Role of Alternators in Automotive Charging Systems
Maintaining the electrical stability of a vehicle and replenishing the energy reserves of the starter battery are vital functions performed by the automotive charging system, guaranteeing uninterrupted operation of various vehicle systems. The core of this essential system lies in the alternator, a component that has continuously evolved from its inception to meet the increasing electrical needs of contemporary vehicles. Delving into the crucial role of alternators within this domain, our primary focus will be on their function in generating electrical power and charging the starter battery.
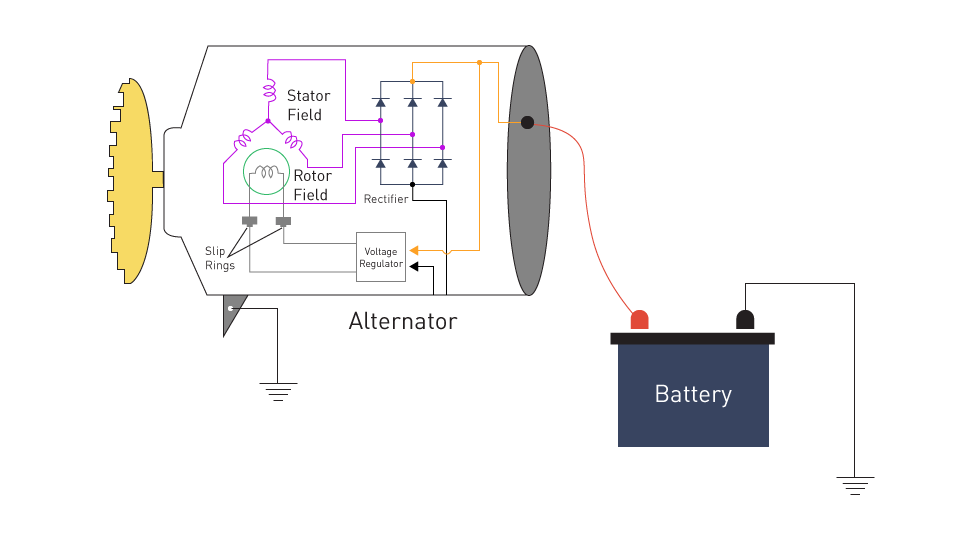
Figure 1: Main Components of the Alternator
Generation of Electrical Power
By definition, an alternator transforms the mechanical energy supplied by the engine into alternating current (AC). However, what enables this conversion?
Electromagnetic Induction: Faraday's Law of Electromagnetic Induction is the fundamental principle that empowers the alternator. A changing magnetic field is produced when the engine rotates the alternator’s motor within its stator. The production of AC occurs as a result of the voltage induced in the stator windings by this altering magnetic field.
Synchronous Generation: With the engine speed, the alternator works synchronously. Hence, the AC’s frequency produced changes proportionally with the engine's revolutions per minute (RPM). By operating synchronously, the alternator can efficiently produce power over a broad spectrum of engine speeds.
Construction and Operation of Alternators
The basic mechanisms involve a specific blend of design and engineering principles; however, its fundamental function seems straightforward. Understanding the intricate operation of alternators requires delving into their fundamental construction elements and grasping the governing processes that dictate their functionality.
Rotor and Stator Design
At the core of the alternator's function lies the principle of electromagnetic induction, which relies on two main components: the rotor and the stator.
Rotor: The rotating element of the alternator is known as the rotor. Fundamentally, it functions as an electromagnet, implying that its magnetic field arises from the flow of an electric current through it. Constructed with an iron core, the rotor integrates a coil wound around it in its design. The flow of current through this coil, whether from the battery or an alternative source, generates a magnetic field. The crucial aspect lies in both the strength and design of the rotor's magnetic field. Changes in the strength of the field can notably impact the alternator's efficiency and reliability.
Stator: The stationary component of the alternator that surrounds the rotor is the stator. Encased within are wire coils that interact with the rotating magnetic field of the rotor. When the rotor rotates and alters its magnetic field orientation concerning the stator, it prompts a voltage induction in the stator coils, illustrating the direct application of Faraday's law of electromagnetic induction. The stator's design aims to optimize induced voltage based on a specific rotor design and speed.
The collaborative interplay of the rotor's magnetic field and the stator's coils leads to the production of alternating current (AC).
Rectification and Voltage Regulation
Upon generation, the alternating current (AC) must undergo conversion and regulation to suit automotive applications, primarily for the purpose of charging the vehicle's battery.

Figure 2: Alternator Circuit Diagram
Rectification: In vehicle electrical systems, direct current (DC) is predominantly utilized. Consequently, it becomes necessary to convert the produced AC into DC. A common method employed to achieve this conversion involves using a rectifier, commonly composed of a 3-phase bridge formed by a set of diodes. By permitting current flow in one direction, diodes efficiently transform the fluctuating AC waveform into a consistent unidirectional DC output.
Voltage Regulation: The alternator's generated voltage fluctuates varies with the engine's speed. However, a relatively stable voltage is needed by the vehicle’s battery and the electrical parts. The voltage regulator maintains a consistent output voltage level, independent of the engine's RPM or the system's current load, ensuring it stays within the desired range. To control the power input to the field winding is the main function of the voltage regulator circuit. If the output voltage and current surpass the standard level, the voltage regulator will reduce the power input to the field winding, resulting in a decrease in the armature winding's voltage, thereby maintaining it at the normal value.
In summation, the complex nature of alternator construction and operation integrates mechanical and electrical engineering principles, specifically designed to meet the distinctive requirements of automotive uses. By intricately designing the rotor and stator and employing advanced rectification and regulation mechanisms, the alternator continues to stand as a crucial component within contemporary automobiles.
Performance Parameters and Efficiency
In an age emphasizing energy reliability and efficiency, comprehending the performance metrics of automotive alternators becomes imperative for designers and users alike. Though power supply is the primary role of the alternator, the vehicle's overall performance and lifespan can be notably influenced by its efficiency, output quality, and thermal management. Within this segment, we will examine the fundamental performance aspects of alternators and go deeper into the complexities surrounding their operational efficiency.
Output Voltage and Current Ratings
Consistency and reliable power are the core parameters of any electrical device. This is evaluated through its voltage and current outputs for alternators.
Output Voltage: To recharge the battery and power other electrical parts in the vehicle is the basic function of an alternator. For this purpose, the alternator needs to produce a voltage level exceeding that of the battery, commonly averaging between 13.8V and 14.4V in a 12V system. The generated output voltage depends on both the rotor's rotational speed and the intensity of its magnetic field. However, it is also impacted by the electrical load imposed on the alternator and the condition of the battery's charge. As discussed in the aforementioned section, this output remains within the desired range and is ensured by voltage regulation, therefore, safeguarding the battery and other electrical parts from potential damage.
Current Ratings: Alternators are typically indicated in amperes (A) and also rated based on their maximum current output. This rating offers insight into the highest electrical capacity that the alternator can manage. The current rating is influenced by factors such as the cross-sectional area of the wire within the stator windings and the overall efficiency in the design of the alternator. When a vehicle incorporates multiple high-power electrical accessories, such as amplifiers or extra lights, it becomes crucial to verify that the alternator's current rating can meet the heightened demand.
Alternator Efficiency and Cooling
The effectiveness of the alternator's operation under different conditions is as crucial as its output when assessing performance.
Efficiency: The alternator’s efficiency pertains to its ability to convert mechanical energy derived from the engine's drive belt into electrical energy effectively. It represents the relationship between the electrical power output and the mechanical power input, expressed as a ratio. Due to losses in the cooling system, bearings, iron, copper, and the voltage drop across the diode bridges, the efficiency of automotive alternators faces limitations. At higher speeds, air-cooled alternators experience a significant reduction in efficiency primarily caused by increased fan resistance. Meanwhile, modern alternators typically exhibit an efficiency range of 70% to 80% at moderate speeds.
Cooling: Alternator generates heat as it works. Elevated temperatures have the potential to degrade insulation, disrupt diode functionality, and abbreviate the lifespan of the alternator. The majority of alternators integrate a cooling mechanism, frequently utilizing either the engine's cooling fan or an internal fan within the alternator for this purpose. For high-performance or heavy-duty applications, alternators may utilize advanced cooling systems like liquid cooling. These systems, such as extensions to the engine cooling mechanism, are instrumental in preserving optimal operating temperatures, thus ensuring sustained performance and longevity.
To summarize, a delicate equilibrium between its electrical outputs and operational efficiency results in the alternator's performance. Engineers have the opportunity to create vehicles that provide dependable electrical power through comprehension and enhancement of these parameters, while optimizing energy efficiency and extending the lifespan of components.
直接登录
创建新帐号