Introduction to AC Motors
Basic Concepts and Characteristics
Direct current (DC) motors and alternating current (AC) motors differ in that AC motors use alternating current instead of direct current for charging. Alternating current (AC) motors stand out for their ability to convert electrical energy into mechanical energy through the interaction of internal magnetic fields. Brushes and commutators, typically included in DC motors are not necessary for AC motors to accomplish this. As a result, AC motors are easier to build and frequently more reliable during extended periods of operation.
The principle of electromagnetic induction determines the operation of alternating-current (AC) motors. According to this principle, a fluctuating magnetic field within the motor generates an electric current in the conductor that is present in the rotor, which is the part of the motor that is rotating. The alternating current (AC) in the stator, the stationary part of the motor, interacts with the induced magnetic field in the rotor to produce torque, which drives the rotor.
Generally speaking, alternating current (AC) motors can be divided into two categories: induction motors and synchronous motors. Induction motors, including squirrel-cage and wound-rotor types, are intrinsically capable of starting themselves because they operate at a frequency that is slightly lower than the supply frequency. When compared to asynchronous motors, synchronous motors operate at the supply frequency and require extra mechanisms in order to begin operation.
Historical Development and Significance
One of the most important developments in the field of electrical engineering is the invention of alternating current (AC) motors, which represents a big step forward in the application of electrical power to mechanical labor. Innovators such as Nikola Tesla and Michael Faraday, whose discoveries in electromagnetism paved the path for practical uses of alternating current power, created the theoretical framework for alternating current motors in the 19th century.
Nikola Tesla's discovery of the alternating current motor in the late 1880s was a significant step forward, since it provided a solution that was both more effective and more feasible for the transmission and consumption of electrical power over great distances. This was in contrast to the direct-current systems that Thomas Edison campaigned for. Tesla's work on alternating current (AC) motors, particularly his invention of the induction motor revolutionized the conversion of electrical energy into mechanical energy, ultimately leading to the widespread adoption of AC power systems.
The significance of alternating current motors extends beyond their technical achievements. By providing electricity to factories, running pumps and compressors, and moving electric vehicles, they have been an essential component in the process of industrialization that has taken place all over the world. Because of their adaptability and high level of efficiency, alternating current (AC) motors have become an indispensable component in virtually every facet of contemporary life, ranging from small home gadgets to big industrial operations.
The evolution of alternating current (AC) motors throughout history highlights the significance of these motors in the progression of both civilization and technology. Advancements in materials, design, and control systems drive their continuous development, reflecting the constant search for more effective, dependable, and environmentally friendly methods to convert electrical energy into mechanical power. Consequently, alternating current (AC) motors continue to position themselves at the forefront of electrical engineering, serving as a symbol of the junction of scientific discovery and practical invention.
Electromagnetic Induction and Magnetic Fields
Principles of Electromagnetic Induction in AC Motors
In the 1830s, Michael Faraday made the first discovery of electromagnetic induction, which is the fundamental concept that underpins the operation of alternating current (AC) motors. It describes the mechanism by which an electric voltage (and maybe a current if the circuit is closed) is induced in a coil of wire by a changing magnetic field that is contained within the coil. This principle is absolutely essential when it comes to the operation of alternating current (AC) motors, which rely on alternating current to generate spinning magnetic fields.
Electromagnetic induction occurs in alternating current (AC) motors when the alternating current flowing through the stator windings creates a rotating magnetic field. This field generates a current in the rotor, which consists of conductive material. According to Faraday's electromagnetic induction law, the magnitude of the induced voltage is proportional to the rate of change of the magnetic flux through the circuit, as stated by Faraday's law of electromagnetic induction. This law provides the basis for the relationship between the two variables. As a result, the induced current in the rotor is responsible for creating its magnetic field. This magnetic field, in turn, interacts with the stator's rotating field to generate torque, which then causes the rotor to revolve.
Interaction of Magnetic Fields and Alternating Current
Alternating current (AC) motors are characterized by a dynamic process that involves the interplay of magnetic fields and alternating current. This interaction leads to the transformation of electrical energy into mechanical energy. The alternating nature of the AC power supply causes the magnetic field of the stator to rotate. The frequency of the AC current and the number of poles in the motor design determine the rotation speed, known as the synchronous speed.
According to the principle of electromagnetic induction, the spinning magnetic field that is produced by the stator causes a current to be induced in the rotor. As a result of Lenz's Law, which stipulates that the induced current will flow in a direction that is opposite to the change that caused it, the magnetic field of the rotor will make an effort to follow the spinning field of the stator. While operating an induction motor, the rotor will always be slightly behind the field of the stator. This phenomenon, which is referred to as "slip," is essential for the generation of torque.
These magnetic fields interact with one another to produce a force that acts on the rotor, which in turn causes the rotor to rotate. Using Fleming's left-hand rule, it is possible to determine the direction of the force (and consequently the rotation). This rule states that if the thumb, forefinger, and middle finger of the left hand are extended perpendicular to each other, with the forefinger pointing in the direction of the magnetic field and the middle finger pointing in the direction of the current, then the thumb will point in the direction of the force (motion).
The complex interaction between electromagnetic induction and the magnetic fields generated by the alternate current lies at the core of the operation of an alternating current (AC) motor. AC motors are a cornerstone of modern electrical engineering and a vital driver of technical innovation across a wide range of applications because they enable the effective conversion of electrical power into mechanical motion. This makes them an essential component of the current electrical engineering industry.
Understanding Power Factor in AC Motors
In alternating current (AC) motors, the power factor is a measurement that indicates how efficiently the motor utilizes electricity to carry out its function. Real power, which is measured in watts, is the amount of power that the motor requires to perform work. The apparent power, which is measured in volt-amperes, is the amount of power that is drawn from the power source. Connecting an alternating current (AC) motor to a supply network causes the network to perceive it as an inductive load, as the AC motor also includes inductive components. The inductive component of the motor circuit causes the phase of the electric current to lag behind the voltage. Since real power is a function of both current and voltage, the current lag in sinusoidal waveforms will lead to a decrease in real power. To achieve the intended level of real power, the motor must draw a greater amount of current from the network, which is a drawback.
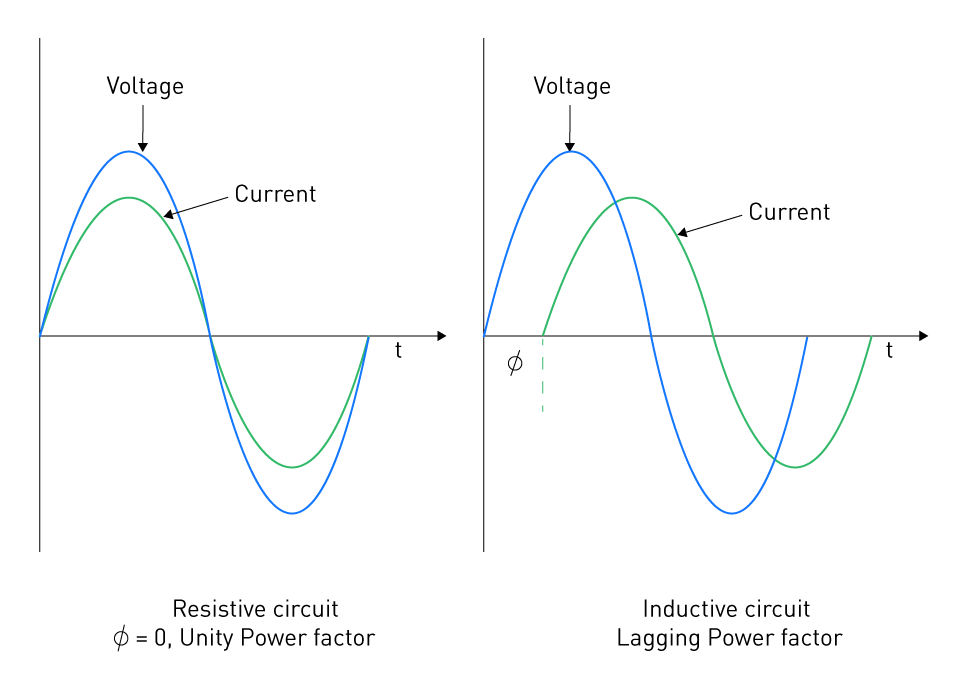
Figure 1: Depiction of Resistive and Inductive Circuit Sinusoidal Waveforms
A low power factor suggests that a significant portion of the electrical power is not effectively converting into meaningful work, while a high power factor signifies efficient use of the electrical power. In this specific case, the motor's perceived current draw is causing the system to lose unwanted heat.
In general, alternating current (AC) motors, and induction motors in particular, have a power factor that shifts depending on the load. The power factor may be high (near to 1) while the load is at its maximum, which is an indication of efficient functioning. On the other hand, when partial loads are present, the power factor might drop dramatically, which can result in an inefficient use of power and greater expenditures due to increasing demand charges from utilities.
Key Components and Their Functions
The smooth integration and functionality of the primary components of alternating current (AC) motors, which include the stator, rotor, and a number of other essential components, is essential to the efficient running of these motors. The conversion of electrical energy into mechanical motion is a process that involves each component playing an important role. The design and material concerns of the motor have a substantial impact on its performance, efficiency, and application suitability.
Detailed Look at Stator, Rotor, and Other Components
Stator: The stator is the stationary component of an alternating current (AC) motor. It is made up of wire coils that are wound around a metal core and enclosed within the housing of the motor at the same time. The alternating current generates a magnetic field that rotates when it travels through these coils. The design of the stator, which includes the number of windings and their arrangement, directly impacts the speed, torque, and efficiency of the motor.
Rotor: The rotor is the component of the motor that is responsible for rotation. It is housed within the stator. Induction motors can utilize a squirrel-cage design, which consists of conductive bars connected at both ends by rings, or a wound rotor, which consists of windings connected to slip rings. The rotor's architecture enables it to interact with the stator's magnetic field, leading to rotation. The motor's starting torque and slip characteristics are influenced by the design of the rotor as well as the material that it is made of.
Cooling System: During operation, alternating current (AC) motors produce heat. To dissipate this heat, which is necessary for preventing damage and maintaining efficiency, it is critical to have efficient cooling systems, which may include fins, fans, or liquid cooling.
Frame: The enclosure of the motor shields its internal components from environmental factors, including dust, moisture, and chemicals. It also has the ability to affect the amount of cooling and noise that occurs. Enclosures are categorized according to the level of protection they offer, with certain designs being more or less appropriate for use in hazardous or outdoor conditions.
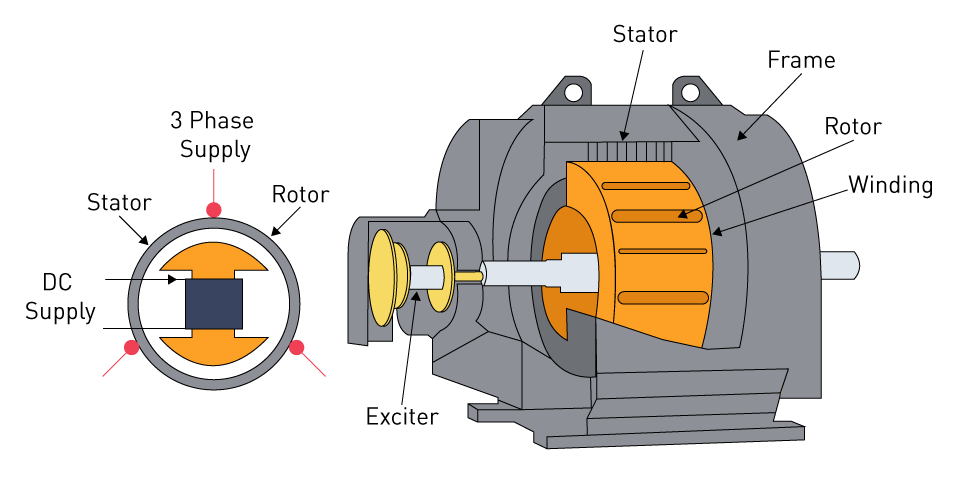
Figure 2: Example Construction of an AC Motor (Synchronous with Exciter)
Material and Design Considerations
The materials used and the design choices made during the manufacturing process significantly affect the performance and lifespan of alternating current (AC) motors.
Magnetic Materials: The magnetic properties of the materials used in the stator and rotor of alternating current (AC) motors play a significant role in determining their efficiency. Magnetic steel or laminations of superior quality can mitigate energy losses through hysteresis and eddy currents.
Electrical Insulation: Insulation materials avoid electrical short connections between winding turns and other motor parts. Insulation is commonly used in the field of electrical engineering. Both the heat tolerance and the longevity of the motor are affected by the insulation that is selected.
Conductor Materials: Copper is a material that is frequently utilized in windings when it comes to conductor materials because of its strong electrical conductivity. Despite aluminum's lower efficiency compared to copper, its lower cost and weight make it suitable for some applications. Copper is the more efficient material.
Structural Materials: The housing of the motor and its structural components need to be sturdy enough to withstand the stresses that are caused by operation as well as the conditions of the environment. Cast iron, steel, and aluminum alloys are some examples of materials that are chosen because of their strength, weight, and cost when compared to other materials.
Design for Manufacturability: Apart from material selection, the design of alternating current (AC) motors considers their assembly, maintenance, and manufacturing capabilities. This category includes modular designs that facilitate simple component replacement and accommodate efficient manufacturing processes.
直接登录
创建新帐号