Importance of Regular Grounding Inspections
The efficiency, dependability, and safety of electrical systems depend on routine grounding examinations. Protecting people and machinery from electrical dangers is the primary function of grounding systems. It is crucial to conduct frequent inspections of these systems to detect and address any possible problems before they cause failures or accidents, as they might deteriorate over time as a result of environmental causes, physical damage, or corrosion.
Ensuring Safety of Personnel and Equipment
Protection from Electric Shock: A well-maintained grounding system can greatly reduce the danger of electric shock by providing a safe path for fault currents to reach the ground. To keep people safe when operating with or near electrical equipment, it is important to inspect the grounding system on a regular basis.
Equipment Protection: Grounding systems shield electrical devices from transient surges, lightning strikes, and voltage spikes. In order to avoid expensive repairs or replacements, it is important to conduct regular checks to make sure the system can manage these events without harming sensitive equipment.
Compliance with Standards and Regulations
Adherence to Codes: Regular inspection and maintenance of grounding systems is necessary to ensure compliance with electrical codes and regulations, such as the NEC and the IEC standards. Compliance with these laws is critical for both legal and insurance reasons, it is crucial to comply with these laws.
Certification and Audits: To maintain certification and pass audits conducted by regulatory agencies, regular inspections are required. To avoid fines and keep operations running smoothly, this compliance is essential for commercial and industrial enterprises.
Identifying and Mitigating Potential Issues
Corrosion Detection: Grounding components, particularly those submerged in soil, can corrode. Regular inspections can prevent corrosion in its early stages and maintain the grounding system in good working order. This allows for prompt maintenance and replacement of damaged parts.
Physical Damage: The environment or construction operations can cause physical impacts, such as damage to the grounding conductors and connections. In order to find such damage and fix it before it affects the system's functionality, inspections are necessary.
Maintaining System Performance and Reliability
Performance Verification: Grounding system performance is checked often to ensure a low-resistance path to ground. This verification is essential for electrical system performance and dependability.
Continuity and Integrity Checks: Grounding conductors and connections are inspected for continuity and integrity. Broken or loose connections can limit the efficacy of the grounding system, posing safety risks and device failure.
Preventing Downtime and Operational Disruptions
Proactive Maintenance: Regular inspections can identify and fix grounding issues, preventing unexpected failures and operational disruptions. Proactive maintenance ensures continuous operations and reduces costly downtime.
Long-Term Cost Savings: Grounding system inspections and maintenance extend the life of electrical equipment and infrastructure, saving money. Preventive maintenance is cheaper than reactive repairs.
Ground Resistance Testing
Electrical systems require ground resistance testing to ensure grounding system performance. Testing determines how well the grounding system dissipates electrical currents into the earth. Earth resistance testing ensures that the grounding system provides a low-resistance channel to the earth, protecting equipment and personnel.
Methods of Ground Resistance Testing
Various scenarios and environments necessitate different ground resistance testing methods. Popular methods include:
1. Fall-of-Potential Method
The most common ground resistance test. The tester drives three stakes into the earth: the ground electrode under test, a potential electrode, and a current electrode. The tester calculates resistance by dividing the voltage drop between the ground electrode and the potential electrode by the current flowing between them.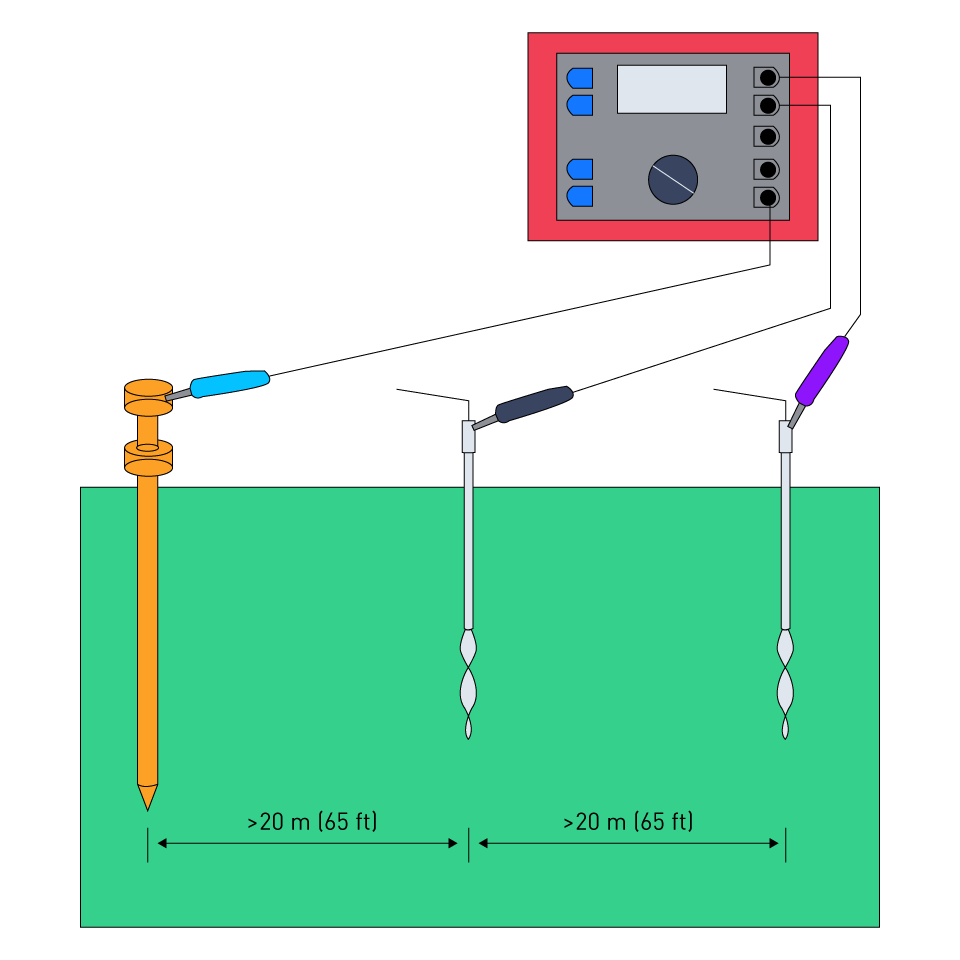
Figure 9: Fall-of-potential ground resistance measurement
Procedure:
- Drive the current electrode to a certain distance from the ground electrode.
- Position the potential electrode halfway between the ground and current electrodes.
- Calculate resistance by applying a test current and measuring voltage drop.
Advantages: Accurate, dependable measurements for large grounding systems.
Limitations: The electrodes require ample space and ground access. Disconnect the site's ground electrode first.
2. Clamp-on Method
A clamp-on ground resistance tester measures resistance without removing the grounding system. It can test individual grounds in multi-grounded systems.
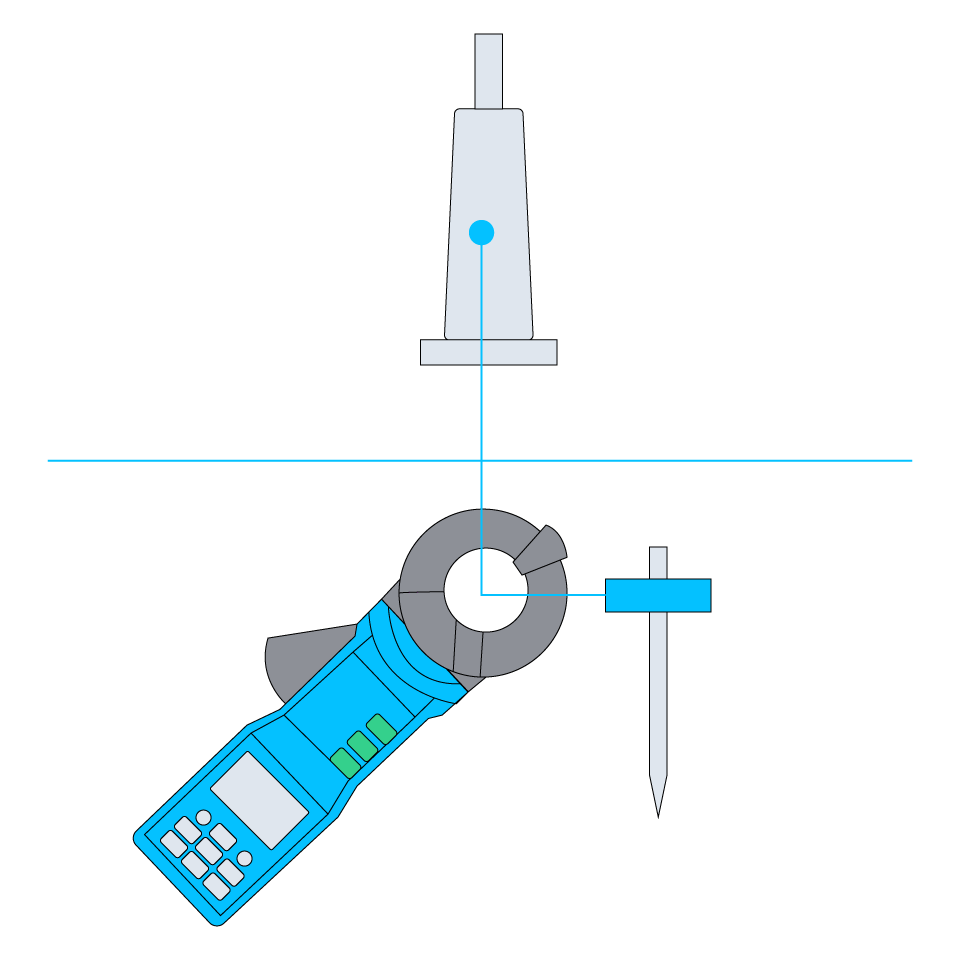
Figure 10: Clamp-on ground resistance measurement
Procedure:
- Positionlace the clamp meter around the ground conductor or rod.
- To compute resistance, the meter creates a test current and detects voltage.
Advantages: No system disruption, non-invasive, fast, and uncomplicated.
Limitations: Complex grounding systems may be less accurate than fall-of-potential.
3. Selective Method
A clamp-on tester and auxiliary electrodes detect ground resistance in the selective technique, like the fall-of-potential method. This method tests certain grounding system pieces.
Procedure:
- Measure resistance at grounding system sites using the clamp-on meter.
- Isolate grounding system sections using auxiliary electrodes for detailed testing.
Advantages: Combines fall-of-potential precision with clamp-on ease.
Limitations: Needs specificRequires specialized equipment and expertise.
Interpreting Test Results
Resistance Values: Acceptable ground resistance values vary by application and specification. Ground resistance around 5 ohms is suitable for most commercial and industrial applications. Critical systems may need lower resistance.
Consistency: Regular testing should produce consistent results. Resistance levels that alter significantly over time may indicate grounding system degradation, necessitating further examination and maintenance.
Environmental Factors: Soil moisture, temperature, and composition all influence ground resistance measures. Interpret test results based on these parameters.
Maintenance and Corrective Actions
Regular Testing Schedule: Schedule ground resistance testing to maintain the grounding system. System criticality and environmental circumstances may affect this timeline.
Corrective Actions: Improve soil conductivity, add ground rods, or repair damaged connections if excessive resistance values are found.
Documentation: Record ground resistance test dates, procedures, and results. This paperwork is necessary for tracking grounding system performance and meeting standards.
Maintenance Practices to Ensure Effective Grounding
Electrical installations require proper maintenance to ensure the reliability and safety of their grounding systems. Regular maintenance detects and fixes problems before they fail, protecting equipment and personnel. For grounding system effectiveness, follow these maintenance steps.
Regular Visual Inspections
Conduct Routine Inspections: Grounding system visual inspections are essential. Examine the grounding conductors, connectors, and electrodes for signs of wear, corrosion, damage, and looseness.
Inspect Grounding Electrodes: Inspect grounding electrodes such as rods, plates, and wires for rust or other damage that could affect the grounding system.
Check Connections: Make sure all connections are secure and corrosion-free. Rusty or loose connections increase resistance and limit grounding system effectiveness.
Cleaning and Tightening Connections
Remove Corrosion: Grounding conductors and connectors might operate poorly if corroded. Frequently clean connections to remove oxidation and corrosion.
Tighten Connections: Loose connections increase resistance and failure. The grounding connections should be tight and secure to maintain a low-resistance channel.
Soil Condition Monitoring
Assess Soil Moisture Levels: Soil moisture affects grounding system resistance. Increasing resistance in dry weather can compromise the grounding system. Grounding electrode soil moisture should be monitored regularly.
Enhance Soil Conductivity: To minimize grounding resistance, add moisture-retaining compounds or conductive materials such as bentonite or conductive concrete to high soil resistivity locations.
Periodic Ground Resistance Testing
Scheduled Testing: Test the grounding system periodically with ground resistance testing. Regular testing detects resistance increases that may need correction.
Document Results: Keep detailed records of ground resistance tests, including date, method, and results. This documentation tracks grounding system performance and identifies trends that may signal concerns.
Environmental Impact Assessments
Monitor Environmental Changes: Construction, soil erosion, and vegetation growth might impact the grounding system. Monitor these changes and make adjustments as appropriate.
Protect Grounding Components: Flooding, soil erosion, and chemical exposure can destroy grounding components.
Preventive Maintenance Programs
Develop a Maintenance Schedule: Preventive maintenance should include inspections, cleaning, connection tightening, and ground resistance testing. Following this schedule keeps the grounding system working.
Train Personnel: Maintenance staff should be skilled in grounding system maintenance. Training should include inspection, cleaning, and ground resistance testing.
Upgrading and Enhancing Grounding Systems
Add Grounding Electrodes: Grounding electrodes can lower resistance in high-resistance circuits. Check the electrode installation and grounding system.
Upgrade Connections and Conductors: Use corrosion-resistant, high-quality materials. Upgrades to better materials can extend grounding system life and performance.
Implement Advanced Technologies: To improve grounding system performance and dependability, consider using sophisticated grounding technologies such as ground augmentation materials or digital monitoring systems.
直接登录
创建新帐号