In the realm of sensor design, understanding the fundamental architecture is key to tailoring sensors for specific applications. At the heart of a sensor's design is its sensing element, the critical component that interacts with the environment, responding to stimuli like temperature, pressure, or light. This response is then converted into a measurable signal through a transduction mechanism, which can vary from generating electrical voltages to altering resistance.
Further processing of this raw signal is often required to make it useful, which involves stages like amplification, filtering, and analog-to-digital conversion. The final output interface then ensures the sensor's compatibility with external systems, ranging from simple displays to complex data acquisition and control systems. This overarching architecture guides the specific design choices, such as material selection and interfacing, which are crucial for the sensor’s performance, efficiency, and integration into wider systems.
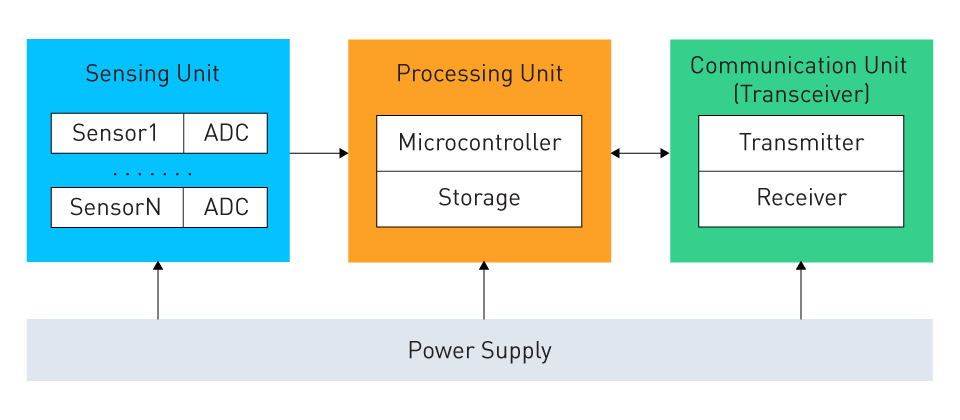
Figure 1: Sensor architecture
Material Selection for the Sensing Element
The choice of material for the sensing element is a critical decision in sensor design, as it directly affects the sensor's performance and suitability for its intended application. Several key considerations must be taken into account:
Type of Measurement: The nature of the physical phenomenon being measured (such as temperature, pressure, humidity, light, etc.) largely dictates the material choice. For instance, thermocouples for temperature measurement typically use different metal alloys, while piezoelectric materials are chosen for pressure sensors.
Accuracy and Precision: The selected material should enable the sensor to perform measurements with high accuracy and precision. This involves minimal deviation from the true value (accuracy) and consistent performance over repeated measurements (precision). Certain materials are inherently more stable and provide more reliable readings.
Sensitivity: Sensitivity refers to the degree of responsiveness of the sensor to changes in the measured parameter. The material should exhibit a significant and measurable change in its properties (electrical, optical, mechanical, etc.) even with slight variations in the stimulus.
Range and Operating Conditions: The material must withstand the full range of expected operating conditions without degradation. This includes considerations of temperature range, humidity levels, exposure to chemicals or radiation, and mechanical stress, ensuring the material's stability and longevity under these conditions.
Response Time: The time a sensor takes to react to a change in the measured parameter is crucial, especially in applications requiring real-time monitoring or control. Materials with faster response times are preferred in dynamic environments to ensure timely data collection and processing.
Form Factor and Packaging
The overall design of a sensor's form factor and packaging is crucial, as it determines how well the sensor can operate and survive in its intended environment. Several key considerations are pivotal in this aspect of sensor design:
Environmental Conditions: The packaging must protect the sensor from environmental factors like humidity, temperature extremes, and UV radiation. The material and design should ensure stable operation irrespective of external conditions.
Protection from Contaminants: Ensuring the sensor is shielded from contaminants such as dust, moisture, and chemicals is crucial. This is where Ingress Protection (IP) ratings become significant, indicating the level of protection offered against various foreign bodies and liquids.
The International Electrotechnical Commission (IEC) developed the Ingress Protection (IP) ratings. These ratings specify the level of protection offered by an enclosure against solid and liquid ingress. The rating is a two-number designation (e.g. IP65), with the first number indicating the level of protection offered against solid ingress and the second number indicating the level of protection offered against liquid ingress. The enclosure for a sensor must match application requirements, and IP ratings offer a standardized way of ensuring that sensor enclosures comply with application requirements.
Mechanical Durability: The sensor package should be robust enough to withstand mechanical stresses such as vibration, shock, and impact, especially in industrial or automotive applications.
Size and Form Factor: The physical size and shape of the sensor need to be compatible with the space constraints of the application. In wearable devices, for instance, compactness and unobtrusiveness are key design aspects.
Ventilation and Heat Dissipation: Efficient heat management is essential, particularly for sensors that generate heat during operation or are used in high-temperature environments. The design should allow for adequate heat dissipation to prevent overheating and ensure long-term reliability.
Electromagnetic Interference (EMI) Shielding: Sensors operating in environments with high electromagnetic noise require shielding to prevent interference that could compromise measurement accuracy.
Packaging Regulations and Standards: Compliance with relevant industry standards and regulations is necessary to ensure safety, especially in sectors like healthcare, aviation, and automotive.
Ease of Integration: The design should facilitate easy integration into existing systems, considering aspects like mounting options, connector types, and cable management.
Design for Specific Applications: Wearables, Industrial, Airborne
Wearables: For wearable applications, the sensor's form factor must prioritize user comfort, aesthetics, and ergonomic integration. The designs are typically compact, lightweight, and flexible, allowing seamless integration into clothing, accessories, or directly onto the skin. Bio-compatibility and skin-friendly materials are crucial to avoid irritation or adverse reactions. Packaging for wearables should also consider protection against environmental factors like moisture and dust, and enable unobtrusive and continuous monitoring of physiological parameters or environmental conditions.
Industrial Applications: In contrast, industrial applications often necessitate robust and durable form factors capable of withstanding harsh environments, such as extreme temperatures, corrosive substances, or high pressures. The packaging needs to be resilient, protecting the sensor elements from physical damage, contaminants, and electromagnetic interference. Integration with industrial equipment might require customization to align with existing systems and workflows, ensuring accurate and reliable sensing without disrupting normal operations.
Airborne Devices: Airborne sensor applications, such as those in drones or satellites, demand form factors that optimize aerodynamics, weight, and space utilization. The materials and packaging must endure high-altitude conditions, extreme temperature fluctuations, and mechanical stresses encountered during flight. Secure mounting, minimal drag, and efficient heat dissipation are essential design considerations to prevent malfunctions and ensure sustained performance in airborne conditions.
Adaptation to Specific Applications: Regardless of the application domain, the form factor and packaging should be tailored to the specific requirements and constraints of the intended use. This may involve innovative design approaches to accommodate unique shapes, sizes, mounting options, and protection levels. Modularity and scalability in design can offer versatility, allowing adaptation to various applications without significant modifications.
User Interface and Accessibility: The design should also consider user interactions, including display readability, button accessibility, and connectivity options, ensuring user-friendly operation and data access. For applications requiring user input or feedback, intuitive interfaces and clear indication of sensor status are vital to facilitate user engagement and accurate data interpretation.
Form factor and packaging are integral components of sensor design, significantly impacting the sensor's functionality, integration, and user acceptance in diverse applications. Thoughtful consideration of design elements, tailored to the specific needs and constraints of wearables, industrial settings, and airborne devices, is crucial to developing effective and reliable sensors. Balancing practicality, innovation, and user-centric design is key to advancing sensor technologies and broadening their applicability across various domains.
Power Considerations
In the design of sensors, power considerations hold paramount importance as they substantially influence the sensor's efficiency, longevity, and practicality. Proper attention to energy consumption and power sources is vital, especially for portable and remote applications where energy resources are limited or inaccessible.
Energy Harvesting
Energy harvesting is an innovative technique to garner energy from the surrounding environment, converting available ambient energy forms, such as light, heat, or motion, into electrical energy to power the sensor. This strategy can significantly extend the operational life of the sensor, reduce dependency on external power sources, and facilitate the deployment of sensors in isolated or harsh environments.
For instance, photovoltaic cells can harvest energy from sunlight, thermoelectric generators can exploit temperature gradients, and piezoelectric materials can convert mechanical stress or vibrations into electrical energy. The choice of energy harvesting method should align with the environmental conditions and energy availability at the deployment location to ensure consistent and sufficient power supply.
Low-Power Design
Implementing low-power design principles is crucial to optimize energy consumption and prolong battery life. Techniques such as duty cycling, where the sensor periodically enters a low-power sleep mode, can significantly reduce power consumption. The integration of low-power components, efficient signal processing algorithms, and power management systems are essential to maintaining high performance while minimizing energy usage.
Adaptive sampling rates and dynamic power scaling can further optimize power consumption based on the current operational demands and environmental conditions. Ensuring the sensor operates only when necessary and at the lowest sufficient power level contributes to energy conservation and extended operational life.
Battery Selection
Choosing the appropriate battery is another critical aspect of power considerations, entailing the evaluation of capacity, weight, lifespan, and environmental conditions. The battery should provide sufficient energy to sustain the sensor's operation between charges or replacements, considering the energy demands of sensing, processing, and communication activities.
The weight and form factor of the battery should align with the design constraints of the sensor, especially in wearables and airborne applications where weight and space are at a premium. Assessing the operating temperature range, rechargeability, and environmental impact of the battery is also crucial to ensure reliable operation and compliance with environmental standards.
Integration and Optimization
Seamlessly integrating energy harvesting technologies, low-power design principles, and appropriate batteries requires meticulous design and optimization. Balancing energy supply and demand, while accommodating the practical constraints and operational requirements of the sensor, is essential to realize efficient, sustainable, and reliable sensing solutions.
Power considerations are integral to the successful design and deployment of sensors. Energy harvesting, low-power design, and thoughtful battery selection are pivotal strategies to address the energy constraints and enhance the sustainability and reliability of sensors. Optimizing these elements according to the application's needs and environmental conditions is imperative to advance sensor technology and expand its applications in various domains.
Application-Specific Considerations
The design of sensors is not a one-size-fits-all endeavor. Different applications impose unique requirements and challenges, necessitating a tailored approach to sensor design. This customization ensures that sensors not only fulfill their basic function but also adapt to the specific demands and constraints of their intended environment.
Impact of Specific Application Requirements on Sensor Design
Need for Custom Sensors and Specialized Features: The specificity of an application can significantly influence sensor design. For instance, sensors developed for space applications must endure extreme temperatures, vacuum conditions, and intense radiation, features that are not typically required in standard industrial or consumer sensors. Similarly, biomedical sensors intended for wearable health monitoring devices must be highly sensitive, unobtrusive, and biocompatible, ensuring they can be worn comfortably for extended periods without affecting the user's daily activities.
Customization Examples: In space applications, sensors often require special materials and shielding to protect against cosmic radiation and thermal extremes. They also need to be highly reliable and capable of functioning autonomously over long periods due to the infeasibility of maintenance or repairs. This leads to the development of custom sensors with specialized features like enhanced durability, miniaturization, and advanced data processing capabilities to handle the unique challenges of space environments.
Tailoring Sensor Design to Meet Specific Application Requirements
Custom sensor design involves a comprehensive understanding of the application's environment, the parameters to be measured, and the integration with other system components.
Design Considerations: This could include optimizing the sensor's size and form factor for seamless integration, selecting specific materials for durability or sensitivity, and engineering the signal processing algorithms to provide accurate and reliable data under specific conditions.
Example in Space Applications: In designing sensors for a Mars rover, engineers must consider factors like the Martian dust, atmospheric composition, and temperature fluctuations. This might lead to the development of sensors with advanced filtering capabilities to prevent dust interference, materials that can withstand temperature extremes, and calibration techniques that maintain accuracy in varying atmospheric conditions.
Testing and Validation
In the intricate process of sensor design, testing and validation are critical steps that ensure the final product performs as intended and is reliable in its application. This phase not only assesses the sensor’s functionality but also its ability to meet the specific demands of its operational environment.
Importance of Testing and Validation
Testing and validation are crucial for multiple reasons:
Performance Assurance: They confirm that the sensor meets the desired specifications and performs accurately under expected conditions.
Reliability Verification: Long-term reliability is assessed, ensuring that the sensor maintains its performance over time and under various environmental stressors.
Safety and Compliance: Especially in critical applications, testing is necessary for safety and adherence to industry standards and regulations.
Methods for Verifying Sensor Performance and Reliability
Different methodologies are employed based on the sensor type and its application:
Laboratory Testing: Controlled environment tests to evaluate performance against known standards. This may include temperature, humidity, and pressure tests.
Field Testing: Deploying the sensor in real-world conditions to understand its behavior in actual operational environments.
Accelerated Life Testing: Simulating extended operational conditions to predict lifespan and identify potential long-term issues.
Performance Metrics: Evaluation against key metrics like sensitivity, accuracy, response time, and drift.
Ensuring the Quality of Sensor Design
Quality assurance in sensor design involves several strategies:
Iterative Testing: Incorporating testing at various stages of the design and development process, not just as a final check.
Statistical Analysis: Utilizing statistical tools to analyze test data, identify patterns or anomalies, and make informed improvements.
Certification Processes: Pursuing relevant certifications and complying with industry-specific standards.
Feedback Loops: Integrating feedback from testing phases back into the design process for continuous improvement.
直接登录
创建新帐号