Surge Protection Devices (SPDs)
Surge Protection Devices (SPDs) are essential components in protecting electrical systems against voltage surges and spikes, which are some of the most frequent and potentially dangerous AC line disruptions. SPDs are intended to safeguard sensitive equipment by controlling transient voltages and directing surge currents away from devices connected to the power supply.
Functionality and Importance of SPDs
Principle of Operation: SPDs detect voltage surges and transient spikes that exceed the typical operating voltage range. The SPD promptly kicks in when it detects these disruptions, transferring any surplus energy to neutral lines or the ground to protect the linked equipment from the surge.
Importance: The major value of SPDs stems from its ability to avoid equipment damage, data loss, and operational downtime caused by electrical surges. This protection is particularly essential for sensitive electronic devices like computers, medical equipment, and industrial control systems, that can be easily damaged by transient voltages.
Types of SPDs
Type 1 SPDs: These devices, which are installed at the service entry, are intended to guard against external surges, especially those brought on by utility grid switching or lightning. For layered surge protection, they are usually used in combination with other kinds of SPDs.
Type 2 SPDs: These are usually positioned at distribution panels, downstream of the service entry. They offer defense against internal surges produced by heavy equipment switching as well as residual surges that flow via Type 1 devices.
Type 3 SPDs: These point-of-use devices offer excellent protection for some sensitive electronics. They are often located near the equipment they protect, providing a last line of defense against surges that may have gone through Type 1 and Type 2 SPDs.
Overvoltage Protective Elements
Overvoltage protective elements are critical components of surge protection devices (SPDs), which protect electrical systems and equipment against transient overvoltages induced by lightning, switching processes, and other causes. These elements are roughly divided into two types: voltage switching components and voltage limiting components. Each category contains a unique set of components meant to defend against overvoltage by either redirecting or clamping the excess voltage.
Voltage Switching Components
When the voltage rises over a certain threshold, voltage switching components turn to an "ON" state, which directs the surge current away from delicate equipment.
Spark Gap: Spark gaps are straightforward devices made up of two electrodes divided by an air or gas gap. The gas ionizes and forms a conductive route between the electrodes when the voltage across the gap is greater than the gas's breakdown voltage. As a result, rather than passing through the protected equipment, the surge current can now flow via the spark gap. Considering that they can withstand high surge currents, spark gaps find extensive use in high-energy applications.
Advantages:
- Capable of managing large surge currents.
- Simple and strong construction.
Disadvantages:
- Slower reaction time than other components.
- Potential for wear and degeneration over time.
Gas Discharge Tube: Similar in functioning to spark gaps, gas discharge tubes (GDTs) provide a more regulated discharge environment by using a sealed tube filled with an inert gas, such neon or argon. The breakdown voltage of GDTs is more consistent, and they can withstand several surges without experiencing significant degradation.
Advantages:
- High surge current handling capabilities.
- Consistent and reliable breakdown voltage.
Disadvantages:
- Response time is slower than with solid-state components.
- Sometimes a larger voltage is needed to start conduction.
Voltage Limiting Components
When a transient overvoltage happens, the impedance of voltage-limiting components increases with voltage rise, clamping the voltage to a safe level and preventing the voltage from above the breakdown threshold of the protected equipment.
Metal-oxide Varistor (MOV): Zinc oxide and other metal oxides are used to make MOVs, which are nonlinear resistive components. The MOV's resistance drastically drops when it is exposed to high voltage, enabling it to conduct and clamp the voltage to a safe level. Because of its great energy absorption capacity and quick reaction time, MOVs are frequently utilized in SPDs.
Advantages:
- Quick response time.
- High capability for absorbing energy.
- Low cost/energy ratio and broad availability.
Disadvantages:
- Can deteriorate with repeated surges over time.
- Limited surge lifetime that needs to be replaced on a regular basis.
Transient Voltage Suppression (TVS) Diode: Semiconductor devices called TVS diodes are used to guard against sudden overvoltages in electronic circuits. They clamp the voltage to a predefined level in response to sudden surges in voltage very rapidly. TVS diodes' quick response time and precise clamping make them perfect for safeguarding delicate electrical components.
Advantages:
- Very quick reaction time (in nanoseconds).
- Accurate voltage clamping.
- Ideal for safeguarding delicate electronics.
Disadvantages:
- Less absorption of energy compared to MOVs.
- May cost more than other protective components.
Installation Considerations
Location: Installing SPDs at several positions across the electrical infrastructure, from the main service entry and distribution panels to individual outlets, is necessary for effective surge protection. This is known as a tiered approach.
Coordination: SPDs must be coordinated with the electrical system's grounding and bonding to provide the best performance. Miscoordination might result in SPD failure or a reduction in the lifespan of the protective system.
Standards and Compliance: SPD installation should follow national and international standards established by organizations like as the IEEE, NEC, and IEC. Compliance with these standards assures that the SPDs are acceptable for their intended uses and are properly installed.
Benefits of SPDs
Reduced Repair and Replacement Costs: SPDs may save businesses a lot of money on repairs and replacements since they protect electrical equipment from damage.
Increased System Reliability: SPDs improve overall system reliability and uptime by reducing surge-related issues.
Enhanced Safety: SPDs improve the safety of electrical systems by reducing the risk of electrical fires and other surge-related dangers.
Voltage Regulation and Stabilization
Stabilization and control of voltage are essential tactics for preserving steady power quality in electrical systems. By guaranteeing that voltage levels stay within a certain range, these methods improve system performance overall and shield equipment from any harm brought on by voltage fluctuations.
Importance of Voltage Regulation and Stabilization
System Stability: Stable voltage is crucial to the reliability of electrical systems, especially in industrial and commercial contexts where sensitive equipment requires consistent voltage to function properly.
Equipment Protection: Voltage fluctuations can cause equipment malfunctions, lower efficiency, and more wear and tear, reducing the lifespan of costly machinery and electronics.
Energy Efficiency: Proper voltage control can improve the efficiency of electrical equipment, decreasing energy waste and operational expenses.
Techniques and Devices
Voltage Regulators: These devices automatically regulate the voltage level to keep it in the specified range. They are crucial in situations when the incoming power source regularly deviates from standard voltage levels.
- Servo-controlled Voltage Stabilizers: These stabilizers employ a servo motor to continually adjust the voltage transformer, correcting for any incoming voltage variations.
- Electronic Voltage Regulators: These regulators use electronic circuitry to respond quickly to voltage changes, making them ideal for sensitive and essential applications.
Line Conditioners: A line conditioner produces a clean, steady power output by regulating voltage in addition to filtering out noise. They are especially helpful in situations when there is a lot of electromagnetic interference, and the equipment is susceptible to small power quality issues.
Tap Changing Transformers: Transformers with on-load tap changers are helpful in high-capacity applications because they can modify their voltage ratios according to the load conditions. This allows the output to remain stable even in the presence of large input voltage changes.
Applications
Data Centers: Stable voltage is crucial in data centers to avoid hardware damage and data loss. Data integrity and continuous service are guaranteed via voltage stability and control.
Hospitals: For medical equipment to function properly, precise voltage levels are often required. Voltage regulators guarantee that these specifications are fulfilled, enhancing patient safety and the standard of care.
Manufacturing Facilities: Voltage variations in the manufacturing process can lead to dangerous working conditions, machine damage, and defective products. Robust voltage control has a major positive impact on both safety and productivity.
Integration with Renewable Energy Sources
Voltage control and stabilization have become more important as renewable energy sources such as solar and wind are integrated into power systems. Because of their intermittent nature, these energy sources may cause voltage fluctuation. Advanced voltage regulation technology can reduce these impacts, guaranteeing a consistent power supply despite the fluctuation of renewable energy sources.
Harmonic Filters
Harmonic filters are specialized devices that reduce the impact of harmonic distortions in power systems. Non-linear loads create harmonics, which can dramatically decrease power quality, resulting in inefficiencies, device failures, and lower electrical infrastructure lifespan. Harmonic filters are essential for reducing these undesirable frequencies, preserving the general health of the power system, and guaranteeing the seamless operation of delicate electronic devices.
Function and Importance of Harmonic Filters
Harmonic filters are used to restrict or divert harmonic frequencies produced by electrical equipment back to the power source, preventing them from spreading throughout the power system.
Importance: These filters improve power systems' reliability as well as efficiency by lowering harmonic distortions. They are essential in cases like data centers, hospitals, and industrial sites where there are extremely high standards for power quality.
Types of Harmonic Filters
Passive Harmonic Filters: These filters use a mix of inductors, capacitors, and resistors to provide a low-impedance route at certain harmonic frequencies. Passive filters are set to target certain harmonics and perform best when the harmonic producing conditions are consistent and predictable.
Active Harmonic Filters: These are modern devices that employ power electronics to feed adequate currents into the power supply. Active filters can adapt to changing conditions and respond to a wide variety of harmonic frequencies, making them ideal for use in situations with diverse and dynamic electrical loads.
Hybrid Harmonic Filters: Hybrid filters combine the qualities of both active and passive filters, providing flexibility and high efficiency levels in contexts with complex and highly changeable harmonic distortion challenges.
Applications and Benefits
Improved Equipment Performance: Harmonic filters shield delicate equipment from harmonic distortions that can lead to malfunctions, overheating, and early aging.
Compliance with Standards: Many sectors are required to follow rigorous harmonic level rules (for example, IEEE-519). Using harmonic filters assists firms in meeting regulatory standards, avoiding penalties and assuring ongoing operations.
Energy Savings: Harmonic filters improve total energy efficiency by lowering harmonic-related losses and increasing power factor, resulting in considerable cost savings in power-intensive applications.
System Stability: Reducing harmonic distortions improves the stability of the power system, lowering the danger of outages and increasing the reliability of electrical supply.
Installation Considerations
System Analysis: Before installation, a detailed investigation of the power system is required to determine the types and sources of harmonic distortion. This analysis guides how to choose between passive, active, and hybrid filters.
Location: Harmonic filters are often put near harmonic sources or at critical locations in the electrical distribution system to enhance their efficacy in reducing disruptions.
Capacity and Rating: Harmonic filters have to be the right size for the load and the particular harmonic frequencies that are used in the system. Improper size might worsen power quality problems and result in inadequate performance.
Challenges and Maintenance
Dynamic Loads: Passive harmonic filters might be difficult to keep working effectively in situations where loads are constantly changing. In such cases, active or hybrid filters—which can adjust to changes in load—might be more appropriate.
Cost Considerations: Active harmonic filters are more sophisticated and cost more than passive filters. The choice to invest in these technologies should balance the long-term advantages of enhanced power quality against the initial expenditures.
Regular Maintenance: Harmonic filters need to be maintained on a regular basis to ensure they continue to operate correctly and effectively, just like any other electrical component. Replacement of worn-out parts, connection checks, and performance monitoring of filters are a few examples of maintenance tasks.
Uninterruptible Power Supplies (UPS)
Uninterruptible power Supplies (UPS) are essential parts of any facility's infrastructure that need clean, steady, and consistent electricity. They act as a buffer against surges, power outages, and other disruptions, guaranteeing that data integrity is preserved, and critical equipment continues to function even in the face of electrical irregularities.
Role and Importance of UPS Systems
Continuous Power Supply: The purpose of UPS systems is to deliver rapid backup power in the event that the primary power supply malfunctions or becomes unstable. In settings where even a momentary interruption of power can have disastrous effects, such as data centers, hospitals, and telecommunications infrastructure, this capacity is crucial.
Power Quality Improvement: UPS systems do more than simply supply backup power; they also enhance the quality of power that reaches linked devices. They do this by conditioning the power, which entails controlling voltage, eliminating noise, and maintaining power frequency stability.
Types of UPS Systems
Standby UPS: This is the most basic kind of UPS, including battery backup and surge protection. Only when it senses a power outage does the UPS switch to battery power. Standby UPS systems are appropriate in less critical areas or in situations with few power outages.
Line-Interactive UPS: These systems provide more complex features including voltage regulation. They regulate voltage levels without the use of batteries, making them more energy efficient. Line-interactive UPS systems are widely utilized in small business settings and for network equipment.
Double-Conversion (Online) UPS: The most modern type of UPS, double-conversion systems, offer total protection by continually converting incoming AC power to DC and then back to clean AC power to power the attached loads. This continual conversion process protects the output from power supply anomalies, making these systems excellent for safeguarding sensitive IT equipment and data center infrastructure.
Table 1: UPS comparison
Feature/Factor | Standby UPS (Offline UPS) | Line-Interactive UPS | Online UPS (Double Conversion) |
---|---|---|---|
Operation | Powers devices directly from the main supply, switching to battery during an outage. | Uses a voltage regulator to handle minor power fluctuations, switching to battery during significant outages. | Continuously converts incoming AC to DC and then back to AC, providing continuous power from the inverter. |
Power Protection | Basic protection against outages and surges. | Moderate protection against surges, sags, and brownouts. | High protection against all types of power disturbances, including outages, surges, sags, brownouts, and electrical noise. |
Switching Time | Typically 5-12 milliseconds. | Typically 2-4 milliseconds. | Zero transfer time, as the inverter is always on. |
Voltage Regulation | No active regulation, relies on battery switch. | Regulates voltage through an autotransformer. | Provides continuous, tightly regulated power with no interruptions. |
Efficiency | High efficiency when on mains power. | High efficiency with minor efficiency loss during voltage regulation. | Lower efficiency due to continuous double conversion process. |
Cost | Least expensive. | Moderately priced. | Most expensive. |
Complexity | Simple design and easy to maintain. | More complex with additional voltage regulation components. | Most complex with continuous conversion circuitry. |
Applications | Ideal for home and small office use with less critical loads. | Suitable for small to medium-sized businesses with moderate protection needs. | Best for data centers, server rooms, and critical applications requiring the highest level of power protection. |
Battery Usage | Uses battery only during outages. | Uses battery during significant power fluctuations and outages. | Continuously uses the battery, even when mains power is available. |
Power Quality | Provides basic power quality. | Improves power quality with voltage regulation. | Delivers the highest power quality with continuous power conditioning. |
Noise Filtering | Basic filtering of electrical noise. | Moderate filtering of electrical noise. | Advanced filtering of electrical noise. |
Applications and Benefits
Reliability: UPS systems improve the stability of electrical systems by providing a fail-safe against power outages and quality concerns, allowing operations to continue uninterrupted.
Equipment Protection: UPS systems help to increase the lifespan of sensitive electronic equipment by stabilizing the power supply and conditioning incoming electricity, protecting it from voltage fluctuations, surges, and other electrical risks.
Operational Continuity: UPS systems are essential for ensuring operational continuity and protecting against data loss and service interruptions in industries such as healthcare, banking, and manufacturing.
Installation and Maintenance Considerations
Capacity Planning: Calculating all of the devices that need to be protected and accounting for future capacity is necessary when selecting the best UPS.
Battery Management: Upgrading batteries regularly is essential to keeping UPS systems operating efficiently. One of the most frequent reasons why UPS fail is failure of the batteries.
System Testing: Regular testing of the UPS system, including a full battery discharge, is required to guarantee that the system functions properly during a power outage.
Lightning Protection
Lightning protection is an important part of protecting electrical systems and infrastructure from the damaging effects of lightning strikes. Lightning surges, with their great intensity and quick increase time, can cause significant damage to structures, electrical lines, and sensitive electronics. Implementing efficient lightning protection measures can help to reduce these hazards and assure the safety and reliability of electrical systems.
Need for Lightning Protection
Lightning protection is necessary because lightning strikes have the potential to inflict considerable damage. These damages include:
Physical Damage: Towers, other infrastructure, and buildings can sustain structural damage from lightning strikes.
Electrical Surges: Lightning strikes can cause high-voltage surges in electrical systems, harming transformers, circuit breakers, and other components.
Fire Hazards: Lightning's tremendous heat can ignite flames in forests and structures.
Data Loss: Surges caused by lightning can cause sensitive electronic equipment, such computers and communication devices, to malfunction and lose data.
Loss of Life: Lighting can critically hurt living beings near the hit site, frequently resulting in death.
Effective lightning protection systems are critical for preventing these damages and ensuring the integrity and operation of electrical systems.
Standards
Several national and international standards offer guidance for developing and installing lightning protection systems. Adherence to these standards guarantees that protective measures are both effective and trustworthy. Some of the important standards are:
NFPA 780: Comprehensive instructions for preventing lightning damage to structures can be found in the National Fire Protection Association (NFPA) Standard for the Installation of Lightning Protection Systems.
IEC 62305: The procedures for risk assessment, system design, and lightning protection measure execution are outlined in the International Electrotechnical Commission (IEC) Standard for Protection Against Lightning.
IEEE 998: Recommendations for shielding substations from lightning strikes can be found in the Institute of Electrical and Electronics Engineers (IEEE) Standard for Direct Lightning Stroke Shielding of Substations.
These standards address risk assessment, system components, installation procedures, and maintenance needs, among other elements of lightning protection.
Lightning Protection Systems
Lightning protection systems are intended to intercept, channel, and dissipate the energy of lightning strikes safely into the earth, thereby safeguarding structures, electrical systems, and humans. The key components of a lightning protection system are:
Air Terminals (Lightning Rods): Air terminals, also known as lightning rods, are pointed metal rods positioned at the structure's highest points. They are intended to attract lightning strikes and give the optimum angle of contact.
- Function: Air terminals intercept lightning strikes and start the safe conduction of lightning electricity to the earth.
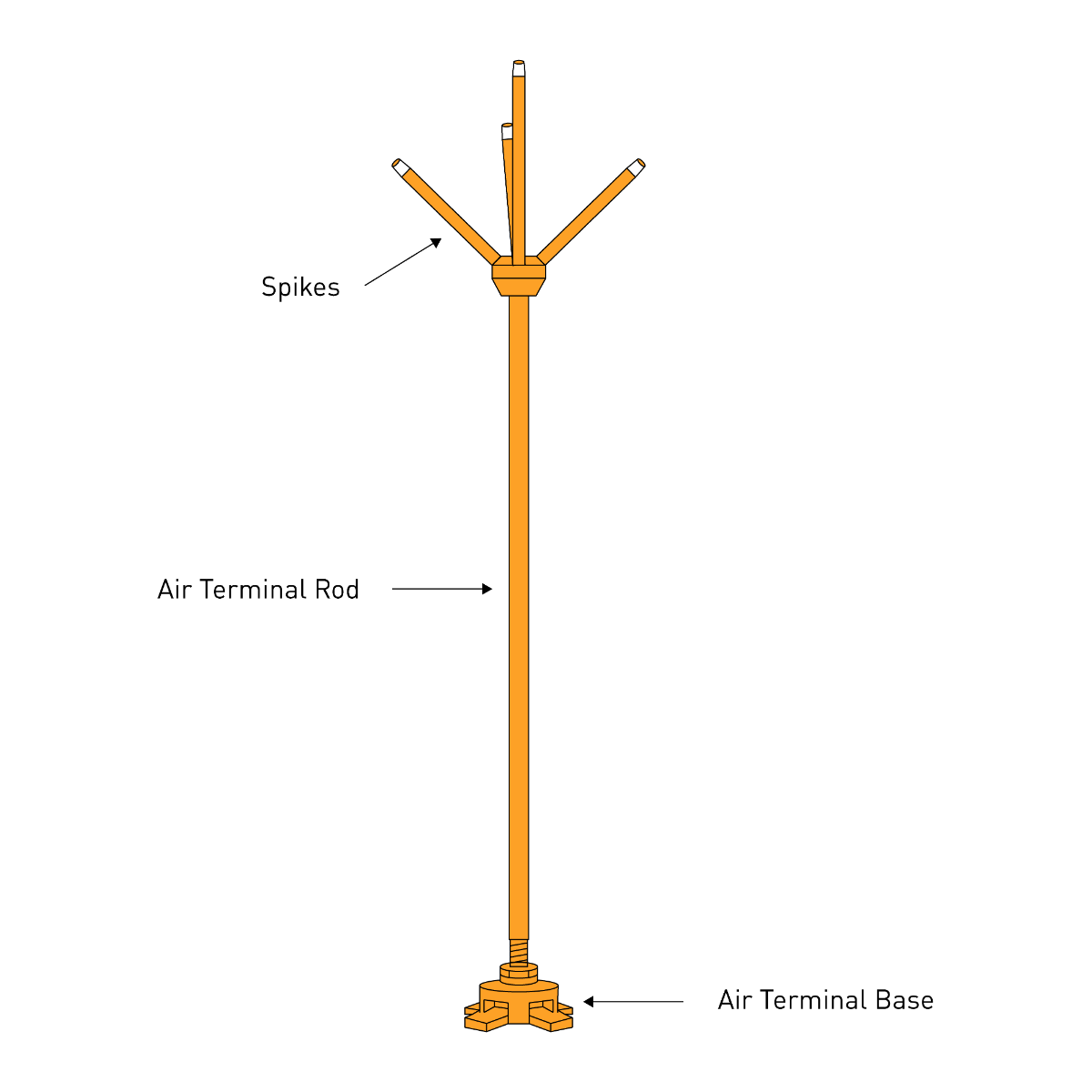
Figure 10: Air terminal
Conductors: Conductors are metal wires or strips used to connect air terminals to the grounding system. They create a low-resistance channel for lightning current to proceed to the ground.
- Function: The lightning current is channeled securely from the air terminals to the grounding system via conductors.
Grounding System: The grounding system is made up of ground rods, plates, or meshes that are buried underground. It provides a safe technique of dissipating lightning current into the earth.
- Function: The grounding system directs lightning energy into the ground, preventing it from inflicting damage to the structure or electrical systems.
Surge Protection Devices (SPDs): To shield delicate equipment from surges caused by lightning, SPDs are put at strategic locations throughout the electrical system. These gadgets clamp or redirect surplus energy to limit the voltage.
- Function: SPDs keep overvoltages from reaching and harming electrical devices.
Bonding and Equipotentialization: Bonding is the process of electrically joining all metal pieces of the structure such that they have the same electrical potential. Equipotentialization eliminates harmful voltage gaps that might result in sparks or electrical arcs.
Grounding and Bonding Techniques
In electrical systems, grounding and bonding techniques are essential safety precautions used to shield workers and equipment from electrical malfunctions. These methods are essential for providing a safe channel for the dissipation of fault currents and static charges as well as for reducing a variety of electrical disturbances, including surges.
Importance of Grounding and Bonding
Safety: The main goal of grounding is to stop voltages from building up which might shock anyone who comes into touch with electrical equipment's non-insulated parts.
System Protection: Grounding offers the least resistance channel for electrical current to go back to the source or into the ground, safeguarding the system from harm caused by electrical faults.
Enhanced Reliability: Proper grounding and bonding increase the electrical system's overall reliability by stabilizing voltage levels and assisting in the effective removal of faults.
Grounding Techniques
System Grounding: This entails connecting a system's neutral point to ground. System grounding serves to stabilize the voltage during normal operations and remove faults by providing a channel back to the source.
Equipment Grounding: Equipment grounding makes sure that an electrical device's conductive components, which may accidentally get electrified, are linked to the ground. The safe dissipation of fault currents is aided by this connection.
Earthing: One popular technique is earthing, which involves driving an electrode or ground rod into the ground. Static discharges and fault currents are intended to be securely dispersed into the ground via the earthing system's low resistance channel, protecting individuals as well as equipment in the process.
Bonding Techniques
Bonding: Bonding connects all non-current carrying metallic components in an electrical system, such as enclosures, frames, and raceways, to provide an electrically conductive channel. This channel eliminates any possible difference between conductive elements, lowering the risk of electric shock or sparks that might ignite combustible substances.
Table 2: Earthing vs. Grounding vs. Bonding
Aspect | Earthing | Grounding | Bonding |
---|---|---|---|
Definition | Connecting the non-current carrying parts of electrical equipment to the earth. | Connecting electrical systems to the earth to ensure safety and stability. | Connecting metallic parts of an electrical system to ensure they are at the same potential. |
Purpose | To prevent electric shock by ensuring that exposed conductive parts do not become live in the event of a fault. | To stabilize the voltage levels of the electrical system and to provide a path for fault currents. | To eliminate potential differences between conductive parts and reduce the risk of electric shock and equipment damage. |
Typical Components | Earth rods, earth mats, or earth plates buried in the ground. | Ground rods, ground plates, grounding electrodes, or ground grids. | Conductive paths, such as bonding conductors, straps, or jumpers, between metallic parts. |
Key Function | Protects people and equipment from electrical faults by providing a low-resistance path to the earth. | Stabilizes electrical systems and helps protect against lightning, surges, and unintentional contact with higher voltages. | Ensures that all metal parts are at the same electrical potential to prevent shock hazards and ensure effective operation of protective devices. |
Regulations and Standards | Governed by local electrical codes, IEC standards, and IEEE standards. | Governed by local electrical codes, IEEE standards, and IEC standards. | Governed by local electrical codes and standards such as NEC (National Electrical Code) and IEEE. |
Examples of Application | Earthing the frame of electrical appliances, machinery, and transformers. | Grounding the neutral of power systems, grounding of substation equipment. | Bonding of metal water pipes, gas pipes, metal enclosures of electrical equipment. |
Impact on Safety | Essential for preventing electric shock by ensuring exposed metal parts do not carry voltage. | Essential for overall system safety, voltage stabilization, and protection from lightning strikes. | Critical for eliminating differences in potential between conductive parts, thereby preventing shock and fire hazards. |
Measurement | Typically measured in ohms, representing the resistance between the earth electrode and the ground. | Typically measured in ohms, representing the resistance between the ground electrode and the ground. | Typically measured in ohms or milliohms, representing the resistance between bonded parts. |
Testing Methods | Earth resistance test, fall-of-potential method. | Ground resistance test, fall-of-potential method, clamp-on ground testing. | Continuity testing, resistance measurement between bonded parts. |
Applications and Benefits
Prevention of Electrical Fires: Proper grounding and bonding prevent electrical fires by eliminating unwanted voltage on conducting elements.
Noise Reduction in Systems: Grounding can minimize electrical noise on grounding and bonding networks, which is important for the operation of sensitive electronic equipment.
Compliance with Electrical Codes and Standards: In accordance with several national and international electrical codes and standards, including the National Electrical Code (NEC) in the United States, implementing grounding and bonding techniques is not only advised but also required.
Maintenance and Testing
Regular Inspections: To maintain the integrity of the grounding and bonding systems over time, regular testing and inspections are essential. Their effectiveness can be compromised by physical harm, corrosion, or modifications to the electrical system.
Resistance Testing: Periodic testing of the grounding system's resistance, such as the fall-of-potential test, guarantees that the grounding is effective and within the safe limits specified by relevant standards.
直接登录
创建新帐号