Safety Protocols and Procedures
Concerning the protection of maintenance staff and the prevention of damage to equipment, it is of the utmost importance to guarantee safety during motor maintenance and troubleshooting. To significantly reduce the likelihood of accidents and injuries, it is possible to establish and follow stringent safety regulations and procedures. These are the most important precautions to take for your own safety:
Lockout-Tagout (LOTO) Procedures: Implementing lockout-tagout procedures is crucial to ensure the correct shutdown and isolation of the motor and its control system before commencing any maintenance or troubleshooting. This prevents the motor from automatically energizing without warning, protecting workers from electrical shocks, burns, and mechanical accidents.
Personal Protective Equipment (PPE): It is extremely important that all individuals who are involved in the maintenance of motor vehicles are outfitted with the appropriate personal protective equipment. In order to defend against potential dangers such as sparks, hot surfaces, and electrical discharges, this includes flame-resistant clothing, face shields, safety goggles, and electrical gloves designed specifically for use with electrical equipment.
Electrical Safety Measures: It is of the utmost importance to implement electrical safety procedures since motor maintenance frequently involves contact with electrical components. This involves the use of insulated tools, the correct grounding of equipment, the provision of appropriate training for the individual on how to operate with hazardous voltage, and the guarantee that all electrical test equipment is rated appropriately for the voltages and currents that it may be exposed to.
Mechanical Safety Measures: It is critical to have mechanical safeguards in place to prevent harm to the body. Among them are the securing of rotating parts, the utilization of proper lifting techniques and equipment when working with heavy motor components, and the verification that all machine guards are in place and in excellent condition.
Hazard Communication: Communicating the dangers associated with specific motors and jobs in a clear and concise manner is crucial. This should include labeling all sources of energy, easy-to-understand instructions for safe operation, and signage that raises awareness among personnel about potential hazards.
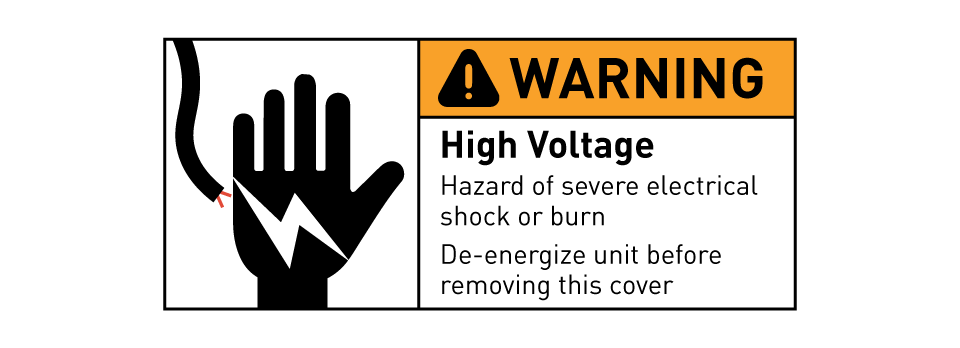
Figure 2: Example of a hazard label
Chemical Safety: When it comes to motor maintenance, the use of lubricants, cleansers, and other chemicals necessitates the implementation of appropriate handling methods. All employees involved in these activities should have access to Material Safety Data Sheets (MSDS), and they should take adequate precautions to ensure the safe handling and storage of chemicals, preventing any accidents or exposure to hazardous substances.
Training and Certification: It is imperative that all maintenance professionals participate in regular training sessions in order to guarantee that they are well-versed in the most recent safety rules and procedures. This training should cover topics such as responding to emergencies, using personal protective equipment (PPE) correctly, safely handling tools and chemicals, and staying up-to-date on regulatory compliance.
Emergency Procedures: It is essential to have emergency procedures that are both well established and continually rehearsed. Included in these should be procedures for dealing with electrical fires, injuries, and any other emergencies that may occur on the premises. At regular intervals, drills should be carried out to ensure that all personnel are aware of how to respond appropriately and in a timely manner.
Training and Awareness for Maintenance Personnel
Effective training and awareness programs are essential to ensure the safe execution of motor maintenance and troubleshooting. These programs ensure that all maintenance professionals possess the necessary information and skills to perform their duties safely and effectively. The following is an example of how these programs might be organized and carried out:
Comprehensive Training Programs: Both initial and ongoing training programs should cover all areas of motor maintenance and troubleshooting. These programs should include theoretical knowledge of motor mechanics, practical skills for maintenance operations, and detailed safety measures. The facility should adapt the training to the specific types of motors and machinery it uses.
Safety Certification: Employees should be encouraged or obliged to receive safety certification that is pertinent to their roles whenever it is possible to do so. When it comes to creating a baseline of safety knowledge that all people are required to acquire, certifications such as OSHA (Occupational Safety and Health Administration) training for electrical safety, mechanical safety, and hazardous materials handling are quite beneficial.
Regular Safety Drills: Carrying out regular safety exercises helps to reinforce the right safety procedures and ensures that people are able to respond effectively in the event of an emergency. The purpose of these drills is to replicate a variety of circumstances, such as electrical outages, mechanical problems, and fire crises.
Use of Visual Aids: The use of visual aids in the vicinity of the maintenance area, such as posters, warning signs, and instructional labels, can help to reinforce training and ensure that workers' safety is at the forefront of their minds. These tools have the potential to be especially useful in settings that utilize many languages or in which literacy problems may be present.
Mentorship and On-the-Job Training: By pairing new workers with veterans with years of expertise, mentorship can increase the effectiveness of safety training. Less experienced staff members can learn directly from professionals through this hands-on method, gaining insightful practical knowledge and safety recommendations that come only through experience.
Updates on Industry Standards: It is of the utmost importance to ensure that people are kept up to speed on the most recent industry safety standards and regulatory requirements. This is something that may be accomplished by participating at industry conferences, conducting regular seminars, and sending out newsletters.
Feedback Mechanisms: It is possible to contribute to the maintenance of a safe working environment by putting in place a feedback process that allows employees to report any issues they may have regarding safety and make suggestions for changes. This encourages a proactive approach to safety and ensures prompt resolution of any potential hazards.
Psychological Safety Training: In addition, it is essential to provide people with training in psychological safety, which encompasses the management of stress, the recognition of exhaustion, and the development of strategies for positive communication within teams. The implementation of psychological safety training contributes to the establishment of an atmosphere in which members of a team are able to openly address safety concerns without the fear of being blamed or punished.
直接登录
创建新帐号