and accuracy. The major building blocks of a Delta-Sigma ADC are shown in the following illustration:
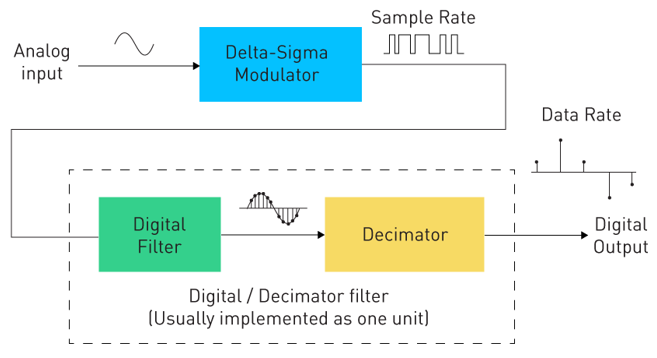
Figure 2: Delta-Sigma ADC Block Diagram
The input of the Delta-Sigma modulator receives an analog input voltage from us. The output will be a pulse-wave, where each pulse's width corresponds to the input voltage's amplitude. Although the pulse-wave is heavily polluted with high frequency noise, it seems to be the analog input voltage. So, we apply a digital filter on this pulse wave. This noise is being reduced by the digital filter, and we can see that the output now accurately reflects the analog input voltage. However, the oversampling makes this data too much for the control unit to manage, thus it is followed by a Decimator block. To make the oversampled data processable, the decimator simply reduces the data rate.
Applications requiring accurate measurements, like fuel injection systems and engine control units (ECUs), benefit greatly from the usage of delta-sigma ADCs.
Enhancing Safety with ADCs
ADCs are essential for improving the safety of contemporary automobiles. For instance, a vehicle's safety features include ADAS, braking systems, and stability control systems.
ADCs are employed in ADAS, for instance, to transform analog signals from radar sensors and cameras into digital information. Following the processing of this data, choices may be made about steering, braking, and acceleration as well as the detection of other cars, pedestrians, and obstructions.
ADCs are utilized in braking systems to transform analog information from pressure sensors into digital data. The vehicle's stability can then be improved by processing this data to regulate the amount of braking force supplied to each wheel.
Enhancing Performance with ADCs
ADCs are essential for boosting the performance of contemporary automobiles. They are utilized in a number of performance systems, such as fuel injection systems, transmission control systems, and engine control systems.
The best use of ADCs, for instance, in engine control systems is to transform analog signals from different sensors, such temperature sensors, pressure sensors, and oxygen sensors, into digital data. The engine's performance and efficiency may then be improved by processing this data to manage different parts of its functioning, including fuel injection, ignition timing, and throttle control.
ADCs are utilized in transmission control systems to transform analog signals from different sensors, including pressure and temperature sensors, into digital data. The transmission's functioning may then be controlled using this data, improving the vehicle's efficiency and maneuverability.
Case Studies: ADCs in Automotive Applications
ADCs are employed in a variety of automobile applications, including performance and safety systems. Here, we'll examine a few particular applications in more detail and consider how ADCs might improve performance and safety.
ADCs In Advanced Driver-Assistance Systems (ADAS)
Adaptive cruise control, lane keeping assistance, and automatic emergency braking are a few examples of the automated driving aid offered by advanced driver-assistance systems (ADAS). To identify other cars, pedestrians, and obstructions, these systems rely on a range of sensors, including radar sensors, lidar sensors, and cameras. The following image shows the key elements of an ADAS system:
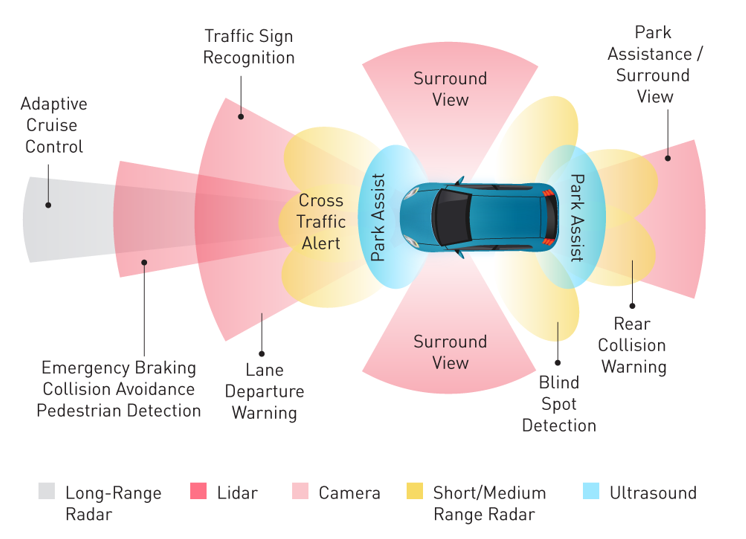
Figure 3: ADAS main components
By transforming the analog signals from various sensors into digital data, ADCs play a critical part in ADAS. The computer systems of the car can use this data to process steering, braking, and acceleration choices.
For instance, a radar sensor may be used to gauge the distance to the car in front of you in an adaptive cruise control system. An ADC transforms the analog signal from the radar sensor into digital data, which is then processed to change the vehicle's speed in order to maintain a safe following distance.
Due to its quick reaction time, a high-speed SAR ADC may be employed in this application. The short reaction time enables the system to react to changes in the distance to the car in front quickly, improving driving comfort and safety.
ADCs in Engine Control Systems
In order to maximize the performance and economy of an engine, engine control systems regulate a number of elements of its functioning, including fuel injection, ignition timing, and throttle control. The working characteristics of the engine are tracked by these systems using a range of sensors, including temperature, pressure, and oxygen sensors. The following image shows the different sensors that an engine control unit uses:
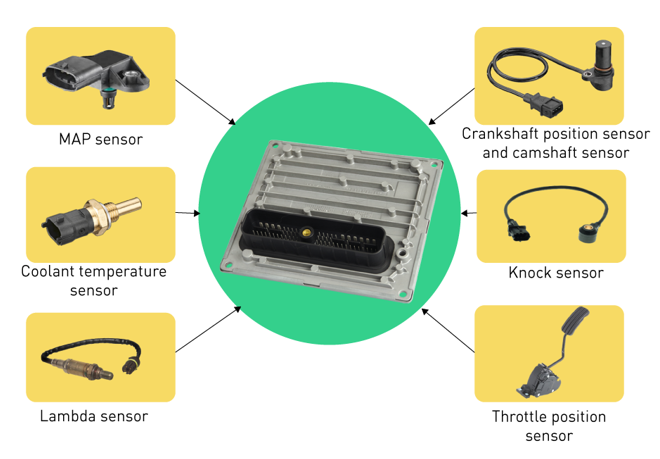
Figure 4: ECU main sensors
The analog inputs from these sensors are converted into digital data by ADCs, which are essential components of engine control systems. The engine control unit (ECU) can use this data to process many elements of the engine's functioning.
For instance, a fuel pressure sensor may be used in a fuel injection system to gauge the pressure of the gasoline in the fuel rail. An ADC transforms the analog fuel pressure sensor input into digital data, which is then processed to regulate the amount of gasoline injected into the engine.
Due to its great resolution and accuracy, a high-precision Delta-Sigma ADC may be employed in this application. The system can accurately manage the quantity of gasoline injected into the engine, improving engine performance and economy because of its high resolution and precision.
Conclusion
ADCs, which can transform actual analog impulses into digital data, are essential parts of contemporary vehicle systems. With their great resolution and accuracy, high-precision ADCs may dramatically improve these systems' performance and safety, leading to safer, more effective, and more pleasurable cars. The function of ADCs will grow in importance as the automotive industry continues to develop toward greater digitalization and automation, determining the future of automotive technology.
_______________________
Did you find this interesting? Get valuable resources straight to your inbox - sent out once per month!
直接登录
创建新帐号