Introduction to Electronic Components in Automotive Systems
Contemporary vehicles embody intricate systems that seamlessly incorporate a diverse range of electronic elements, enabling capabilities that surpass simple point-to-point transportation. Handling everything from safety systems to entertainment, engine control, navigation, and more, these electronic elements have become a crucial part of the automobile. In this section, we will explore the overview of the diversity and roles of electronic elements in today’s automotive systems.
Overview of the Diversity of Electronic Components
Automotive electronics' ascent has spurred an unparalleled proliferation of components housed within vehicles. These contain but are not constrained to:
Sensors: Physical properties such as pressure, speed, temperature, and proximity are measured by sensors.
Actuators: Actuators are the mechanisms that transform electrical signals into physical actions, like solenoids and motors.
Electronic Control Units: Electronic Control Units like Body Control Modules (BCMs) and Engine Control Units (ECUs) handle numerous functions of the vehicle and engine body respectively.
Power Electronics: Within the vehicle, elements such as inverters and voltage converters manage and transform electrical power.
Communication Networks: Through protocols such as CAN Bus, FlexRay, LIN, and Ethernet, it allows intra-vehicle communication.
User Interface Components: User Interface Components like buttons, touchscreens, and display units enable human interaction with the vehicle’s systems.
Role of Electronic Components in Modern Vehicles
In modern vehicles, the wide range of electronic elements serves multiple crucial roles:
Enhanced Control: The vehicle can optimize its efficiency, emissions, and performance via ECUs and numerous sensors. Different driving conditions and styles can be adapted by advanced control techniques.
Increased Safety: For real-time decision-making and execution, attributes such as Electronic Stability Control (ESC), airbag control units, and Anti-lock Braking Systems (ABS) depend on electronic components.
Comfort and Convenience: Electronic elements improve the driving experience from climate control systems to advanced infotainment options.
Navigation and Connectivity: Offering navigation aids and allowing characteristics such as remote diagnostics, GPS modules, wireless communication interface, and Ethernet enable vehicles to be part of a wider connected ecosystem.
Energy Management: In electric and hybrid vehicles, energy management plays a pivotal role, where power electronic elements handle the flow of energy between motors, batteries, and other loads.
Autonomous Driving: Advanced electronic systems, capable of independently sensing, deciding, interpreting, and executing driving functions, are pivotal for the evolution of autonomous driving.
To summarize, advances in electronics have played a significant role in shaping the evolution of automotive technology. An array of sensors, power electronics, microcontrollers, actuators, communication modules, and user interfaces collaborate harmoniously to enhance the efficiency, safety, and enjoyment of contemporary vehicles. The synchronized operation embodies an amalgamation of engineering expertise spanning various fields, ensuring their pivotal involvement in an era of rising connectivity and autonomy within vehicles.
Sensors in Automotive Systems
In automotive systems, sensors have become an inseparable part of today’s vehicles. Offering crucial real-time information that contributes to safety, comfort, functionality, and efficiency, sensors are imperative for the car. In this section, we will explore the numerous types of sensors, and their different roles and applications.
Different Types of Sensors
Based on the physical quantities they estimate, automotive sensors can be categorized. Let’s check some of the important types:
Pressure Sensors: Within the brake system, engine, tires, etc., pressure sensors are used to measure multiple pressures. For example, to alert drivers about under-inflated tires, tire pressure monitoring systems (TPMS) rely on these sensors.
Temperature Sensors: In monitoring coolant temperature, cabin temperature, engine temperature, and oil temperature, temperature sensors are important. To maintain optimal working conditions and avert overheating, they enable the control systems.
Proximity Sensors: Proximity sensors, frequently employed within parking assistance systems, identify objects in close proximity and furnish drivers with feedback, thereby aiding in collision prevention.
Speed Sensors: Speed sensors are used to estimate the speed of multiple elements such as transmission output, engine speed, and wheels. For functions such as ABS and cruise control, they are important.
Oxygen Sensors: Oxygen sensors are found in the exhaust system and measure the oxygen levels in the exhaust gases, enabling the engine control unit to regulate the fuel mixture for optimized combustion.
Position Sensors: Position sensors are utilized to find the position of multiple elements such as crankshaft, camshaft, throttle, etc. For engine timing and performance, they are crucial.
Light Sensors: Based on ambient light levels, light sensors can automatically control headlights, improving convenience and safety.
Rain Sensors: Rain sensors are utilized to handle windshield wipers by adjusting their speed as per rain intensity.
Inertial Sensors: To detect the vehicle’s orientation and motion, inertial sensors like gyroscopes and accelerometers are used in stability control systems.
Roles and Applications of Sensors
In automotive systems, the applications of sensors are wide and continuously growing with progress in technology:
Engine Management: To make sure optimal engine performance, emissions control, and efficiency, sensors such as temperature, oxygen, and pressure sensors feed data to the ECUs.
Safety Systems: Offering real-time data to avert skidding and control loss, speed and inertial sensors are important in systems such as traction control, ABS, and ESC.
Comfort and Convenience: Through adaptive lighting, automatic climate control, parking assistance, and more, sensors improve the driving experience.
Fuel Economy: With accurate monitoring and control, sensors contribute to better fuel efficiency by ensuring the engine functionality within optimal factors.
Preventive Maintenance: Abnormalities can be detected by sensors. It also triggers timely maintenance, and eventually increases the lifespan of vehicle components.
Autonomous Driving: Future autonomous vehicles will rely on a wide range of sensors, such as radar, LiDAR, and cameras, essential for enabling the vehicle to perceive and engage with its environment.
In automotive electronics, sensors display one of the most crucial and versatile elements. Their roles are manifold from basic functionalities to advanced, intelligent characteristics. Advancements in automotive technology are expected to escalate the dependence on sensors, fostering increased innovation and their integration across various domains within vehicle design and operation.
Actuators in Automotive Systems
In automotive systems, actuators serve a basic role that transforms electrical signals into mechanical action. Collaborating seamlessly with sensors, they react to diverse control signals, executing vital functions within the vehicle. Exploring various actuator types, their multifaceted functions, and how they are employed in the automotive sector is the focus of this section.
Different Types of Actuators
Based on their function and the type of motion they develop, actuators in automotive systems can be classified. Some common types are:
Motors:
- DC Motors: DC motors are frequently utilized in windshield wipers, window regulators, and electric power steering.
- Stepper Motors: Stepper motors are used in HVAC systems for airflow control and to handle gauges.
- Brushless DC Motors: Brushless DC motors are employed in high-efficiency applications such as electric vehicles’ drivetrains.
Solenoids: To transform electrical energy into linear motion, solenoids are electromagnetic actuators. These are commonly utilized in door locks, starter systems, and fuel injectors.
Relays: Relays, although not classified as actuators in the conventional sense, function as switches capable of managing significant currents using a minimal control signal. In handling multiple actuators in the vehicle, relays are important.
Pneumatic Actuators: These actuators are compressed air to fulfill the desired motion, utilized in brake systems and suspension control.
Hydraulic Actuators: Hydraulic actuators are present in systems that need high force, like hydraulic power steering systems and brake actuators.
Thermal Actuators: Actuators of this type depend on materials capable of altering their shape based on temperature fluctuations, similar to the ones employed in the thermostatic valves within cooling setups.
Piezoelectric Actuators: They provide accurate control and quick response times usually found in modern fuel injectors.
Roles and Applications of Actuators
In automotive systems, the applications of actuators are varied, enclosing nearly every parameter of vehicle operation:
Engine Control: To optimize engine performance, emissions, and fuel efficiency, actuators handle air intake, exhaust flow, and fuel injection.
Transmission Control: Enabling smooth and efficient power transfer, electric and hydraulic actuators engage and disengage clutches and shift gears.
Climate Control: In HVAC systems, actuators handle temperature, distribution, airflow, elevating passenger comfort.
Safety Systems: Actuators offer the force required to handle the vehicle’s direction and speed in braking and steering systems. In systems such as electronic stability control (ESC) and anti-lock braking (ABC).
Convenience Features: Amenities like adjustable mirrors, automatic seat adjustment, power windows, and more are enabled by actuators.
Suspension Systems: Actuators within adaptive suspension systems dynamically alter stiffness and damping features, thereby enhancing both the ride quality and handling performance.
Emission Control: In exhaust systems, actuators manage the operation of emission control elements and the flow of gases.
Autonomous and Advanced Driver Assistance Systems (ADAS): Actuators will play a crucial role in future autonomous vehicles by carrying out intricate driving maneuvers seamlessly, eliminating the need for human intervention.
For the modern driving experience, actuators are necessary in automotive systems. Enabling a multitude of enhanced functions that elevate efficiency, performance, safety, and comfort, they offer mechanical reactions to electronic commands. It's crucial for automotive engineers to grasp the various kinds, functions, and uses of actuators, given their role in crafting and assimilating progressively intricate and smart systems within the forthcoming vehicle generations.
Electronic Control Units (ECUs)
At the core of a contemporary vehicle's electronic structure lie the Electronic Control Units (ECUs), functioning as primary processing hubs. These units decipher inputs from diverse sensors, overseeing and reacting to signals, and ultimately directing required operations through actuators. Exploring the nuances of these essential elements, the focus is directed toward Engine Control Units (ECUs) and Body Control Modules (BCMs) in this segment.
Overview of Control Units in the Vehicle
Within the vehicle, Electronic Control Units are specialized microcontroller units that control particular functions. From transmission shifting and engine performance to climate control, infotainment, and safety systems, they handle everything.
Basic Building Blocks of Electronic Control Units: The following main building blocks are included in ECUs:
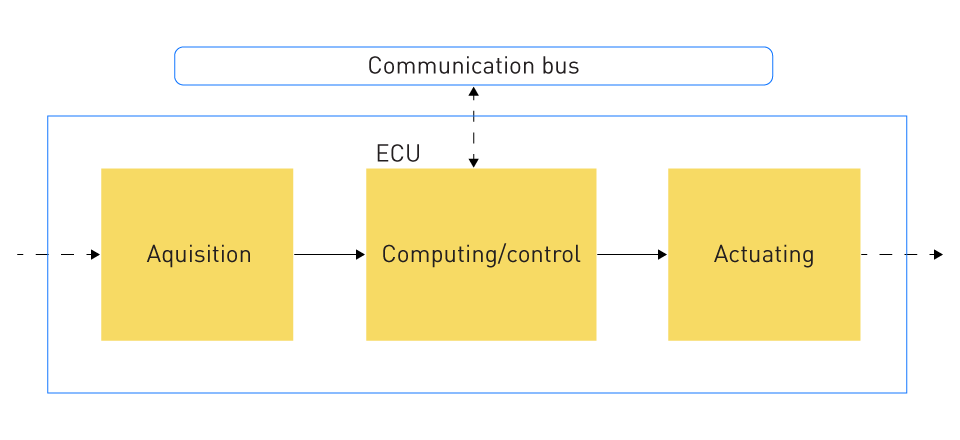
Figure 1: Basic building blocks of an ECU
The interface to the sensors linked with the ECU is known as “acquisition.” It either has digital or analog conditioning circuits. The microcontroller, encompassing computing and control functionalities, executes arithmetic logic operations along with its supporting components. Within the circuit, communication bus is the various type of connections (LIN, FlexRay, CAN, Ethernet, etc.) to the other ECUs. The term "actuating" refers to the collective switches within the module responsible for managing a range of electric loads, including motors, heaters, solenoids, and more.
Modularity: Modular in design, Electrical Control Units can be individualized modules catering to engine control, airbag systems, transmission control, and various other functionalities. With modern vehicles housing over 100 ECUs, numerous automotive suppliers specialize in designing these units for various aspects of the vehicle system. When observing a car manufacturer's vehicle, we admire not only the manufacturer but also acknowledge the diverse suppliers whose products are integrated into the system.
Integration: To ensure the complete vehicle system functions cohesively, control units interact with each other, sharing data and commands.
Real-time Processing: To respond to quickly changing conditions, like changes in vehicle speed, engine load, or driving conditions, multiple control units need real-time processing capabilities.
Adaptability: Control Units are becoming increasingly flexible and can be updated with new characteristics and optimization with the growth of software-defined functionalities in vehicles.
Engine Control Units (ECUs)
Due to its high complexity and significance, the Engine Control Unit (ECU, known by the same abbreviation as Electrical Control Unit) stands as one of a vehicle’s critical Control Unit, holding responsibility for overseeing and regulating the engine’s operations.
Functionality:
- Fuel Management: To increase performance, emissions, and fuel efficiency, the ECU estimates the optimal fuel-to-air ratio, manages the ignition system, and handles fuel injection timing.
- Monitoring Engine Conditions: To ensure the engine functions within safer aspects, the ECU continuously handles engine temperature, air intake, exhaust gases, engine temperature, and other parameters.
- Emission Control: The ECU serves a critical role in meeting emission standards by combining with systems such as the catalytic converter and the exhaust gas recirculation (ECG).
Adaptation and Diagnostics: In contemporary ECUs, the capacity to adjust to wear and alterations in operational circumstances affecting diverse vehicle components, such as a potentially obstructed air filter, enables the ECU to sustain peak performance by modifying its control variables. For service technicians, they also offer diagnostic capabilities.
Body Control Modules (BCMs)
The duties of Body Control Modules (BCMs) encompass a spectrum of functions that do not pertain to the drivetrain; rather, they concentrate on managing the passenger compartment and the exterior aspects of the vehicle.
Functionality:
- Lighting Control: Handling interior lighting, headlights, and taillights.
- Climate Control: Managing air conditioning, heating, and ventilation.
- Door and Window Control: Controlling central locking, electric windows, and other access-related characteristics.
- Infotainment Integration: To handle navigation, audio, and connectivity functions, numerous BCMs interact with the infotainment system.
Networking: In the vehicle, BCMs frequently interface with some other modules, needing strong communication ability. For numerous sensors and actuators related to body functions, they usually act as a hub.
Security: In vehicle security, immobilizers, handling alarm systems, and keyless entry, the BCM serves a crucial part.
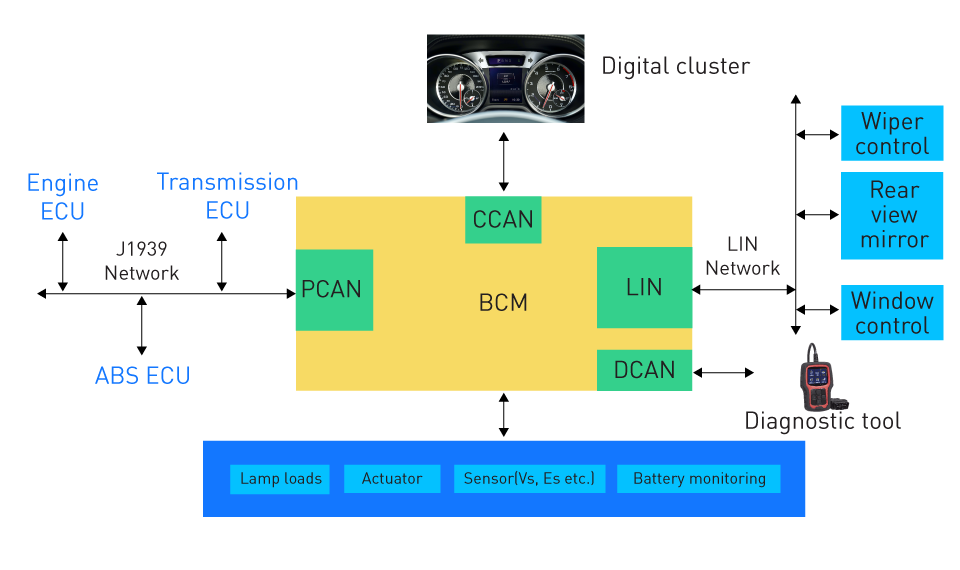
Figure 2: Example of the BCM functions
Conclusively, allowing a range of complicated functionalities that elevate safety, comfort, performance, and convenience, Control Units are focal point to the seamless operation of modern vehicles. Creating a cohesive and responsive automotive system necessitates intricate integration and coordination, exemplified by the diverse array of Control Units like ECUs and BCMs, each serving different types and functions. Automotive engineers and technicians must possess a comprehensive grasp of these units for effective design, development, maintenance, and troubleshooting. As vehicles increasingly integrate software and connectivity solutions, a continual evolution underscores the significance of this understanding.
Power Electronic Components
Power electronic components serve as the foundational support enabling the conversion and regulation of electrical energy within the intricate automotive electronics ecosystem. Converters and inverters are crucial components that play a pivotal role in adjusting and altering electric power to cater to the distinct requirements of various subsystems within a vehicle. In this section, we delve into the critical role of these components and offer an in-depth understanding of their applications and functionalities.
Converters
The power electronics devices that are used to change the voltage level of an electrical source are known as converters. Converters serve a critical role in multiple applications in the context of automotive systems:
DC/DC Converters:
Function: Offering adaptability in interfacing various subsystems that need varying voltage levels, they transform a source of DC voltage from one level to another.
Application in Electric Vehicles (EVs): To step down the voltage from the high-voltage battery to the 12V system, DC/DC converters are employed.
Buck Converters: Buck converters are frequently used in energy-efficient applications and step down the voltage from a higher level to a lower level.
Boost Converters: Boost converters, on the other hand, elevate voltage levels from a lower to a higher tier, playing a critical role in systems such as regenerative braking, which involves capturing and storing energy.
Power Factor Correction (PFCs) Converter:
Function: To adjust the voltage and current waveforms in the on-board charger, PFC converters are utilized, eventually optimizing the power factor. Maximizing electrical power conversion guarantees an efficient transformation into valuable work output.
Application in Electric Vehicles (EVs): PFC converters are pivotal in EV onboard charging systems, significantly minimizing harmonic distortions while elevating the efficacy of the power conversion procedure. These converters, through their near-unity power factor maintenance, facilitate enhanced energy transfer efficiency from the grid to the vehicle, resulting in decreased charging duration and minimized energy wastage.
Design Considerations:
Efficiency: The key to decreasing losses is picking appropriate switching elements and control techniques. Switching losses and conduction losses are the two main sources of losses origin. Increasing the switching frequency has the potential to decrease component sizes within the circuit; however, it concurrently raises the switching losses produced in the converter components. To minimize conduction losses, one can opt for components with lower resistance or parallel components, but at the expense of increased circuit size and cost.
Thermal Management: To manage heat dissipation, adequate cooling systems must be deployed. High-power applications necessitate the utilization of either air cooling, facilitated by a fan, or liquid cooling methods. Both scenarios require the establishment of low thermal resistance between the switching components and the cooling surfaces of the module, achieved through the use of heatsinks and thermal interface materials.
Noise Suppression: To mitigate electromagnetic interference (EMI), proper grounding, filtering and shielding tactics are required.
Isolation: Hazardous voltage isolation rules shall be applied if the voltage transformed is greater than 60V
Inverters
In the realm of electric and hybrid vehicles, the crucial conversion from direct current (DC) to alternating current (AC) is accomplished by inverters.
Function:
DC to AC Conversion: To drive the electric motors in EVs and hybrid electric vehicles (HEVs), inverters take the DC power from the high-voltage battery and transform it to the required AC power.
Variable Frequency Drive: Enabling accurate control of the motor torque and speed, advanced inverters can vary the frequency of the output AC.
Key Applications in Automotive Systems:
Motor Control: Motor control is utilized in electric and hybrid vehicles to operate the main traction motors.
Power Management: Adapting to the different requirements during various driving conditions, power management helps in the distribution of power across multiple subsystems.
Design Challenges:
Efficiency: Needing careful selection of semiconductors and control algorithms, high efficiency is required to increase range in EVs. Traction inverters power E-Machines with a maximum rating of 700kW.
Reliability and Durability: Robust design and rigorous testing are crucial along with the important role of inverters in propulsion.
Integration: A multidisciplinary technique is required due to the complexity of combining inverters into other systems, like thermal management systems and battery management.
The principles guiding the design of DC/DC converters also extend to the realm of inverters.
The integral elements of the automotive power electronic landscape are converters and inverters. Efficiently enabling control over electrical power, they adapt to modern vehicles' diverse and intricate energy needs, ensuring flexibility in management. A deep understanding of how they function, their applications and the essential design considerations is crucial for automotive engineers, especially given the swift progress in electric and hybrid vehicle technology. The sophistication and intricacy of modern automotive electronic systems are underscored by their pivotal role in energy conversion, management, and optimization. This emphasizes the vital need for interdisciplinary expertise and knowledge within this dynamic field.
Communication Modules and Interfaces
To function effectively, today’s vehicles are furnished with a wide range of electronic equipment and systems that must interact with one another. To effectively communicate, it's essential to have resilient, adaptable, and streamlined interfaces and modules due to the intricacy involved. Within automotive engineering, complex interaction is facilitated by four primary communication technologies: the Controller Area Network (CAN) Bus, Local Interconnect Network (LIN), Ethernet, and FlexRay. Within the vehicle’s complete architecture, each has particular roles and features that fit different requirements.
Controller Area Network (CAN) Bus
In the automotive industry, the CAN Bus is a robust and largely used communication protocol. A multi-master serial bus system is in operation, enabling communication between multiple devices without reliance on a central computer. Arbitration decides who speaks first. Each node includes its identifier within its broadcast, and among the nodes broadcasting concurrently, the one possessing the highest identifier number gains priority to speak first.
Functionality:
Message-based Protocol: Messages aren't transmitted between nodes using addresses; instead, every node within the bus has visibility of the message, empowering them to determine whether to discard or process it, thereby facilitating adaptable and efficient data transmission.
Fault Tolerance: The system's design ensures uninterrupted operation, even in the event of specific network components failing, such as an open or short circuit occurring in one of the data lines.
Applications:
Real-Time Control: Real-time control is employed in crucial systems such as braking, power steering, and engine control.
Diagnostics: Onboard diagnostics (OBD) streamlines troubleshooting and maintenance procedures.
Design Considerations:
Data Rate: Data rate usually works at speeds up to 1 Mbps.
Security: To avert unauthorized access and tampering, appropriate security measures can be implemented.
Hardware Layer:
CAN is considered a half-duplex network. Differential lines known as CAN_HIGH and CAN_LOW carry signals. The disparity in voltage between these two lines signifies either a digital 1 or 0. Both ends of the CAN bus require termination using 120 ohms resistance, while the CAN harness should possess a characteristic impedance of 120 ohms to minimize reflections.

Figure 3: CAN topology
Local Interconnect Network (LIN)
Compared to CAN, LIN is a more cost-effective communication protocol and is utilized for less time-sensitive communication within the vehicle.
Functionality:
Master-Slave Configuration: Simply network management by including one master and multiple slaves.
Low Data Rate: With data rates up to 20 kbps, it is suitable for non-critical operations.
Applications:
Interior Systems: It is used for mirrors, seat adjustment, window controls, and other comfort features.
Hardware Layer:
LIN is considered a half-duplex network. A single line carries the signal, and the return of the signal is ground. Typically, LIN signals operate at battery voltage, although the standard permits them to utilize a dedicated discrete bus voltage exclusively allocated for LIN. A resistor pulls up each node to the bus voltage, with a stronger pull-up resistor specifically populated at the Master node.
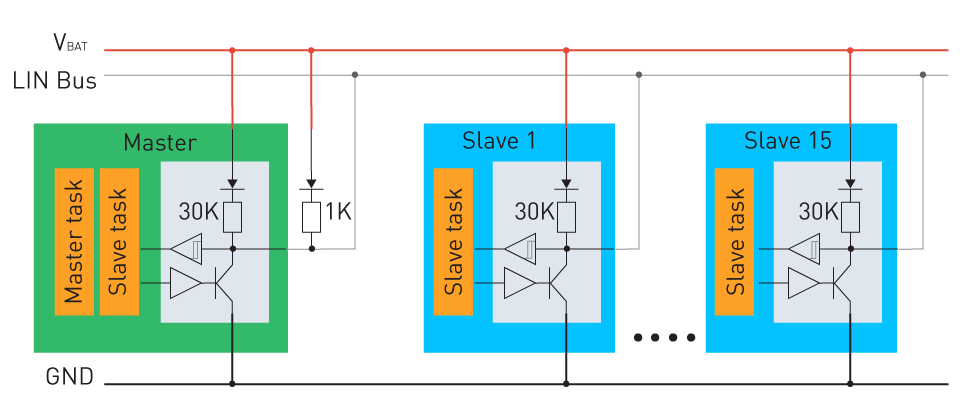
Figure 4: LIN topology
Ethernet
Especially in advanced driver assistance systems (ADAS) and infotainment systems, ethernet in automotive applications is becoming increasingly popular.
Functionality:
High Data Rate: Enabling the transmission of substantial data volumes, it sustains speeds of at least 1 Gbps or higher.
Standardized Protocol: Enables compatibility across a spectrum of devices and systems.
Applications:
Infotainment Systems: Infotainment systems are utilized for complicated user interfaces, video streaming, and navigation.
ADAS: In advanced safety features, ADAS allows high-speed communication needed for real-time processing.
Hardware Layer:
Communication via Ethernet can occur in either half-duplex or full-duplex modes. Galvanically isolated twisted pair cables for TX and RX signals mitigate both common mode and differential mode noise emissions. Only two nodes are present in an ethernet bus. With the assistance of gateways and switches, communication between multiple nodes is solved.
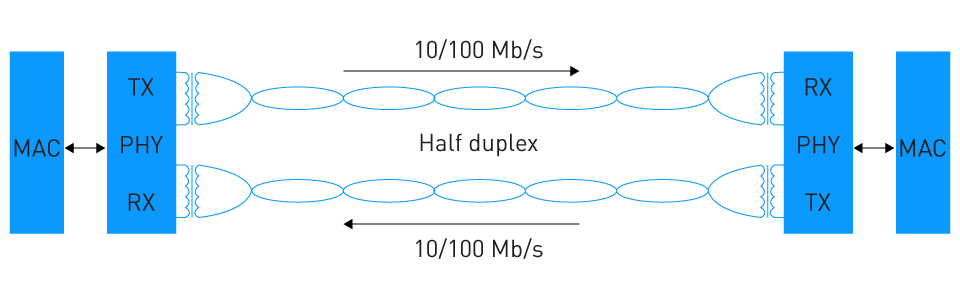
Figure 5: 100 Mbit ethernet connection
Flexray
Offering deterministic data transmission, FlexRay is designed for high-performance automotive applications.
Functionality:
Dual-Channel Architecture: Fault tolerance and redundancy are provided by dual-channel architecture.
Time-Triggered Communication: Synchronous and asynchronous communication are supported by time-triggered communication and enable precise timing control.
Applications:
Drive-by-Wire Systems: It is suitable for critical control applications such as steering, or throttle control.
Hardware Layer:
The bus is like CAN. The same bus can accommodate multiple nodes. Twisted pairs constitute the signals, enabling the utilization of a secondary channel (Channel B) to provide redundancy in case the initial channel is compromised.
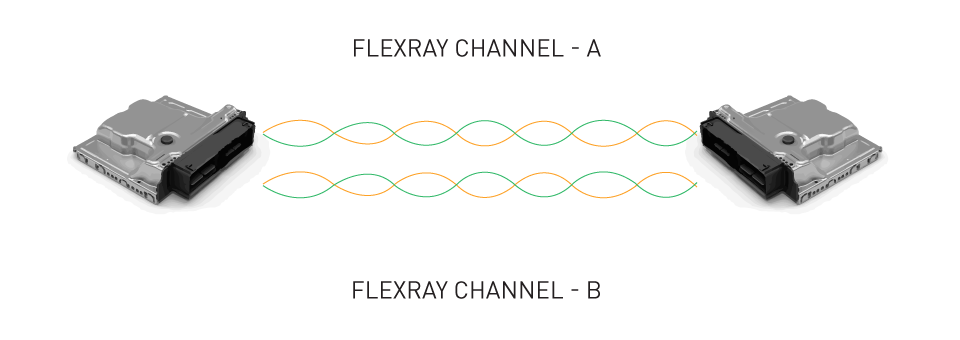
Figure 6: Flexray in dual-channel configuration
Network Topologies
Bus Topology: Bus topology has a single communication line connecting all devices and it is used in CAN networks. Although it is simple and cheap but can become complex if numerous devices are connected.
Star Topology: Star topology includes a single node connected to all other devices and is usually employed with Ethernet and LIN. It can create a single-point failure due to centralization, which simplifies wiring.
Hybrid Topology: Hybrid topology is a combination of multiple topologies. According to their requirements, it enables flexibility and optimization of different network segments. This topology is frequently used by FlexRay.
Ring Topology: Allowing data to flow until it reaches its destination, ring topology connects devices in a circular pattern. It is employed in some FlexRay implementations. Along with offering fault tolerance, it adds complications.
Mesh Topology: Offering different paths for data travel, mesh topology connects devices to several others in the network, and it can be seen in high-redundancy applications. It can be complicated and expensive to implement but enhances reliability.
Various protocols and topologies work in harmony to facilitate the intricate communication network within a vehicle, each fulfilling distinct roles and catering to specific applications. CAN and LIN address conventional control functions, each with their unique cost and performance traits. Meanwhile, FlexRay and Ethernet are instrumental in ushering in the next wave of features for vehicles, demanding increased data rates and advanced setups to support next-generation capabilities.
Gaining comprehension of these networks and their fundamental topologies offers a foundational perspective into how electronic systems are intricately orchestrated within contemporary vehicles. This capability equips engineers with the expertise necessary to craft and resolve intricacies within systems, meeting the demands of today's interconnected automotive realm, which is progressively more autonomous. Choosing the appropriate communication protocol and network topology meticulously is crucial for constructing a vehicle electronics architecture that is optimized, resilient, and prepared for future advancements.
User Interface Components
Advanced User Interface (UI) elements facilitate the interaction between the driver and the vehicle’s numerous systems in modern vehicles. Providing the driver to monitor and control the vehicle’s functions efficiently, these UI components have become crucial in offering a seamless and intuitive driving experience. These user interfaces are constituted by display units and input devices like touchscreens and buttons. We will delve into the roles, types, and applications of these necessary elements in this section.
Display Units
Display units serve as vital elements, furnishing both the driver and passengers with essential visual feedback and information. Playing a crucial role, they interpret data sourced from diverse vehicle systems, entertainment choices, navigation aids, and beyond.
Types and Functions:
Instrument Cluster: Included in this are the speedometer, fuel gauge, tachometer, and additional crucial indicators reflecting the vehicle's status. Digital displays, commonly employed in modern vehicles, facilitate customization and seamless integration with various other systems.
Infotainment Display: Typically, these interfaces are touchscreens granting access to entertainment, climate control, navigation, and connectivity functionalities.
Head-Up Displays (HUDs): Projected onto the windshield, HUDs (Heads-Up Displays) enable drivers to access crucial driving information without diverting their eye from the road ahead.
Design Considerations:
Visibility: Achieving optimal visibility across different lighting scenarios is essential.
Ergonomics: Optimizing driver comfort and safety by appropriately positioning and sizing the displays.
Integration: Creating synergy between the display and additional interior design components while meeting system requirements.
Input Devices (e.g., Buttons, Touchscreens)
Enabling interaction and control over the vehicle's diverse electronic systems for both the driver and passengers, input devices play a crucial role. Traditional mechanical controls and advanced touch-sensitive interfaces are included in this.
Types and Functions:
Buttons and Knobs: Functions that need frequent adjustment, like cruise control, climate controls, phone handling and audio volume often use button and knobs and provide tactile feedback.
Touchscreens: At the center of contemporary infotainment systems lie touchscreens, offering a versatile and intuitive interface for navigation, entertainment, and adjusting settings.
Voice Controls: Voice controls, increasingly prevalent in modern vehicles, facilitate the hands-free operation of diverse functions, thereby improving both safety and convenience.
Design Considerations:
Usability: With attention to the size, shape, and controls of placement, they are designed for ease of use.
Accessibility: Guaranteeing controls are easily accessible and distinguishable by tactile sensation.
Aesthetics: Harmonizing the control design to match the vehicle's overall interior style.
In shaping the advance driving experience, user interface components are crucial. By integrating well-designed display units and a variety of input devices, modern vehicles adopt a user-centered approach that boosts both functionality and aesthetic allure.
For automotive engineers, manufacturers, and designers, understanding the design, functionality, and integration of these elements are crucial. With the ongoing evolution of vehicles incorporating advanced features and increased connectivity options, the significance of user interface components is poised to expand, seamlessly integrating technology into our daily transportation necessities.
直接登录
创建新帐号