Introduction to Vehicle Electrical Systems
With the inclusion of advanced electrical systems, the sector of modern vehicles has transformed. The functionality of a vehicle relies heavily on these systems, as they drive fundamental operations ranging from essential lighting and ignition to advanced safety features and infotainment. For automotive engineers and technicians, grasping vehicle electrical systems holds paramount importance as it merges emerging electronic technologies with traditional mechanical engineering principles.
Definition: The network comprising electrical components, wiring, and circuits within a vehicle constitutes its electrical systems, responsible for generating, storing, and distributing electrical energy throughout the entirety of the vehicle. Careful design and maintenance of this intricate network are imperative to ensure the seamless delivery of power to diverse subsystems without inducing interference or failures.
Components
The vehicle electrical systems consist of the below mentioned main components:
Battery: Acting as the primary pool of electrical energy, it supplies power when the engine is inactive and assists in initiating the engine's startup process. In contemporary times, lithium batteries are increasingly dominating as the preferred type, extending even to the 12V systems in newly manufactured vehicles.
Alternator: In charge of producing electrical energy during engine operation, preserving the battery's charge, and supplying power to the vehicle's electrical components, aided by its internal voltage regulator.
Starters: Starters draw energy from the battery to turn the engine over and are used to initiate the engine’s function.
Wiring and Connectors: A network of cables and connections interconnects electrical components and circuits within the vehicle, facilitating the transmission of energy and signals throughout its systems.
Fuses and Relays: Safety features are designed to avert electrical overloads and enable the management of high-power devices via lower-power circuits.
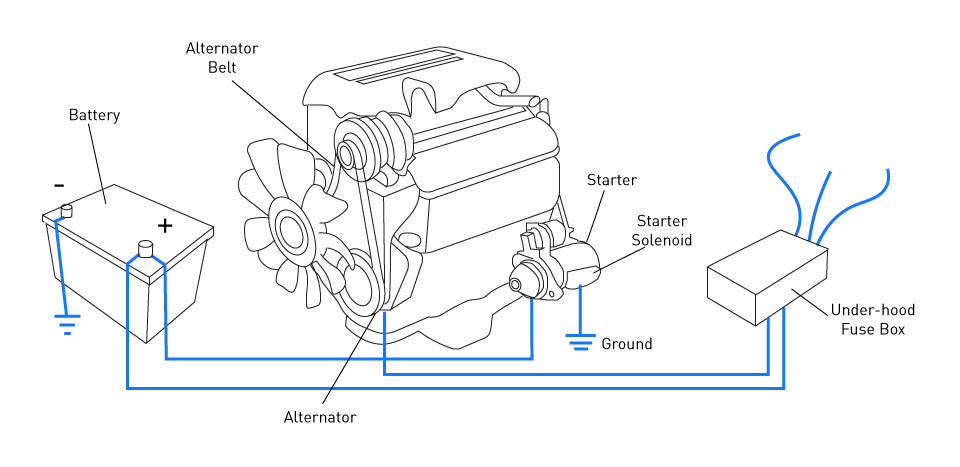
Figure 11: Main components of Vehicle Electrical System
Functionality: To produce, distribute, and handle the electrical energy needed to regulate numerous vehicle operations is the main function of vehicle electrical systems. These systems allow a huge range of conveniences and requirements from charging mobile devices to starting the engine.
Integration with Electronics: With the increase of electronically controlled devices, the difference between electrical and electronic systems in vehicles has continuously become blurred. Modern electrical systems have seamlessly fused with electronic control units, sensors, actuators, and communication networks, establishing a unified ecosystem conducive to advanced control and seamless communication.
Evolution: The technological advancements within the automotive industry are displayed by the emergence of vehicle electrical systems. Simple electrical circuits for lighting and ignition are dependent on early vehicles. The implementation of power windows, air conditioning, and advanced safety systems resulted in the development of intricate electrical architectures. In the present era, electric and hybrid vehicles continue to expand horizons, demanding intricate and highly efficient electrical systems tailored for high-voltage applications.
Within automotive engineering, the introduction to vehicle electrical systems provides a glance into a crucial and multifaceted field. With the ongoing evolution of vehicles, their increasing complexity and capabilities elevate the significance of electrical systems. This necessitates a comprehensive grasp of principles, components, and optimal practices. Armed with this foundation, engineers and technicians can adeptly tackle the challenges and seize the opportunities brought by contemporary vehicles, be they traditional internal combustion engines or state-of-the-art electric vehicles. Welcoming the intricacies inherent in vehicle electrical systems doesn't just stimulate innovation; it also guarantees the safety, efficiency, and reliability of the vehicles that interconnect our world.
Role of Electrical Systems in Vehicles
In contemporary vehicles, electrical systems surpass their traditional role of supplying power, evolving into multifaceted components that intricately interact with diverse subsystems, notably electronics. In this section, we will delve into the significance of electrical systems and their dynamic collaboration with electronic components, highlighting their combined efforts in establishing a cohesive and effective operation.
Interaction with Electronic Systems
Integration of Systems: Vehicle electrical systems have evolved beyond standalone entities and are now intricately interconnected with electronic systems. As vehicles embrace more advanced technologies, the complexity of integration between electrical and electronic systems has notably intensified. Communication between electrical and electronic systems is pervasive from engine control units (ECUs) to advanced driver-assistance systems (ADAS).
Control and Communication: The required power to electronic systems is provided by the electrical systems, however their role is beyond this basic function. The control between different parts of the vehicle is facilitated by electrical systems. Consider the scenario where sensor signals are relayed to ECUs, directing actuators based on the acquired data. This continuous cycle facilitates real-time adjustments and the optimization of performance.
Interconnected Networks: Communication between different electronic devices is enabled by vehicles having networks such as Local Interconnect Network (LIN) and Controller Area Network (CAN). To guarantee smooth communication and coordination among diverse subsystems, the electrical systems need to consistently deliver dependable power to these networks.
Energy Efficiency: Better energy management and efficiency are enabled by the collaboration between electrical and electronic systems. Capturing kinetic energy and converting it into electrical energy, systems such as regenerative braking in hybrid and electric vehicles store the generated power in the battery. In demonstrating the crucial role within modern energy-saving strategies, this interplay highlights the significance of electrical systems.
Safety and Reliability: To ensure safety and reliability, the synergy between electrical and electronic systems remains pivotal. The flawless synchronization of electrical and electronic components is the cornerstone on which safety features such as anti-lock braking systems (ABS) and electronic stability control (ESC) depend. Many systems incorporate fault detection and diagnostics, allowing for the early identification of potential issues.
User Interface and Convenience: In addition to powering electronic control units, electrical systems also supply energy to user interfaces like touchscreens and display units. Enabling interaction with diverse vehicle functions such as navigation, entertainment, and climate control, these interfaces emphasize the inseparable connection between electrical and electronic systems for both drivers and passengers.
The extensive and multifaceted involvement of electrical systems within vehicles, especially in their interplay with electronic systems, holds significant importance. Through this collaboration, intricate control, efficiency, safety, communication, and user convenience are facilitated. With the ongoing evolution of technology, the central focus of automotive design and engineering will persist in ensuring the seamless integration and interaction between electrical and electronic systems. For producing advanced, efficient, and safe vehicles that fulfill the demands of the modern world, understanding of this relationship is critical. It portrays a vision of a future in which vehicles transcend mere transportation, evolving into complex ecosystems interwoven with interconnected technologies.
Power Generation and Distribution
At the core of a vehicle's electrical system lies power generation and distribution, which sustain a myriad of devices and subsystems essential for ensuring seamless operation, safety, and convenience. Within this section, the fundamental elements of power generation and distribution are explored, encompassing alternators and starters, relays and contactors, as well as power distribution units.
Alternators and Starters
Alternators:
In continuous power generation within a vehicle, alternators serve an imperative role. When the engine operates, these systems transform mechanical energy from the crankshaft into electrical energy. This electricity serves the dual purpose of recharging the battery and energizing diverse electrical systems within the vehicle.
Design and Operation: The composition of modern alternators commonly comprises a rectifier, rotor, stator, and voltage regulator. As the rotor rotates within a magnetic field, it initiates the generation of an alternating current (AC) within the stator windings. Subsequently, the rectifier's function is to transform this alternating current (AC) into direct current (DC), fulfilling the electrical requirements of the vehicle.
Regulation: Ensuring a voltage supply of around 14.5 V, voltage regulators maintain the output voltage within specified limits. It's notable that while the voltage regulator typically ensures a nearly constant voltage, it's not always entirely reliable. Hence, all modules powered by the battery must meet the universal requirement of operating within the 9V-18V range. Moreover, network communication should sustain functionality even at battery voltages as low as 6V.
Starters:
To initiate the combustion process, starters are responsible for cranking the engine. To turn the engine over during the start phase, they transform electrical energy from the battery into mechanical energy.
Design: A solenoid, gear, motor, pinion gear, and drive mechanism are present in the starters. The solenoid engages the pinion gear with the flywheel, and the motor turns the engine over when the ignition switch is turned.
Importance: The failure of starters can make the vehicle inoperable, so the starters must be robust and dependent.
It's important to highlight that starters create a transient known as "cranking" on the battery line. In colder temperatures, this cranking effect intensifies and might reduce the battery voltage to as low as 3V, aligning with the transient immunity standards for battery supply. This occurrence is commonly termed "cold cranking."
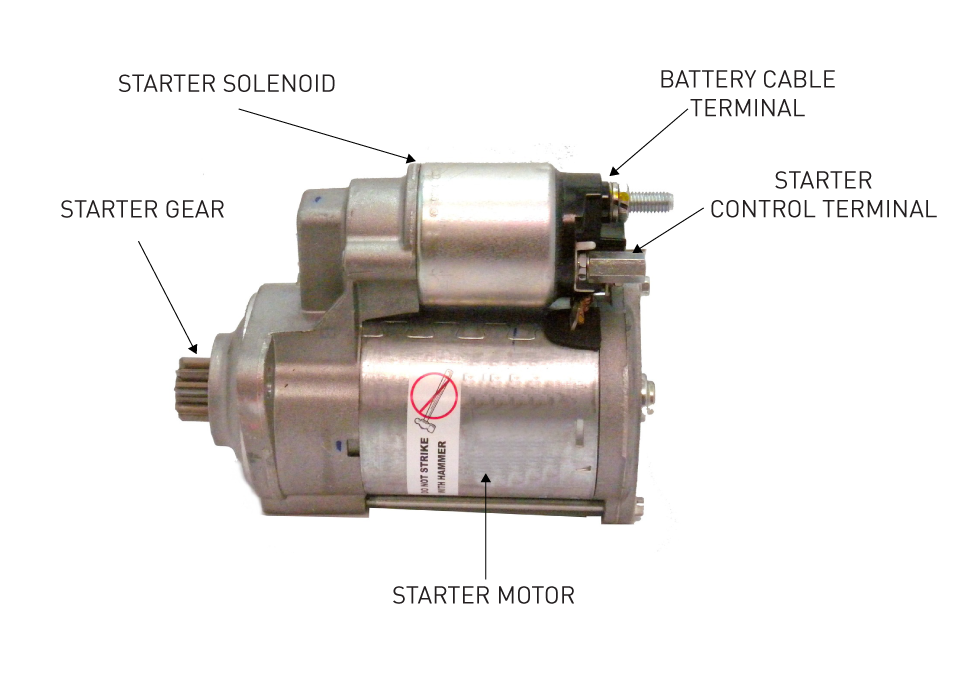
Figure 12: Picture of a starter
Relays and Contactors
Relays:
Electrically operated switches that handle circuits within the vehicle are known as relays.
Functionality: Through the utilization of a small signal to regulate a significantly larger current, relays facilitate the management of components within the low-voltage system, including fans, headlights, and fuel pumps.
Types: There are different types of relays such as solid-state, electromagnetic, and thermal relays, each caters to different applications.
12V-48V and 30A are the typical ratings of automotive relays. Low-voltage systems are their intended users.
Contactors:
Contactors operate based on similar principles to relays; however, their design caters to managing high power levels and finds common usage in electric vehicle applications.
Use Cases: Contactors play a frequent role in electric vehicles, facilitating the secure connection or disconnection of the battery pack to ensure safe operational conditions. Contractors find another application in the onboard high-voltage charger system, serving to link the EV charging equipment with the onboard charger.
The electric loads on the bus produce inrush current due to their input capacitances when closing a relay or contactor. This inrush current has the potential to reach levels that are 10 to 100 times higher than their usual nominal current consumption. Hence, when choosing the suitable relay or contactor for an application, it's crucial to assess their capacity to endure the frequency of inrush current occurrences over the vehicle's lifespan.
As the contacts are opened while the loads draw current, voltage transients are produced along the supply cables owing to the inductive kickbacks resulting from cable inductance. Excessive voltage transients can damage the switch.
Power Distribution Units (PDUs)
The allocation of electrical power throughout the vehicle is regulated by PDUs, directing it to different subsystems based on their respective requirements.
Functionality: To distribute power efficiently and offer safety from overcurrent or short-circuit conditions, PDUs include relays, switches, and fuses.
Integration: Providing diagnostic capabilities and intelligent power management, advanced PDUs incorporate with vehicle control systems.
The intricate process of generating and distributing electrical power within vehicles involves a multifaceted interplay among distinct components, each possessing specific roles and characteristics. Commencing the engine's operation using starters, consistently supplying the vehicle's electrical requirements through alternators, overseeing high-power devices via relays and contactors, and efficiently distributing power through PDUs, these elements constitute the fundamental framework of the vehicle's electrical infrastructure. For automotive engineers and technicians striving to guarantee the dependability and effectiveness of contemporary transportation systems, comprehending their operation, functionality, and integration stands as a crucial necessity.
Wiring and Cabling
The intricate network of wiring and cabling serves as the vehicle's nervous system, interconnecting diverse components and systems within the automobile. Within this section, an extensive overview is presented regarding the principal components of this network: wiring harnesses, connectors, terminals and their crucial functions in upholding the vehicle's functionality are thoroughly examined.
Wiring Harnesses
The assembling of electrical cables or wires is known as wiring harnesses that serve as the conduits transmitting signals or electrical power throughout an automobile. Their design aims to maximize the wiring system's organization, safeguarding its components while ensuring flexibility in operation.
Design and Structure:
Insulation and Conduit: Insulation of wires within the harness prevents short circuits, often bundling them in a protective conduit to withstand environmental elements like moisture, heat, and abrasion.
Routing and Layout: Careful planning of a wiring harness layout is essential to minimize electromagnetic interference (EMI), lower the chances of wear and damage, and simultaneously enable easier diagnostics and repairs.
Standardization: The design of wiring harnesses adheres to industry standards, guaranteeing compatibility, safety, and quality consistency among various manufacturers and models.
Functionality and Applications:
Transmission of Signals and Power: Data signals between controllers, sensors, actuators, and various electronic devices are transported through wiring harnesses. Additionally, these harnesses distribute electrical power to a multitude of components, including lights, fans, and motors.
Vehicle Subsystems Integration: Allowing for modular assembly and specialized functionalities, distinct harnesses are frequently tailored for diverse subsystems such as the engine, chassis, or infotainment.
Connectors
Vital elements within the vehicle's electrical system, connectors and terminals play a crucial role in facilitating both the physical and electrical connections of wires.
Types and Designs: An array of shapes, sizes, and types characterizes connectors, all customized to match specific applications and distinct requirements. The electronics' IP (Ingress Protection) requirement is determined by the locations where the vehicle packaging takes place. Varied IP requirements necessitate the use of connectors with different levels of IP protection. For instance, the area under the vehicle bonnet presents a harsh water ingress environment. Components placed there might be immersed in water from below and subjected to high-pressure, high-temperature jet washing by users aiming to clean the space beneath the bonnet. Hence, it's essential for these connectors to hold ratings of IPx8 (for immersion protection) and IPx9 (for jet wash protection) as well.
Locking Mechanisms: Numerous connectors are equipped with locking mechanisms to guarantee secure connections, effectively preventing accidental disconnection caused by vibration or pulling forces. The locking mechanism plays a crucial role in minimizing fretting between the plug and receptacle terminals, which are in contact with each other. This action is vital as fretting, occurring during vibration, can potentially damage the contact surfaces and lead to fretting corrosion.
Standardization: Similar to wiring harnesses, adherence to specific standards is crucial for connectors to ensure compatibility and reliability across diverse systems and vehicles.
Terminals: The pins within connector terminals establish the electrical contact between the plug and receptacle components. Choosing the terminal plating material is a critical decision, heavily reliant on both the application and the vehicle's packaging location. In scenarios where minimal current flows through the terminals, it's advisable to avoid tin plating due to its susceptibility to galvanic corrosion. Since no heating current is available to remove the oxide layer, gold plating stands as a more durable solution in such cases.
The reliable operation of modern vehicles heavily relies on the foundational aspect of wiring and cabling within the vehicle's electrical system, which includes the strategic design and implementation of wiring harnesses, connectors, and terminals. The intricate interaction among multiple subsystems, ranging from engine control to entertainment and safety features, is mirrored in the complexity of this network. Engineers, designers, and technicians involved in automotive electrical systems must grasp the characteristics, functionality, and standards governing these components. This understanding is crucial as it enables innovation while upholding safety and performance standards without compromise.
Grounding and Shielding
Grounding and shielding are imperative factors of the electrical system design in the complex automobile environment. In maintaining the dependability, and functionality of the vehicle, these concepts play a critical role. Exploring the significance of adequate grounding and methods employed to shield electrical systems against Electromagnetic Interference (EMI) is the focus of this section.
Importance of Proper Grounding
To ensure a stable reference voltage, grounding is a practice of electrically connecting elements to a common ground point, usually the vehicle’s frame or chassis. For multiple reasons, proper grounding is crucial:
Voltage Stability:
Reference Point: A common reference point for various electronic elements is provided by grounding with assurance that voltage levels remain consistent across the system. Here, the reference point shows that each signal level reading is compared with the ground voltage.
Noise Reduction: Leading to more correct signal processing and control, proper grounding reduces voltage fluctuations and noise. Indeed, vehicle components must sustain operational status within a ground shift voltage range of +- 1V, a criterion that necessitates validation through design. This specific requirement mitigates the susceptibility to potential ground voltage fluctuations.
Techniques for Shielding from Electromagnetic Interference (EMI)
Data corruption, unexpected behavior, and malfunction in electronic systems can be caused by electromagnetic interference. To safeguard from this type of interference, shielding techniques are used. Protection from noise emission is considered as a more complex task than protection from immunity in almost all cases:
Shielding Materials:
Metal Enclosures: To surround sensitive or noisy elements, metal enclosures are frequently employed. Protection from magnetic and electric noises are provided by the metals. The noise gets cancelled by a process known as “Eddy-current”, if a magnetic noise couples to the metal enclosure. When an electric type of noise couples with the enclosure, it gets redirected along the surface of the enclosure, preventing the noise from permeating to the opposite side of the enclosure wall.
Ferrite Beads: Utilized for the suppression of high-frequency noise within electrical circuits, they function as effective filters against electromagnetic interference (EMI). Beads are notably advantageous due to their cylindrical shape, allowing easy attachment around a wire harness. This external application serves as a palliative to an electronic module beyond its enclosure, effectively filtering its emitted noise.
Cable Shielding:
Coaxial and Twisted Pair Cables: By carrying electric fields within the cable or by cancelling out electromagnetic fields, these cable designs inherently decrease EMI.
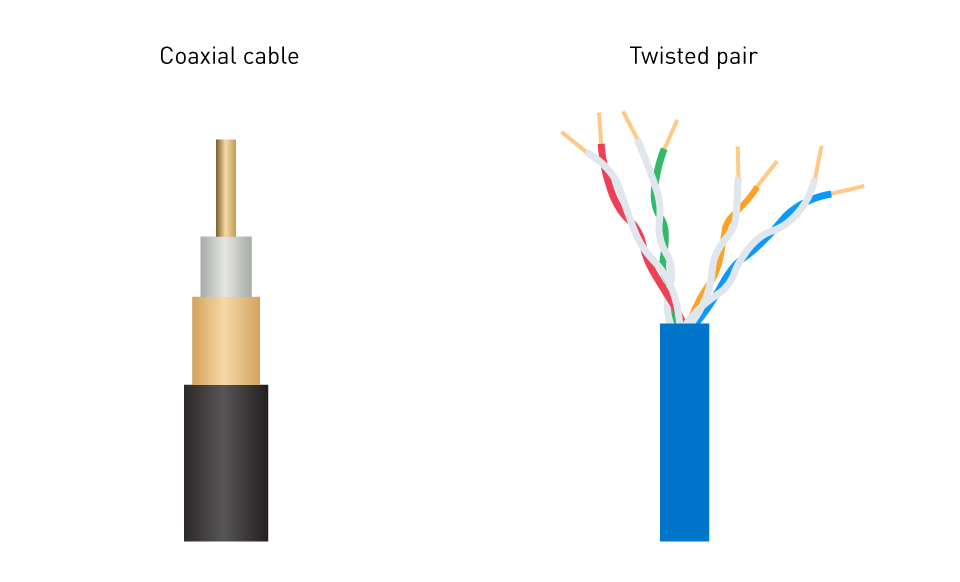
Figure 13: Coaxial and Twisted Pair cables
Grounding Strategies:
Ground Planes and Loops: The best grounding strategy remains a topic lacking consensus. Typically, ground planes are ideally continuous; however, designers may opt to introduce cutouts in the plane to redirect higher frequency signals away from delicate analog circuitry. To reduce loop inductive and plane capacitive emissions to the surrounding, another important rule is to minimize ground loops of higher frequency or high current signals.
Standards and Regulations:
Compliance with Industry Standards: CISPR is known as the main EMI standard. The general needs for electromagnetic emission and immunity of electric devices are contained by this. Car manufacturers in the automotive industry adopt CISPR as a foundational standard for their EMI needs, tailoring it to suit specific vehicle requirements. For instance, they may omit certain radio frequency emission band requirements that aren't pertinent to their vehicles.
Grounding and shielding constitute more than technical components in electrical system design; they form essential elements crucial to the overall safety, performance, and reliability of contemporary vehicles. Proficiency in grasping the fundamentals of effective grounding principles and the diverse methods used to mitigate EMI is imperative for automotive engineers and technicians. Facilitating the creation of sturdy and reliable electrical systems guarantees adherence to both legal and industry benchmarks. This underscores the pivotal role of grounding and shielding as foundational components in the realm of automotive electrical design. Adhering to EMI emission standards stands as the primary hurdle in automotive electronics design. Amidst the era of EV vehicle advancements, this task amplifies in complexity, posing an even greater challenge.
直接登录
创建新帐号