Introduction and Principle of Operation
Zeta converters are a type of DC-DC power converter that can convert voltage in both the step-up and step-down directions. They share traits with the Ćuk converter and were developed from a combination of buck and boost converters. Zeta converters are used in many different applications, such as battery-powered systems, solar energy harvesting, and telecommunications, because of their adaptability and excellent efficiency.
The Zeta converter's working principle relies on the use of magnetic components (inductors) and capacitors to store and transfer energy between its input and output sides. The energy storage phase and the energy transfer phase make up the two main components of the Zeta converter's operation. During the energy storage phase, the input power source charges the inductor, while the energy transfer phase involves transferring the stored energy to the output load via the capacitor.
The Zeta converter's capacity to maintain constant input and output currents is among its significant advantages. Low input and output current ripple, decreased electromagnetic interference (EMI), and better reliability are the effects of these characteristics. The Zeta converter can also offer input-output isolation upon request, thus increasing its adaptability in a variety of applications.
Circuit Topology and Key Components
Figure 20 shows another modification of the Ćuk converter obtained by swapping the positions of the transistor and inductor L1. This converter topology is similar to the SEPIC topology, so it is also called the “inverse SEPIC”.
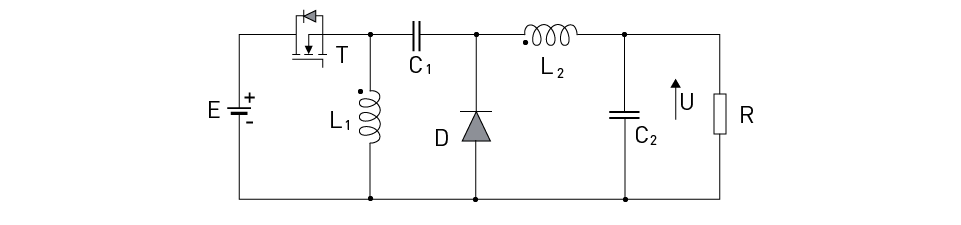
Figure 20: The ZETA converter circuit diagram
In steady-state, the average voltage across the inductors is zero, so the average voltage across the capacitor is equal to the DC voltage source. The capacitance of the capacitor can be considered sufficiently large to neglect the AC component of the voltage across it. Figure 17 shows the equivalent circuit of the SEPIC converter during the tON period. During this period, the voltages across the inductors L1 and L2 are:
$$U_{L1} = E$$ $$U_{L2} = U_{L1} + U_{C1} - U = E$$so that their currents linearly increase.
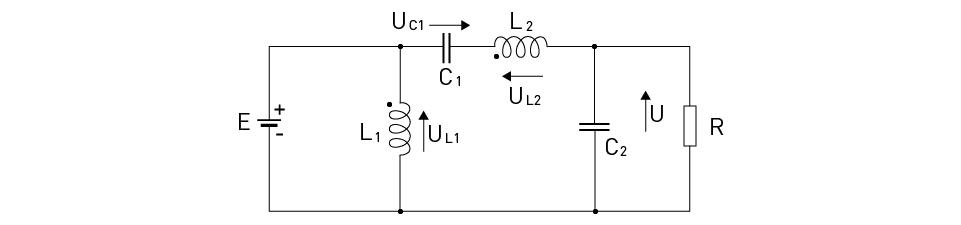
Figure 21: The ZETA converter circuit diagram – interval tON
Figure 22 shows the equivalent circuit of the SEPIC converter during the period tOFF. In this period, the voltages across inductors L1 and L2 are:
$$U_{L1} = -U_{C1} = -U$$ $$U_{L2} = -U$$so that their currents linearly decrease. Unlike the SEPIC converter, in the ZETA converter, the input current is discontinuous while the output current is continuous. Like in the SEPIC converter, the inductors in the ZETA converter can be magnetically coupled if inductors with equal inductance are selected, which reduces the alternating component of the current in individual inductors.
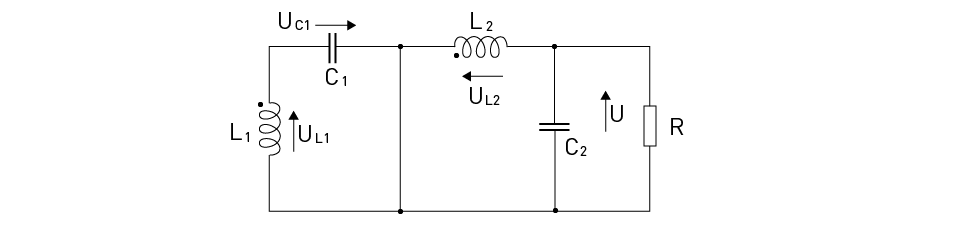
Figure 22: The ZETA converter circuit diagram – interval tOFF
In steady state, the average voltage value on the inductor is equal to zero:
$$E \cdot T \cdot d = U \cdot T \cdot (1 - d)$$ $$\Leftrightarrow U = E \cdot \frac{ d}{1 - d}$$which means that this converter operates as a buck-boost converter.
The Zeta converter is a fourth-order DC-DC converter characterized by its unique topology, combining elements from buck and boost converters. The key components of a Zeta converter include an input voltage source, two inductors (L1 and L2), two capacitors (C1 and C2), a diode (D), and a switch (S), typically a MOSFET or IGBT. The arrangement of these components is crucial to the performance and efficiency of the Zeta converter.
In a typical Zeta converter topology, the input voltage source is connected to one end of the first inductor (L1). The other end of L1 is connected to the switch (S), which controls the current flow through the inductor. The diode (D) is connected in parallel with the switch, with its anode connected to the common node between L1 and S and its cathode connected to the output side. The second inductor (L2) is connected between the cathode of the diode and the output voltage node. The capacitors (C1 and C2) are connected in series between the output voltage node and the ground, with their common node connected back to the input voltage source.
During the operation of a Zeta converter, the switch (S) alternates between ON and OFF states, controlling the flow of energy through the circuit. When the switch is ON, the input voltage source charges inductor L1, and energy is stored in its magnetic field. At the same time, the diode (D) is reverse-biased, and energy stored in inductor L2 is transferred to the output load through capacitor C2. When the switch turns OFF, the current in L1 continues to flow through the diode (D), charging inductor L2 and discharging capacitor C1. The energy stored in L2 is then transferred to the output load through capacitor C2.
The performance, efficiency, and size of the Zeta converter are directly influenced by the selection of inductors, capacitors, diode, and switch. To achieve the best performance, it is essential to use components with adequate current and voltage ratings and low parasitic elements. Furthermore, the smaller size of the magnetic components made possible by high-frequency switching might lead to a more compact design.
Continuous and Discontinuous Conduction Modes
Zeta converters, like other DC-DC converters, operate in two distinct conduction modes: continuous conduction mode (CCM) and discontinuous conduction mode (DCM). The choice of conduction mode depends on various factors, including the application, load requirements, and desired efficiency.
Continuous Conduction Mode (CCM): In continuous conduction mode, the current flowing through both inductors (L1 and L2) never drops to zero during the switching cycle. Higher power applications often choose CCM operation because it offers better power transfer efficiency and less output voltage ripple. Furthermore, compared to DCM, CCM has a simpler control and analysis process. CCM operation, however, could lead to higher inductor diameters and elevated core losses.
Discontinuous Conduction Mode (DCM): In discontinuous conduction mode, at some time during the switching cycle, the current flowing through one or both of the inductors (L1 and L2) drops to zero. For lower-power applications or when the load varies greatly, DCM operation is typically recommended. Compared to CCM, DCM can offer higher efficiency at low loads and smaller inductor sizes. However, DCM operation is accompanied by increased output voltage ripple and more complex control and analysis requirements.
The unique application and design requirements determine whether a Zeta converter should operate in CCM or DCM mode. In general, designers may use a combination of CCM and DCM operation or a control approach that switches between CCM and DCM as necessary for applications demanding high efficiency across a wide load range.
Optimizing the performance of a Zeta converter in a specific application requires an understanding of the distinctions between CCM and DCM operation. When choosing the best conduction mode, designers must take into account the load requirements, component sizing, efficiency, and output voltage ripple.
Design Considerations and Calculations
A variety of considerations and calculations go into designing an effective and dependable Zeta converter to ensure the right component selection and system performance. When constructing a Zeta converter, it's important to keep the following things in mind:
Input and output voltage specifications:Determine the necessary input and output voltage levels for your application to ensure you select appropriate component values and calculate the switch's duty cycle (D).
Output power and load requirements: Consider the output power and load requirements of your application, which will impact the converter's conduction mode (CCM or DCM) and the size of the inductors and capacitors needed.
Inductor selection and calculation: Choose suitable inductor values (L1 and L2) based on the desired conduction mode, input/output voltage specifications, and load requirements, which will impact the converter's efficiency, output voltage ripple, and transient response.
Duty cycle calculation: Calculate the switch's duty cycle (D) - the ratio of the switch's ON time to the total switching period - to determine the input-output voltage relationship necessary for proper converter operation.
Capacitor selection: Select the input (Cin) and output (Cout) capacitors based on desired output voltage ripple, transient response, and converter stability, as proper capacitor selection is vital for maintaining stable output voltage and minimizing voltage fluctuations.
Switching frequency: Choose an appropriate switching frequency considering factors such as efficiency, component size, and electromagnetic interference (EMI), as higher switching frequencies may enable the use of smaller inductors and capacitors, but may also result in increased switching losses and EMI.
Control strategy: Decide on a control strategy (voltage mode, current mode, or digital control) to regulate the converter's output voltage or current. Your control strategy will determine the complexity of the control circuit and its performance in different operating conditions.
Thermal management: Ensure proper thermal management by estimating power losses and guaranteeing adequate heat dissipation to maintain converter efficiency and ensure long-term reliability.
Efficiency and Losses
Efficiency is critical to power converter design, as it directly influences the overall system performance, power dissipation, and thermal management. The efficiency of a Zeta converter is the ratio of the output power to the input power, expressed as a percentage. To optimize efficiency, it is essential to understand and minimize the various losses that occur within the converter.
Conduction losses: When current passes through power electronic parts like switches, diodes, and inductors, conduction losses happen. These losses depend on the square of the current passing through them and are mostly caused by the resistive nature of the components. To minimize conduction losses, designers can select components with lower resistance, or they can improve the structure of the circuit to lessen parasitic resistances.
Switching losses: Switching losses occur during the transitions between the ON and OFF states of the power switches. During these transitions, voltage, and current are present simultaneously, which causes power dissipation. The switching frequency, the rate at which voltage and current change during transitions, and the properties of the switching devices all have an impact on switching losses. Designers can select switches with quicker switching speeds or enhance gate drive circuits to shorten transition times to reduce switching losses.
Diode reverse recovery losses: Diode-reverse recovery losses are associated with the diode's behavior during the reverse recovery process. The diode briefly experiences reverse current flow as it transitions from its conducting state to its blocking state. At high frequencies, the power dissipation caused by this current flow might be substantial. Designers can employ Schottky diodes or fast recovery diodes, which have incredibly rapid reverse recovery periods, to reduce reverse recovery losses. Core losses in magnetic components.
Core losses in magnetic components: Core losses occur in the magnetic cores of inductors and transformers due to the alternating magnetic fields. These losses are influenced by the converter's operating frequency, shape, and core material. By selecting the proper core materials and refining the magnetic component designs, designers can reduce core losses
Capacitor losses: Equivalent series resistance (ESR) and dielectric losses are the main causes of capacitor losses. These frequency-dependent losses can be reduced by using capacitors with lower ESR and appropriate dielectric materials.
Applications and Examples
Zeta converters are versatile and efficient DC-DC converters that offer various advantages, such as continuous input and output currents, high voltage conversion ratios, and the ability to step up or step down the input voltage. Due to these characteristics, Zeta converters find applications in a wide range of industries and systems. This section presents some typical applications and examples of Zeta converters.
Power supply applications: Zeta converters are widely used in power supply designs, providing regulated output voltages for various loads, such as digital circuits, analog circuits, and power amplifiers. They are ideal for applications requiring a stable output voltage over a wide input voltage range, such as battery-powered devices and automotive systems.
Renewable energy systems: In renewable energy systems, such as solar and wind power installations, Zeta converters can regulate and convert the varying input voltages from the energy sources into the desired output voltages. Their ability to handle wide input voltage ranges ensures optimal performance of connected loads and maximum power extraction.
Electric vehicle power systems: Zeta converters are useful in electric vehicle power systems, providing multiple voltage levels to power various subsystems, such as motor drives, auxiliary loads, and battery management systems. They efficiently convert high voltage from the battery pack to required lower voltages and are suitable for bidirectional power flow applications, including regenerative braking and battery charging. Telecommunication systems.
Telecommunication systems: Telecommunication systems use Zeta converters to provide stable power to sensitive electronic equipment, such as base stations, network switches, and routers. The continuous input and output currents of Zeta converters reduce electromagnetic interference (EMI) and noise generated in these systems, ensuring reliable and efficient operation LED lighting applications.
Zeta converters can drive LEDs with constant current, providing uniform brightness and long life in LED lighting applications. Their wide input voltage range makes them suitable for various lighting applications, such as automotive, street, and industrial lighting systems.
直接登录
创建新帐号