Introduction to DC Motors
Basic Concept and Operation of DC Motors
Electric motors that run on direct current are known as direct-current (DC) motors. These motors can convert electrical energy into mechanical energy by combining magnetic fields and currents. The stator, which is responsible for maintaining a steady magnetic field, and the rotor, also known as the armature, which rotates inside the magnetic field, are the two basic components that make up DC motors at their core. Because of the flow of direct current through the armature winding, the motor is able to generate an electromagnetic force, which in turn causes the motor to rotate.
When placed within a magnetic field, a current-carrying conductor experiences a force that is perpendicular to both the magnetic field's direction and the current's. DC motors operate based on this fundamental law, which is called Lorentz's force law. This force generates torque on the armature, causing it to revolve. By adjusting the amount of current that is flowing through the armature winding, it is possible to make adjustments to the magnitude of this torque and, as a result, the speed of the motor.
Historical Context and Evolution
Direct-current (DC) motors have played a crucial role in the advancement of electrical engineering and technology throughout history. Michael Faraday's discovery of electromagnetic induction in 1831 led to the construction of the first useful DC motors in the 19th century. An idea that would eventually result in the development of the electric motor was based on Faraday's concepts, which set the framework for the transformation of electrical energy into mechanical energy.
The Gramme machine was the first electric machine that was capable of functioning effectively as a motor. Zenobe Gramme, a Belgian electrical engineer, invented it in 1873. This development demonstrated the usefulness of electric motors and sparked further innovations. Inventors like Thomas Edison and Nikola Tesla were making substantial contributions to the rapid development of electric power systems by the late 19th century. These contributions included significant breakthroughs in direct-current magnetic motor technology.
Refinement of direct current (DC) motors occurred during the beginning of the 20th century. The introduction of superior materials and the incorporation of components like commutators and brushes accomplished this. As a result, DC motors were easier to use and more dependable. In a variety of applications, including industrial machinery, transportation, and domestic appliances, DC motors have become increasingly popular as a result of these improvements.
The ongoing development of DC motor technology during the 20th century and into the 21st century led to the development of brushless DC motors. Advancements in semiconductor electronics made this possible. By eliminating the need for physical commutation, these motors offer various advantages over their brushed counterparts, including improved efficiency, dependability, and decreased maintenance.
Operating Principles
As a result of the interplay between magnetic fields and electrical currents, direct current (DC) motors are able to convert electrical energy into mechanical energy. This is accomplished through the fundamental principles of electromagnetism. This section discusses the formation of rotational motion, the involvement of electromagnetic fields, commutation, steady-state and transient behaviors, and regenerative and dynamic braking mechanisms. These fundamental operating principles are what make it possible for this energy conversion to take place.
How DC Motors Generate Rotational Motion
The interplay of two magnetic fields is what causes DC motors to generate rotational motion. The current flowing through the armature windings creates one magnetic field, while either permanent magnets or field windings in the stator generate the other magnetic field. The armature windings are responsible for the flow of electric current that enters the motor through the brushes and commutator. The interaction between this current and the stator's magnetic field generates a force on each of the armature's conductors. This force is perpendicular to both the direction of the current and the magnetic field, which causes the armature to rotate. This is in accordance with Fleming's left-hand rule regarding force.
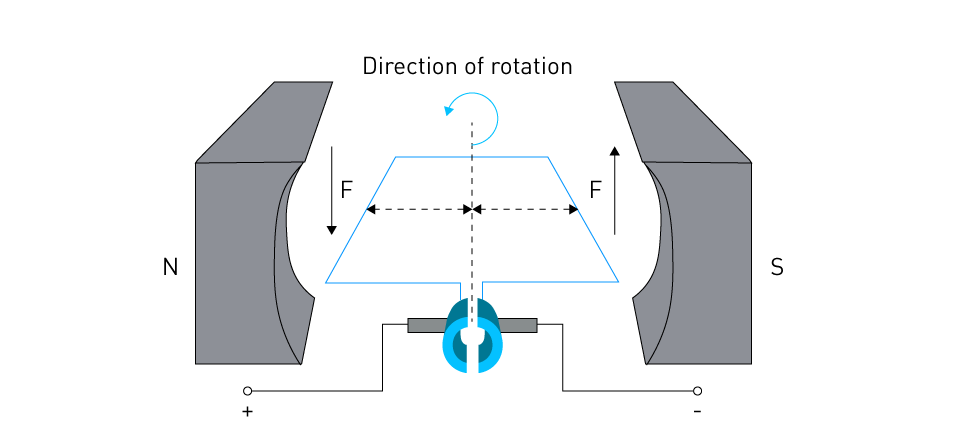
Figure 1: Generation of Rotation In a DC Motor
Commutation
In DC motors, the process of commutation involves reversing the direction of current in the armature windings in order to keep the rotational motion in a single direction as continuous as possible. The brushes and commutator regularly reverse the current flow in the windings while the armature maintains its spinning position. The interaction of the magnetic fields always directs the torque in the same direction, allowing the motor shaft to rotate smoothly and uninterruptedly.
Torque Characteristics
Understanding Torque in DC Motors: The interaction between the armature current's magnetic field and the environment's magnetic field produces a torque on the armature, causing it to rotate. By modifying the magnitude of the current that flows through the armature windings, it is possible to control the amount of torque that is experienced and, as a result, the speed at which the motor operates. This fundamental principle underpins the operation of DC motors, enabling control over the speed and torque output.
Relationship Between Torque and Motor Variables: The link between torque and the variables of a DC motor is complex and involves a number of different aspects, including the armature current, the strength of the magnetic field, the architecture of the motor, the supply voltage, and different load characteristics. There is a linear relationship between the armature current and the torque output, which means that current is the most important component in controlling torque. Similarly, enhancing the strength of the magnetic field through field windings or permanent magnets boosts the overall torque. The design parameters of motors, such as armature dimensions and winding configurations, significantly influence turbine capabilities. The supply voltage determines the maximum armature current, which indirectly influences torque. The supply voltage primarily affects the speed of the motor.
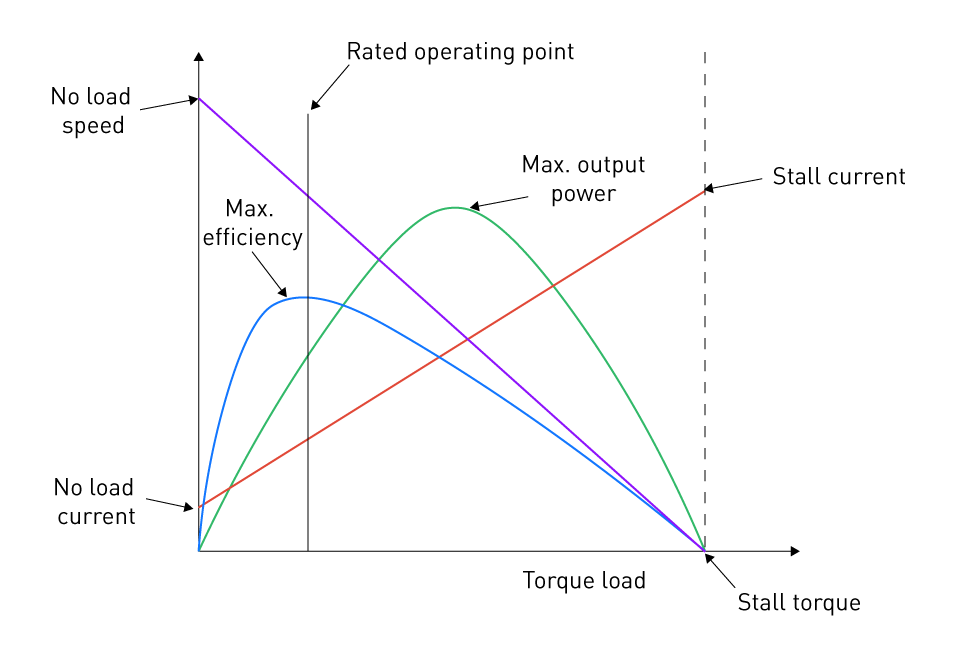
Figure 2: Characteristic Curves Of A Brushed DC Motor
Basic Equations of The DC Motor
Voltage Equation
The back electromotive force (EMF), armature resistance, armature current, and terminal voltage are all related variables in the voltage equation for a direct current (DC) motor.
$$V=E+Ia \times Ra$$Where:
V can be expressed as the terminal voltage (volts).
E corresponds to the back EMF (volts).
Ia is expressed as the armature current (amperes).
Ra is expressed as the armature resistance (ohms).
Back EMF Equation
A direct current (DC) motor produces a back electromagnetic field (E) proportional to its speed, which can be expressed as follows:
$$E=ke \times \omega$$Where:
ke represents the motor's back EMF constant (volts per radians/second).
ω represents the angular velocity of the motor shaft (radians/second).
E represents the back EMF (volts).
Torque Equation
The torque that is generated by a direct current (DC) motor is proportional to the armature current, and the equation for calculating torque is as follows:
$$T=kt \times Ia$$Where:
T represents the torque created by the motor (Newton-meters or Nm).
kt represents the motor's torque constant (Nm per ampere).
Ia represents the armature current (amperes).
Regenerative and Dynamic Braking
Regenerative Braking: The direct current (DC) motor functions as a generator when the braking system is regenerative. When the load on the motor causes the armature to move at a speed that is greater than the speed at which it would move without any load, the motor generates electrical energy and feeds it back into the battery. This procedure not only lowers the motor's speed but also recovers energy that would otherwise waste as heat.
Dynamic Braking: To achieve dynamic braking, the armature windings must be connected to a resistor. This is accomplished by unplugging the motor from its power supply. The motor continues to spin, acting as a generator and dissipating its kinetic energy as heat in the resistor, ultimately bringing the motor to a complete halt.
直接登录
创建新帐号