Speed and Torque Characteristics
Having a deep understanding of the relationship between speed and torque in servo motors is crucial for effectively choosing and fine-tuning these motors for particular uses. A speed-torque curve often depicts the connection between these two factors, playing a crucial role in analyzing the motor's performance across various load situations.
Analysis of Speed-Torque Curves
The speed-torque curve provides a visual representation of the motor's ability to produce torque at different speeds. As speed increases, the available torque tends to decrease, and vice versa, according to the curve. The design of the motor and the control strategy employed influence this inverse relationship, which is a fundamental aspect of motor performance.
Starting torque at the base of the curve is essential for applications that need a powerful initial push or pull, especially when zero speed is involved. As the motor accelerates, the torque gradually decreases until it reaches a continuous torque rating at nominal speed. Beyond this point, the torque continues to decrease until it reaches its minimum at maximum speed.
Understanding the Trade-offs between Speed and Torque
The speed-torque curve highlights the numerous considerations when using servo motors.
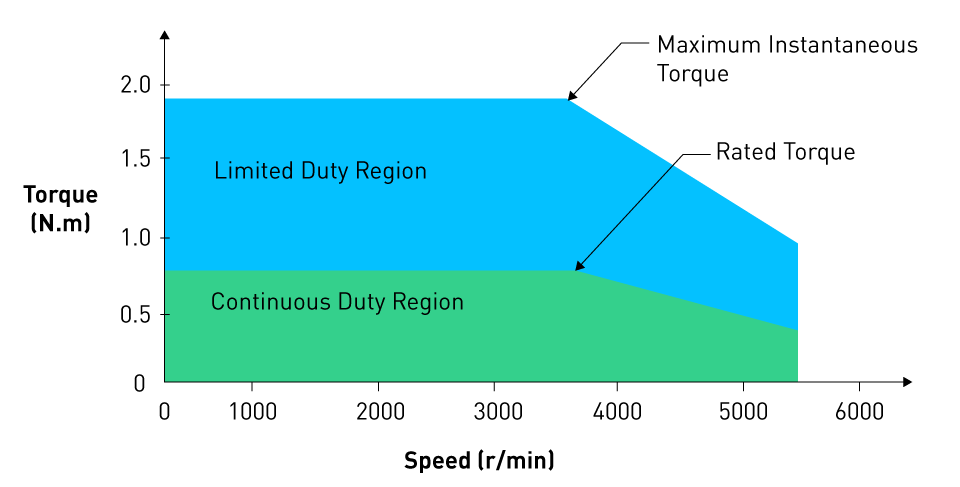
Figure 1: Typical Speed-Torque Characteristics of Servo Motors
High Torque at Low Speeds: With servo motors, high torque can be produced at low speeds. This makes them ideal for tasks that require significant force to initiate or move a heavy load, even when operating at slower speeds. Robotic arms and lifting mechanisms commonly use this capability to accurately control heavy loads.
High Speed with Lower Torque: With higher speeds, the torque output decreases, making it ideal for tasks requiring quick movements and lighter loads, such as spinning or rapid positioning in assembly lines.
We identify and differentiate between continuous and limited regions in the torque-speed curve. In the continuous region, the motor can operate without overheating. In the restricted area, the motor has a limited operating time.
Choosing the right servo motor for a specific application involves finding the perfect balance between the necessary speed and torque. When designing a system, it is important to take into account the operational profile of the application. These include acceleration requirements, typical and peak loads, and the desired speed range.
Engineers have the ability to enhance the motor's performance by utilizing gearboxes to boost torque at lower speeds or by choosing motors with custom windings and magnetic materials that are better suited for the specific application's needs.
In addition, sophisticated control strategies have the ability to adapt the motor's operation in real-time, ensuring that it maintains the best possible torque at different speeds. This results in improved performance throughout the motor's entire operational range.
Accuracy and Precision
Precision and accuracy play a crucial role in the performance of servo motors, particularly in applications that require precise positioning of components. Servo motors stand out from other motor types due to their exceptional accuracy and precision.
Factors Affecting Precision and Ways to Enhance It
There are various factors that can impact the accuracy of servo motors, such as mechanical backlash, system rigidity, and the quality of the feedback device. To further improve precision, it is important to consider and address these factors:
Minimizing Mechanical Backlash: The slight movement between gear teeth, known as backlash, can result in positional inaccuracies. By utilizing top-notch gears with minimal backlash or implementing gearless drive systems, this particular source of error can be significantly reduced.
Ensuring System Rigidity: Flex in the mechanical system can cause deviations in the motor's output, just like a materials engineer would want to avoid. Improving the stiffness of the mounting and coupling components ensures that the motor's movements are accurately transmitted to the load.
Utilizing High-Quality Feedback Devices: The precision of the feedback devices directly influences the accuracy of the servo system. By utilizing encoders or resolvers with enhanced resolution and accuracy, one can guarantee that the feedback precisely mirrors the motor's position or speed.
Temperature Compensation: Temperature fluctuations can have an impact on the precision of servo motors, as they can alter the resistance of electrical components and cause mechanical parts to expand. By incorporating temperature compensation into the control system, these effects can be mitigated.
Calibration and Tuning: Regular calibration and tuning of the feedback system and control parameters are essential for maintaining the servo motor's long-term precision. Adjusting the PID control settings may be necessary to account for wear and changes in the system's dynamics.
Efficiency and Reliability
Efficiency and reliability are crucial factors that greatly impact the performance, cost, and lifespan of servo motors. These factors are particularly important in industrial applications, where minimizing downtime and energy consumption can have a significant impact on finances.
Efficiency Considerations in Servo Motor Operation
Efficiency in servo motor operation is a metric that gauges the motor's ability to efficiently convert electrical energy into mechanical work. Efficiency is crucial in order to lower energy consumption and minimize heat generation, which can have a negative impact on motor performance and durability.
Optimized Design: Modern servo motors are meticulously designed with cutting-edge magnetic materials and finely-tuned windings to minimize electrical losses. With servo systems, motors are able to use just the right amount of power needed for the task at hand, preventing any unnecessary energy waste.
Regenerative Braking: Numerous servo systems use regenerative braking, in which the energy produced during deceleration is redirected back into the power supply rather than wasted as heat. This feature not only enhances the overall system efficiency but also lessens the thermal load on the motor.
Advanced Drive Electronics: The drive electronics are essential for optimizing the efficiency of servo motors. Advanced servo drives have the capability to dynamically adjust voltage and current to perfectly align with the motor's load demands. This results in minimal inefficiencies and maximized energy utilization.
Reliability Factors and Maintenance Requirements
Consistency is key when it comes to servo motors. Their reliability is measured by their ability to perform consistently over time, without any hiccups or failures. Proper maintenance is crucial for extending the operational life of a motor.
Robust Construction: Industrial applications demand servo motors to withstand rapid speed changes and continuous operation. With the use of top-notch bearings, seals, and construction materials, servo motors are able to function dependably in a wide range of environmental conditions.
Thermal Management: Efficient thermal management is essential for ensuring long-term reliability. Various features equip servo motors to prevent overheating, a common cause of motor failure. These features include heat sinks, cooling fans, and thermal overload protection.
Feedback System Integrity: The integrity of the feedback system is crucial for ensuring the precise functioning of servo motors. This includes component reliability, such as encoders or resolvers. Regular inspection and calibration of these components are crucial maintenance tasks to guarantee the system's overall reliability.
Predictive Maintenance: With the rise of smart sensors and IoT connectivity, predictive maintenance has become more practical. By closely monitoring the motor's condition in real-time, any potential issues can be detected early on. This proactive approach aids in preventing failures due to issues such as bearing wear or overheating, enabling the timely implementation of preventative measures.
直接登录
创建新帐号