Exploring Sensor Technologies: A Comprehensive Guide to Magnetic Position Sensors and Their Competitors

Get valuable resources straight to your inbox - sent out once per month
We value your privacy
Introduction
In the dynamic realm of engineering, accurate position sensing plays a vital role in numerous applications. From industrial automation intricacies to robotic precision and vehicle control systems, the need for precise position detection is paramount. Magnetic position sensors have emerged as a prominent choice due to their unique advantages, making them highly attractive in various scenarios.
Nevertheless, to fully comprehend their potential and make well-informed sensor selections, it is essential to compare magnetic sensors with other types like optical, capacitive, inductive, and ultrasonic position sensors. This comparative analysis allows engineers and designers to identify the strengths and weaknesses of each sensor type, enabling them to choose the most suitable sensor for specific applications, thereby enhancing overall performance and efficiency in engineering endeavors.
Table 1 lists the principles for certain sensors, as well as their advantages and disadvantages.
Table 1: Summary of Sensor Types
Sensor type | Principle | Advantages | Disadvantages |
Optical position sensor | Utilizes optical technology for position measurement. | Enables non-contact measurement with exceptional resolution and accuracy, boasting rapid response times. | Prone to interference from ambient light and temperature fluctuations, requiring a clear line of sight. |
Capacitive position sensor | Utilizes changes in capacitance to measure position or displacement. | Offers high resolution and sensitivity at a cost-effective price point, capable of measuring through non-conductive materials. | Susceptible to changes in humidity and temperature, necessitating calibration for each target material, and susceptible to noise. |
Inductive position sensor | Utilizes magnetic induction for position or displacement measurement. | Provides robust and reliable performance, immune to dust and moisture, and can function effectively in high-temperature environments. | Limited in range and resolution, impacted by nearby metal objects, and necessitating a conductive target. |
Ultrasonic position sensor | Utilizes sound waves for distance or position measurement. | Enables non-contact measurement at a low cost with user-friendly operation, capable of detecting soft or transparent objects. | Vulnerable to noise and air turbulence, resulting in low resolution and accuracy, with a slow response time. |
Magnetic position sensor | Utilizes magnetic fields for position or angle measurement. | Enables contactless measurement with remarkable durability and robustness, designed to withstand harsh environmental conditions. | Sensitive to external magnetic fields, leading to limited range and resolution. |
Optical Position Sensors
Optical position sensors, which function based on light reflection or interruption, have established a specialized role in applications where utmost precision is essential. Their significance is particularly prominent in sophisticated fields like microscopy and semiconductor manufacturing, where precision is paramount. These sensors operate on a simple yet effective principle: by detecting and measuring alterations in light, they can accurately ascertain positional changes. As a result, they offer the level of accuracy required to meet the stringent demands of such precise industries.
Figure 1 shows the operational mechanism of an optical position sensor. The sensor emits a light beam that hits a mirror and is then directed onto an engraved strip. This strip modulates the light, and the modified light is captured by a light receiver. By processing this signal, the sensor can accurately determine the position along the strip. Nevertheless, despite their inherent precision, optical sensors do have a notable weakness: they exhibit high sensitivity to environmental conditions. Factors like dust, humidity, and other particulates have the potential to disrupt the light path, leading to possible inaccuracies in readings.
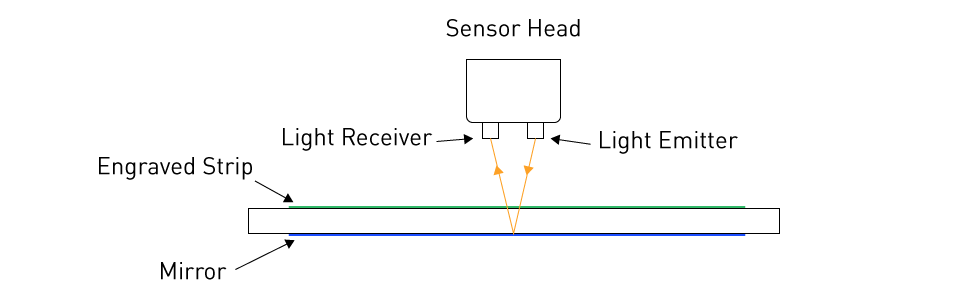
Figure 1: Optical Position Sensor Working
Consequently, these sensors may be less suitable for use in harsh or uncontrolled environments where such environmental interferences can occur. In sharp contrast, magnetic position sensors continue to be reliable even in these demanding circumstances. They can consistently provide precise readings, are unaffected by dust or humidity, and are a desirable option for applications in challenging situations. It's crucial to remember that high-end optical sensors may still outperform magnetic sensors in terms of resolution and accuracy.
Capacitive Position Sensors
Capacitive position sensors are built upon the principle of gauging alterations in electrical capacitance to precisely establish an object's position. Recognized for their exceptional accuracy and ability to withstand temperature fluctuations, these sensors are widely applied across various industries. There are two primary approaches employed for detecting object position in capacitive position sensors, described below.
Changing the Capacitor's Dielectric Constant
Figure 2 shows the operation of a capacitive position sensor when the dielectric constant changes. The capacitance can fluctuate depending on how the dielectric is positioned in relation to the plates, and this is monitored.
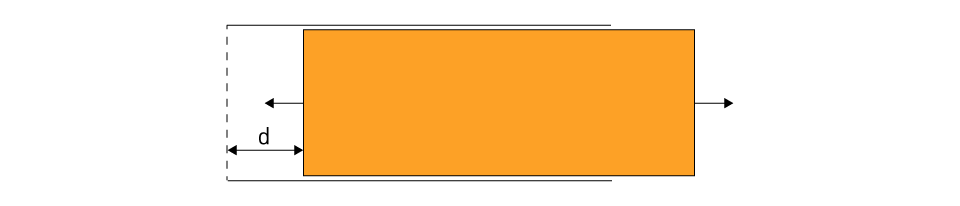
Figure 2: Changing Dielectric Constant
Changing the Overlapping Area of the Capacitor Plates
Figure 3 shows how the capacitive position sensor works when one of the capacitor's two plates' overlapping regions changes. A fluctuation in capacitance is produced by the change in the overlapping region and is then recorded. Capacitive sensors do, however, have some drawbacks. Changes in the material being sensed or its proximity to the sensor may make them especially sensitive. Additionally, situations with a lot of electromagnetic interference might seriously impair their functionality.
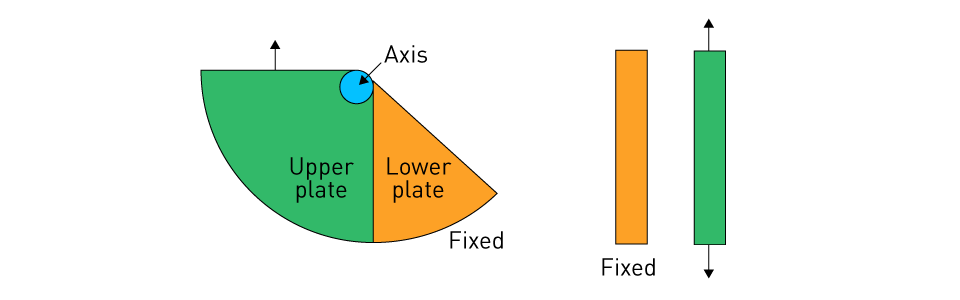
Figure 3: Changing Overlapping Area of Upper Plate
On the other hand, magnetic location sensors exhibit resistance to such difficulties. They continue to function well even in situations with significant electromagnetic noise and are mostly unaffected by changes in the material being felt. They are frequently a favored option in electrically loud conditions due to their robustness.
Inductive Position Sensors
Inductive sensors provide reliable performance in a range of applications by operating on the idea that variations in the inductance of an electrical circuit are caused by the movement of a metallic item. They are especially well suited for industrial applications where filthy, dusty, or wet situations are frequent due to their resistance to these circumstances.
Figure 4 shows how a typical inductive proximity sensor functions. The sensor contains an oscillator that generates an electromagnetic field, extending from the sensing face. When metallic objects come into close proximity, eddy currents are induced in them, causing a modification in the oscillation amplitude. This change in amplitude triggers a corresponding alteration in the output state, following Lenz's law.
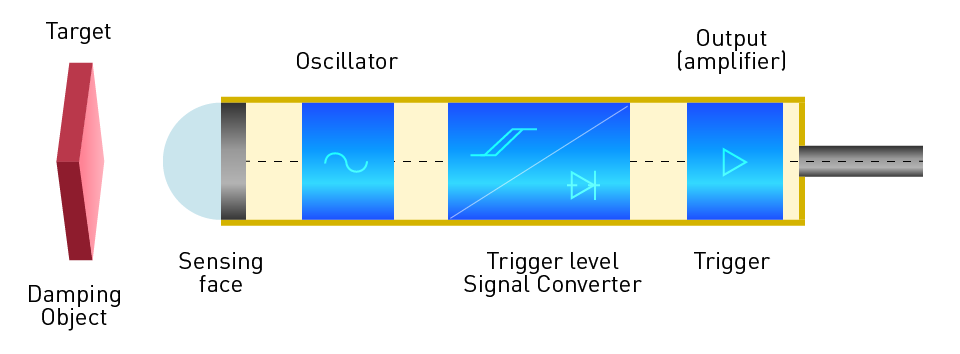
Figure 4: Working of Inductive Proximity Sensor
Inductive position sensors encompass various types, among which linear variable differential transformers (LVDTs) and rotary variable differential transformers (RVDTs) are commonly employed. Both LVDTs and RVDTs operate on the same principle of inductance change but are specifically designed to measure different types of motion. LVDTs are utilized for linear displacement measurement, while RVDTs are well-suited for capturing rotary displacement. However, inductive sensors typically have a narrow sensing range, and the presence of nearby metallic objects may compromise their function. This can be difficult in tight mechanical spaces where several metallic components cohabit. Due to their lack of these restrictions, magnetic position sensors provide a wider sensing range, increasing their flexibility in a variety of applications. Their versatility and application range is increased by their capacity to detect through non-magnetic materials.
Ultrasonic Position Sensors
Ultrasonic sensors are a great option for level sensing applications since they have a wide detecting range and use the propagation of sound waves produced by piezoelectric crystal transducers to measure distance (see Figure 5). When the sensor can't be placed close to the target, its capacity to determine position without physical contact is a big advantage.
Figure 5 shows ultrasonic position sensor operation. This sensor works by sending out ultrasonic waves, then watching for them to re-enter the air after colliding with anything. The sensor can precisely determine the distance to an object by computing the delay between signal transmission and reception. Precision position sensing is made possible by this operating principle in a variety of applications, including robotics and car parking systems.
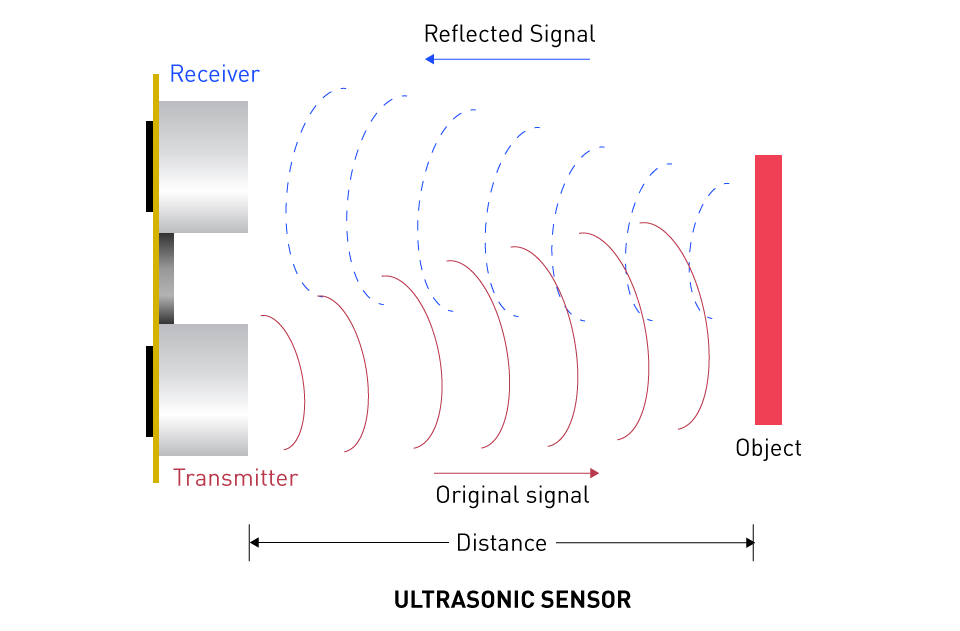
Figure 5: Working of Ultrasonic Position Sensor
However, a number of variables, including temperature fluctuations, wind, and alterations in the surface conditions of the object being sensed, can have an impact on how well they operate. These elements may affect the sound waves speed and reflection, which could result in errors.
Once more, magnetic sensors show themselves to be a more reliable choice. They can perform consistently and dependably because of the way they work, which renders them resistant to the variables that can affect how well ultrasonic sensors work.
Cost Comparison of Magnetic Sensors with their Competitors
Cost concerns are frequently the main deciding factor when choosing a sensor technology. This covers not just the original purchase price but also ongoing maintenance costs and the sensor's durability.
- Magnetic Sensors: Despite having a somewhat higher initial cost, magnetic sensors, which are renowned for their great endurance, frequently provide a lower total cost of ownership during their lifespan. They are a cost-effective option for many applications due to their robustness, which leads to little maintenance requirements and long-term reliability.
- Optical Sensors: Despite typically being less to acquire than magnetic sensors initially, optical sensors may require more frequent maintenance. This is because they require frequent cleaning or perhaps replacement because they are sensitive to environmental pollutants like dust or dirt.
- Capacitive Sensors: These sensors can be quite precise while having a reasonably inexpensive initial cost. However, they are sensitive to temperature and humidity fluctuations, which could necessitate more regular calibration and possibly even replacement, increasing long-term expenditures.
- Inductive Sensors: Similar to magnetic sensors, inductive sensors are often robust and resistant to environmental variables. However, because of how intricately they are built, their initial cost may be rather considerable. They often have low maintenance costs.
Example of Position Sensors Applications
Position sensors play a key role in a variety of applications in different sectors. Let's look at several instances where these adaptable sensors are used.
- Magnetic Position Sensors: Automotive applications frequently use magnetic sensors. They are crucial for the durability, accuracy, and long-term dependability of throttle and brake position sensors. Magnetic sensors are also utilized in robotic arm position tracking in industrial automation, where they benefit from their high precision and resistance to environmental disturbance.
- Optical Position Sensors: Optical position sensors are used in a variety of imaging and diagnostic devices, such as endoscopes and microscopes, in the medical industry. They offer advantages including high precision and non-contact operation. Their high resolution and precision are important benefits in industrial applications for alignment and quality control procedures.
- Capacitive Position Sensors: Capacitive sensors have widespread applications in various consumer electronic devices. One notable example is their integration into the touch screens of smartphones and tablets, providing several advantages such as efficient power usage and exceptional sensitivity. In the industrial domain, capacitive sensors play a pivotal role in proximity sensing and liquid-level detection tasks. An outstanding feature of these sensors is their ability to function through non-conductive materials, which confers a considerable advantage in diverse scenarios.
- Inductive Position Sensors: The implementation of inductive sensors primarily revolves around heavy-duty industrial applications. These robust sensors find extensive usage in various settings like CNC machines, elevators, and assembly lines. Their non-contact nature proves to be invaluable in these demanding environments, ensuring minimal wear and tear. Additionally, the sensors' high durability and resilience to dust, dirt, and moisture further enhance their suitability for deployment in such challenging conditions.
Emerging Trends in Sensor Technologies
As we delve deeper into the world of sensor technology, it becomes evident that emerging trends and ongoing advancements are influencing the future of position sensors. For example, a rising interest lies in combining different sensor technologies to capitalize on their strengths and mitigate their weaknesses effectively.
By integrating magnetic sensors with other types like optical or capacitive sensors, a promising avenue opens up, offering improved performance and heightened reliability. Moreover, the rise of sophisticated signal processing and machine learning algorithms presents the potential to extract greater value from sensor data, leading to enhanced accuracy and the ability to compensate for inherent limitations or biases in the sensors. These advancements hold the key to elevating the performance of magnetic position sensors and broadening their scope of applications significantly (see Figure 6).
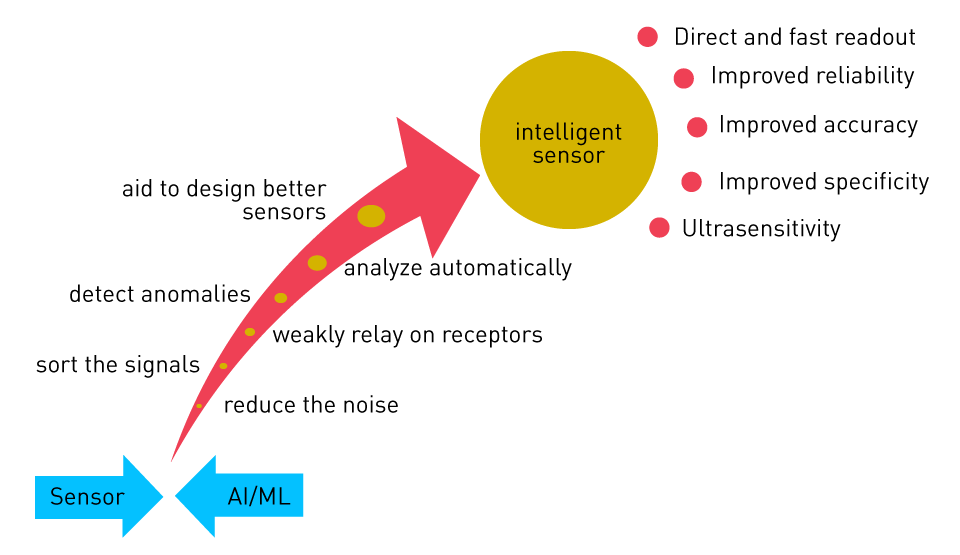
Figure 6: Integration of AI in Sensors – Intelligent Sensors
Conclusion
In conclusion, the field of position sensing is large and varied, with each type of sensor bringing distinct advantages and disadvantages to the table. Magnetic position sensors have some drawbacks despite their outstanding resistance to external factors and capacity to detect through non-magnetic materials.
The selection of the appropriate sensor type requires careful analysis of the application in question and its requirements concerning accuracy, resolution, sensing range, climatic conditions, and cost. Engineers must consequently have a thorough understanding of how magnetic position sensors compare to other types in terms of performance. This information will be extremely helpful as they navigate this complex area and create effective, dependable, high-performance systems to satisfy the needs of their specific applications.
_______________________
Did you find this interesting? Get valuable resources straight to your inbox - sent out once per month!
直接登录
创建新帐号