Introduction to the Harsh Environment of Automotive Electronics
Modern cars have evolved largely due to advancements in automotive electronics. Electronics have become an essential feature of cars, appearing in everything from simple ignition systems to advanced driver-assistance technologies. But the automobile counterparts have to contend with a tough, unforgiving environment, unlike most typical consumer gadgets. Thus, ensuring that these systems operate dependably under all external situations presents a challenge to designers and engineers.
Complex Operating Conditions: From the bitterly cold winters of Alaska to the sweltering summers of the Sahara, automotive electronics are supposed to function flawlessly in a wide range of environmental circumstances. They come into contact with abrupt temperature variations, which are quite stressful on electronic parts. These extreme temperatures not only cause material expansion and contraction but also abrupt temperature fluctuations, which puts stress on the electronic assemblies.
Vibrational and Mechanical Stresses: An automobile's operational environment is dynamic by nature. Vehicle electronics are subject to vibrations all the time from the speed, potholes, and engine revving. If these oscillatory motions are not properly managed, they may result in premature failure, fatigue, and even disconnections.
Exposure to Contaminants: An automobile's undercarriage is not the cleanest area in the world. The car's construction allows for the infiltration of dirt, water, dust, and even salts (particularly in regions where roads are salted throughout the winter). Electronic component deterioration, short circuits, and corrosion can result from these impurities, particularly when coupled with dampness.
High Electrical Stresses: With its plethora of sensors, actuators, and computers, the vehicle electrical system is a complicated network of high voltages and currents. Various transient circumstances like load dumps and surges might subject the components to elevated electrical stresses.
Integration with other Systems: The electronics in automobiles work together. They are integrated and work with a variety of other systems, including pneumatic, hydraulic, and mechanical ones. The necessity for resilience is further highlighted by this interconnection, since a breakdown in one system can have a domino effect on other systems.
Automotive electronic systems traverse a perilous trajectory. In addition to guaranteeing functionality, they also need to exhibit exceptional robustness and dependability. Because of these strict specifications, specific design philosophies, material choices, and testing procedures have been developed to make sure automotive electronics can withstand the demands of their particular operating environment.
Vibration
Due to both internal vehicle operations and external environmental conditions, automotive electronics are constantly exposed to varying degrees and types of vibrations. If not sufficiently addressed, these vibrations may negatively impact the functionality, dependability, and lifespan of electronic components.
Typical Vibration Levels and Types in Automotive Electronics
Random Vibration: In contrast to its periodic counterparts, random vibration is unpredictable and can originate from many factors, including engine turbulence and uneven roads. Because of its unpredictable nature, it is a primary issue and is characterized by its spectrum intensity.
Sinusoidal Vibration: This is a regular frequency periodic vibration that is usually caused by spinning components such as tires or engines. Although it is predictable, the vibration's effects can be amplified by resonating with specific components.
Shock: Shock is a rapid, strong force or acceleration, similar to what happens when you hit a pothole or are in the terrible case of an accident, but it is not a constant vibration. Electronics must be able to sustain such sudden loads without malfunctioning.
Design Considerations to Minimize Vibration at a Component Level
Component Mounting: The proper fasteners, adhesives, or soldering procedures should be used to mount components securely. Flexible mounts or dampers can be used to absorb and disperse vibrational energy for bigger components, such as electrolytic capacitors or relays.
Component Selection: Certain parts are made to be more vibration-resistant than others. For example, solid-state electronics might be favored over those that have moving elements. Additionally, for automotive applications, components with higher inherent G-force tolerance should be used.
Circuit Board Design: Vibration can be considered when designing printed circuit boards (PCBs). Using thicker boards, cutting down on trace length, and adding tie points or anchors are some of the techniques. Cycle fatigue can be a major cause of component failure in cases of board flex.
Enclosure and Packaging: Vibrations can be reduced by the enclosure itself in certain situations. The use of damping layers or materials with built-in damping capabilities can be advantageous. Vibration impacts can also be lessened by the enclosure's general form and design, including any internal bracing or support.
Resonance Avoidance: Ensuring that no assembly or part has a natural frequency that coincides with the vibration frequencies the vehicle experiences regularly is vital. Vibrations can be greatly amplified by resonance, leading to an abrupt failure. FEA analysis is typically performed to determine the system's and its component's self-resonance frequencies.
Environmental Testing: To replicate real-world conditions, all designs must lastly go through extensive vibration testing. Before the component is mass-produced, this aids in the identification of any potential weak areas or resonances.
In conclusion, vibration management in automotive electronics design is critical due to the dynamic nature of automobiles. The durability and dependability of vehicle electronic equipment can be guaranteed by engineers by comprehending the origins of these vibrations and planning with mitigation in mind.
Humidity
Due to variations in temperature, geographic location, and regular vehicle use, humidity is a constant problem for car electronics. Vehicles work in various temperature regimes and are tight spaces, so condensation is regular. If not handled properly, this could negatively impact electronic systems.
The Effect of Humidity on Electronic Components
Particularly when coupled with other impurities, humidity can hasten corrosion, result in short circuits, or even induce dendritic growth in the spaces between conductive lines. For example:
Corrosion: Prolonged moisture exposure can cause the majority of metals used in solder joints and electronic components to corrode, which will reduce the component's lifespan and performance.
Electrical Leakage: A PCB's surface may become conductive due to moisture, which can result in parasitic currents that impair circuit functionality or cause it to fail completely. The degree of board contamination affects the parasitic current's value as well.
Delamination: PCB moisture absorption can cause conformal coating layer or solder resistance to delaminate, increasing the board's vulnerability.
Coating and Potting Technologies
Protective measures are needed to address humidity issues; coatings and potting are two of the most popular ones.
Coatings: PCB surfaces are directly coated with these thin layers, which are frequently only a few micrometers thick. While offering protection from pollutants and moisture, they also make repairs and rework simpler. Typical coatings consist of urethane, silicone, and acrylic.
Potting: To form a solid insulation, this entails covering the entire electrical assembly with a material that is either solid or gel-like. Although potting provides excellent resistance to moisture and physical harm, it almost completely prevents future repairs or rework. Common potting chemicals include silicone, polyurethane, and epoxy.
Breather Vents to Reduce Humidity and Pressure Levels Inside an Enclosure
Function: In order to balance the pressures inside the housing and outside, breather vents function in two ways: they let gases and air flow freely back and forth. These breather vents therefore swiftly correct the temperature and pressure imbalance that results from a sudden, chilly thunderstorm striking a housing that has been scorching in the sun all day. This can shield enclosures from deformation brought on by pressure in addition to protecting seals from stress. Additionally, this degree of breathability can lessen the frequency and intensity of condensation.
Breather Design: Vents frequently have membranes that let air through but keep liquid water out, keeping the interior dry even in wet or splash-prone conditions. Desiccant materials, which actively collect and retain moisture, are also incorporated into some sophisticated vents to further lower interior humidity levels.
Placement: Vent placement is very important. They must be placed away from splashes and debris where they can effectively exchange air. Furthermore, the accumulation of outside impurities shouldn't impair their functionality.
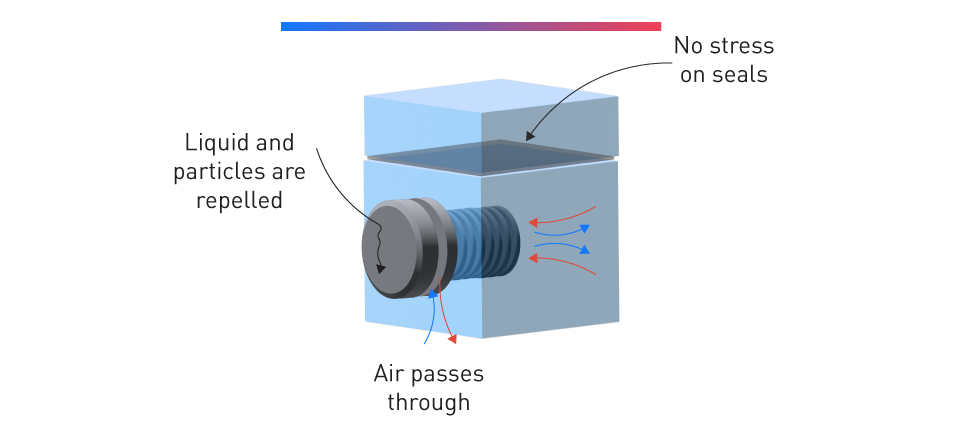
Figure 1: Example Application of a Breather Vent
In conclusion, it is impossible to exaggerate the impact of dampness on car electronics. The ongoing demand for additional electronics in cars makes humidity management through coatings, potting, and ventilation techniques essential. Even in the face of changing climatic circumstances, electronics are made to be durable and dependable through proper design and preventive actions.
Thermal Shock
Thermal shock is a natural environmental stress in the field of automotive electronics. It is defined as a sudden and severe change in temperature that occurs quickly and exposes electronic components to extreme temperatures. Given the variety of climates and operating circumstances that vehicles encounter, the significance of comprehending and mitigating thermal shock cannot be emphasized.
Typical Thermal Shock Requirements in Automotive Electronics
Range: It is widely believed that automotive electronics will not malfunction in temperatures ranging from -40°C to 125°C. These numbers may even be higher given the particular purpose of the car and the target market.
Cycle Duration: The length of the thermal cycle, or the amount of time at high and low temperatures, might change depending on the component in issue and the testing guidelines. At each temperature extreme, typical durations could range from a few minutes to several hours.
Cycle Repetitions: Automotive electronics may undergo hundreds or even thousands of temperature cycles during testing to guarantee durability and dependability.
Testing Chambers: To replicate these circumstances, standardized test chambers—also referred to as thermal shock chambers—are employed. These chambers are capable of quickly switching between extremes of temperature to replicate real-world situations.
The Effect of Thermal Shock on Soldering and Enclosure Sealing Fatigue
Solder Fatigue: The crucial connections in electronic assemblies, solder joints, are particularly weak points. These joints may break or even come apart due to thermal expansion and contraction. The pressures on solder junctions joining two dissimilar materials might be particularly high because various materials expand at different rates. The solder experiences work hardening throughout repeated cycles, which makes it more brittle and prone to failure. The cross-section microscope study of surface mounted electronic components that were heated to a high temperature is shown in the accompanying image. The solder joint between the component's lead and the copper footpad of the printed circuit board is where the crack is visible.
Component Warping: Rapid temperature variations can cause internal tensions that can cause other components, like ceramic capacitors or IC packages, to distort or crack.
Enclosure Seals: Additionally susceptible to damage are the seals that keep impurities and moisture out of electronic enclosures. Gaskets and sealing materials can deteriorate, lose their flexibility, or even shatter with frequent heat cycling, which could compromise the protective properties of the enclosure.
Material Considerations: The resistance of an assembly to thermal stress can be greatly influenced by the solder alloy, PCB material, and component package types selected. Engineers frequently select materials with complementary or matching coefficients of thermal expansion (CTEs) in order to reduce these stresses. For instance, ceramic is frequently used as a PCB material with superior thermal conductivity and a complimentary CTE with the delicate ceramic capacitors and resistors in high temperature settings, such as automatic transmissions.
Automotive electronics design and dependability are severely hampered by thermal shock. It's critical to comprehend the usual specifications and how they affect soldering and enclosures. Automobile engineers may guarantee the long-term dependability of electronic systems even in the most severe circumstances by taking these considerations into account early in the design process and selecting materials and constructions that can tolerate these burdens.
Water and Dust Ingression
In automotive electronics, it is pivotal to maintain protection against water and dust. Automobiles frequently encounter a variety of environmental conditions, such as dusty roads and severe downpours, so protective measures against these factors are necessary. The IP rating is one of the main standards used by the industry to gauge and define enclosure protection levels.
What is an IP Rating?
Definition: IP stands for "ingress protection". The IP rating system is an internationally accepted method for grading the level of protection offered to electrical enclosures against the infiltration of solid objects, dust, water, and accidental contact.
Format: Usually, an IP rating consists of two integers. The degree of protection against solids (such as dust) is indicated by the first digit, and the degree of protection against liquids (usually water) is indicated by the second. An IP65-rated gadget, for example, is resistant to water jets and dust.
Solid Protection (First Digit)
- IP0x: No special protection
- IP1x: Protection against objects >50mm
- IP6x: Dust-tight, no ingress of dust
Liquid Protection (Second Digit)
- IPx0: No protection
- IPx4: Protection against water splashes from any direction
- IPx7: Protection against temporary immersion in water
- IPx9k: Protection against close-range, high-pressure water sprays
Note that a system does not always meet all lower level IP rating protection levels just because it has a higher IP rating. For example, a system rated IPx9k can tolerate short-term high-pressure water spray testing, but it may not be able to endure longer-term IPx7 water immersion tests since the ingress mechanisms used in these tests differ. As a result, it is frequently necessary to run the system through each IP rating test independently.
IP Rating Requirements Based on Vehicle Packaging Locations
Engine Compartment: This region may experience elevated temperatures, possible fluid leaks, and pollutant infiltration. An IP67 or IP69k rating is usually necessary for electronics in this area, particularly if they are going to be in close proximity to coolant, lubricants, or cleaning agents.
Undercarriage and Wheel Wells: These components in these areas are constantly exposed to mud, road debris, and splashes because of their close proximity to the road. For parts like ABS sensors or transmission modules, a high IP rating, like IP68, is frequently required.
Interior Cabin: Infotainment systems and HVAC controllers are examples of interior components that are often less exposed to moisture and dust. They often need an IP42 rating, though, as they should be able to withstand the odd spill or splash.
Door Panels and Side Mirrors: Certain parts, such as side mirror adjusters and window regulators, must be shielded from possible water intrusion from rain or car washes. These components would be appropriate for an IP65 rating.
Roof and External Sensors: Particularly when it comes to ADAS and autonomous driving, cameras, LiDARs, and other external sensors need to be able to withstand a variety of weather conditions, such as rain, snow, and dust. They frequently fetch high IP ratings, such IP67 or above.
Ultimately, it is imperative to comprehend the IP rating system and the several prerequisites that are contingent upon the positioning of electronic components within a vehicle. Automobile manufacturers may greatly improve the robustness, dependability, and security of their electrical systems by making sure that the right kind of ingress protection is in place. Achieving the appropriate IP ratings and protecting electronics from the challenging automotive environment depend heavily on proper sealing, gasketing, and enclosure material selection.
Cleanliness in Automotive
High standards of cleanliness are required in the automobile industry, particularly for the Printed Circuit Board Assembly (PCBA). This goes beyond aesthetics. Contaminants on the board can result in a wide range of problems, from component failures to electrical malfunctions. Let's examine the requirements, issues, and safeguards pertaining to cleanliness in car electronics in more detail.
IPC Standard Requirements for PCBA Cleanliness
Overview: Standards for PCBA cleanliness have been established by the IPC (Institute for Printed Circuits), notably IPC J-STD-001 and IPC-CH-65B. They serve as benchmarks for judging if electronic assemblies are acceptable on a worldwide scale.
Resistivity of Solvent Extract (ROSE): This is a typical test procedure that is described in the IPC standards. It involves washing the PCB in a solvent and measuring the solvent's resistivity to find out how contaminated it is with ions.
Thresholds: The previous acceptable level was 1.56 micrograms of ionic contamination per square centimeter. But given that electric component packages are getting smaller by the day, IPC advises against using any kind of threshold to decide what constitutes sufficiently clean. According to the updated recommendations, the board must undergo a Dewing test or a SIR (Surface Insulation Resistance) test.
Corrosion and Dendrites as a Result of Dirty Production Process
Corrosion: Metal components may corrode if there are ionic impurities remaining on the board. These impurities can form conductive pathways when coupled with moisture, which might result in unforeseen electrical currents that can damage components.
Dendritic Growth: Corrosion on the surface of printed circuit boards is known as dendritic growth, or electro-chemical migration. These are very little metallic growths that resemble threads and can develop in between electrical channels. Since dendrites are conductive, they may cause electrical shorts in devices. Ionic pollution, moisture, migration-prone metal in component leads, and voltage bias are the combined causes of them.
Preventive Measures
Clean Production: The inception of clean production commences at the manufacturing stage. Regular monitoring of production line cleanliness, utilization of high-purity solvents, and the commitment to maintaining a clean environment are crucial measures for significantly minimizing contaminants.
PCBA Coating: When a conformal coating is applied to PCBA, it acts as a protective layer, effectively sealing existing contaminants and guarding against external factors such as mechanical abrasions, moisture, and contamination. Acrylics, silicones, and urethanes represent different types of coatings, each offering distinct advantages tailored to specific applications. Ensuring sufficient coating thickness on electronic surfaces, particularly component leads and terminals, which feature bending corners where surface tension opposes coating material application, is imperative.
Preventing Condensation: In many contamination-related problems, moisture is a catalyst as it assists in making the conductive ionic channel that is mandatory for corrosion to occur. Enclosure designing is imperative to prevent condensation. Several measures can be enacted to mitigate internal condensation:
- Hermetically Sealed Metal Enclosure: Due to its nature of high humidity absorption, plastic enclosures are susceptible to condensation, resulting in the accumulation of water inside. However, sufficient protection is provided by the metal enclosures.
- Place Components Far from Each Other: As the distance between electric potentials increases, the likelihood of corrosion forming between voltage potentials and impacting the circuit diminishes.
- Protective Coating: As aforementioned, protective coatings not only safeguard against contamination but also assist in preventing condensation from affecting the electronics.
- Potting: Potting can entirely cover the electronic components and offers solid insulation.
- Breathing Vents: For equalizing external and internal pressures and removing internal humidity, breathing vents are useful.
Regular Inspection: The utilization of inspection techniques, such as Ion Chromatography or visual examinations under microscopes, during production lines can assist in the early identification and prevention of contamination-related issues.
In conclusion, cleanliness is non-negotiable in automotive electronics. The objective extends beyond merely creating functional components; it encompasses guaranteeing longevity, reliability, and optimal performance throughout the product's entire lifecycle. For essential functions, vehicles rely more on complex electronic systems, the significance of these standards and practices will inevitably expand further.
直接登录
创建新帐号