Introduction to Motor Control
Overview and Importance of Motor Control in Various Applications
Motor control is a crucial component of modern automation and machinery. It plays a crucial role in a wide variety of applications, ranging from industrial manufacturing equipment to domestic appliances and automobile systems. The essence of motor control is the ability to manage the performance of electric motors in a precise and efficient manner. This comprises adjusting the speed, torque, and location of the machine in order to fulfill the requirements of a particular application. Motor control plays a crucial role in maximizing energy efficiency, enhancing product durability, and promoting user safety. In industrial settings, precise motor control is critical to achieve high production rates with minimal waste. On the other hand, in consumer electronics, it helps to improve gadgets' usefulness and efficiency.
Basic Concepts and Terminologies in Motor Control
To have a complete understanding of motor control, it is necessary to be familiar with the following fundamental ideas and terminologies:
Speed Control: The process of adjusting the rotational speed of a motor's output shaft to align it with the intended setpoint is known as speed control. In situations where process control is dependent on precise speed regulation, this is of the utmost importance.
Torque Control: Torque control refers to the process of adjusting the motor's torque output in applications that require certain force levels, such as lifting systems or starting large loads.
Position Control: When it comes to robotics, CNC machinery, and other precision applications, position control is an essential component since it guarantees that the motor will reach and remain in a particular position.
Open-Loop Control: An open-loop control system operates the motor according to predetermined conditions without providing feedback on the result. This type of control method is appropriate for straightforward applications in which precise control is not essential.
Closed-Loop Control: A closed-loop control system uses feedback systems to adjust the motor's operation based on real-time data. This type of control enables precise control over the motor's speed, position, and torque.
PID Control: PID Control is a sophisticated closed-loop control approach that involves proportional, integral, and derivative aspects. Its purpose is to fine-tune the motor's reaction to changes in operating conditions.
PWM (Pulse Width Modulation): By adjusting the width of the pulses represented in a waveform, a technique known as Pulse Width Modulation (PWM) allows for effective control of both speed and torque. The motor receives power control from this technique.
Types of Motor Control Systems
Motor control systems significantly influence the control and operation of motors in various applications. Generally, we can classify these systems into two main categories: electronic and electromechanical. Each of these categories has its own set of characteristics, advantages, and uses.
Electronic
Electronic motor control systems use solid-state electronics to manage the operation of motors. This category includes a wide variety of technologies, ranging from straightforward diode rectifiers to intricate programmable logic controllers (PLCs) and digital signal processors (DSPs). In addition to their precision and adaptability, electronic systems also have the capacity to interface with contemporary industrial networks and automation systems. This is the primary advantage of electronic systems. They provide exact control over the motor's speed, position, and torque by utilizing complex algorithms and feedback mechanisms.
Electronic controllers are able to accommodate a wide range of motor types, including servo motors, stepper motors, alternating current (AC) motors, and DC motors. There are numerous instances that illustrate the flexibility of electronic systems. Some examples include variable frequency drives (VFDs) for alternating current (AC) motors and pulse width modulation (PWM) controllers for direct current (DC) motors. Not only do these technologies improve the performance and efficiency of motor operations, but they also contribute to the reduction of energy consumption as well as the decrease of the amount of wear and maintenance that is required.
Electromechanical
Electromechanical motor control systems use mechanical components and electrical circuits to control the operation of a motor. When it comes to starting, stopping, and reversing motors, these systems frequently make use of contactors, relays, and timers. Before the widespread use of electronic systems, electromechanical controls served as the basis for motor control. Applications that prioritize simplicity and robustness continue to utilize these controls.
The durability and ease of maintenance of electromechanical systems are two of the reasons why they are highly regarded, despite the fact that they are less exact than their electronic counterparts. Because they are less susceptible to environmental factors such as heat and dust, they are suitable for use in severe industrial situations. Additionally, electromechanical systems have the potential to provide a solution that is both cost-effective and efficient for applications that do not require the complex control capabilities that electronic systems would normally have.
Components of Motor Control Circuits
Motor control circuits, which operate motors effectively and accurately, comprise essential components, each of which plays a crucial role in the entire process. Controllers, sensors, and actuators are the components that make up the backbone of any motor control system. These components are included in an assortment of components. To construct efficient motor control circuits, it is critical to have a thorough understanding of each component's function and role.
Detailed Description of Components
Controllers: Controllers are the most important component of the motor control circuit, acting as the "brain." It is responsible for processing sensor input signals, implementing control algorithms, and generating output commands for various actuators. Basic microcontrollers, programmable logic controllers (PLCs), and digital signal processors (DSPs) are all examples of controllers. Controllers can also be as complex as they are basic. The application's requirements determine the specific tasks they perform, like speed regulation, position control, or torque management.
Sensors: Sensors are responsible for providing real-time data on the surroundings and the motor's operation parameters. Common types of sensors used in motor control circuits include speed sensors, position encoders, current sensors, and temperature sensors. These sensors provide the controller with information, allowing it to make decisions and modifications based on accurate data in order to maintain the required level of motor performance. A speed sensor, for example, would detect motor speed variations and then communicate this information to the controller. The controller then makes adjustments to the power output in order to keep the speed constant.
Actuators: Actuators are the components that execute the controller's commands, thereby directly influencing the motor's operation. In motor control circuits, actuators commonly refer to power electronics components such as transistors, thyristors, and relays. Actuators regulate the power delivery to the motor. In order to achieve exact control over the motor's speed, torque, and position, these devices have the capability to turn the power on and off, modify the power levels, or invert the direction of existing current.
Function and Role of Each Component in a Motor Control Circuit
Within a motor control circuit, the interaction that takes place between controllers, sensors, and actuators is absolutely necessary for the circuit to function correctly. The controller analyzes data from the sensors to determine whether the motor is operating within the specified parameters. If the controller detects deviations, it calculates the required adjustments and signals the actuators to adjust the motor's power supply accordingly. It is the responsibility of this closed-loop control system to guarantee that the motor accurately responds to both external commands and internal feedback, which ultimately results in optimal performance under a variety of scenarios.
In a conveyor belt system, for example, sensors are responsible for monitoring the speed of the belt as well as the conditions of the load. Meanwhile, the controller is responsible for adjusting the speed of the motor in order to maintain a constant product flow rate, regardless of the load. In order to achieve these modifications, actuators are responsible for modulating the motor's power, which guarantees that the system will function smoothly and effectively.
Principles of Motor Control
It is vital to have a solid understanding of the fundamentals of motor control in order to design and create systems that are capable of managing the functioning of motors in a precise and efficient manner. In order to ensure that the motor is operating at its full potential across a wide range of applications, these principles serve as a guide for the design and execution of control strategies that regulate motor speed, torque, and direction.
Operating Principles for Controlling Motor Speed, Torque, and Direction
Speed, torque, and direction are the three most important components of motor performance, and the primary objective of motor control is to manage all three of these aspects.
Speed Control: Regulating the power delivery to the motor is necessary to adjust its speed. Variable frequency drives (VFDs), which manipulate the power supply's frequency, typically accomplish this for alternating current (AC) motors. Controlling the speed of DC motors can be accomplished by adjusting the voltage that is applied to the motor or by employing pulse width modulation (PWM) techniques, which are designed to manage power in an effective manner.
Torque Control: The torque, which is the rotational force that is created by the motor, is directly related to the current that is flowing through the windings of the motor. Controlling this current enables precise management of the motor's torque. This is an essential feature for applications that require powerful interactions with physical systems, such as lifting or propulsion.
Direction Control: The conventional method for achieving direction control involves changing the direction in which current flows through the motor's circuit. DC motors can achieve this by flipping the polarity of the applied voltage. With AC motors, phase sequence adjustments can reverse the motor's direction.
Overview of Open-loop and Closed-loop Control System
The existence or absence of feedback mechanisms distinguishes the two primary categories of motor control systems. These categories are open-loop and closed-loop systems.
Open-Loop Control Systems: In an open-loop system, the performance of the control action remains unaffected by the outcome. This implies that the system operates based on preset settings, making no adjustments to accommodate load fluctuations or environmental conditions. Open-loop systems are both easier to use and less expensive than closed-loop systems, but they do not possess the same level of precision or adaptability. They are ideal for inclusion in applications in which precise control of speed, torque, or position is not of the utmost importance.
Closed-Loop Control Systems: Closed-loop control systems use feedback mechanisms to adjust the control action based on the output. Sensors monitor the motor's performance and provide real-time data to the controller. The controller then makes adjustments to the motor's function in order to achieve the desired result. This feedback loop allows for precise control over the motor's speed, torque, and direction by accounting for disturbances and load variations. Robotic arms, CNC machines, and automated assembly lines are examples of applications that require a high level of precision and hence require closed-loop systems.
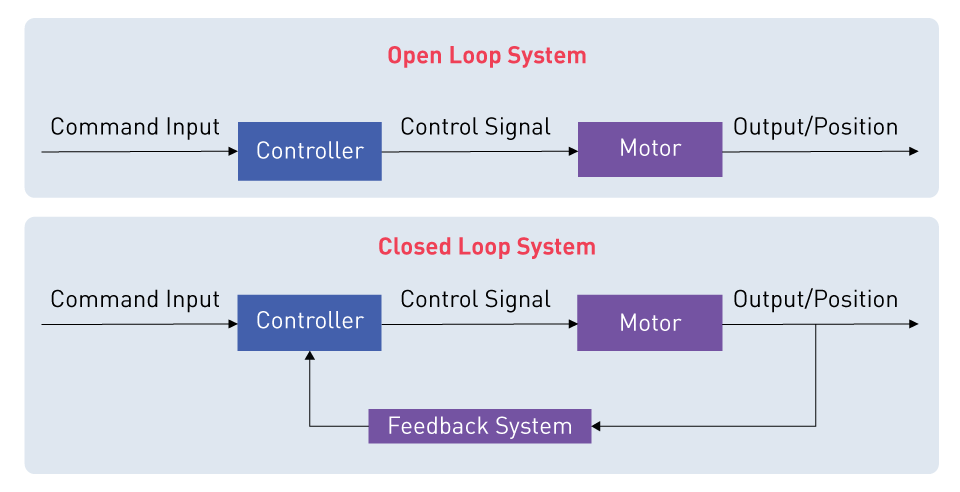
Figure 1: Open-Loop versus Closed-Loop System
Advanced Control Techniques
The use of sophisticated control techniques is critical in the field of motor control because they improve performance, precision, and efficiency in a variety of applications. These techniques, which include fuzzy logic, PID control, and model predictive control (MPC), provide complex solutions for the management of motor operations, particularly in circumstances that are difficult to work in.
PID (Proportional, Integral, Derivative) Control and Its Applications
Motor control systems widely recognize PID control as one of the most widespread and efficient control schemes on the market. It adjusts the motor's input based on three parameters: the proportional (P), integral (I), and derivative (D) terms. There are three types of errors: the proportional term handles the current error, the integral term takes into account the accumulation of errors from the past, and the derivative term forecasts errors that will occur in the future. Examples of applications that make extensive use of this control approach include conveyor belts, robotic arms, and CNC machines. These are all examples of applications that require precise control of speed and position. PID controllers are highly regarded for their adaptability and ability to significantly increase system stability and response time. As a result, they are ideal for dynamic systems with varying loads and operating conditions.
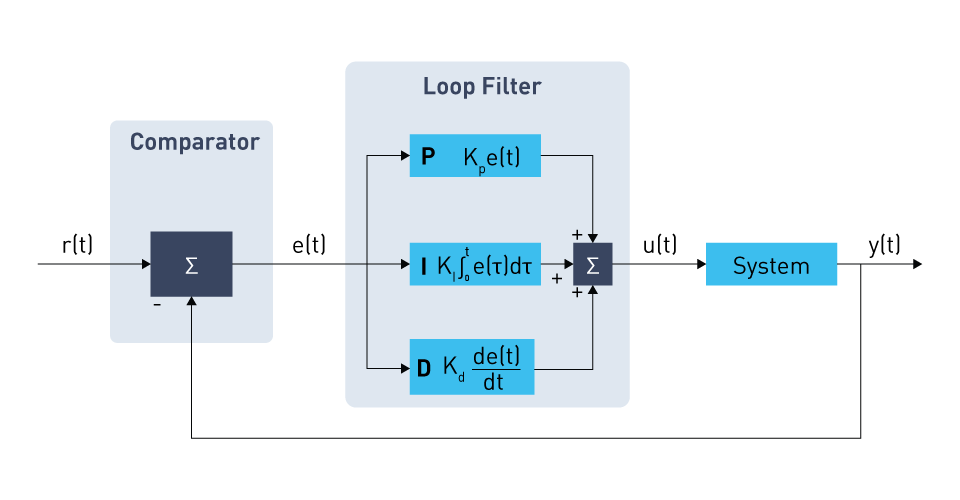
Figure 2: Depiction of the PID Control Loop in the Time Domain
The system subtracts the sampled signal, y(t), from the input signal r(t), which could be the controller's torque or speed demand. This is something that we can observe. The symbol e(t) denotes the produced error or difference, which the PID filter then sends. The three components of the PID filter individually modify the error signal, subsequently combining the transformed value with the other values. The motor will adjust to a new value, known as the control variable, as a result. This shifts the value of y(t) towards the desired value, represented by r(t). The PID filter in the loop ensures that y(t) closely follows r(t) and minimizes e(t) close to 0. This ensures that the loop is functioning properly.
Fuzzy Logic Control
Fuzzy logic control, by addressing the uncertainties and imprecisions inherent in the control process, provides an alternative to conventional binary logic control approaches. This method replaces the commonly used "true or false" (1 or 0) boolean logic with the "degrees of truth" approach. Fuzzy logic controllers, also known as FLCs, are especially helpful in situations where the mathematical modeling of the system is either complicated or completely lacking. FLCs are able to efficiently handle nonlinearities and changeable system dynamics because they use a set of rules that are based on expert knowledge. This makes them excellent for applications such as automobile control systems, which are subject to rapid changes in the operating environment.
Model Predictive Control (MPC)
For the purpose of predicting future states and controlling activities, MPC is a sophisticated control approach that makes use of a model of the motor and the load it is carrying. By optimizing these projected states against a set of limitations (such as maximum torque or speed limits), MPC is able to determine the optimal control inputs that will result in the desired outcome. This strategy's effectiveness is particularly high in systems where it is possible to forecast and minimize the effects of future disruptions or changes. MPC finds extensive application in industries like chemical processing and aerospace, where safety, efficiency, and precision hold paramount importance.
Techniques for Optimizing Control and Response in Challenging Environments
Advances in control algorithms and technology continuously push the boundaries of motor control further into the future. For instance, adaptive control approaches adjust the control parameters in real time, taking into account the performance of the system under study. This allows for the processing of changes in the motor's characteristics or the load it is carrying. In a similar manner, networked control systems connect motors, sensors, and actuators through a communication network. This allows for coordinated control of distributed systems. When applied in contexts that are both complex and subject to rapid change, such as automated manufacturing plants or autonomous cars, these strategies offer benefits that boost performance.
Driving and Controlling Stepper Motors
In applications that require precision control, stepper motors are an indispensable component. They are recognized for their capacity to transform electrical pulses into discrete mechanical movements. Complex methods enable the driving and controlling of stepper motors, enabling their use in a wide range of applications that require accurate positioning and repeatability.
Operating Modes
Different modes of operation are available for stepper motors, and each mode offers a distinct set of benefits based on the requirements of the application:
Full Step: The motor moves through its basic step angle, which is typically 1.8 degrees for a 200-step motor, for each and every pulse that it receives when it is operating in full step mode. This mode provides the highest possible torque because it energizes the greatest possible number of windings without those windings overlapping. This material is excellent for applications that require high speed and torque, although it does not necessarily require high precision.
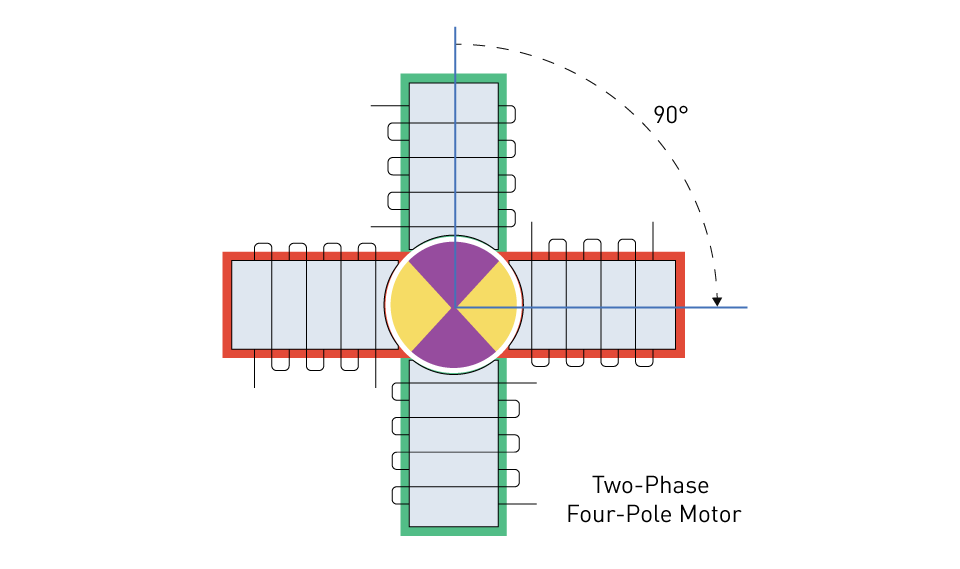
Figure 3: Full-Step Mode
Half-Step: Half-stepping is a technique that involves alternating between energizing two phases and energizing a single phase. This technique efficiently reduces the step angle by half while simultaneously increasing the resolution by two times. Compared to full stepping and other modes, this mode improves smoothness and spatial resolution but decreases torque.
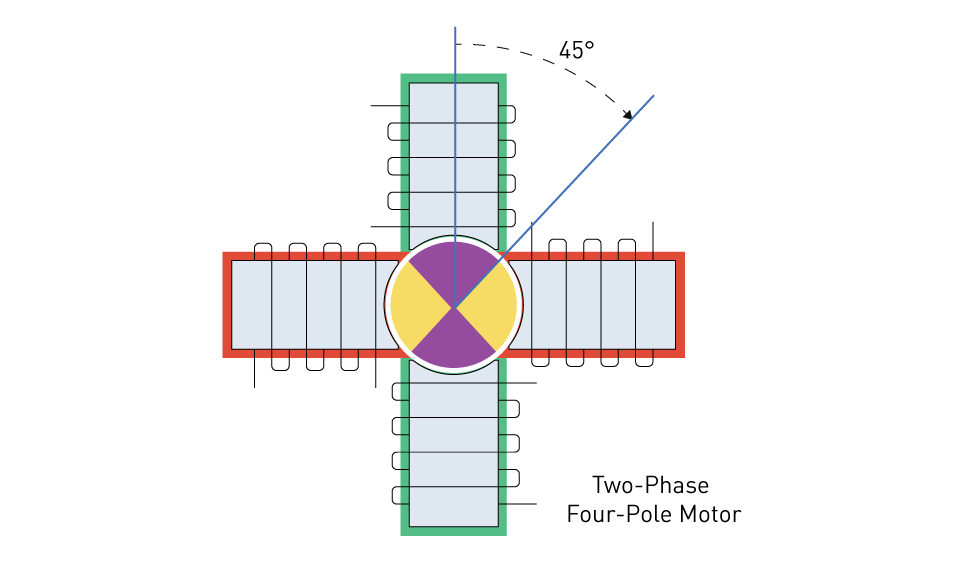
Figure 4: Half-Step Mode
Microstepping: This technique separates each entire step into smaller steps, resulting in a significant increase in the motor's resolution. The stepper motor is controlled in this mode to achieve smoother motion and more precise control, but at a somewhat reduced torque. This mode is utilized to achieve these goals. The microstepping technique is especially useful for applications that require extremely precise positioning and fluid movement.
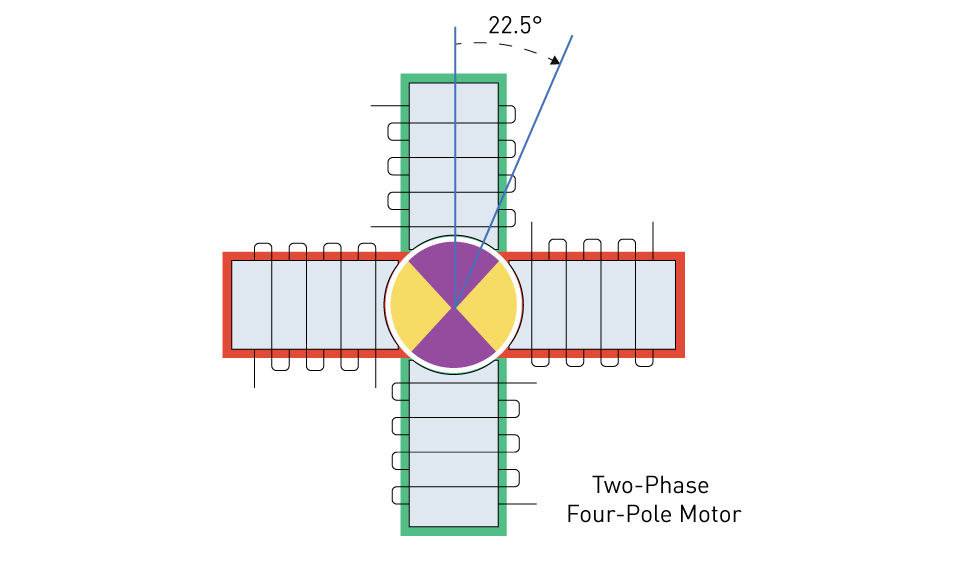
Figure 5: Microstepping Mode
Stepper Motor Driver Types
Different kinds of drivers, which are necessary for determining the operating mode and performance of stepper motors, make it easier to control stepper motors. These drivers include all of the following:
Current-Limiting Drivers (L/R Drivers)
- Description: L/R drivers are able to exert direct control over the current flowing through the motor windings using resistors or rheostats. Applying a constant voltage across the windings accomplishes this. Despite the fact that it is less efficient and produces a substantial amount of heat, this method is easier and may be less expensive.
- Application: Applications typically use them when cost is a key consideration and precise control of motor speed and torque is less crucial.
Chopper Drive Drivers
- Description: These drivers control the current flow by rapidly switching the applied voltage to the motor coils on and off, a process known as chopping. By modifying the on-off ratio, also known as the duty cycle, it is possible to get more exact control of the current and, consequently, the torque, which in turn improves performance.
- Application: CNC machines and robots are two examples of applications that make extensive use of chopper drives. Applications that demand enhanced efficiency and control employ these drives.
Speed Control and Regulation in DC Motors
The regulation of the speed of direct current (DC) motors is an essential component in a wide variety of applications, ranging from consumer electronics to pieces of industrial machinery. Effective speed control can enhance the performance, efficiency, and longevity of a DC motor. This section investigates approaches and methods for controlling and regulating the speed of DC motors, specifically focusing on pulse width modulation (PWM) techniques.
Techniques and Methods for Speed Control of DC Motors
The voltage across a DC motor's terminals primarily determines its speed. Therefore, we can control the motor's speed by adjusting the supply voltage. To accomplish this, there are a few different approaches:
Voltage Control: Motor speed can be linearly adjusted by changing voltage. This is accomplished through the use of voltage control. This is typically accomplished through the utilization of electrical circuits or variable resistors that are capable of modulating the voltage.
Field Current Control: Another method for controlling the speed of a DC motor is to vary the current that flows through its field winding. The speed can be increased by decreasing the field current, and vice versa. This strategy is especially helpful for motors that require a wide range of speed control since it allows for greater flexibility.
Armature Resistance Control: Armature resistance regulation, which involves adding resistance in series with the armature circuit, can restrict the amount of current that flows through the motor. This process generates heat in the resistors, leading to a decrease in efficiency compared to other approaches due to power loss.
Use of Pulse Width Modulation (PWM) Methods
One method that stands out as particularly effective for controlling the speed of DC motors is pulse width modulation (PWM). The duration of the "on" period, also known as the pulse width, determines the average voltage and, consequently, the motor's speed. This approach includes switching the supply voltage to the motor on and off at a high frequency.
Efficiency: The pulse width modulation (PWM) method is more energy-efficient than resistive methods because it modulates speed without a considerable loss of power, in contrast to the resistive methods.
Precision: Pulse width modulation (PWM) achieves precision by enabling fine-grained control over motor speed. This allows for precise adjustments, which are essential for applications such as robotics and automated systems.
Versatility: Electronic circuits like microcontrollers can implement pulse width modulation (PWM), making it adaptable to a wide range of applications and simple to link with other control systems for comprehensive motor management.
Dynamic Response: The rapid switching action of pulse width modulation (PWM) gives a quick reaction to speed adjustment orders, which enables dynamic speed adjustments that are suitable for real-time control settings.
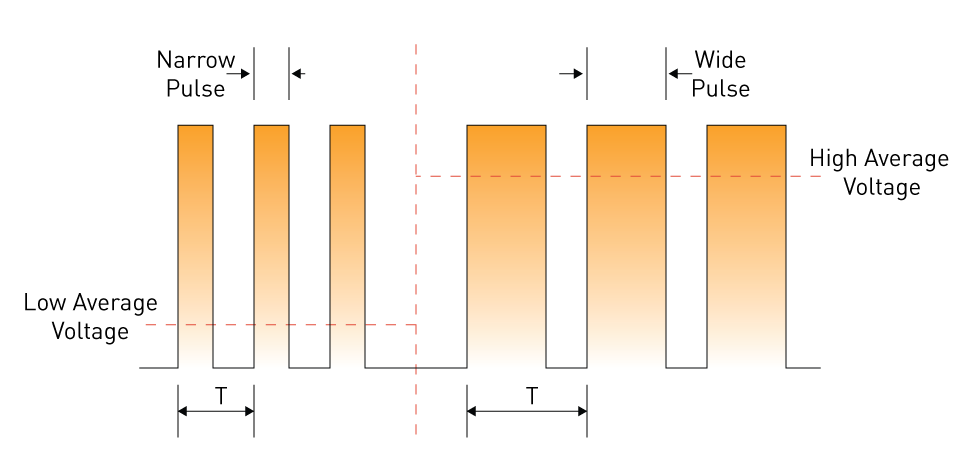
Figure 6: Depiction of Pulse-Width Modulation
Whenever pulse width modulation (PWM) control is applied, the controller circuit will chop the supply voltage of the motor at a specific frequency. A higher average voltage and a greater amount of current are delivered to the motor as a result of wider pulses, which reflect a longer time of voltage being supplied to the motor during each chopping cycle.
Microcontrollers or integrated circuits designed specifically for motor control are often used to generate pulse width modulation (PWM). These devices are able to change the duty cycle of the pulses based on control inputs or feedback from the motor system. Because of its versatility and efficiency, pulse width modulation (PWM) is the method of choice for controlling the speed of DC motors in modern applications.
Speed Control and Regulation In AC Motors
Alternating-current (AC) motors were a huge step forward in motor technology because they offered versatility and efficiency across a wide range of applications. This event marked a significant achievement in motor technology. When it comes to maximizing performance in industrial automation, heating, ventilation, and air conditioning (HVAC) systems, and variable-load applications, effective speed control and regulation of AC motors are essential. This section analyzes the approaches and methods used for speed control of alternating current (AC) motors, emphasizing the crucial role of variable frequency drives (VFDs).
Techniques and Methods for Speed Control of AC Motors
There are several ways to control the speed of alternating current (AC) motors, each tailored to the specific type of AC motor and its application requirements:
Voltage and Frequency Control: Because the speed of an alternating current (AC) motor is directly proportional to the supply frequency and inversely proportional to the number of poles, the speed of the motor may be successfully controlled by adjusting the voltage and frequency that are supplied to the motor. The motor is able to function at a variety of speeds without sacrificing its torque because of this technology.
Slip Control: When it comes to squirrel cage induction motors, managing the slip, which refers to the difference between the rotor speed and the synchronous speed, provides an additional method for adjusting the speed of the motor. It is possible to control the slip in order to change the motor's speed. Modifying the external load or varying the resistance in the rotor circuit can accomplish this.
Pole Changing: Certain alternating current (AC) motors are constructed with variable pole numbers that can be changed in order to alter the motor's synchronous speed. This technology provides discrete speed steps for applications that require a limited range of speed settings.
Variable Frequency Drives (VFDs)
Variable-frequency drives are at the forefront of technologies that control the speed of alternating current (AC) motors because they offer precision, efficiency, and flexibility that no other method can match.
Principle of Operation: Variable frequency drives (VFDs) can control the speed of an alternating current (AC) motor by adjusting the frequency and voltage of the provided electricity. Variable frequency drives (VFDs) have the ability to fine-tune the motor speed and torque to meet the application's requirements by altering these parameters.
Energy Efficiency: Variable Frequency Drives (VFDs) can drastically reduce energy consumption by allowing motors to operate only at the required speed. This is especially beneficial in applications that involve varying loads and do not require full speed all the time.
Enhanced Control: By enabling smooth acceleration and deceleration control, VFDs enhance control by reducing the mechanical stress on the motor and any associated equipment. When it comes to applications that require delicate handling, accurate positioning, or the coordinated operation of several motors, this exact control is absolutely necessary.
Application Versatility: It is possible to employ variable-frequency drives (VFDs) in a wide variety of industries, from regulating pumps and fans in heating, ventilation, and air conditioning (HVAC) systems to driving conveyors in industrial plants. Given their capacity to enhance process control while simultaneously lowering operational costs, they are a vital component in contemporary industrial settings.
Integrated Motor Controllers
Integrated motor controllers have emerged as a significant advancement in motor control technology's ongoing evolution. These controllers combine control functions and drive circuitry into a single small unit, making them a significant step forward. The purpose of these integrated systems is to simplify the process of motor control, which will result in an increase in both functionality and efficiency across a wide variety of applications.
Integrated motor controllers combine all of the fundamental motor control components into a single, coherent module. These components include driver circuits, power electronics, and feedback mechanisms. This integration simplifies installation, configuration, and operation, particularly beneficial in scenarios where space and simplicity are key considerations.
Functionality and Advantages
Compact Design: With their compact design, integrated motor controllers lower the footprint that is necessary for motor control systems. This is accomplished by combining many components into a single unit. When it comes to applications that require a small amount of space, such as robotics, portable gadgets, and automotive applications, this compactness is absolutely essential.
Ease of Use: It is easier to use these controllers because they reduce the number of external components and wires that are required, which in turn simplifies the design and implementation of motor control systems. This ease of use shortens the amount of time required for creation and significantly reduces the complexity of troubleshooting and maintenance.
Advanced Features: Integrated motor controllers typically include advanced features such as PID control, regenerative braking, and fault detection. These controllers also typically incorporate other advanced control algorithms and features. These attributes improve the motor's performance, efficiency, and dependability.
Versatility: Integrated motor controllers are capable of driving a wide variety of motor types, including brushless DC (BLDC) motors, stepper motors, and direct current (DC) motors. This breadth of capabilities allows them to serve a wide variety of applications, ranging from precise medical devices to industrial machinery.
Applications
The precision of control, compactness, and ease of integration are three of the most important factors in the application of integrated motor controllers, which find use in a variety of industries. In the realm of consumer electronics, they make it possible to reduce the size of gadgets like drones and handheld tools using smaller components. In the field of industrial automation, they contribute to the dependability and effectiveness of robotic arms and transportation systems. Applications in the automotive industry benefit from their durability and compact size, which are necessary for electric vehicle powertrains and accessory drives.
Technological Trends
Ongoing advancements in semiconductor technology and power electronics continuously enhance the capabilities of integrated motor controllers. These controllers are able to handle greater currents and voltages without sacrificing their performance or reliability as a result of innovations in materials and design that are pushing the boundaries of efficiency, heat management, and power density.
直接登录
创建新帐号