Application Requirements
Precision Measurement Application Requirements
It is critical to analyze the technical requirements for the precision measurement application before selecting an ADC.
Signal Frequency Range: The frequency range of interest will differ from one application to the next.
Resolution Requirements: The resolution requirements might range from high to very high depending on the application.
Noise Sensitivity: Accuracy is vital, therefore noise sensitivity and a high signal-to-noise ratio are essential.
Sampling Rate: The needed sample rate varies depending on the application.
Complexity and Cost Constraints: Take into account the precision measuring application's complexity and cost limits.
Calibration Needs: Precision measuring applications need periodic calibration for optimal performance.
ADC Selection
Precision measurement applications need ADCs with high resolution, high precision, and low noise to assure accurate data capture.
Potential ADCs for Precision Measurement
Here are some examples of ADCs used in precision measuring applications:
SAR (Successive Approximation Register) ADC: Because of their good mix of speed and accuracy, SAR ADCs are a preferred choice for precision measurement. They have moderate to high resolutions and can do accurate measurements at acceptable rates. Data collection systems, medical equipment, and scientific instruments frequently employ SAR ADCs.
Delta-Sigma ADC: Delta-sigma ADCs provide a high resolution and low noise performance. They are especially effective in precision measurement applications requiring signal integrity and accuracy, such as audio, vibration analysis, and strain gauge measurements.
Pipelined ADC: Pipelined ADCs provide high-speed conversion while maintaining acceptable resolution and accuracy. They are well suited to applications requiring precise measurements at high data rates, such as communication receivers, high-frequency testing equipment, and radar systems.
Consider resolution, accuracy, noise performance, speed, and the required dynamic range when selecting an ADC for precise measurement applications. External considerations such as power consumption and cost may also play a role in selecting the best ADC for your unique precision measurement demands. To guarantee that the chosen ADC matches the needed performance parameters, always review the datasheets and application notes given by the manufacturer.
Selecting a Delta-Sigma ADC for Precision Measurement Applications
Due to its special features that correspond well with the needs of such systems, a delta-sigma ADC is frequently used for precision measurement applications. The following are some of the reasons why a delta-sigma ADC could be used for precision measurement:
High Resolution: Delta-sigma ADCs may achieve extremely high resolutions, often ranging from 16 to 24 bits or more. Because of their high resolution, they can reliably catch and quantify minor changes in the input signal, making them excellent for detecting minute fluctuations in physical quantities in precision measurement applications.
Low Noise: Oversampling and noise-shaping methods are used in delta-sigma ADCs to shift quantization noise towards higher frequency areas. As a result, low-frequency noise is significantly decreased, resulting in excellent signal-to-noise ratio (SNR) performance. This low noise property is critical in precision measurement applications to provide accurate and dependable data capture, especially when dealing with low-level signals.
High Linearity: Due to the nature of the delta-sigma modulation process, delta-sigma ADCs have great linearity. Because of its linearity, the input signal is accurately represented, enabling accurate measurements with little distortion.
Signal Integrity: As a result of their ability to shape noise, delta-sigma ADCs are particularly well-suited for situations where signal integrity is crucial since quantization noise is less of an issue. Maintaining signal integrity is crucial for getting accurate findings in precision measurement.
Simplicity of Post-Processing: The final digital output from a delta-sigma ADC is produced as a high-frequency bitstream that has to be filtered and decimated. Due to the noise shaping's ability to move quantization noise to higher frequencies where it may be removed more easily during post-processing, this procedure may be rather straightforward.
Integration with Sensors: It is simple to combine delta-sigma ADCs with a variety of sensors, such as resistive bridge sensors, thermocouples, and strain gauges. The design of precision measurement systems is made simpler by this integration, which also enables direct sensor interfacing without the use of extra signal conditioning equipment.
Low Power Consumption: The usual power consumption of delta-sigma ADCs is minimal, making them appropriate for battery-operated or low-power precision measuring applications.
Delta-sigma ADCs are frequently used in precision measurement applications such as industrial instrumentation, scientific research, temperature sensing, strain measurement, pressure sensing, and many other fields where accuracy and dependability are crucial. This is because of their high resolution, low noise, and excellent signal integrity characteristics. To make sure a delta-sigma ADC is the optimum choice for the specific precision measurement task at hand, it's crucial to thoroughly analyze the needs of the application and the trade-offs involved, such as sampling rate and latency.
Introduction to Delta-Sigma ADC
Recap of Delta-Sigma ADC Architecture
High-resolution applications frequently use Sigma-Delta ADCs, commonly referred to as Delta-Sigma (ΔΣ) ADCs. A Delta-Sigma ADC has a fundamentally different design than conventional ADCs. It comprises a digital filter coming after a delta-sigma modulator. The input signal is oversampled at a very high rate, which is how the Delta-Sigma modulator operates. In order to shift the quantization noise to higher frequencies, it uses a technique called noise shaping. The next digital filter successfully eliminates the high-frequency noise by averaging the modulated samples. With very straightforward analog circuitry, very high resolution may be achieved with Delta-Sigma ADCs by the use of oversampling and noise shaping.
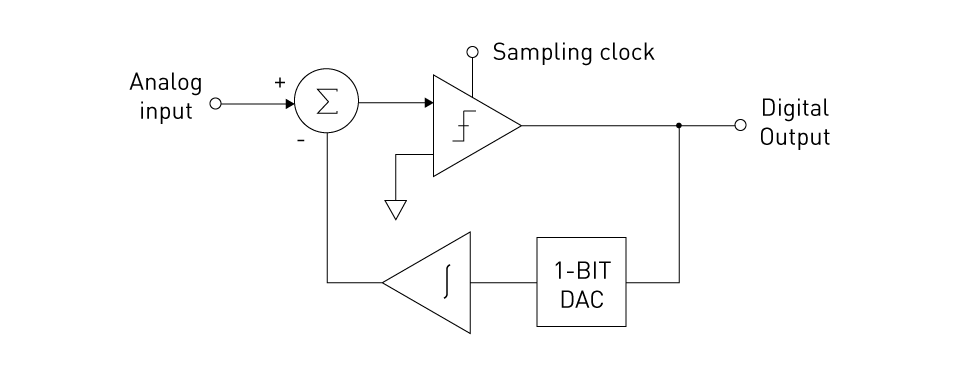
Figure 2: Delta modulator
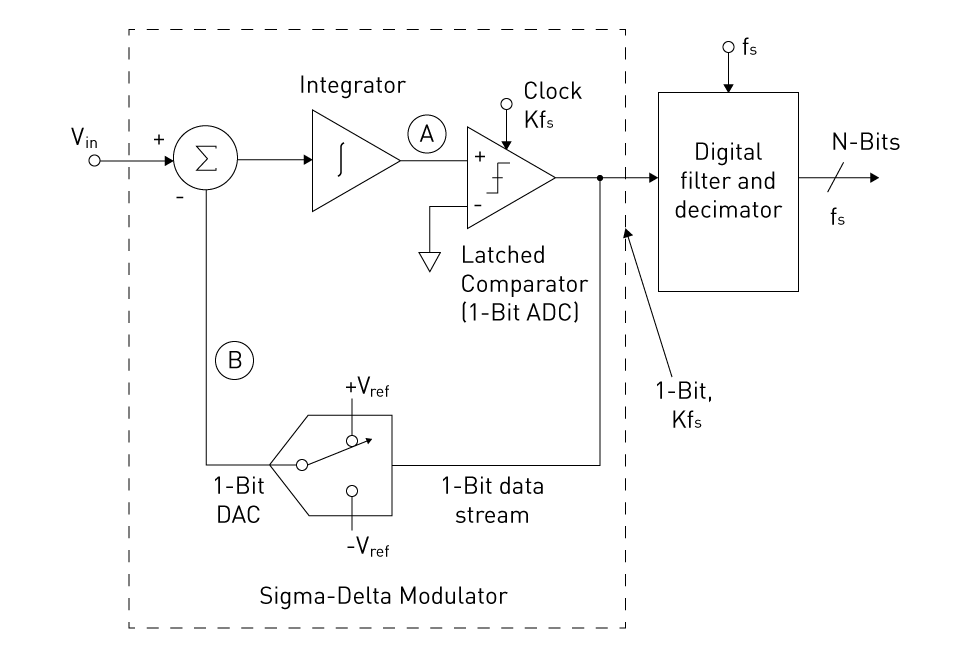
Figure 3: First-order Sigma-Delta ADC
Importance of High-Resolution in Precision Measurements
In applications involving precise measurement, high resolution is essential. High-resolution ADCs are required when the signal of interest is faint (near the noise floor) or when subtle variations in signal levels need to be recognized. Precision measurements benefit from the increased resolution that delta-sigma ADCs can give compared to other ADC types thanks to their inherent noise-shaping and oversampling capabilities. High-resolution is particularly important in the following situations:
Sensor Data Acquisition: A high-resolution ADC makes sure that even the smallest changes are reliably recorded when monitoring physical factors like temperature, pressure, or strain.
Audio Processing: An ADC with high resolution is necessary for high-fidelity audio in order to capture the whole dynamic range of sound.
Medical Instruments: High-resolution ADCs are essential in medical equipment like ECG or EEG machines because the physiological signals' amplitudes might be quite tiny.
Scientific Instruments: ADCs with high resolution are necessary for instruments like spectrometers and chromatographs used in scientific research to precisely assess the characteristics of diverse materials.
Industrial Control Systems: For maintaining control over operations and assuring quality and safety in industrial automation and control systems, precise measurements are essential.
Design And Integration Process
Specifications
Establishing the ADC's specs is the first stage in the design and integration process. The resolution (number of bits), maximum sampling rate, dynamic range, signal-to-noise ratio (SNR), and total harmonic distortion (THD) are among the important characteristics. The ADC's resolution needs to be good enough to record even the slightest alterations in the signals that are important to the application. The Nyquist-Shannon sampling theorem further states that the maximum sampling rate should be adequate to correctly sample the signals of interest.
Circuit Design Considerations
After requirements are defined, circuit design comes into focus. Several factors need to be taken into account while discussing Delta-Sigma ADCs:
Analog Input Stage: To reduce noise and distortion, considerable planning must go into the analog input step. It is advised to utilize excellent operational amplifiers and passive parts.
Digital Filtering: Digital filtering is used by delta-sigma ADCs to attain high resolution. The latency and frequency response of the ADC are impacted by the filter choice, therefore choosing the right filter is essential (for example, a Sinc filter).
Oversampling Rate: In order to obtain the appropriate noise shape while taking into consideration processing constraints, the oversampling rate must be chosen carefully.
Power Consumption: Particularly with battery-powered systems, care must be made to optimize power usage.
Calibration And Error Compensation
Accuracy is crucial in applications involving precision measurement. Error-reducing calibration procedures are used. Offset, gain, and linearity flaws should all be taken into account with Delta-Sigma ADCs. By monitoring well-known reference signals and changing the ADC's output in accordance, error compensation may be accomplished. Additional error reduction can be achieved by digital post-processing.
Integration into Measurement System
It takes careful planning to integrate the Delta-Sigma ADC into the measuring system:
Interfacing: Other system elements including microprocessors, FPGAs, and memory must connect with the ADC. For quick and reliable data transfer, the interface (SPI, I2C, etc.) must be chosen carefully.
Synchronization: It may be important to synchronize various ADCs in multi-channel systems.
Firmware and Software Development: The creation of software and firmware is a crucial step in the integration process. Control of the ADC, data processing, and interaction with other system elements are all included in this.
Testing and Validation: The entire system must be tested after integration to confirm that it complies with the required requirements. This involves evaluating the ADC's performance within the context of the entire system and confirming that it satisfies the needs of the application under actual operating circumstances.
Results And Analysis
Data Acquisition and Analysis
Data collection and analysis start as soon as the Delta-Sigma ADC is successfully integrated into the measurement system. Data can be collected constantly or in bursts, depending on the application. The integrity of the obtained data must be confirmed, especially in high-resolution applications where even the smallest changes might have a big influence on results. Advanced analytical algorithms may also be used to analyze the data and extract the necessary characteristics or information.
Evaluation of Precision and Accuracy
It is crucial to assess the measuring system's precision and accuracy. While accuracy refers to how closely the measurements match the real values, precision deals with the consistency of the readings. The system might be assessed using strategies including error histograms, frequency domain analysis, and statistical approaches.
Particular consideration must be paid to noise floor, dynamic range, and linearity for high-resolution Delta-Sigma ADCs. Any anomalies must be investigated to see whether the ADC, analog input stage, digital filtering, or other system components are to blame.
Recommendations for Further Development
On the basis of the assessment and comparison, suggestions for future improvement might be made. These suggestions might consist of:
Hardware Enhancements: For instance, enhancing the power supply design or adopting ADCs with superior intrinsic performance.
Filtering and Calibration Improvements: This might entail improving calibration processes or using more sophisticated digital filtering algorithms.
Algorithm Optimization: Using complex algorithms to analyze data and rectify errors.
System Level Optimizations: Including improved heat control, physical layout improvements, and improved component integration.
Exploring Alternative Technologies: If the Delta-Sigma architecture has any intrinsic constraints, it would be worthwhile to look into alternative ADC technologies or hybrid strategies.
直接登录
创建新帐号