Oil-Immersed Transformers
In the ecosystem of transformer technologies, oil-immersed transformers are a widely used variation. They are well-known for their efficiency and reliability in high-power applications, which accounts for their widespread utilization. One of the most important aspects of these transformers' operation is the cooling mechanism that they use, which has a direct impact on their operational efficiency, longevity, and safety. In the next part, we will go into the intricacies of oil-immersed transformers, including the cooling processes that they utilize and the benefits that they provide.
Principle of Oil-Immersed Transformer Cooling
Insulating oil serves as both a coolant and an electrical insulator in oil-immersed electric transformers. The transformer circulates this oil within its casing, absorbing heat from the core and windings during operation. After that, the heated oil rises and flows towards the cooler regions of the transformer, releasing its heat into the surrounding environment. This technique utilizes the laws of convection for heat transfer, and the natural circulation of oil effectively cools the interior components of the transformer.
Types of Oil-Immersed Transformer Cooling Systems
Oil Natural Air Natural (ONAN): The transmission of heat takes place in naturally cooled oil-immersed transformers (Oil Natural Air Natural) through the processes of natural convection and radiation. The oil absorbs the heat, which then circulates naturally within the transformer, transferring it to the tank walls and ultimately to the surrounding air. It is common practice to employ this technique in transformers of a smaller size, where the amount of heat generated is quite minimal.
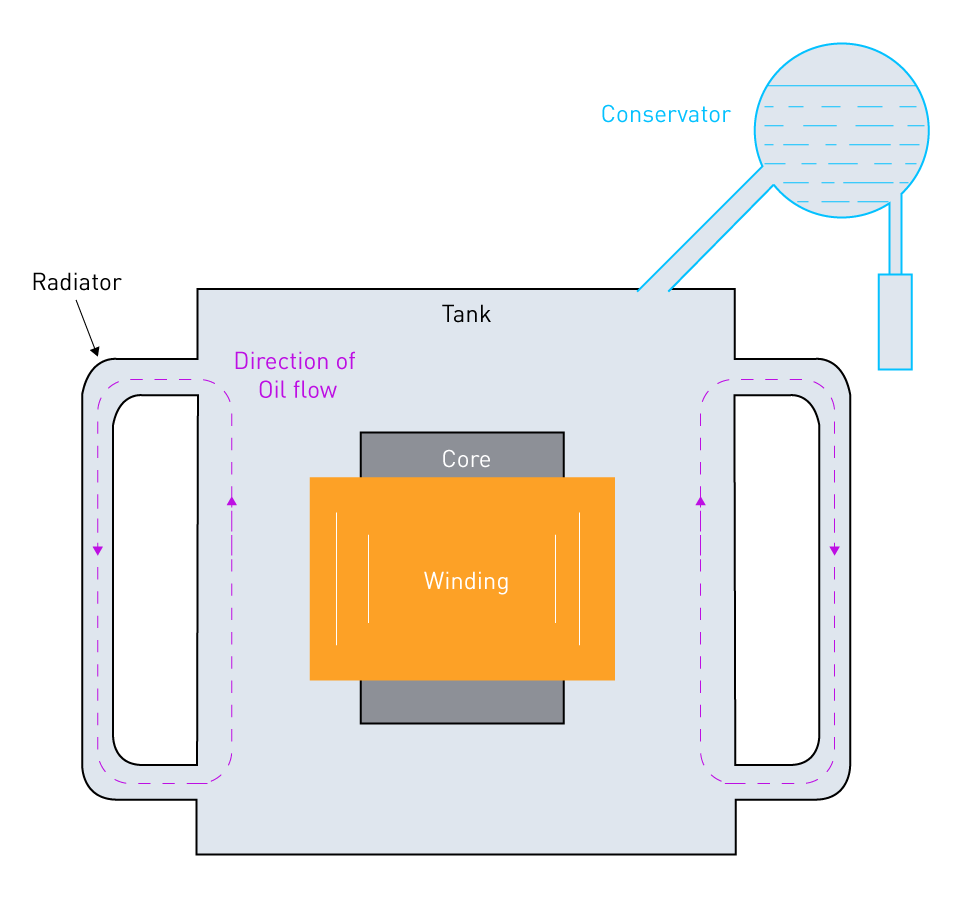
Figure 14: Oil Natural Air Natural (ONAN) transformer cooling
Oil Natural Air Forced (ONAF): Forced air cooling systems are utilized for larger transformers when the heat generated is too much for natural cooling techniques to keep the transformer at a safe temperature. This type of cooling system is referred to as oil natural air forced (ONAF). Fans are used to supplement the air cooling that occurs during the transformer's operation, which is powered by natural oil circulation. The ONAF system triggers the fans when the transformer's load increases and the generated heat exceeds the natural air circulation's cooling capacity. It is possible for the ONAF system to offer effective cooling, which guarantees that the transformer will function within the acceptable temperature range.
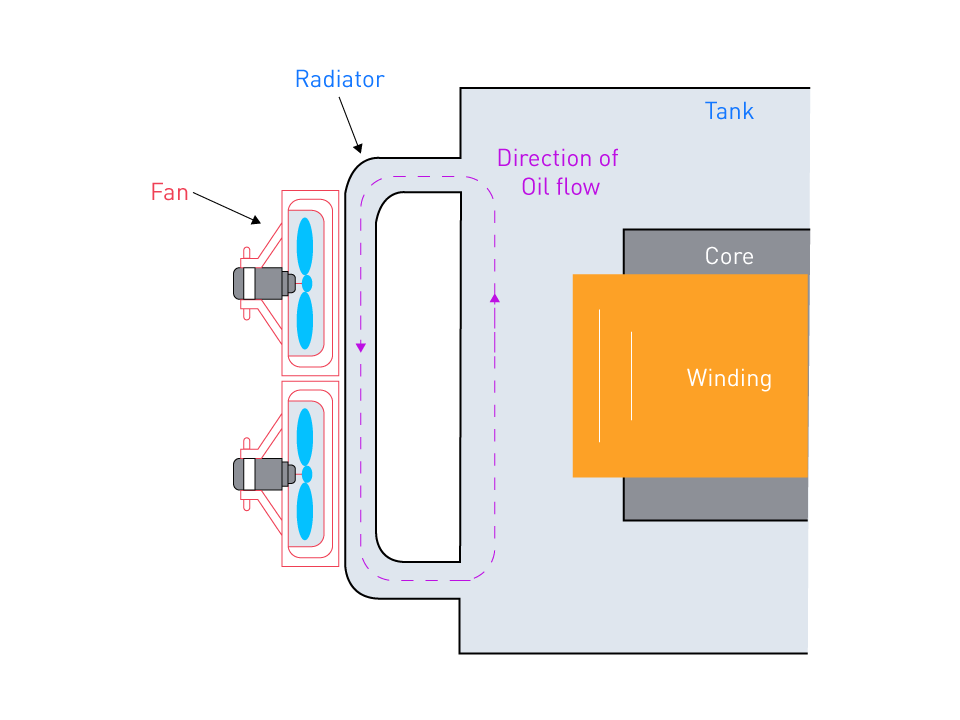
Figure 15: Oil Natural Air Forced (ONAF) transformer cooling
Oil Forced Air Forced (OFAF): The term "Oil Forced Air Forced" (OFAF) refers to the use of oil pumps to actively circulate the insulating oil within the transformer. Natural oil circulation involves pumping the oil through the transformer and the cooling radiators or heat exchangers. This is in contrast to the natural oil circulation, which is dependent on the temperature gradient. A more uniform temperature distribution and a more effective transmission of heat from the transformer core and windings to the oil are both achieved through the utilization of this forced circulation device. Fans blow air over the radiators or cooling fins to improve the rate of heat transfer from the oil to the surrounding environment. When compared to the use of natural air convection, the use of forced air cooling results in a significant improvement in heat removal rate. The transformer is able to manage higher loads and work under more demanding conditions without overheating thanks to this approach, which provides a cooling solution that is very efficient.
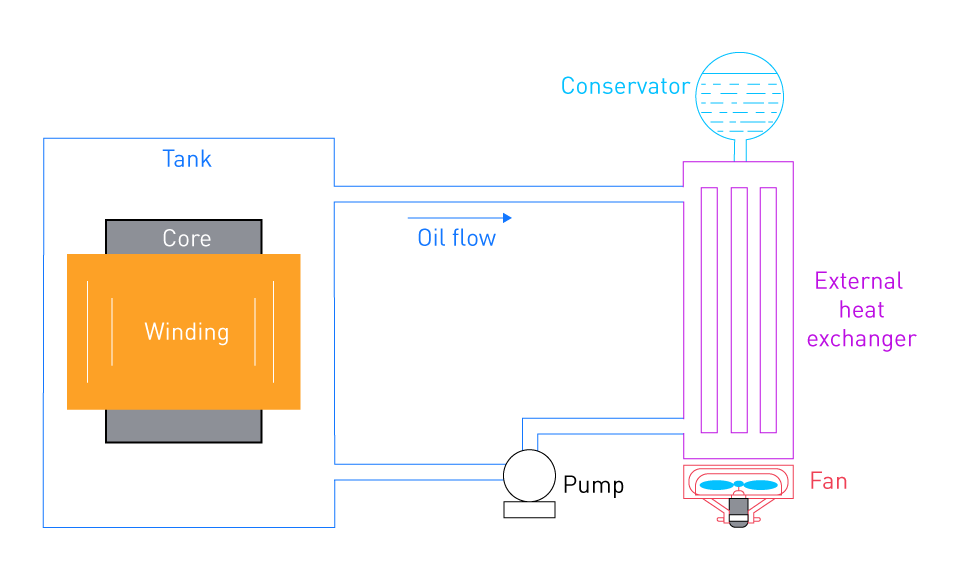
Figure 16: Oil Forced Air Forced (OFAF) transformer cooling
Oil Forced Water Forced (OFWF): In exceptionally high-power applications, oil-immersed transformers may use a mix of forced oil circulation and water-cooled heat exchangers. This type of transformer is referred to as oil-forced water-forced (OFWF). In order to properly remove heat from the system, the oil is circulated between the transformer and a radiator. Additionally, the oil absorbs heat through water channels. This strategy is not only highly effective but also more complex, often reserved for specific situations with high demand.
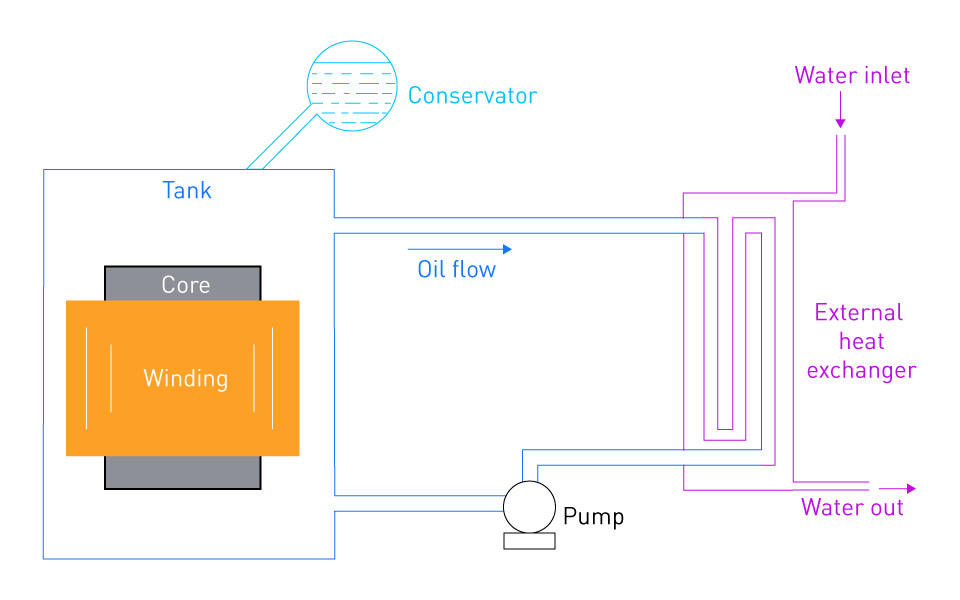
Figure 17: Oil Forced Water Forced (OFWF) transformer cooling
Advantages of Oil-Immersed Transformers
High Efficiency: Oil-immersed transformers are able to function efficiently even when subjected to high load circumstances because of the effective heat transfer qualities of insulating oil.
Reliability: In addition to its cooling properties, the oil also serves as a powerful electrical insulator, which contributes to the transformer's overall reliability and durability.
Cost-Effective: When it comes to medium to high power ratings, oil-immersed transformers provide a solution that is both cost-effective and balanced in terms of performance and initial investment.
Repairability: Oil-immersed transformers are typically easier to repair and maintain than other types of transformers, which allows them to have a longer service life.
Dry-Type Transformers
Dry-type transformers, a significant subset of transformer technologies, distinguish themselves by the absence of liquid cooling media, making them an essential component of the overall spectrum of transformer technologies. Dry-type transformers, in contrast to their oil-immersed counterparts, rely on air or gas to provide insulation and disperse heat. As a result, dry-type transformers are a favored choice in some applications for reasons related to safety, the environment, and operating efficiency. We will discuss the various cooling methods used in dry-type transformers in this section, along with the benefits of these systems and their typical applications.
Cooling Principles in Dry-Type Transformers
Dry-type transformers have a primary cooling mechanism that involves the circulation of air or gas around the windings and core in order to remove excess heat that is created during operation. This can be accomplished by the use of forced air systems or natural air cooling, depending on the size of the transformer, its design, and the amount of thermal load it faces.
Natural Air Cooling (AN): In smaller dry-type transformers, natural air cooling (AN) occurs when ambient air naturally circulates around and through the unit. This occurs because the heat generated by the transformer itself causes the device to be naturally cooled. When the air gets warmer, it rises and moves away from the transformer, which causes it to take in cooler air from the surrounding environment. There is no need for additional energy to be used for cooling fans or pumps because this method is straightforward, dependable, and simple.
Forced Air Cooling (AF): It is possible that natural air cooling will not be enough to maintain acceptable temperature levels for larger transformers or those working under high-load conditions. This is why forced air cooling (AF) is implemented. In situations like these, forced air conditioning systems are utilized. Fans or blowers in these systems enhance air circulation. This method greatly improves the transformer's capacity to dissipate heat, enabling it to manage higher power densities and function more effectively in demanding conditions.
Advantages of Dry-Type Transformers
Safety and Environmental Benefits: Dry-type transformers are safer in enclosed places and environmentally sensitive areas because they eliminate the possibility of oil leakage. In addition to reducing the fire hazard, the lack of combustible liquid improves safety in commercial and industrial environments.
Maintenance and Lifetime: Dry-type transformers often require less maintenance than oil-immersed devices because they do not require continuous monitoring and replacement of cooling fluids. This results in a longer lifespan for the transformer. Additionally, dry-type transformers' solid insulation materials are less likely to deteriorate over time, potentially extending the unit's service life.
Installation Flexibility: The flexibility of installation allows dry-type transformers to be positioned closer to the load, reducing the need for extensive cable runs and the associated losses. It is also possible to put them in a larger variety of locations, including indoors or in areas with restricted airflow, due to their sturdy design and the absence of liquid cooling.
Applications of Dry-Type Transformers
Transformers of the dry type are particularly well-suited for applications in which safety, environmental concerns, or space limits are of the utmost importance. The following are examples of common use cases:
Urban and Commercial Buildings: Dry-type transformers are suitable for use in urban and commercial structures because of their low maintenance requirements and fire safety. These transformers are ideal for use in residential complexes, shopping centers, and office buildings.
Industrial Facilities: Dry-type transformers provide a dependable power solution in industrial facilities, eliminating the environmental and safety issues associated with oil cooling. This is especially useful in industries where there is a concern about fire danger or chemical exposure.
Renewable Energy Projects: Wind farms and solar installations frequently use dry-type transformers in their renewable energy projects. This is because these types of installations place a high value on environmental protection and ease of maintenance.
Factors Affecting Choice of Cooling Method
A number of different considerations determine the cooling mechanism for transformers. Each element significantly impacts the transformer's performance, efficiency, and suitability for a particular application. The following are the most crucial aspects to consider:
Load Capacity: More effective cooling techniques are usually needed to manage the increased heat produced at higher load capacities. For instance, oil forced air forced (OFAF) or oil forced water forced (OFWF) cooling is frequently used in big power transformers.
Transformer Size and Rating: In order to ensure that they run within acceptable temperature limits, larger transformers with higher ratings require cooling methods that are more effective. On the other hand, simpler cooling systems, such as Oil Natural Air Natural (ONAN), may be utilized by smaller transformers.
Ambient Temperature: An important factor is the ambient temperature, which refers to the climatic conditions that exist at the location where the transformer is located. To guarantee that heat is dissipated in an appropriate manner, more strong cooling technologies are required in areas that are hotter.
Installation Environment: Environment of Installation Transformers that are installed inside or in tight places may require different cooling methods than those that are installed outside to ensure proper operation. The limited natural airflow that occurs inside of transformers makes it possible for them to rely more on forced cooling solutions.
Maintenance Requirements: Certain cooling methods are easier to maintain than others, and this is one of the maintenance requirements. When compared to forced cooling technologies, which may entail pumps and fans, natural cooling solutions, such as ONAN, often require less maintenance.
Efficiency and Reliability: More sophisticated cooling systems, such as OFAF or OFWF, have the potential to deliver improved cooling effectiveness and reliability, which is essential for applications that are significant in the field of power distribution and transmission.
Cost: The cost of various cooling systems can vary greatly, both in terms of their initial cost and their ongoing operational cost. Forced cooling systems are typically more expensive to install and operate than other types of cooling systems because they require additional equipment (such as pumps and fans) and consume more energy.
Noise Levels: Because of the operation of fans and pumps, forced air cooling systems, such as ONAF and OFAF, produce a higher level of noise than other types of cooling machines. In locations that are sensitive to noise, it may be preferable to use cooling technologies that are quieter.
Cooling Medium: The cooling medium for some transformers is air, whereas for others it is oil or even water. Some transformers use neither of these. Efficiency, maintenance, and the influence on the environment are some of the considerations that should guide the selection of a cooling medium. However, in order to maintain its high level of efficiency, water cooling (OFWF) necessitates additional infrastructure and maintenance.
Redundancy and Safety: When it comes to essential applications, having a redundant cooling system might be crucial in order to guarantee that the system will continue to function without interruption. The use of forced cooling systems typically results in improved control and dependability, both of which are necessary for transformers located in critical components of the power grid.
Regulatory and Environmental Considerations: Environmental restrictions, particularly those related to the use of specific coolants and heat disposal, may influence the choice of cooling technology.
直接登录
创建新帐号