Introduction to Battery Management Systems
In modern automotive applications, battery management systems (BMS) are essential, particularly for electric and hybrid vehicles (HEVs). Serving as the brains behind battery operations, BMS makes sure that batteries run safely, healthily, and at their best. This section describes the essential elements of a BMS and sheds light on its function and importance in automotive systems.
Role and Significance of BMS in Automotive Systems
Since batteries are the foundation of electric mobility, the significance of BMS in the context of contemporary automotive systems cannot be emphasized.
Here is a breakdown of the main responsibilities and the importance of BMS:
Safety Assurance: BMS keeps an eye on several battery characteristics, including voltage, current, and temperature, to avert potentially hazardous situations like overcharging or overheating.
Performance Optimization: BMS maintains optimal performance, optimizing the efficiency and range of electric cars by controlling the charging and discharging processes.
Health Monitoring: BMS can forecast the battery's life and alert users when maintenance or replacement is required by continuously evaluating the state-of-charge (SOC) and state-of-health (SOH).
Energy Management: By coordinating battery operations with the vehicle's energy needs, load shedding, and energy regeneration techniques, BMS plays a critical role in energy management.
Integration with Vehicle Systems: The BMS communicates with other vehicle systems to provide coordinated functioning of the propulsion, thermal management, and other systems as well as to give the driver vital information.
Components of a BMS
Several linked components, each with a distinct function make up a typical BMS. The principal elements consist of:
Sensors: Sensors take the temperature of the battery cells and the current in the battery pack. They provide data in real-time and act as the system's eyes.
Control Module: The circuit module that gathers, processes, and decides upon sensor data. It uses algorithms to control the charging and discharging operations as well as to predict SOC and SOH.
Protection Circuitry: This consists of Charge and Discharge switches that can be shut off in the event of an overcharge, over-discharge, short circuit, or overtemperature. These switches are managed by the Control Module.
Balancing Circuitry: The balancing circuitry makes sure that each cell in the battery pack receives an equal amount of charge, which increases the battery's overall lifetime and efficiency.
Communication Interfaces: These facilitate fault identification and diagnosis by allowing communication between BMS master and slave units as well as with other vehicle systems.
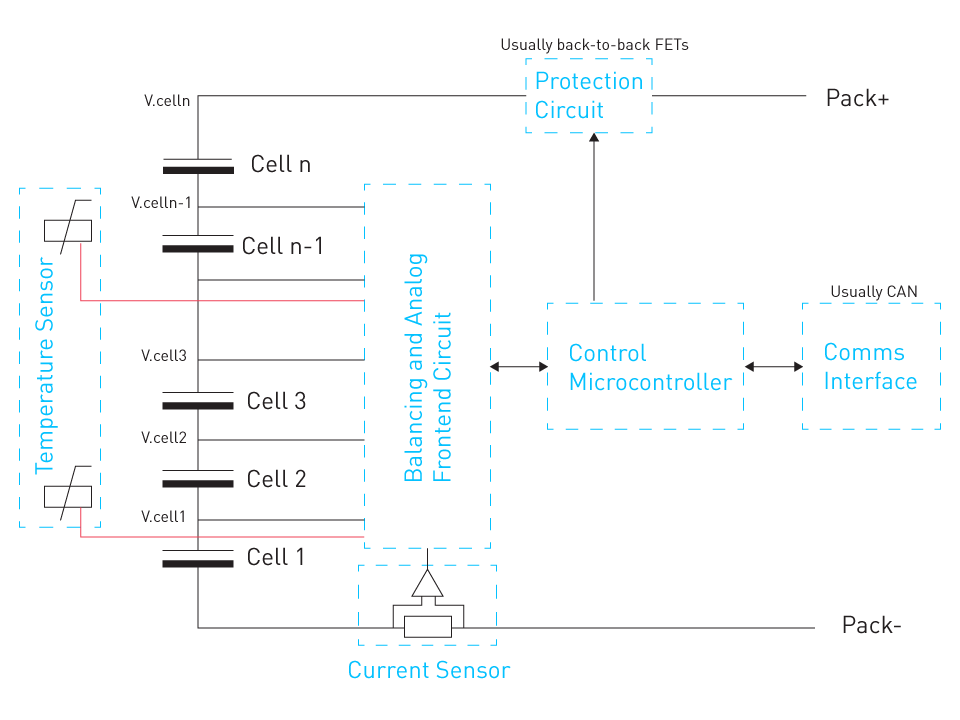
Figure 1: Block Diagram of a BMS
Battery Management Systems are vital cogs in the complex machinery of modern automotive systems, particularly in electrically powered vehicles. Through rigorous monitoring, controlling, protection, balancing, and communication, BMS ensures that batteries are not only performing at their best but are doing so in a manner that is safe, efficient, and sustainable. The intricate synergy of its components symbolizes a robust technology that supports the broader vision of clean and intelligent mobility. Future advancements in BMS will likely continue to be pivotal as the automotive industry evolves towards more electrified and automated solutions.
Monitoring and Controlling Battery Parameters
Battery Management Systems (BMS) rely heavily on monitoring and managing different battery characteristics. It assures safe and efficient battery operation, extends battery life, and improves overall vehicle performance. This section goes into detail about the essential metrics that BMS monitors and controls, such as the state-if-charge (SOC), start-of-health (SOH), voltage, current, temperature, and the charge and discharge processes.
State-of-Charge (SOC) Estimation
The current state-of-charge (SOC) of a battery is expressed as a percentage of its nominal capacity. An accurate SOC estimate is critical for optimal performance since it tells the driver about the amount of energy available, allowing choices such as when to charge to be made.
Methods: Various approaches, including Coulomb counting and voltage-based estimate, are used, and they are frequently combined to improve accuracy.
Importance: Provides real-time energy information, impacting driving and charging behavior.
State-of-Health (SOH) Estimation
The state-of-health (SOH) of a battery shows its overall condition in comparison to its fresh state. SOH estimates requires complicated algorithms that take into account a variety of parameters like charge/discharge cycles, temperature history, and aging effects.
Methods: Impedance measurement, cycle analysis, and adaptive algorithms are all included.
Importance: Essential for estimating battery life and maintenance requirements.
Voltage and Current Monitoring
Voltage and current monitoring between battery cells and packs is critical for performance and safety.
Voltage Monitoring: Voltage monitoring ensures that cells operate within acceptable limits. Voltage imbalances can signal problems such as uneven resistance, which can lead to efficiency losses. The monitoring of pack-level voltage is also a critical parameter for many vehicle operations.
Current Monitoring: Measures the flow of electric charge to and from the battery pack, which aids with SOC estimate and the detection of abnormal circumstances like overcurrents and short circuits.
Importance: Essential for balanced operation, security, and efficiency optimization.
Temperature Monitoring
The temperature of the battery pack has a considerable influence on performance, safety, and longevity.
Methods: NTC (Negative Temperature Coefficient Thermistors) sensors strategically distributed across cells and modules are used.
Importance: Aids thermal management by preventing overheating or excessive cooling and influencing other metrics such as SOC and SOH.
Charge and Discharge Processes
The ability to manage charging and discharging is critical to battery performance and lifespan.
Charging Control: BMS handles charging currents, voltages, and stages such as constant current (CC) and constant voltage (CV). It also communicates with charging infrastructure to verify standard compliance.
Discharging Control: The BMS ensures that discharging happens within safe limits by taking into account elements such as current, voltage, temperature, and remaining capacity.
Importance: This factor has a direct impact on battery efficiency, life duration, and the capacity to satisfy vehicle needs.
Monitoring and managing battery characteristics inside BMS is an art and science that combines technological complexity with practical concerns. The BMS maintains a harmonic balance of safety, performance, and efficiency through constant observation, precise estimates, and intelligent control. BMS functions as the orchestrator of a finely-tuned symphony, whether judging the immediate state via SOC, assessing overall health via SOH, controlling crucial parameters like voltage, current, and temperature, or handling the complicated dance of charging and discharging. Sensor technology, data analytics, and adaptive algorithms advancements are further refining this orchestration, promising even more nuanced and responsive battery management in the future of vehicle systems.
Battery Protection Mechanisms
Protection methods are required in Battery Management Systems (BMS) to maintain the safety, dependability, and lifetime of the battery system. These safeguards keep the battery from running in situations that might cause irreversible damage, loss of efficiency, or safety issues. Overcharge and over-discharge states, as well as short circuit and heat situations, are two major areas of concern. This section will go over these important features of battery protection.
Over-Charge and Over-Discharge Protection
These safeguards keep the battery from charging or draining over its safe limits. In the case of a Lithium-ion battery, for example, the maximum permitted cell voltage is 4.1-4.2V. The minimum permissible cell voltage ranges from 2.4 to 3V.
Over-Charge Protection
- Function: Prevents the battery from being charged over its maximum voltage, preventing potential harm.
- Methods: This includes voltage monitoring and charges current control. When a specified voltage threshold is achieved, cut-off circuits can be utilized to disconnect the charger.
- Importance: Assists in the prevention of possible risks such as electrolyte leakage, swelling, and thermal runaway.
Over-Discharge Protection
- Function: Prevents the battery from discharging below its minimum voltage, preventing cell reversal and capacity loss.
- Methods: Monitors voltage and works with system control to lower or disconnect loads when certain thresholds are achieved.
- Importance: Prevents permanent damage to battery cells and contributes to battery longevity.
Short Circuit and Thermal Protection
Short-circuit protection and protection from extreme heat are crucial for preserving safety and functionality.
Short-Circuit Protection
- Function: Detects and responds to short circuit problems, reducing current flow and, if required, disconnecting the battery.
- Methods: To cut off current flow, current sensors and fast-acting protection circuits are used. For self-recovery, resettable fuses can be used.
- Importance: Critical for safety, as it prevents overheating, fire, and other catastrophic failures.
Thermal Protection
- Function: Thermal protection is a function that ensures the battery functions within a safe temperature range.
- Methods: Uses temperature sensors and thermal modeling to control cooling or heating systems, and may shut down or restrict battery operation under high heat.
- Importance: Controls thermal stress, reduces thermal runaway, and promotes peak performance and longevity.
Battery Protection Mechanisms in BMS play an important role in safeguarding, continuously working behind the scenes to preserve a healthy balance between performance and safety. These devices operate as diligent guardians of the battery's integrity, whether they are controlling the energy intake and outflow through overcharge and over-discharge safeguards or monitoring for more sudden and harmful circumstances like short circuits and heat extremes.
BMS guarantees that the multiple issues of managing complex electrochemical energy storage systems are handled with accuracy and dependability by including advanced sensors, control algorithms, and responsive action paths. As battery technology advances and the demands on energy storage systems become more complicated, these protective measures will advance as well, facilitated by continual research and technical innovation.
The dependable and safe functioning of battery systems is more than a technical requirement in the context of automotive systems; it is a commitment to user safety, environmental responsibility, and the robust future of electric mobility.
Balancing Techniques
Battery balancing is a vital component of Battery Management Systems (BMS) in automotive and other applications that require multi-cell batteries. Balancing ensures that all cells in a battery pack have the same state-of-charge (SOC). This section introduces cell balance and delves into two basic techniques: passive and active cell balancing.
Introduction to Cell Balancing
The act of ensuring that all individual cells in a battery pack attain an equal level of charge is known as cell balancing. This is required because even tiny variances in manufacture, aging, temperature, or self-discharge rates can cause variations in individual cell voltage levels and capacity.
Why Cell Balancing is Necessary
- Performance: Unbalanced cells can decrease overall battery performance since the performance of the weakest cell can decide the performance of the entire pack.
- Longevity: Imbalanced cells might cause certain cells to degrade quicker, limiting the total longevity of the battery pack.
- Safety: Extreme imbalance may cause certain cells to be overcharged or over-discharged, thus posing a safety issue.
Passive and Active Cell Balancing Techniques
There are two methods for balancing the cells in a battery pack: passive balancing and active balancing. Both strategies attempt to equalize the charge of the cells, although they do it in different ways.
Passive Cell Balancing
- Function: Removes excess charge from cells with greater voltage, often via a resistor or a transistor-resistor network. The diagram below demonstrates a passive balancing circuit. With the assistance of the transistor switch, each battery cell may be drained independently via resistors Rn and Rn-1. The rate of discharge is determined by the resistor values used.
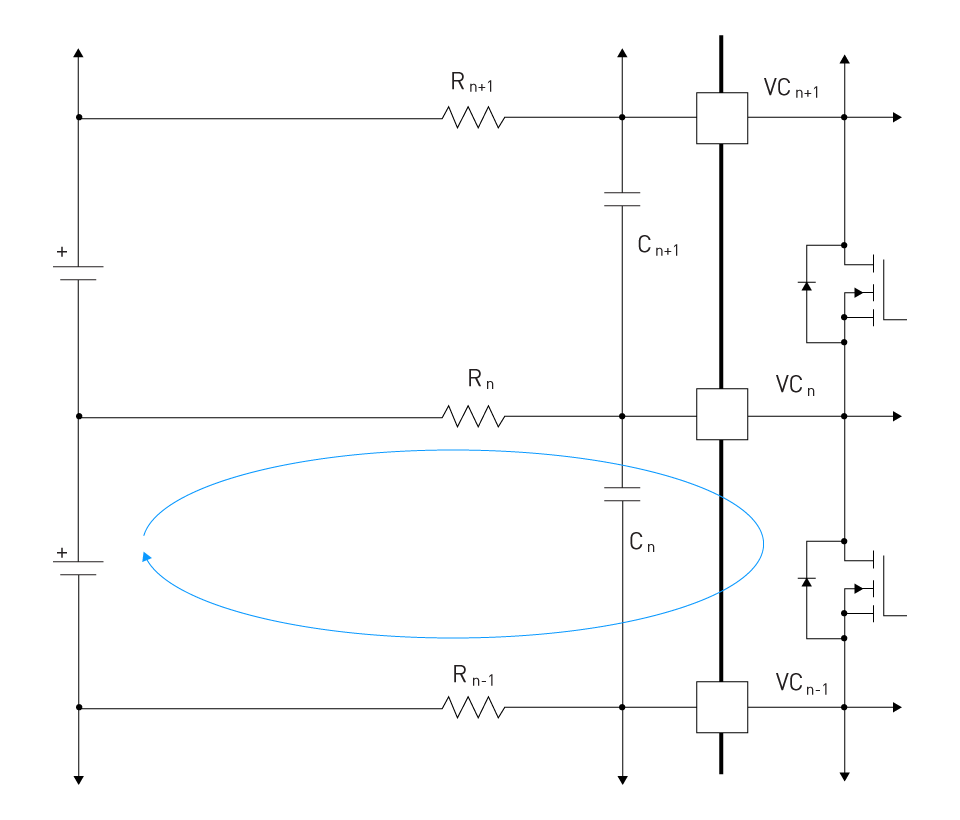
Figure 2: Example of Passive Cell Balancing
- Pros: Less complicated, less expensive, and doesn't need intricate control systems.
- Cons: Energy is lost as heat, which might lead to issues with thermal management. It is less effective, especially with big imbalances.
Active Cell Balancing
- Function: Instead of releasing the extra energy as heat, the charge is transferred from higher-charged cells to lower-charged ones. An energy storage device, such as an inductor, transformer, or capacitor, can assist with this.
- Pros: Higher efficiency as energy is preserved rather than dissipated. More quickly fixes imbalances and is appropriate for bigger battery packs.
- Cons: Requires more area on the printed circuit board and is more costly and sophisticated. It calls for extra parts and complex control methods. furthermore prone to causing issues with electromagnetic emission.
Cell balancing is essential to a battery pack's long-term performance, reliability, and security. While passive balancing might be less effective and respond more slowly, it is a simpler and more affordable option. However, reality dictates that even for EV car battery packs, passive balancing often suffices. In contrast, active balancing, albeit more complex and expensive, offers a more efficient and responsive solution, especially ideal for bigger battery packs.
The decision between passive and active balancing will be based on the particular needs of the application, including the battery pack's size, anticipated imbalances, efficiency requirements, and financial limitations. These considerations need to be carefully taken into account by engineers building BMS in order to choose the best balancing strategy for their specific system.
New solutions are created and balancing techniques are continuously improved in the quickly developing field of battery technology. The performance of individual battery systems is improved by research and development in this field, which also advances energy storage technologies more broadly and promotes the sustainability of electric vehicles.
BMS Communication and Diagnostics
Battery Management Systems (BMS) are not separate components in automobile systems. They have to control internal communication between master and slave components, perform continuous diagnostics and defect detection, and interact with the vehicle's many subsystems efficiently. These crucial BMS functioning areas are covered in detail in this section.
Communication with Other Vehicle Systems
The infotainment system, transmission control unit (TCU), engine control unit (ECU), and other vehicle systems must all be able to interact with the BMS without any difficulties. Coordination of control and optimal performance are made possible by this connection.
Data Exchange: Important data is communicated with other systems, such as voltage levels, temperature, and battery state-of-health (SOH) and state-of-charge (SOC).
Protocols: For this communication, common protocols like FlexRay, LIN (Local Interconnect Network), and CAN (Controller Area Network) may be utilized.
Importance: It guarantees synchronized functioning, security, and energy economy by modifying battery consumption in accordance with driving circumstances and user preferences.
Communication between BMS Master and Slaves
A BMS Master overseeing several Slave units, each of which is in charge of keeping an eye on a group of cells or modules, is a common hierarchical structure seen in sophisticated battery systems. Because this voltage does not exceed dangerous limits and no additional caution shall be paid for in the design, high-voltage battery packs often partition their cells into 48V (Li-Ion) groups. BMS slaves are responsible for managing these groups individually.
Master Unit: Overseeing coordination, decision-making, and communication with other vehicle systems are the responsibilities of the master unit.
Slave Units: Keep an eye on a single cell or a group of cells and relay information to the Master.
Communication Protocols: The BMS can communicate quickly and reliably by using I²C, SPI, or other protocols.
Synchronization: Enhances performance and safety by ensuring that every component of the BMS functions in unison.
Diagnostics and Fault Detection
Continuous problem identification, diagnostics, and monitoring are essential to the battery system's performance, safety, and dependability.
Fault Detection: This involves locating problems like as communication faults, internal shorts, overcharging, undercharging, and overheating.
Diagnostics Tools: Makes use of both software and hardware tools to keep an eye on system behavior and compare it to predetermined performance benchmarks.
Predictive Maintenance: Advanced diagnostics can identify possible faults before they become significant, allowing for proactive maintenance
Safety Protocols: To avoid damage or risks, the BMS starts safety procedures in the case of a detected failure. These procedures include disconnecting the impacted cells or shutting down the system.
The BMS's duty as the main hub for battery control and monitoring includes extensive communication and diagnostic features. The performance, safety, and energy economy of the vehicle is improved by the BMS by facilitating seamless communication between its components and other vehicle systems. In today's electric and hybrid automobiles, continuous diagnostics and problem detection provide an additional degree of dependability, making these systems essential.
The cooperation and integration of various car systems become ever more essential as automotive technology develops. Future BMS functionality and design will probably be influenced by evolving standards, enhanced communication protocols, and advanced diagnostics tools, all of which will help create safer, more effective, and intelligent automobiles.
直接登录
创建新帐号