Test Set-Up and Procedures
In the development of digital isolators, evaluation and testing are critical elements to ensure reliability, performance, and compliance with specifications.
Essential Equipment and Set-Up Configurations
Test Equipment: To test digital isolators, the primary instruments are oscilloscopes, spectrum analyzers, signal generators, and network analyzers. These tools play a pivotal role in producing stimuli and calculating the isolator’s response precisely.
Power Supply and Load Conditions: Critical for testing, a stable power supply is essential due to the potential of fluctuating voltages to skew results. In aiding the assessment of the isolator’s performance under typical operating scenarios, configuring load conditions that mimic real-world applications plays a crucial role.
Signal Integrity Testing Set-Up: The set-up for assessing signal integrity includes equipment capable of producing high-speed digital signals and measuring factors such as jitter, rise time, and fall time. Pattern generators and high-bandwidth oscilloscopes are generally utilized.
Isolation and Insulation Test Set-Up: To evaluate the isolator's capacity to withstand high voltages, it is advisable to use high-voltage insulation testers. Applying a voltage higher than the isolator’s rated isolation voltage and measuring leakage current are involved in this process.
Automated Test Equipment (ATE): ATE systems are frequently used for complete and efficient testing. By automating the testing procedure, these systems enable quick testing of different parameters across various devices.
Ensuring Accurate and Reliable Results
Calibration and Standardization: To ensure accuracy, regular calibration of testing tools is important. Also contributing to the reliability of the results is the utilization of standardized testing procedures, in accordance with industry norms.
Repeatability and Reproducibility: Designed to be repeatable and reproducible, tests should yield the same results under consistent test conditions, even when conducted with varying equipment or by different operators.
Control of Environmental Conditions: During testing, environmental factors such as humidity, temperature, and electromagnetic interference should be controlled. Especially for stress testing, environmental chambers may be utilized for temperature and humidity control.
Data Analysis and Interpretation: As important as the testing itself, proper analysis and interpretation of the test data hold significance. Understanding the value of each tested parameter and how variations can affect the isolator's performance in real-world applications is involved in this.
Documentation and Reporting: It is essential to maintain detailed documentation of test procedures, configurations, and results. Along with supporting the traceability of the testing process, it also aids certification and compliance efforts.
Compliance and Standards
Adherence to industry norms and standards is not only a regulatory requirement but also a key factor in ensuring product quality and market acceptance in the development and testing of digital isolators.
Adherence to Industry Norms
Understanding Regulatory Frameworks: Specific regulatory frameworks governing electronic components exist in different industries and regions. Standards set by organizations such as the International Electrotechnical Commission (IEC), the Institute of Electrical and Electronics Engineers (IEEE), and Underwriters Laboratories (UL) are included in this for digital isolators. For legal compliance and market entry, it is critical to adhere to these standards.
Testing for Compliance: Involving a series of tests, compliance testing is designed to ensure that the digital isolators meet the specific needs set forth by these standards. Different aspects like electromagnetic compatibility (EMC), electrical safety, and environmental robustness are covered by these tests.
Certification Process: A critical step is obtaining certification from recognized regulatory bodies. Submitting the digital isolators to accredited testing facilities, where they undergo rigorous testing, is involved in this process. For launching products in certain markets, successful certification is often a prerequisite.
Continuous Compliance: Continuous monitoring and reevaluation are necessary for compliance, especially as standards and regulations evolve over time, emphasizing that compliance is not a one-time effort. Staying informed about changes in standards and ensuring ongoing compliance with their products is necessary for manufacturers.
Importance in Product Development and Market Acceptance
Building Trust with Customers: A testament to the quality and reliability of digital isolators is their compliance with industry standards. By building trust, it assures customers and end-users that the product fulfills performance and high safety benchmarks.
Facilitating Market Entry: A legal need for entering specific markets is to adhere to industry norms. Facilitating smoother market entry, products meeting these standards are more likely to be accepted by customers and regulatory authorities.
Risk Mitigation: The risk of product failures and associated liabilities is reduced by compliance. Protecting the manufacturer from legal and financial repercussions ensures that digital isolators are less likely to cause harm or malfunction.
Influence on Design and Quality Control: The design and quality control processes of digital isolators are often influenced by compliance requirements, necessitating rigorous testing and quality assurance measures. This results in enhancements to both manufacturing processes and product design.
Environmental and Stress Testing
In the evaluation of digital isolators, environmental and stress testing are pivotal components. Even under numerous challenging conditions, they can withstand and function reliably.
Assessing Reliability Under Various Conditions
Scope of Environmental Testing: Exposing digital isolators to a range of conditions encountered in real-world applications constitutes environmental testing for them. Such testing encompasses humidity fluctuations, pressure variations, extreme temperatures, and exposure to corrosive or reactive substances.
Temperature and Humidity Testing: To ensure reliable operation in both hot and cold climates, as well as in conditions with high moisture, digital isolators undergo testing for extreme temperatures and varying humidity levels. Thermal cycling and humidity resistance checks are typically included in these tests.
Mechanical Stress Testing: Critical mechanical stress tests, including shock and vibration testing, are imperative, particularly for isolators utilized in automotive, industrial, or aerospace applications, where mechanical stress is prevalent.
Altitude and Pressure Testing: Digital isolators undergo testing to ensure their ability to withstand environments at high altitudes or under unusual pressure conditions, without compromising their integrity or functionality, in relevant applications.
Identifying and Mitigating Potential Failures
Early Failure Identification: Before the deployment of digital isolators in actual applications, stress testing aids in determining potential failure points present in them. This encompasses the assessment of the durability of the packaging, the robustness of the isolation barrier, and the stability of the internal circuitry under stress.
Accelerated Life Testing: Conducting accelerated life testing, entailing subjecting isolators to conditions surpassing their standard operating range, facilitates the prediction of their lifespan and aids in the detection of long-term dependability concerns. Such capability permits manufacturers to implement essential adjustments in design or materials, thereby augmenting durability. A standard accelerated stress test for determining the lifetime of an isolator dielectric as a function of voltage is the time-dependent dielectric breakdown (TDDB) test.
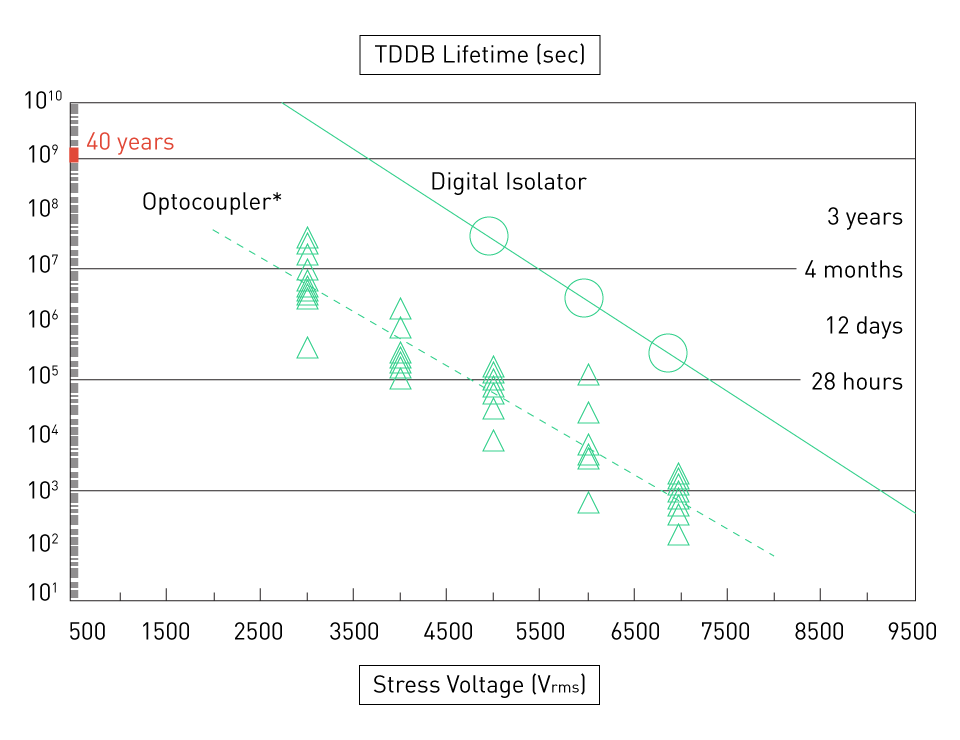
Figure 1: Optocoupler vs. Digital Isolator TDDB Lifetime
Failure Mode and Effects Analysis (FMEA): Integration of FMEA into the stress testing process helps in comprehending how diverse stress factors may cause failures, critically informing the development of techniques to lessen these failure modes.
Design Optimization: Feedback from environmental and stress testing informs the design process, enabling the optimization of digital isolators to improve their resilience and reliability. This could entail alterations in material selection, packaging methods, or circuit design.
Compliance with Application-Specific Standards: Digital isolators must meet environmental and stress testing standards for certain applications. For instance, compliance with standards dictating their ability to withstand the harsh conditions typical in automotive environments is a requirement for automotive-grade isolators.
直接登录
创建新帐号