Introduction to ADCs in Industrial Control
Overview and Importance
Industrial control systems rely heavily on analog-to-digital converters (ADCs). The monitoring, control, and optimization of industrial processes, which frequently include a wide range of physical variables including temperature, pressure, flow rates, and humidity are common tasks for these systems. These physical parameters are analog by nature. These analog impulses are converted into digital data using ADCs, which enables contemporary microcontrollers and digital signal processors to run complex control algorithms.
It is impossible to overestimate the significance of ADCs in industrial control systems, they include:
Real-time Monitoring: ADCs enable the immediate observation of process parameters, guaranteeing the stability and effectiveness of the process.
Control: Through feedback control mechanisms, ADCs utilize digital data to make determinations and regulate devices such as motors, valves, and heaters.
Safety and Reliability: Monitoring systems relying on ADCs can identify irregular conditions and activate alerts or safety measures, thus averting accidents and assuring the dependability of industrial processes.
Data Logging and Analysis: By transforming physical measurements into digital data, ADCs streamline the process of recording data and analyzing trends, which are crucial for predictive maintenance and process enhancement.
Typical Requirements for ADCs in Industrial Control Systems
When choosing an ADC for industrial applications, it's important to carefully evaluate the following factors:
Resolution: This dictates the smallest discernible change in the analog input that can be translated into the digital output. High-resolution ADCs are imperative in applications demanding meticulous control, such as managing chemical compositions within a process.
Sampling Rate: The speed at which the ADC samples the analog signal holds paramount importance in time-sensitive scenarios. A higher sampling rate becomes indispensable for capturing swift variations in process variables.
Accuracy and Linearity: Accuracy denotes the proximity of the ADC's output to the true analog value, while linearity guarantees that the ADC's output maintains a proportional relationship with the input across its entire range. Both play a pivotal role in ensuring the reliability of the control system.
Isolation: In industrial settings, electrical noise and elevated voltages are prevalent. ADCs featuring isolation capabilities are frequently mandatory to avert interference and safeguard control circuits.
Robustness: ADCs integrated into industrial control systems must exhibit robustness capable of consistently operating in challenging environments, including those characterized by high temperatures, vibrations, or corrosive conditions.
Power Consumption: In specific applications, especially where power resources are limited or heat dissipation is a concern, minimizing power consumption assumes significance when selecting an ADC.
ADCs in Process Control
Role in Monitoring and Control
Process control stands as an engineering discipline specialized in the oversight and enhancement of operations within manufacturing and diverse industrial contexts. Within these arenas, a multitude of physical parameters encompassing temperature, pressure, flow rates, and chemical compositions necessitate continuous monitoring and optimization. ADCs play a pivotal role in this landscape by transforming analog signals that represent these physical variables into a digital format. This transformation empowers digital control systems to effectively process and manage this crucial data.
In the monitoring phase, data acquisition takes place through sensors and transducers. Subsequently, this data is relayed to a control algorithm, which, based on the current state of the process, formulates decisions. These decisions, in the form of control instructions, are then dispatched to various actuators such as valves, motors, and heaters to meticulously regulate the ongoing process. ADCs constitute an integral link within this operational chain, facilitating the conversion of the analog realm into the digital domain, where contemporary control methodologies find their application.
Specific ADC Requirements
Resolution, speed, and isolation are the three main requirements for process control applications for ADCs:
Resolution: In process control, minor adjustments to a parameter may have a big impact. To detect these minute changes, the ADC needs to have a high resolution.
Speed: Many operations require speedy responses, thus the control system must do the same. To record quick changes in the analog signal, a high sampling rate ADC is needed.
Isolation: Electrical noise and possibly harmful voltages are common in industrial settings. To guarantee that these conditions do not adversely affect the control electronics, ADCs must have the ability to isolate electrical signals.
Case Study: ADC in a Temperature Control System
Let's examine a case study involving temperature control in a chemical reactor. In such reactors, temperature plays a pivotal role in influencing reaction rates. To regulate temperature effectively, these reactors are typically equipped with a heating system and a cooling mechanism to keep temperatures within a specified range.
In this scenario, temperature measurement relies on a thermocouple, which generates an analog signal. To process this signal, it must undergo conversion into a digital format, a task entrusted to an Analog-to-Digital Converter (ADC). Given the critical nature of temperature precision in this application, a high-resolution ADC is the preferred choice.
The moment the ADC transforms the temperature data into a digital signal, the next step involves a microcontroller or a Programmable Logic Controller (PLC) executing a control algorithm, often a Proportional-Integral-Derivative (PID) controller. The purpose of this algorithm is to maintain the desired temperature. The control output from the algorithm is then employed to modulate the heating and cooling systems accordingly.
In this system, the ADC emerges as a pivotal component. Its resolution has a direct impact on the control system's capacity to accurately regulate the reactor's temperature. Additionally, the sampling rate of the ADC holds significance; if it's too low, the control system may respond sluggishly, potentially leading to oscillations or instability. Moreover, ensuring electrical isolation is vital to shield the ADC's measurements from any electrical noise originating from the reactor's heating elements or other equipment.
ADCs in Robotics and Automation
Sensing and Feedback Control
In the realm of robotics and automation systems, Analog-to-Digital Converters (ADCs) play a pivotal role in facilitating precise control and interaction with the physical environment. Robots are typically equipped with an assortment of sensors designed to monitor crucial parameters like position, velocity, force, and torque. These sensors, as a rule, generate analog signals that necessitate conversion into digital format for subsequent processing by microcontrollers or digital signal processors.
At the heart of robotics lies the concept of feedback control. In a feedback control system, a robot takes actions based on the data it gathers from sensors in order to adhere to a predefined trajectory or maintain a specific state. For instance, consider a robotic arm: sensors continuously gauge the arm's position and orientation, and this vital information is harnessed to regulate motors responsible for adjusting the arm's position. ADCs are instrumental in closing this feedback loop, as they transform the analog sensor outputs into digital data, thereby enabling the application of real-time control algorithms.
Precision and Speed Requirements
Precision: In robotics, precision and accuracy are crucial, particularly in tasks like assembling, machining, or delicate manipulation. To guarantee that the sensor data is recorded with enough detail for precision control, a high-resolution ADC is required.
Speed: Robotic systems frequently need to follow a high-speed trajectory correctly or react fast to changes in their environment. ADCs with high sample rates are therefore necessary to make sure the control system can run at the needed speed.
Case Study: ADC in a Robotic Arm Control System
Let's consider a robotic arm integrated into an automated assembly line for electronic products. The primary function of this robotic arm is to achieve precise and high-speed placement of small components onto a circuit board.
To execute this task effectively, the robotic arm is outfitted with a suite of sensors, including encoders to provide position feedback and force sensors for ensuring delicate component placement. These sensors generate analog signals, which necessitate conversion into digital format with exceptional precision. This is where the Analog-to-Digital Converter (ADC) plays a pivotal role.
The ADC utilized in this context must possess a high resolution, often exceeding 16 bits, depending on the exacting precision requirements of the task at hand. The resolution of the ADC ensures that the robotic arm can discern even the slightest changes in position and force. Furthermore, a high sampling rate, frequently in the tens of kilohertz range is imperative to enable the control system to respond swiftly.
In the operation of this robotic arm, the control algorithm, typically running on a microcontroller or FPGA receives the digital data transmitted by the ADC. Subsequently, it calculates the necessary adjustments required for the motors' power and direction in real-time. This real-time responsiveness empowers the robotic arm to carry out component placement onto the circuit board with exceptional precision and speed.
ADCs in Medical Systems
Role and Importance
Within the domain of medical systems, Analog-to-Digital Converters (ADCs) stand as indispensable components for the acquisition and processing of a diverse range of physiological signals. These signals, frequently manifesting in analog form require conversion into digital format to facilitate analysis, monitoring, and diagnostic procedures. The precision and dependability of this analog-to-digital conversion are paramount, as inaccuracies could lead to erroneous diagnoses or inappropriate medical interventions.
Specific Medical Applications
Imaging Systems (MRI, Ultrasound):
MRI (Magnetic Resonance Imaging): In the realm of MRI systems, ADCs serve a pivotal role by digitizing analog signals originating from radiofrequency coils. These signals result from fluctuations in the magnetic field and are crucial for the creation of highly detailed images of bodily tissues. The accuracy of this digitization process is paramount in rendering precise and informative visualizations of internal structures.
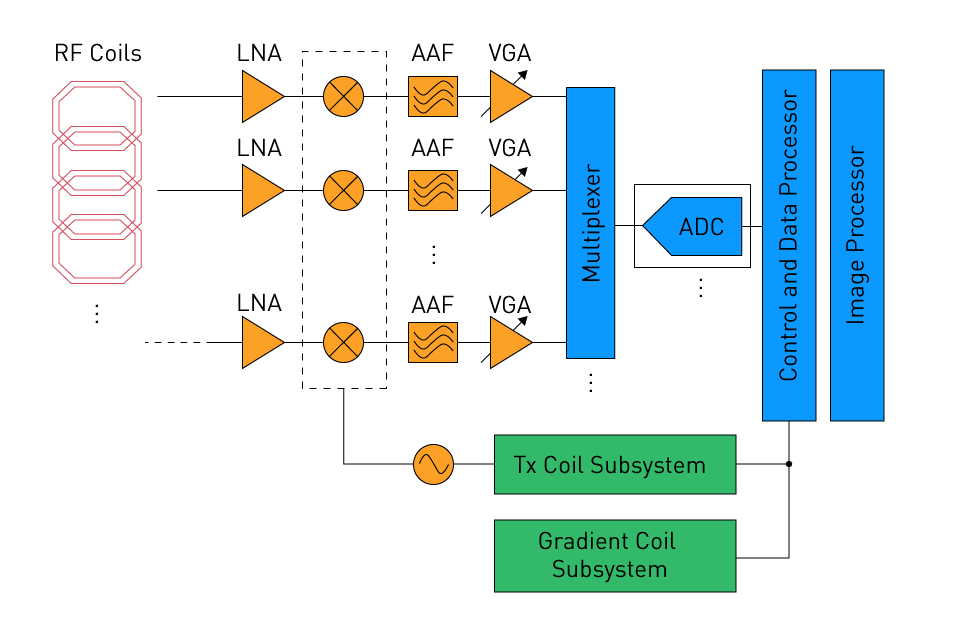
Figure 1: ADC in MRI receiver chain
Ultrasound: High-frequency sound waves are injected into the body during ultrasound imaging, and the echoes are picked up as analog signals. These echoes are transformed into digital signals by ADCs, which are then utilized to produce images of the interior organs.
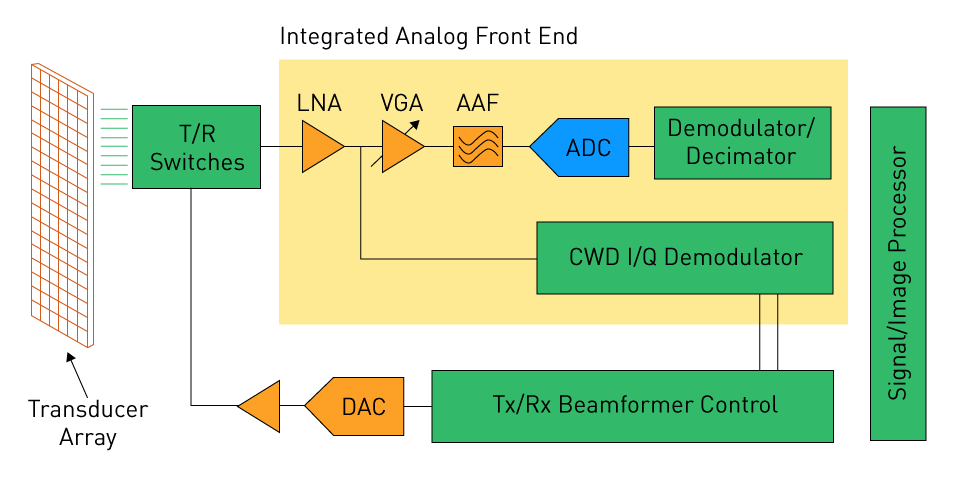
Figure 2: ADC in medical ultrasound front-end signal chain
Patient Monitoring Systems:
ECG (Electrocardiogram): ECG (Electrocardiogram) machines, which track the electrical activity of the heart over time rely heavily on ADCs. The electrodes' analog electrical signals are transformed into digital signals that may be monitored, analyzed, and stored.
Blood Pressure Monitors: Digital blood pressure monitors use ADCs to transform analog sensor pressure readings into digital data that can be displayed and stored.
Medical Research and Lab Equipment:
Gathering diverse physiological signals and data is frequently necessary for medical research. ADCs are used in lab apparatus like oscilloscopes, spectrometers, and data recorders to precisely digitize signals.
Considerations for ADC Selection in Medical Systems
Precision, safety, and noise are the three key factors to be taken into account when choosing an ADC for medical systems.
Precision: Precision stands as a cornerstone in the realm of medical applications. For instance, the demand for high-resolution ADCs becomes evident when capturing intricate details in medical imaging. In patient monitoring, precision holds the key to obtaining accurate readings, thereby ensuring reliable healthcare assessments.
Safety: Paramount in medical contexts is the safety of the patient. ADCs employed in medical applications must conform rigorously to established medical safety standards. Furthermore, they should incorporate isolation features, safeguarding both the patient and the equipment against potential electrical hazards.
Noise: In the world of medical applications, particularly in the context of sensitive measurements like Electrocardiograms (ECGs), maintaining low noise levels is of utmost importance. An ADC with a minimal noise floor is essential to prevent any contamination of the measured signals, thus guaranteeing the fidelity of the medical data.
Data Rate and Latency: In scenarios necessitating real-time monitoring and imaging, the ADC's data rate assumes critical significance. It must have a high data rate and low latency to enable immediate processing and analysis of the signals. This real-time capability is pivotal in providing timely medical insights and facilitating rapid decision-making in healthcare settings.
直接登录
创建新帐号