Introduction to Automation and Robotics
The goal of automation and robotics is to create systems that can execute activities without the need for human interaction. These fields of engineering are combined to create these technologies. This field, which is profoundly changing the way industries operate, has developed through careful inventions and breakthroughs, constituting important turning points in the history of technology.
Brief History and Evolution of Automation and Robotics
Early Developments: Simple automated devices like water clocks were created in ancient civilizations, which is where the origins of automation and robotics may be found. The Industrial Revolution in the 18th century, however, provided the true push for the development of automated technology, with a primary focus on mechanizing manual labor to increase production.
Birth of Modern Robotics: The term "robot" first appeared in a play by Karel Apek called "R.U.R." in 1920, laying the conceptual foundation for modern robotics. George Devol's 1954 creation of Unimate, the first programmable robot, was the result of his quest to build machines with human-like qualities. In 1961, Unimate was put into production and sold.
Advancements in Automation: The incorporation of computer technology into automation systems during the next few decades led to a rapid advancement in technology, making it possible to do increasingly intricate and accurate tasks. Automation spread in many industrial sectors thanks to the advancement of computer numerical control (CNC) systems and programmable logic controllers (PLCs), which improved output quality and optimized manufacturing processes.
Robotics Diversification: As artificial intelligence, materials science, and sensor technology advanced, the field of robotics expanded. Robots began to appear in areas other than industry, such as healthcare, agriculture, and service industries. The advent of collaborative robots, also known as cobots, has demonstrated the potential for human-robot cooperation in shared workspaces, thereby improving operational effectiveness and security.
Current Trends and Future Prospects: Autonomous vehicles, drone technology, and robotic process automation (RPA) are examples of how automation and robotics are synonymous with sophistication and variety today. With continuous research focused on creating robots with cognitive capacities, adaptive learning, and enhanced vision, the never-ending quest for innovation keeps pushing the envelope and offering previously unheard-of possibilities in the fields of automation and robotics.
Automation and robotics' development from simple automated devices to complex, multipurpose robots is a metaphor for humanity's never-ending quest to push boundaries and redefine possibilities. This field has changed industries and daily life through its evolution, which has been characterized by little breakthroughs and revolutionary discoveries. It is still at the forefront of technological development and has the ability to rewrite the rules for future civilizations.
Sensors in Industrial Robots
Industrial robots use a variety of sensors to do jobs with never-before-seen accuracy and efficiency. They are essential to the advancement of production capacities. Sensors are essential for a robot’s ability to sense its surroundings, make decisions, and move in a way that mimics the coordination of senses and motions in organic things.
Role of Sensors in Movement, Precision, and Feedback Systems
Movement and Navigation: Sensors serve as the eyes and ears of industrial robots, making movement and navigation easier. Encoders and accelerometers track the speed and direction of robots, providing crucial data for precise trajectory and placement maintenance. Robots can detect impediments and navigate complex surroundings with the use of proximity sensors and Lidar systems, which reduces the likelihood of collisions and maximizes path planning.
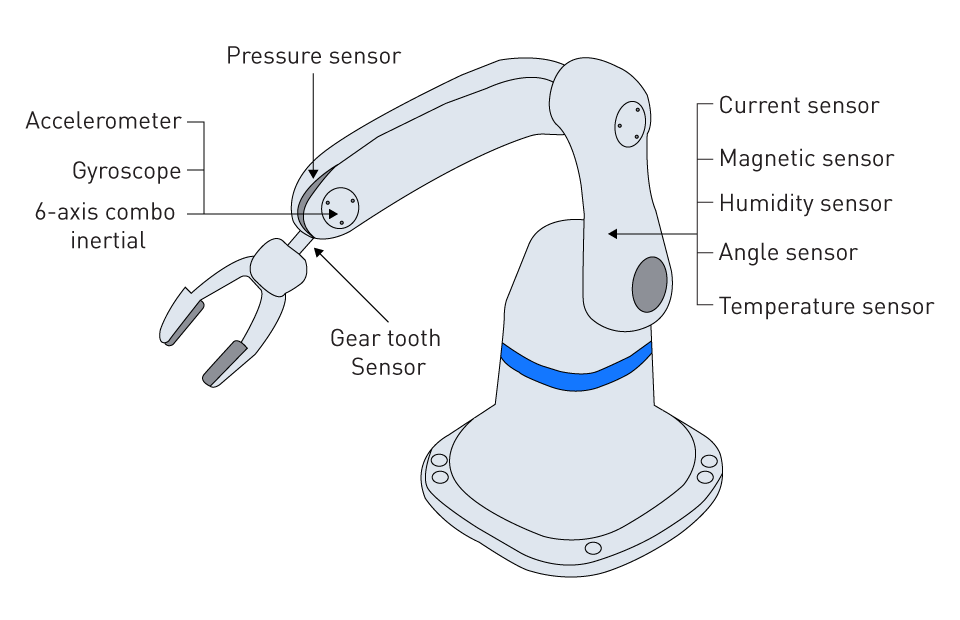
Figure 1: Types of Sensors Used in an Industrial Assembly Robot
Precision and Accuracy: In industrial settings, where even the smallest errors can result in major quality discrepancies, accuracy is crucial. Sensors are useful in this situation. Force-torque sensors, for example, allow robots to apply precisely the right amount of force, which is crucial for assembly activities. Meanwhile, vision systems and cameras guarantee precise component alignment and placement, reducing errors and improving product quality.
Feedback Systems: The foundation of robotic operations that are sensitive and adaptable is the feedback system. The control system receives constant, real-time information from sensors regarding the state of the robot and its surroundings. Algorithms keep an eye on sensor input and instantly adapt as needed. This is an illustration of closed-loop control, which embodies the integration of sensing and actuating functions by allowing the robot to dynamically modify its actions, adjusting for any disparities and guaranteeing the desired result is obtained.
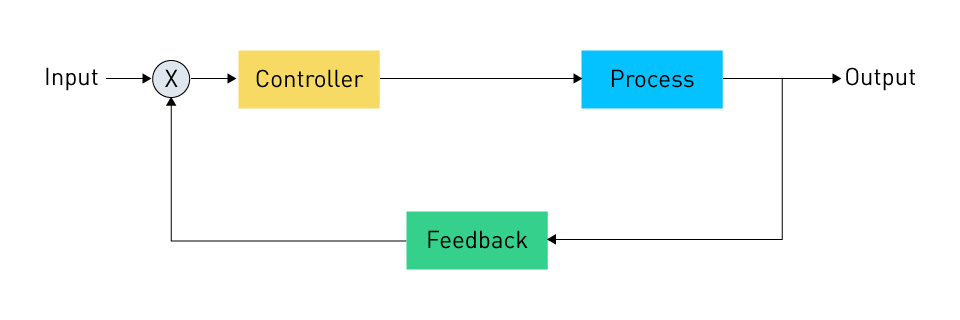
Figure 2: Closed-Loop Control
Integration with Control Systems: Industrial robot performance is enhanced when sensors and control systems work together. Robots can carry out intricate activities like welding, painting, and assembly with extreme precision and reproducibility thanks to sophisticated control algorithms that process sensor data and provide the necessary commands. This integration highlights the significance of sensors in bridging the gap between mechanical actions and computational judgments.
Applications:
- Sensors are used in automotive manufacturing to allow robots to carry out complex welding and assembly operations, guaranteeing structural alignment and integrity.Because sensors have such great accuracy, it is easier to handle and install delicate parts in semiconductor fabrication, preserving the integrity of microelectronic devices.
- Robots that sort, pack, and examine food items are made possible by sensors, which maximize productivity and guarantee that quality standards are met.
Industrial robots' sensors are the key components that make perception and action come together, giving them the unmatched intelligence and precision to interact, navigate, and adapt to their surroundings. Robots are now considered important friends in the industrial landscape because of the complex web of sensors they possess, ranging from force detectors to vision systems when combined with sophisticated control systems.
Collaborative Robots (Cobots)
“Cobots,” or collaborative robots, are a breakthrough advancement in robotic technology that is intended to collaborate with people in a shared office. These robots have advanced sensor systems built right into them, guaranteeing their adaptability, safety, and smooth integration into a variety of industrial settings.
Importance of Touch and Proximity Sensors for Safety
Safety through Sensing: Cobots use proximity and touch sensors to maintain a safe working environment. When they sense the presence of human workers, they modify their behavior accordingly. By ensuring that cobots can quickly stop or alter their movements to prevent collisions and unexpected contacts, these sensors help to reduce the likelihood of workplace accidents and interruptions.
Proximity Sensors: Proximity sensors are essential for determining whether or not people or items are around the cobot. This information allows the robot to make real-time modifications to its movements and functions. Cobots enable high-accuracy obstacle identification and distance measurement through the use of ultrasonic, infrared, and capacitive sensors, resulting in safer and more productive processes.
Touch Sensors: Cobots' touch sensors sense contact with outside objects and enable the robots to react quickly to inadvertent encounters. This quick reaction to tactile feedback is essential for averting mishaps and guaranteeing worker safety, especially in dynamic and uncertain work contexts.
Enhanced Collaboration: By combining proximity and touch sensors, cobots may now operate in harmony with people by sensing their presence and adjusting to their movements. Perceiving and responding to human actions improves productivity and expands human capabilities, resulting in a mutually beneficial and cooperative interaction between humans and robots.
Real-Time Adaptation: By combining sophisticated control algorithms with sensors, cobots are able to adjust their force, speed, and trajectory in response to sensory input. This flexibility is critical to preserving both efficiency and safety in settings where jobs performed by humans and robots are combined.
Applications:
- Cobots help human workers on assembly lines by using touch and proximity sensors to help with activities like part insertion and packaging. This increases production while maintaining worker safety.
- Cobots with sensors are used in healthcare to assist with sensitive surgical operations and patient care. They complement human knowledge by offering precision and dependability.
- Cobots are used in research labs to simplify complex experimental processes and enable scientists to perform precise manipulations safely and effectively.
For safe and effective human-robot collaboration, touch and proximity sensors must be integrated into collaborative robots. These sensors, in conjunction with sophisticated control systems, allow cobots to sense their environment, modify their behavior, and blend in with a variety of industrial environments. This increases the potential for automation and human-robot collaboration across a range of industries.
Drone Technology
Drones, the ultimate predators of automation and robotics, are now synonymous with technological advancement. They are outfitted with sophisticated gyroscopes, accelerometers, and vision systems that enable them to maneuver, steady, and carry out complex tasks over a wide range of terrains. The incorporation of technology is not only essential for augmenting the drone’s skills but also for broadening its possibilities across other industries, such as the precision-driven field of semiconductor fabrication.
Technological Integrations: Gyroscopes, Accelerometers, and Vision Systems
Gyroscopes: By identifying changes in rotational motion and angular orientation, gyroscopes serve as the stabilizing anchors of drones, providing the balance and orientation needed during flight. Drones with this capability can make modifications in real time and stay stable in a variety of air situations.
Accelerometers: By measuring the drone's acceleration, these instruments provide vital information on changes in its direction and velocity. This kind of data is essential for controlling the drone and guaranteeing exact alignment and control throughout its flight path.
Vision Systems: With the help of sophisticated image processing algorithms and cutting-edge cameras, vision systems enable drones to recognize and navigate their environment. Drones can operate independently and safely in a variety of settings thanks to this feature, which is essential for obstacle recognition, navigation, and mission execution.
Case Study: Precision Robotics in Semiconductor Manufacturing
Drones equipped with advanced sensors and control systems are increasingly becoming indispensable in the semiconductor manufacturing industry, where accuracy, dependability, and efficiency are essential. The adoption of these systems has resulted in notable progress in terms of operating efficiency and accuracy.
Semiconductors are essential parts of electronic gadgets that require extreme precision and close attention to detail when being made. Within this framework, drones are transforming conventional methods because of their unmatched agility and accuracy.
Implementation and Impact
Drones fitted with sophisticated sensors and high-resolution cameras carry out routine inspections and monitoring at semiconductor manufacturing facilities, spotting irregularities or flaws in semiconductor wafers. Their accurate and deft movements make it easier to conduct close-up inspections in confined and complex environments, reducing the possibility of human error and improving the accuracy of detection.
Drone integration has greatly improved industrial operations, lowering maintenance costs and downtime while raising yield and quality of output. Their quick and accurate data collection and analysis ensure ideal operating conditions and prevent unanticipated disruptions, which makes proactive maintenance possible.
Future Development
Although the relationship between drone technology and semiconductor manufacturing is still in its early phases, the future seems bright. Drone technology can be further optimized for semiconductor manufacturing through ongoing sensor precision and artificial intelligence improvements.
Future advances might involve the creation of specialized drones that are designed to fit the particular needs of semiconductor production processes, as well as the integration of more sophisticated sensor technology for more nuanced data collection.
With its variety of cutting-edge sensors, drone technology is revolutionizing a number of industries with its accuracy and adaptability. Drone integration in semiconductor manufacturing is not just a novel addition; it is a revolutionary strategy that is altering conventional practices and establishing new standards for operational excellence and product quality.
直接登录
创建新帐号