Delving into the theoretical underpinnings of the buck topology unveils critical considerations that guide its design and optimization. Voltage regulation, a cornerstone of power electronics, involves maintaining a stable output voltage despite variations in input voltage or load conditions. The buck converter achieves this through the modulation of switch-on and switch-off times, ensuring precise control over the energy transfer process. Efficiency considerations are paramount in the design process, reflecting the ratio of output power to input power. Minimizing losses in the conversion process is a constant pursuit, demanding a nuanced understanding of factors such as conduction losses, switching losses, and magnetic losses.
The theoretical foundations of the buck topology extend beyond mere functionality; they embody a delicate balance of control, precision, and efficiency. As engineers navigate the intricate landscape of power electronics, a mastery of these fundamental concepts becomes indispensable. It is through this comprehensive understanding that innovative designs emerge, pushing the boundaries of efficiency and performance in the realm of buck converter applications.
Additional theoretical concepts are described below.
Duty Cycle
The duty cycle in a buck converter is a critical parameter that defines the proportion of time the switch is in the ON state compared to the total switching period. Mathematically, it is expressed as the ratio of the ON time to the total period.
$$\text{Duty Cycle}= D = \frac {T_{ON}}{T_{ON}+T_{OFF}}$$The duty cycle directly influences the output voltage: a higher duty cycle results in a higher output voltage, while a lower duty cycle leads to a lower output voltage. Such that:
$$V_{OUT}=D \times V_{IN}$$Engineers carefully adjust the duty cycle to achieve the desired output voltage based on the application requirements.
The duty cycle also impacts the following:
Efficiency: The duty cycle affects the efficiency of the buck converter. Generally, higher duty cycles result in higher efficiency because the converter spends more time in the continuous conduction mode (CCM), where switching losses are minimized. However, very high duty cycles can lead to increased conduction losses in the switch and other components, which may reduce efficiency.
$$η= \frac {P_{out}}{P_{in}}$$Where Pout and Pin are the output and input powers respectively.
$$P_{out} = P_{in} - P_{losses}$$Plosses is the power loss which can happen due to conduction and switching and is defined mathematically as:
$$P_{losses} = P_{conduction} + P_{switching}$$Output Current Ripple: The duty cycle influences the output current ripple of the buck converter. Output current ripple is the variation in the output current during each switching cycle. Higher duty cycles typically result in lower output current ripple because the inductor has more time to recharge during each switching cycle, leading to smoother output current.
Switching Frequency: In some designs, the duty cycle may indirectly impact the switching frequency of the buck converter. Higher duty cycles may require lower switching frequencies to maintain continuous conduction mode (CCM) operation and avoid excessive conduction losses. Conversely, lower duty cycles may allow for higher switching frequencies without entering discontinuous conduction mode (DCM).
Stability: The duty cycle can also impact the stability of the buck converter's control loop. Proper selection and control of the duty cycle are essential to ensure stable operation and prevent issues such as instability, overshoot, or undershoot in the output voltage.
In summary, the duty cycle plays a crucial role in the operation and performance of a buck converter, affecting parameters such as output voltage, efficiency, output current ripple, and stability. Designers must carefully select and control the duty cycle to meet the requirements of their specific application while optimizing efficiency and performance.
Continuous vs. Discontinuous Conduction Modes
The operating mode of the buck converter is characterized by the behavior of the inductor current during the switching cycle. In continuous conduction mode (CCM), the inductor current never reaches zero during one complete cycle. This mode is typically preferred for applications with varying loads, as it provides smoother and more predictable operation. On the other hand, discontinuous conduction mode (DCM) occurs when the inductor current drops to zero during a portion of the switching cycle. DCM is often employed in low-power applications or when the load varies within a narrow range. The choice between CCM and DCM involves a trade-off between component stresses, efficiency, and complexity of control circuitry.
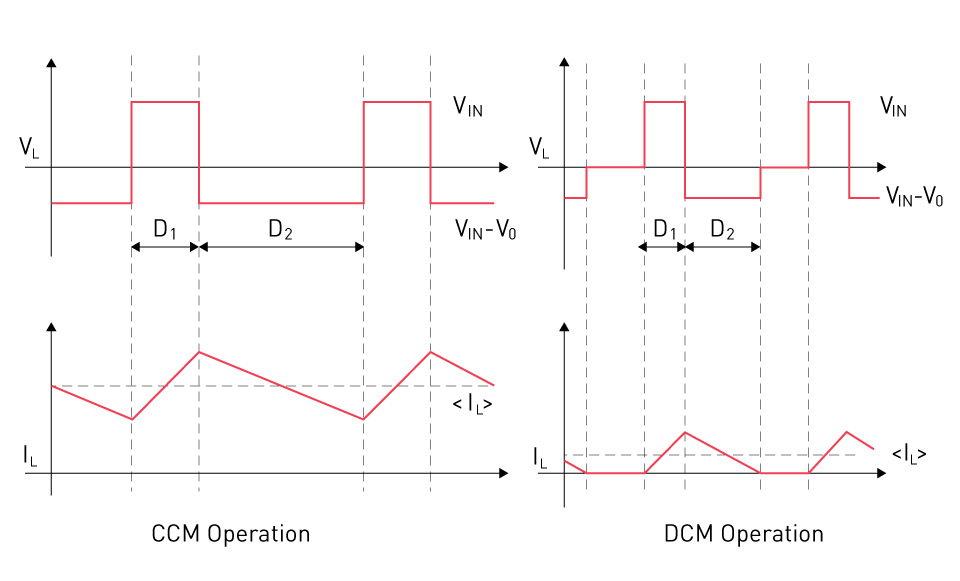
Figure 8: CCM vs. DCM
As it is evident from the figure that in CCM load current never reaches zero which means the circuit is supplying the current for the whole time. However, in DCM the load current may reaches to zero by in a part of the cycle. Still DCM offers higher efficiency sometimes due to the lack of reverse recovery loss on the diode. But not when the duty cycle is too small because it will force a very high current to charge the inductor reducing overall efficiency of the converter.
Advantages of CCM
Stable Output Voltage: CCM provides a more stable output voltage across a wide range of load currents because the inductor current never drops to zero during the switching cycle.
Lower Output Voltage Ripple: Typically, CCM results in lower output voltage ripple compared to DCM, which can be beneficial for applications requiring tight voltage regulation.
Reduced EMI: CCM operation can lead to better electromagnetic interference (EMI) because of the smoother current waveforms and reduced current harmonics.
Disadvantages of CCM
Higher Component Stress: Components such as the inductor and capacitor may experience higher stress due to continuous current flow, potentially leading to larger component sizes and costs.
Lower Efficiency at Light Loads: CCM may exhibit lower efficiency at light load conditions due to increased conduction losses in the switch and other components.
Limited Efficiency at High Loads: In some cases, CCM may not be as efficient as DCM at very high load currents due to increased switching losses.
Advantages of DCM
Higher Efficiency at Light Loads: DCM can offer higher efficiency at light load conditions because it minimizes conduction losses when the load current is low.
Simplified Control: DCM can simplify control circuitry since it naturally occurs at light loads without requiring complex control algorithms.
Reduced Component Stress: Components may experience reduced stress in DCM due to intermittent current flow, potentially leading to smaller and cheaper components.
Disadvantages of DCM
Higher Output Voltage Ripple: DCM typically results in higher output voltage ripple compared to CCM, which may require additional filtering or regulation techniques in sensitive applications.
Limited Stability: DCM operation may lead to stability issues, especially if the control loop is not properly designed to handle the discontinuous nature of the current waveform.
Increased EMI: DCM operation can lead to worse electromagnetic interference (EMI) due to the discontinuous current waveforms and potential ringing effects.
In summary, the choice between CCM and DCM depends on various factors including the specific application requirements, load conditions, efficiency goals, and cost constraints. Designers often optimize their buck converter circuits to transition smoothly between CCM and DCM based on load conditions to achieve the best compromise between efficiency, stability, and other performance metrics.
Impact on Efficiency
Efficiency in a buck converter is a multifaceted consideration influenced by various factors:
Conduction Losses: These losses occur when the switch is in the ON state, and current flows through the inductor and switch. Higher conduction losses are associated with higher input voltages and load currents.
Switching Losses: As the switch transitions between ON and OFF states, there is an inherent loss due to finite switching speed. Faster switching reduces the time the switch spends in transition, minimizing losses.
Magnetic Losses: These losses result from the magnetic field created by the inductor. Proper design considerations, including core material and inductance values, impact magnetic losses.
Trade-offs in Design Choices and Performance
Switching Frequency vs. Efficiency: Choosing a higher switching frequency allows for smaller, more lightweight components but may increase switching losses. Engineers must carefully select the optimal frequency considering efficiency and thermal considerations.
Inductor Size vs. Output Ripple: A smaller inductor reduces size but may lead to increased output voltage ripple. The trade-off involves finding the right balance between size constraints and output voltage stability.
Complexity of Control Circuitry vs. Performance: More sophisticated control circuitry can enhance performance, particularly in dynamic load conditions. However, it comes at the cost of increased complexity and potential for higher component count.
Navigating these trade-offs requires a nuanced understanding of the application's requirements and a careful consideration of the specific challenges posed by the design constraints. Engineers must strike a delicate balance to optimize the buck converter for efficiency, stability, and reliability in diverse operating conditions.
直接登录
创建新帐号