Load Requirements and Criticality Assessment
An extensive evaluation of the load requirements and the criticality of different systems is essential when constructing standby power systems. This procedure has a direct bearing on the facility's operational integrity and safety since it establishes the capacity and complexity of the standby power solution required to guarantee dependable backup during power outages.
Load Requirements Assessment
Classifying and identifying the electrical loads that will be supported in the event of an outage is the first stage in developing an efficient standby power system. This includes:
Cataloging Equipment: Enumerate all devices and systems that will need electricity in the event of a power loss. This covers everything, including servers, medical gear, lights, HVAC, and production machinery.
Quantifying Power Needs: Find out how much power each piece of equipment uses, usually expressed in watts or kilowatts. Typically, measurements of the actual power consumption or device specs can provide this information.
Prioritizing Loads: Not every system is equally important. It's critical to rank them in order of significance for operational continuity, money growth, or safety.
Criticality Assessment
The standby power system's overall architecture may be impacted by knowing which systems are essential. The criticality evaluation categorizes systems based on the potential impact of their failure during a power outage.
Life-Safety Systems: The systems that are most important are life-safety systems, which include smoke evacuation systems, emergency lights, fire alarms, and other systems that are necessary to keep people safe in an emergency.
Mission-Critical Systems: Mission-critical systems for enterprises could be things like telecommunications, IT infrastructure, and machinery needed to keep things running in sectors like manufacturing, financial services, and healthcare.
Convenience Systems: During a blackout, you might temporarily turn off less crucial but more comfortable systems like heating and general lighting without significantly affecting basic operations or safety.
Factors Influencing Criticality
Regulatory Compliance: Some systems, particularly in the healthcare and aviation sectors, require constant power to meet legal or regulatory requirements.
Financial Impact: Systems are frequently considered crucial if their failure could result in a significant financial loss.
Operational Downtime: The criticality assessment gives priority to systems that could seriously impair operations or service delivery.
Sizing and Capacity Planning
When designing standby power systems, sizing and capacity planning are essential steps that guarantee the system can sustain all required operations in the event of a power outage. This stage entails determining the overall power requirements and the system's size to effectively and consistently meet these demands.
Sizing the Standby Power System
A standby power system's lifespan and effectiveness depend on its proper size. While an enormous system can result in needless capital and operating costs, an undersized system might not be able to handle all key demands during an outage. The procedure entails
Summing Up Power Requirements: Compile the overall power requirements from the load assessment step, taking into account each equipment's peak starting power consumption as well as its continuous running power requirements.
Factor in Load Diversity: Not every piece of equipment will operate at maximum efficiency all at once. Load variety factors compensate for this, thereby reducing the overall capacity required.
Consider Future Expansion: Plan future load levels to ensure that the system can handle expansion without requiring significant changes.
Capacity Planning
In addition to fulfilling present power demands, capacity planning entails developing strategies for future adjustments and scaling requirements.
Scalability: To facilitate easy extension, the system should be constructed with modular components whenever practical. This is especially crucial for businesses that are expanding quickly or for establishments that might undergo major technology improvements.
Redundancy Needs: Having redundant parts, such as several smaller generators or batteries rather than one big unit, can improve reliability for important applications. Redundancy guarantees that even in the event that one component fails, the standby system may continue to run.
Fuel Storage and Availability: Having enough fuel on hand is crucial for generator systems, especially in places where long-term blackouts could disrupt the fuel supply. The type of fuel used and its storage have an impact on operating expenses, as well as the viability of continuing long-term operations during a prolonged grid outage.
Load Management Strategies
Load management techniques can be used to maximize standby power systems' efficiency and capacity.
Critical Load Subpanels: Independent electrical subpanels for critical loads can simplify the system and ensure that only essential services continue to operate during an outage, thereby reducing the required capacity.
Demand Response Controls: Adding demand response features that can cut non-essential loads on their own in the event of a power outage can aid in better power distribution management.
Smart Management Systems: To maximize efficiency and fuel efficiency, sophisticated power management systems are able to dynamically control generator output and power distribution while keeping an eye on current load circumstances.
Redundancy and Scalability
Redundancy and scalability are crucial factors in standby power system design that improve power supply arrangements' reliability and future-proofing. These components are essential for guaranteeing that standby systems can handle unexpected malfunctions and adjust to changing power requirements without necessitating total redesigns.
Redundancy in Standby Power Systems
To make sure there isn't a single point of failure in the standby power system, redundancy entails adding extra or duplicate components. In environments where constant power availability is essential, such as data centers, hospitals, and emergency response facilities, this design approach is critical.
N+1 Redundancy: This is a popular setup in which there is one extra backup device (such as a generator or UPS) available in addition to what is required to manage the anticipated load. This configuration makes sure that service won't stop even if one of the parts fails.
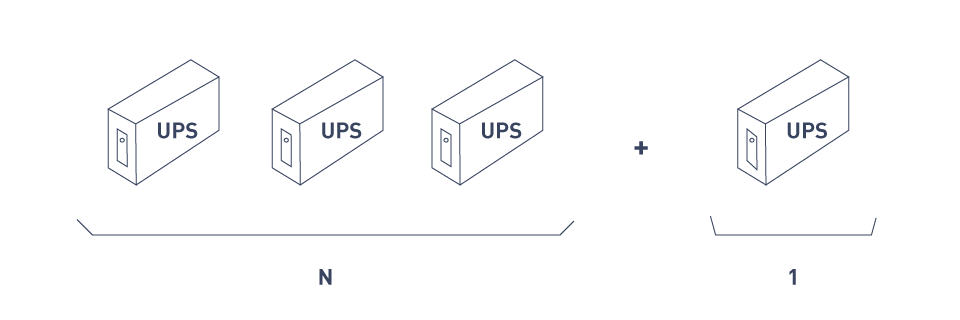
Figure 11: N+1 redundancy
2N Redundancy: More important applications can configure systems with total duplication of the power infrastructure. There are two completely functional systems in a 2N configuration, each of which is able to independently manage 100% of the needed load.
Redundant Configurations: In addition to N+1 or 2N, redundancy can also refer to more sophisticated setups with several backup systems, possibly distributed over various places, offering geographic redundancy and boosting system resilience even more.
Scalability of Standby Power Systems
Scalability is the ability of the standby power system to grow in capability and capacity without requiring major overhauls in order to satisfy the increasing operational demand or evolving technology contexts. This factor is essential for operational dependability and long-term investment efficiency.
Modular Systems: Designing standby power systems with modular components (like modular UPS units) allows for incremental capacity increases. Additional modules can be easily added to the current system as demand increases, requiring no downtime or significant modification. Modular designs also make troubleshooting easier because only defective modules need to be replaced, which lowers the cost and impact of hardware failures.
Flexible Design Architecture: Whenever feasible, flexible architecture should be incorporated into the original design. This could entail installing scalable software and control systems that can manage higher loads, prewiring for more units, or scheduling space for extra batteries or generators.
Integration Capabilities: Another aspect of future scalability is the consideration of integrating new technologies, such as next-generation batteries or renewable energy sources, into the current standby power framework. Early design, which ensures future technology compatibility, can save a lot of money on upgrades later on.
Integration with Existing Infrastructure
An essential component of standby power systems' design and implementation is their integration with current infrastructure. This procedure makes sure that the new systems meet all regulatory criteria, operate seamlessly when switching between primary and standby power sources, and blend in harmoniously with the existing electrical configuration. The standby system's performance and cost effectiveness are maximized through proper integration.
Assessment of Existing Infrastructure
A thorough evaluation of the current electrical systems is the first step toward a successful integration. This evaluation should include the following:
Capacity and Load Analysis: Capacity and load analysis examines the electrical load and its characteristics to ascertain the demands placed on the standby system.
Infrastructure Evaluation: This involves examining the current electrical infrastructure's technical and physical state to find any shortcomings or necessary changes to support the new system.
Compatibility Checks: Compatibility checks involve making sure that the new equipment for standby power is compatible with the electrical components that are already in place, like control systems, distribution panels, and transfer switches.
Design Considerations
The standby system's interaction with the current configuration must be carefully considered for effective integration.
Synchronization: To avoid phase mismatches or other difficulties that could result in poor power quality or equipment damage, standby generators and other power sources must be able to synchronize with the current power grid.
Space and Access: It's important to take into account the physical design of current facilities to make sure there is enough room for the installation of new equipment, such as batteries, UPS systems, and generators, as well as for maintenance access.
Safety and Compliance: Integration needs to adhere to all applicable building codes and safety standards. This includes making sure all cabling and electrical installations are up to code, installing ventilation for generators properly, and having sufficient fire protection equipment.
Implementation Strategies
Phased Integration: By introducing the backup system gradually, current operations can be interrupted as little as possible. With this method, new components can be gradually tested and put into service to make sure they meet operational needs before going fully online.
Use of Advanced Controls: Smart controllers, which are capable of automating power source switching and dynamically managing power loads, are a common feature of modern standby power systems. The integration of sophisticated control systems optimizes the effectiveness and dependability of both the standby and the current systems.
Training and Documentation: It is critical to provide facility managers and technical workers with comprehensive training on the new systems. Proper documentation of the integration process and new system specifications ensures effective performance of ongoing maintenance and troubleshooting.
Testing and Commissioning
Thorough testing and commissioning are required before the standby power system is fully integrated to make sure that every component operates as intended.
Load Testing: Load testing involves simulating a range of operational situations in order to verify how well the standby system performs under various load scenarios.
System Failover Tests: Tests for system failover involve scheduling scheduled outages to simulate the seamless transfer between the primary power source and the backup system, as well as the continued operation of all vital systems.
Regular Maintenance and Updates: After integration, the system requires regular checks and updates to ensure it continues to function correctly and meets the facility's requirements.
直接登录
创建新帐号