Introduction to Servo Motors
Definition and Basic Principles of Servo Motors
A specific kind of electric motor called a servo motor is made to precisely control acceleration, velocity, and angular or linear position. Servo motors are unique among motor types because they have feedback control mechanisms that allow them to precisely control position within a closed-loop system. This system consists of the motor itself, an encoder or other feedback device, and an advanced controller that continually modifies the motor's output in response to the feedback signal in order to achieve and sustain the intended position or motion.
The continual monitoring and adjustment of the motor's position in relation to a commanded position, speed, or torque is the fundamental idea behind servo motor functioning. The controller compares the motor's current state with the intended state using real-time data obtained from the encoder's feedback. Any discrepancy generates error signals, which the controller then uses to adjust the motor's voltage and current to correct its motion. This dynamic process allows servo motors to precisely and quickly control their output, making them ideal for applications requiring precise movements.
Overview of Development and Technological Evolution
The advancement of servo motor technology directly influences the development of control theory, materials science, and electronics. Since their initial development, servo motors have found widespread use in a variety of industrial, commercial, and consumer applications. These include missile guidance and control, as well as radar antenna positioning in the military and aerospace industries.
Early servo systems were mostly used in areas where cost was not a major consideration because they were huge, expensive, and sophisticated, and they used analog electronics. However, the development of digital electronics and microprocessors in the second part of the 20th century marked a significant turning point. These technologies expanded the range of applications for servo motors, enabling the creation of servo drives and controllers that were more economical, effective, and small.
Improvements in permanent magnet materials—such as neodymium magnets—have fueled further progress by significantly increasing the power density and efficiency of servo motors. Furthermore, the accuracy, speed, and dependability of servo systems have increased thanks to the use of complex control algorithms and the integration of cutting-edge feedback devices.
Servo motors are now essential parts of a wide range of devices, including consumer electronics, automated assembly lines, robotic arms, and CNC machinery. Future servo motor technology promises even more performance and versatility thanks to ongoing advancements in power electronics, control schemes, and connections (such as Internet of Things integration).
Components of Servo Motors
Several essential parts make up servo motors, which are essential to contemporary automation and control systems and provide exact control over torque, speed, and position. Gaining an understanding of these parts and how they work is crucial to understanding how servo motors achieve their amazing performance.
Detailed Examination of Motor Components
Motor: Similar to a traditional motor in nature, the motor, the central component of the servo system, frequently operates precisely and effectively at high speeds to achieve greater accuracy. Both AC and DC servo motors have advantages in terms of power efficiency and speed control, depending on the particular application.
Encoder: The encoder is an essential part of the system; it generates signals that indicate the angle or displacement of the motor shaft in order to provide feedback on the motor's position. There are two types of encoders: incremental, which provides relative position data, and absolute, which provides distinct position values. This feedback determines the precise control capabilities of servo systems.
Driver: After processing the encoder position inputs with an integrated controller, the driver circuit constantly drives the motor in a closed feedback loop to reach the required position.
Gears: Although not necessary, servo motors often have additional gears attached to the shaft to decrease rotation speed and increase the motor's output torque.
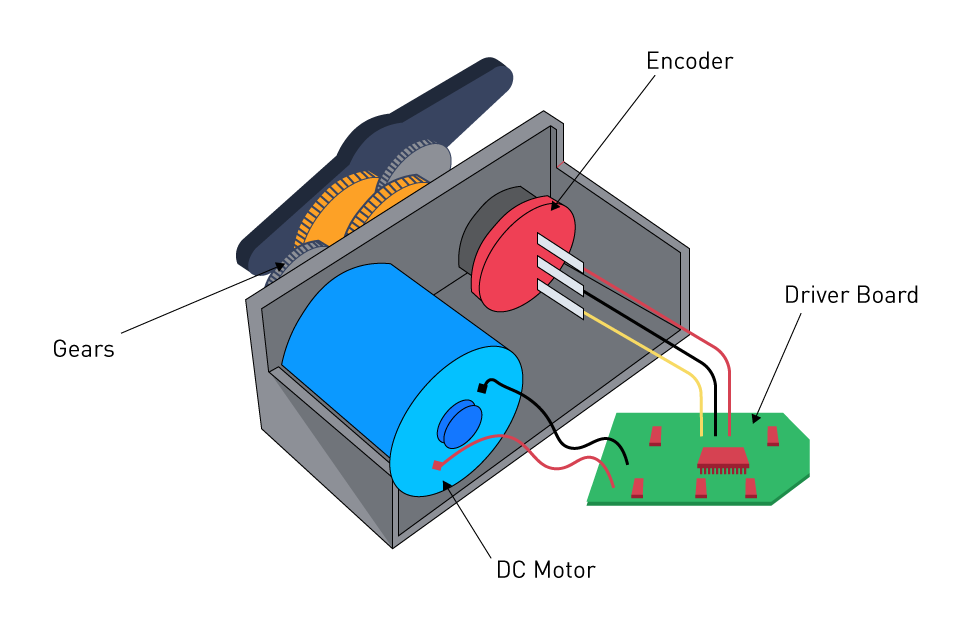
Figure 1: Servo Motor Components
Position Control
Position control is a distinguishing feature of servo motor technology. Servo motors are able to accomplish extremely precise placement by integrating the motor with its encoder and controller. The encoder reports the motor's actual position, which the system continuously compares to the desired position (the command input). In response to any divergence, the controller adjusts the power output to the motor to rectify the position. Servo motors may carry out intricate motion patterns with extreme precision and repeatability thanks to this closed-loop control mechanism.
The interconnected parts of servo motors function as a unit to provide accurate and effective control, a crucial feature for a variety of applications such as robotics, CNC machines, aerospace, and more. Developments in materials science, electronics, and software are fueling the continuous progress of servo motor technology, making it a vital component of contemporary automation and control systems.
Working Principle of Servo Motors
Servo motors are sophisticated electromechanical devices designed to precisely control acceleration, velocity, and angular or linear position. They are essential to many different applications because of their excellent precision and efficiency in performing intricate motion patterns. Three basic operating modes and the integration of mechanical and electrical components to achieve precise control are the foundations of servo motor operation.
Operating Modes
Speed Control: This mode manages the servo motor to maintain a set speed despite changing load circumstances. This is important for applications like fans and conveyor belts where the movement speed needs to stay constant.
Torque Control: The servo's torque control mode enables it to apply a steady torque when a continuous force is required, such as in pressing or winding applications. To compensate for load variations, the motor modifies its power output to maintain the predetermined torque level.
Position Control: The capacity of servo motors to precisely regulate position is their most prevalent and distinctive characteristic. In this mode, a command causes the motor to travel a predetermined distance or angle. This feature is crucial for robots, CNC machines, and other applications requiring precise movement.
How Servo Motors Achieve Precise Control
For servo motors, a closed-loop feedback system provides precise control. This system continuously checks the motor's output and instantly modifies it to conform to the input command that is required. This system's key components include:
Encoder: Sends information to the controller regarding the position or speed of the motor at any given time.
Controller: Analyzes the encoder's feedback and the input command to determine what has to be changed in order to match the desired command with the motor's output.
Amplifier: A bridge arrangement of switching transistors receives signals from the controller and supplies power to the motor in accordance with those signals, varying voltage or current to modify torque, position, or speed as needed.
This feedback loop ensures extremely precise control over the motor's movement of the motor by detecting and correcting any deviation from the target.
The Role of Electrical and Mechanical Systems in Operation
The smooth integration of mechanical and electrical systems is essential to the operation of servo motors. The driver regulates the electrical windings in the motor to produce magnetic fields that rotate the shaft. Even under high operating pressure, the motor's mechanical design, including its shaft, bearings, gears, and frame, maintains precision.
The electrical system provides the motor's mechanical parts with precise regulation through its control circuitry. This includes operating the motor at the appropriate speeds or torques, as well as starting, stopping, and maintaining it in place. Mechanical systems, on the other hand, ensure that the motor moves physically smoothly, effectively, and precisely in line with the electrical control inputs.
直接登录
创建新帐号