Basic Concepts of Thermal Control
An understanding of the basic concepts linked with the transfer and dissipation of heat are at the heart of effective thermal management. Comprehending these concepts is more crucial than ever, given the ongoing miniaturization and heightened power of electronic components in automotive applications. Let’s familiarize ourselves with the rudiments of thermal control before exploring the detailed tactics for managing thermal loads.
Heat Transfer Mechanisms
Conduction: This describes the process of heat transfer occurring within a material or between materials in direct contact, without any accompanying physical movement of the material itself. As heat increases in one region of a material on a molecular level, the energy is passed from the faster-moving particles to the slower ones. Conductive heat transfer commonly occurs in electronics when a heated component interfaces with a solid heat sink connected to it. The heat conduction rate is contingent upon the material's conductivity and the temperature differential across it.
Convection: The process of convection facilitates the exchange of heat between a solid surface and a moving liquid or gas. Convection's effectiveness relies on factors such as the fluid's properties, temperature variance, and velocity. For example, fans are commonly employed in automotive electronic systems to optimize convection, aiding in the dispersion of heat by circulating air over components or heat sinks.
Radiation: Based on their temperature, all objects emit electromagnetic radiation. Radiant heat transfer occurs when energy is emitted, referring to the energy dispersion through radiation. Radiation differs from conduction and convection in that it does not rely on any medium, such as a solid, liquid, or gas, for its occurrence. In contrast, radiation can occur even in a vacuum, just like the radiation of heat from the sun. Radiation typically assumes a subordinate role in electronics compared to other heat transfer mechanisms. However, radiation can emerge as the primary mode of heat transfer in specific scenarios such as space or high-vacuum environments.
Thermal Resistance, Capacitance, and Heat Sinks
Thermal Resistance: Thermal resistance, like electrical resistance, measures the efficiency of heat transfer within a specific medium. The resistance of a substance to the flow of heat is quantified by this measure. For efficient heat transfer in electronic applications, materials possessing high thermal conductivity (and thus low thermal resistance) are favored.
Thermal Capacitance: Like electrical capacitance, thermal capacitance regulates the rate of heat transfer variation over time. Increased thermal capacitance implies the system's capability to retain greater heat energy, consequently resulting in a slower rate of temperature rise.
Thermal Ladder Circuit: Utilized in thermal analysis, the thermal ladder circuit serves as a foundational model, depicting a system's heat transfer traits by interlinking thermal resistances and capacitances in a series configuration. Similar to an electrical ladder circuit, this model equates thermal resistances with hindrances to heat flow, akin to electrical resistance, while thermal capacitances mirror the capacity of materials or components to retain thermal energy, like electrical capacitance. Representing different layers or components within the thermal system, each 'rung' of the ladder analogy simplifies the depiction of intricate heat transfer processes across various materials and interfaces, ensuring an effective representation.
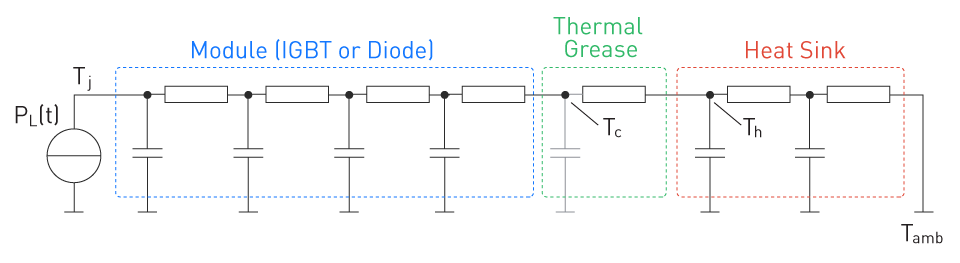
Figure 1: Thermal Ladder Circuit
Heat Sinks: Using thermal contact, these are devices or materials that absorb and dissipate heat from another object. The design of heat sinks aims to optimize contact with the cooling medium, such as air, by maximizing the surface area. Crucial for preventing overheating in power electronics, heat sinks, typically constructed from materials like aluminum or copper with high thermal conductivity, play a vital role. Increasing the surface area of a heat sink through fins, ridges, or other protrusions enhances its capacity to dissipate heat effectively. Fans are commonly utilized to augment the efficiency of a heat sink by boosting convective heat transfer.
To address challenges and formulate solutions regarding thermal management in automotive electronics, an understanding of these fundamental thermal control concepts is essential. This foundational knowledge emerges as the cornerstone of innovation and safety, amidst the industry's drive towards increasingly compact and potent systems.
Active and Passive Thermal Management Solutions
Engineers employ a combination of active and passive thermal management solutions to uphold the optimal operating temperature range of automotive electronics and mitigate the adverse effects of overheating. Although their objective is temperature regulation, the methodologies employed by both differ significantly.
Heat Sinks and Thermal Interface Materials
Heat Sinks: At the core of passive cooling strategies lie heat sinks, devices engineered to absorb heat from electronic components and subsequently dissipate it. Typically crafted from materials boasting high thermal conductivity, like aluminum or copper, they form an integral part of such strategies. Heat sinks promote heat dissipation through convection by enhancing the surface area in contact with ambient air through the incorporation of fins or ridges.
Thermal Interface Materials: Soft and pliable materials, positioned between the heat sink and the component, serve to enhance thermal contact by filling air gaps, thus ensuring improved heat transfer. Due to its poor conductivity of heat, air necessitates the use of thermal interface materials with significantly higher thermal conductivity to bolster heat transfer’s efficiency from the component to the heat sink.
Fans and Liquid Cooling
Fans: Fans help in circulating air around components when deployed as part of active cooling techniques, thereby increasing the convection process. Also, it can significantly increase the heat dissipation rate by drawing cooler air over the components or pushing out the hot air surrounding them. Their effectiveness is particularly pronounced when paired with heat sinks, allowing airflow to be channeled over the fins to enhance cooling capabilities.
Liquid Cooling: To absorb heat, this advanced cooling technique utilizes liquid coolant circulated around the components. Afterward, the warmed liquid flows through a heat exchanger, commonly referred to as a radiator, facilitating the transfer of heat to the surrounding environment. In high-performance automotive electronics or electric vehicle battery systems, where rapid heat dissipation is essential, liquid cooling is frequently favored due to its superior efficiency compared to air cooling.
Thermoelectric Cooling (Peltier Effect)
Operating on the principle of the Peltier effect, thermoelectric coolers, commonly known as Peltier devices, offer a distinct approach to active cooling by generating a temperature differential through the transfer of heat between two electrical junctions. As current traverses through the circuit containing dissimilar conductors, heat is drawn away from one junction (termed the "cold" side) and discharged at the opposite junction (referred to as the "hot" side). Following this, the heat accumulated on the hot side is dissipated utilizing conventional techniques such as heat sinks or fans. Compact in design, devoid of moving components, and capable of delivering precise temperature regulation, these devices are ideal for targeted automotive applications that demand spot cooling.
In conclusion, determining the most suitable thermal management solution—whether active or passive—depends on the distinctive requirements of the specific automotive system. Factors such as spatial limitations, heat generation, power limitations, and reliability preferences play a crucial role in this determination. The most efficient solution to the complicated thermal challenges of advanced automotive electronics is frequently offered by a hybrid approach, which integrates both active and passive techniques.
Power Management Strategies for Thermal Control
In modern automotive electronics, the complexity of thermal challenges extends beyond the realm of passive and active cooling systems. To ensure effective operation while reducing heat production, there is an ever-evolving focus on intelligent power management as we push boundaries of what electronics can attain.
Dynamic Power Scaling
Definition: A technique known as Dynamic Power Scaling dynamically adapts the power consumption and operational performance of a system according to the present workload and thermal conditions. It can effectively regulate heat generation by aligning power usage with real-time requirements.
Operational Modes: Systems equipped with dynamic power scaling typically feature various operational modes, including:
- Performance Mode: This mode harnesses maximum processing capability, resulting in increased power consumption and heat generation.
- Efficiency Mode: This mode provides balanced performance while conserving power and minimizing heat output.
- Low-Power Mode: Although at the expense of reduced performance, this mode focuses on minimal energy consumption and heat generation.
Benefits: By enabling adaptability, electronic components guarantee longevity, efficient power utilization, and effective thermal management by operating optimally under diverse conditions.
Sleep Modes and Power Gating
Sleep Modes: Utilizing a low-power state during periods of inactivity, either in specific components or across the entire system, is an effective strategy for conserving power. The retention of system context varies depending on the depth of the sleep mode, impacting both wake-up time and power consumption levels.
Power Gating: Taking sleep modes to a higher level, this technique entails physically cutting off power to circuit or system components when they are inactive. Through the interruption of the power supply, power gating guarantees an absence of static power consumption, consequently eliminating heat generation from the gated section.
Operational Implication: To implement power gating and sleep modes effectively, one must accurately discern instances of component or system idleness and determine when their full operation is unnecessary. Balancing user experience with power and thermal management optimization, the integration of hardware and software coordination in advanced systems facilitates swift transitions between operational and sleep states.
Benefits: In addition to decreasing overall power consumption, sleep modes and power gating substantially mitigate the heat generation of automotive electronic systems. Their importance lies in extending component longevity, bolstering system reliability, and guaranteeing safe operations.
In conclusion, while power management strategies handle the root cause, cooling techniques address the symptoms of heat production. Engineers can establish comprehensive thermal management ecosystems within automotive electronics by integrating these strategies with cooling solutions, thereby fostering efficiency, resilience, and safety.
Thermal Management in Battery Systems
The critical role of battery systems cannot be overstated as the automotive industry swiftly transitions to electric vehicles (EVs). Lithium-ion batteries, especially, supply the requisite energy to propel electric vehicles across significant distances. Yet, despite their potency, lithium-ion batteries are vulnerable to thermal challenges. In battery systems, efficient thermal management is critical for enhancing life, optimizing performance, and ensuring safety.
Cooling Techniques for Electric Vehicle Batteries
Air Cooling: To dissipate heat from the battery cells, air cooling method uses forced air. The effectiveness of air cooling diminishes in larger battery packs or under extreme conditions, although it is less complex and relatively inexpensive.
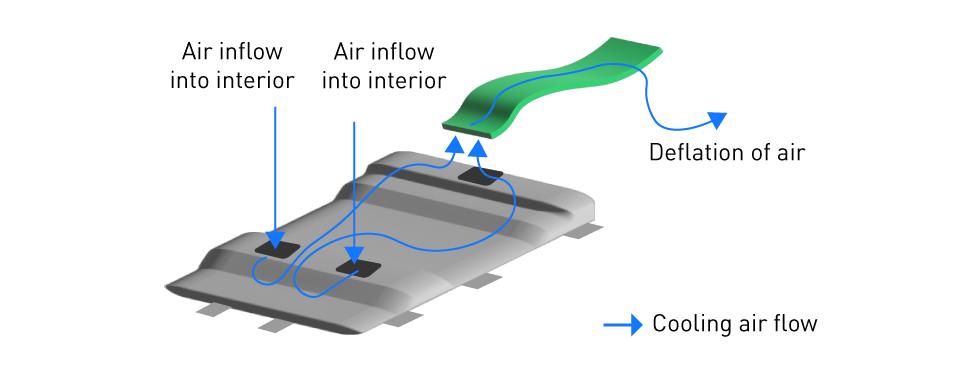
Figure 2: Kia Soul EV Air Cooled Battery System
Liquid Cooling: To absorb and transport heat away from the batteries, a more advanced and efficient method uses liquid coolants. Maintaining a uniform temperature distribution, the coolant circulates around the battery cells effectively. In comparison to air cooling, liquid cooling systems demonstrate greater efficacy in managing higher energy densities and rapid charge/discharge scenarios.
Phase Change Materials (PCMs): Materials utilized in PCM technology absorb and release latent heat as they undergo phase transitions, transitioning between solid and liquid states. Ensuring cells remain within their optimal operating range, these aids stabilize temperature fluctuations within battery packs.
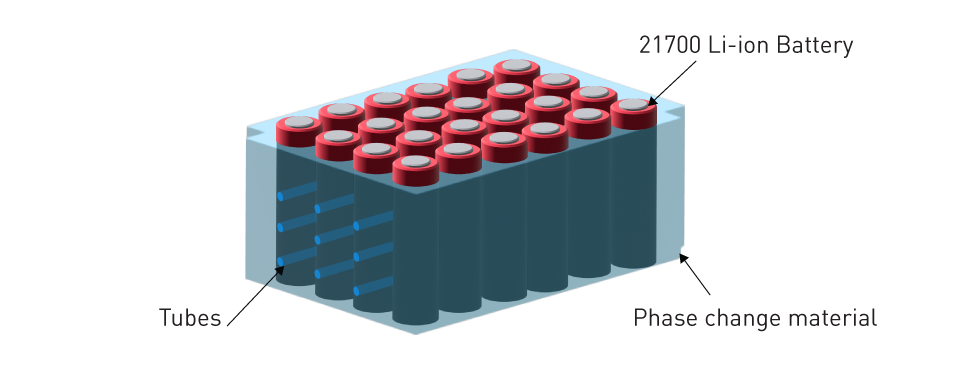
Figure 3: Li-Ion Cells in Phase Change Material
Immersion Cooling: Battery cells are submerged directly into dielectric fluids possessing exceptional heat absorption capabilities in this future technique. By guaranteeing uniform cell temperatures, this technology excels in swiftly distributing and dissipating heat.
Thermal Runaway and Safety Considerations
Definition: Usually resulting from internal or external short circuits, physical damage, manufacturing defects, or overcharging, thermal runaway refers to an uncontrollable exothermic reaction within a battery cell.
Consequences: The occurrence of thermal runaway in a single cell within a battery pack can swiftly raise temperatures, leading to a cascade effect wherein neighboring cells may also become affected. Fires or even explosions can be caused by this domino effect.
Safety Mechanisms: To prevent or mitigate the effects of thermal runaway, modern EV batteries integrate numerous safety features:
- Cooling Systems: As aforementioned, the implementation of effective cooling systems can avert the attainment of temperature thresholds that could trigger thermal runaway in cells.
- Battery Management Systems (BMS): Making real-time adjustments to ensure cells remain within safe operational parameters, a BMS constantly monitors temperatures, charge states, and voltages.
- Physical Barriers: To hinder or decelerate the spread of thermal runaway from one cell to its neighboring counterparts, certain battery packs integrate fire-resistant barriers between cells.
Meticulous thermal management is necessary for the critical nature of battery systems in EVs. The automotive industry, by blending advanced cooling methods with proactive safety measures, stands on the brink of ensuring the reliability and safety of tomorrow's electric vehicles.
Challenges and Solutions
Temperature Uniformity: In EV batteries, numerous cells are included, emphasizing the importance of maintaining a consistent temperature range for each cell to prevent accelerated aging in hotter cells due to non-uniformity.
- Solution: By implementing cooling plates and liquid cooling loops, a more uniform dissipation of heat can be achieved, which in turn promotes a balanced distribution of temperature across cells.
High-Temperature Risks: Resulting in a shortened overall lifespan of the battery, higher temperatures accelerate the degradation of the electrolyte and other battery components. Under extreme circumstances, thermal runaway may occur, initiating a chain reaction that could culminate in fire or explosion.
- Solution: By integrating sensors and control algorithms, active cooling systems can consistently monitor and regulate the thermal conditions of the battery. The battery remains within its safe operational temperature range, which is ensured by this dynamic strategy.
Low-Temperature Performance: By decreasing its efficiency and capacity, the battery’s internal resistance can be increased at low temperatures.
- Solution: Integration of heating elements and insulation sustains the battery at its optimal operating temperature, even under colder climatic conditions.
Thermal Management in Power Electronics for Electric Drive Systems
Serving as the channel between batteries and electric motors, power electronics have become a keystone of modern electric vehicles (EVs). In power conversion, components such as motor controllers and inverters play a pivotal role. Given their responsibility for managing high currents and voltages, these components inherently produce substantial heat. Thus, ensuring efficient thermal management is crucial for achieving optimal performance, safety, and longevity.
Design Challenges in Motor Controllers and Inverters
High-Power Density: Leading to increased power density, these components are becoming more compact as technology progresses. If unchecked, these concentrations can result in "hotspots," potentially leading to performance degradation or even component failure.
Varying Load Conditions: The load on motor controllers and inverters changes frequently in real-world driving scenarios. The fluctuating heat generation rates resulting from this varying load necessitate a thermal management system capable of prompt adaptation.
Integration with Other Systems: Operating in isolation, these power electronic components do not function independently. Being integral components of a larger system, it is imperative that their thermal management solutions align with the vehicle's overarching thermal strategy.
Cooling Solutions and Their Impact on Performance
Air Cooling: Although it represents the most basic form of cooling, air cooling is generally limited to low to mid-power applications because of its comparatively lower cooling efficiency. However, its effectiveness is improved by advances in design, such as fin optimization and increased airflow dynamics.
- Impact: Ideal for vehicles with aggressive performance demands. On the contrary, the larger size of air-cooling solutions may not align well with the compact designs of certain EVs.
Liquid Cooling: Circulating liquid coolants, typically composed of a blend of water and glycol, efficiently draw heat away from the components, surpassing the effectiveness of air cooling. Its superior heat extraction capabilities make this method prevalent in high-performance EVs.
- Impact: Promoting enhanced performance, enabling a more compact design, and ensuring the longevity of components, even under high-stress conditions, liquid cooling stands out as a beneficial solution.
In electric drive systems, the thermal management of power electronics is a multifaceted challenge. Despite the persistence of design challenges, innovative cooling solutions have proven highly successful in maintaining performance and safeguarding the integrity of these essential components. These thermal tactics will undeniably play an imperative role in shaping the EVs of the future as the automotive industry continues its shift towards electrification.
直接登录
创建新帐号