Centralized
Centralized isolated power supply architectures play a crucial role in gate driver applications, offering a streamlined approach to power distribution and isolation that is specifically designed to meet the needs of gate driving requirements. This architecture type centralizes the power supply into a single unit, which then distributes power to different components of the system, ensuring electrical isolation when needed.
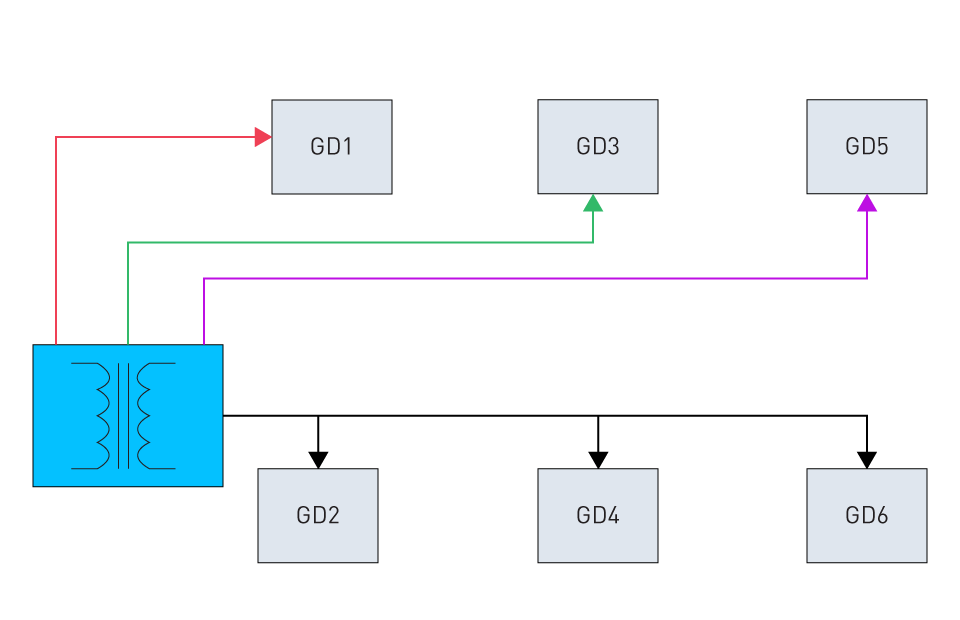
Figure 1: Centralized Architecture
The main power conversion in a centralized architecture, which includes isolation, takes place in a single location within the system. This serves to convert the input power into the different voltage levels needed by the system's components. It effectively separates the input from the output using isolation transformers or other isolation techniques, safeguarding sensitive electronics from high voltages or noise from the power source.
Advantages
The centralized approach offers several key benefits:
Simplified System Design: By consolidating power conversion and isolation into a single location, the design becomes less complex, making it easier to manage power delivery throughout the system.
Cost-Effectiveness: Centralized power supplies offer a more cost-effective solution, particularly in systems with low power requirements for individual components. A single power supply unit can efficiently meet these demands.
Enhanced Reliability: By focusing on a single primary power supply, the overall system's reliability can be enhanced. Centralized systems typically include strong protection features to prevent overvoltage, undervoltage, and thermal overload, which helps to extend the lifespan of the system.
Challenges
On the other hand, centralized architectures also come with their fair share of challenges.
Scalability Limitations: When the system grows or requires more power, the centralized power supply may require extensive upgrades or replacement, resulting in increased costs and added complexities.
EMI: The concentration of traces and components in this scenario can lead to the generation of electromagnetic emissions in a specific area. Extended traces can function as antennas and have the potential to transmit and receive electromagnetic interference, leading to EMI issues within the system. These factors can cause a decrease in system performance, an increase in noise levels, and potential reliability problems as longer traces become more vulnerable to external interference.
Fault Management: Managing faults in centralized power supplies can be quite challenging since they have the potential to impact multiple gate drivers, which in turn can have a significant impact on the overall system.
Increased Power Distribution Losses: When transmitting electricity over longer distances within a system, power distribution losses can be a concern. These losses can have a negative impact on overall efficiency.
Thermal Management: Concentrated heat production can be caused by the concentration of power conversion in a single unit. Implementing effective thermal management solutions that can effectively dissipate heat becomes critical to ensure the system's operational integrity.
Size and Weight: The size and weight of components used in centralized power supplies result in supply units that are bulky and heavy. This may impact the ease of moving the object and pose difficulties for designs that have limited space.
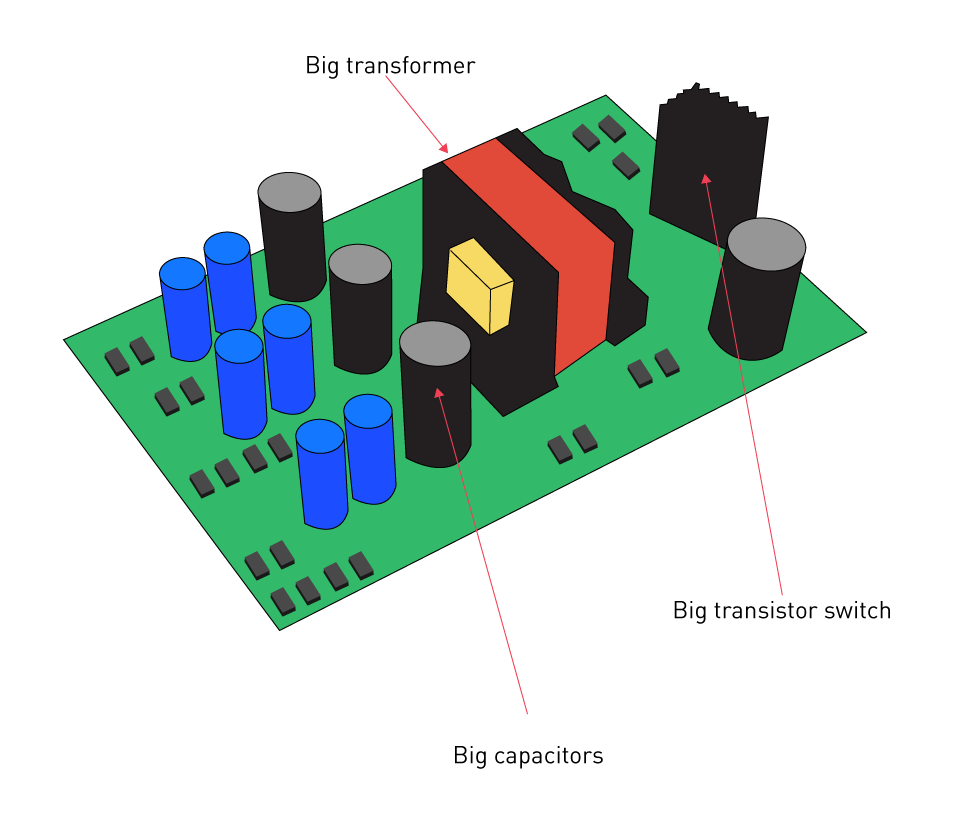
Figure 2: Large Components for Power Supplies with Centralized Architecture
Applications
Centralized, isolated power supplies for gate drivers are essential components in electric vehicle (EV) powertrain systems. As an illustration, the Tesla Model S employs a system that effectively handles the high-power semiconductor switches in the car's inverter. This centralized approach plays a crucial role in enhancing the reliability and performance of the electric drive system in EVs, highlighting its significance in contemporary vehicle technology.
The use of centralized, isolated power supplies for gate drivers in industrial robotics is critical to ensuring accurate and secure operations. ABB, a renowned robotics company utilizes this architecture in their control systems for robotic arms. This not only improves the accuracy of movements but also prioritizes safety in automated processes, thereby highlighting the importance of centralized, isolated power supplies in intricate industrial machinery.
Distributed
Power supply architectures that are distributed and isolated offer a flexible and effective solution for delivering power to intricate electronic systems. This architecture differs from centralized models in that it distributes multiple, smaller, isolated power supplies throughout the system in close proximity to the points of load. This close proximity reduces power loss during transmission and enables more precise power management, catering to the specific requirements of various subsystems.
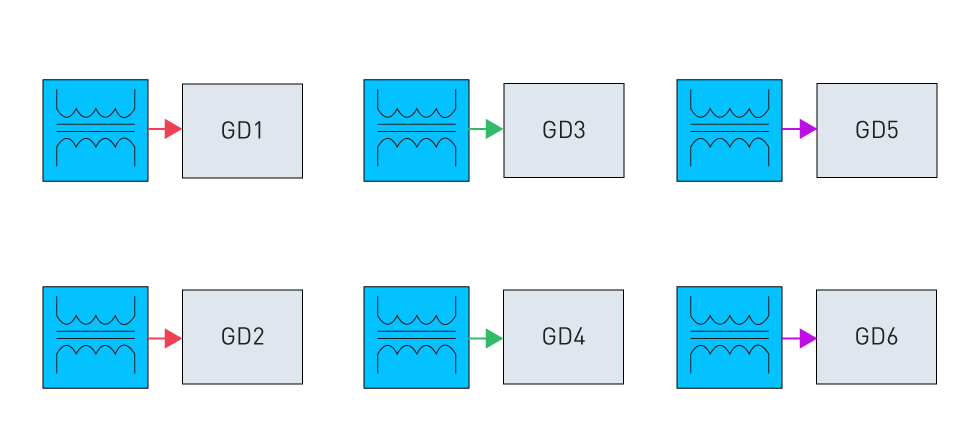
Figure 3: Distributed Architecture
Advantages
Reliability: Ensuring reliability is crucial in distributed architectures, where each power supply is assigned to a specific section of the electronic system, such as gate drivers or sensor modules. This segmentation improves the overall system's reliability by preventing a single power supply failure from affecting the entire system's integrity. This is in contrast to what could happen in a centralized architecture. It streamlines the design and integration of intricate systems, enabling designers to concentrate on the unique power needs of each subsystem separately.
Scalability: In addition, distributed architectures provide substantial benefits in terms of scalability and flexibility. As electronic systems continue to advance, incorporating or adjusting isolated power supplies to support new components or features becomes easier, without the need for a complete overhaul of the central power supply. This systematic approach not only reduces development time and expenses, but also simplifies the process of identifying and resolving issues as well as maintaining the system.
Improved Thermal Management: When it comes to thermal management, distributed architectures truly shine. Strategic power supply distribution evenly distributes heat generation throughout the system, reducing the risk of hotspots that could compromise component reliability. In addition, this distribution method enables more efficient utilization of space within the device, making it easier to accommodate compact or irregularly shaped designs that could pose difficulties for centralized power supplies.
Compact Size and Low Weight: Applications that require distributed, isolated power supply architectures highly value compact size and low weight. These architectures effectively minimize the necessity for lengthy power distribution lines by integrating isolated power supplies near gate drivers, resulting in a decrease in both system size and weight. This approach is especially beneficial in applications with limited space, such as aerospace or portable electronic devices, where size and weight are critical factors.
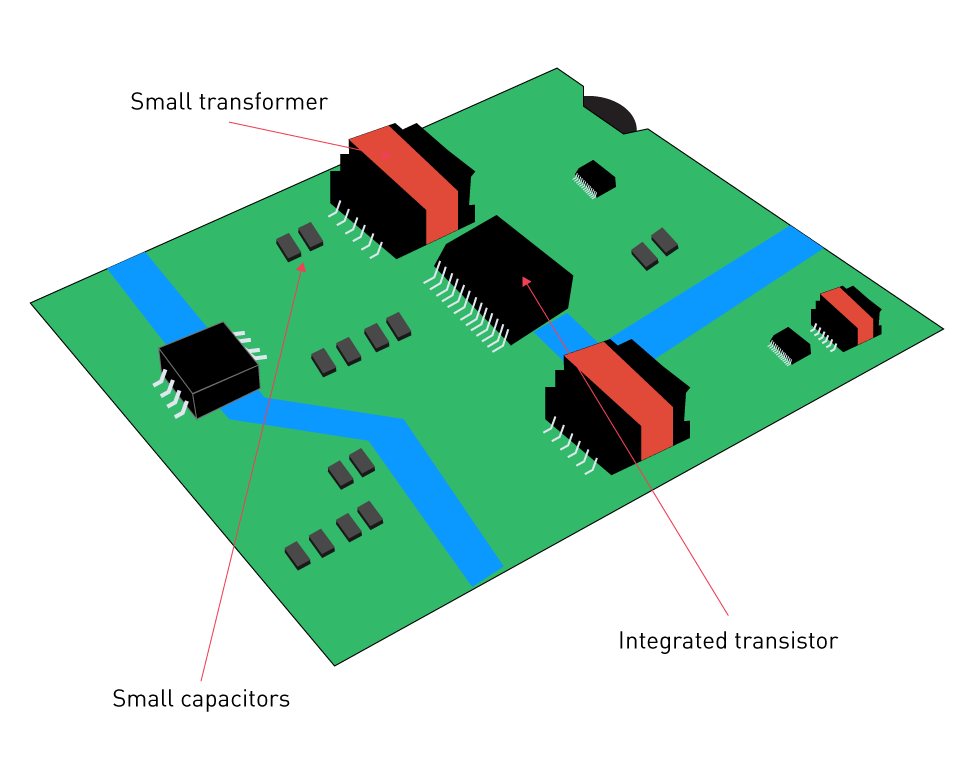
Figure 4: Compact Size and Low Weight for Power Supplies with Distributed Architecture
Challenges
Nevertheless, the distributed approach necessitates meticulous planning and design. In addition, the use of multiple power sources enhances reliability but can result in higher upfront expenses and increased complexity when compared to centralized systems.
Gate Drivers with Integrated Power Supplies
Gate Drivers with Integrated Power Supplies are a game-changer in power electronics design, especially for applications that demand small size, high efficiency, and utmost reliability in power conversion and management. This design incorporates the power supply directly into the gate driver circuit, allowing for a more seamless connection between power delivery and gate driving. This integration provides numerous advantages, such as a decrease in the number of components, increased system reliability, and enhanced power efficiency.
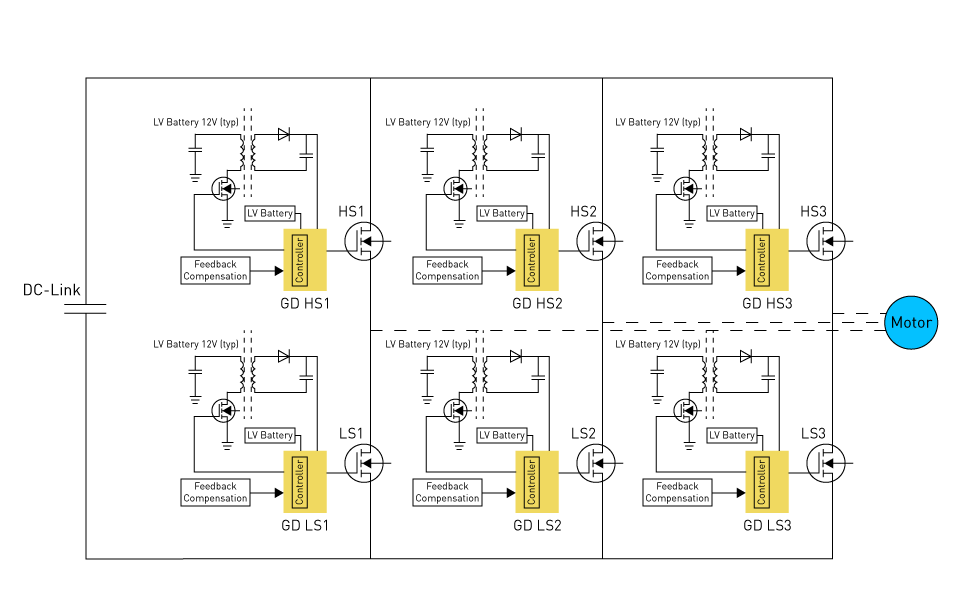
Figure 5: Gate Drivers with integrated Flyback Controller
Advantages
When it comes to isolated gate drivers, having an integrated power supply can greatly simplify the system design. This eliminates the hassle of using separate external power sources for the gate drive circuits. By reducing the physical footprint of the power electronics system, there is a simultaneous reduction in the complexity of the PCB layout. This can result in cost savings in materials and assembly. The power supply's close proximity to the gate driver circuits helps reduce power losses caused by long trace lengths, resulting in improved system efficiency.
Integrating power supplies into gate drivers is extremely beneficial in situations where space is limited and there is a need for efficient power management. In electric vehicles (EVs), aerospace, and renewable energy applications, the compact integration of power management functions with gate driving capabilities enables the development of smaller, more efficient, and more powerful electronic systems.
In addition, gate drivers with built-in power supplies are engineered to provide strong isolation between the high-voltage switching circuits and the low-voltage control electronics. This integrated isolation is essential for safeguarding delicate microcontrollers and other control circuitry from the potentially damaging high voltages and currents commonly found in power electronics applications. The design streamlines and eliminates the need for extra isolation components by incorporating isolation into the gate driver power supply. This not only improves system reliability but also enhances overall performance.
Challenges
Nevertheless, careful management of thermal issues is crucial when designing and implementing gate drivers with integrated power supplies. This is because the compact integration of power conversion components can result in higher thermal density. Designers need to utilize sophisticated thermal management techniques to maintain safe operating temperatures for integrated units. This includes implementing heat sinks, thermal vias, and convection cooling strategies.
直接登录
创建新帐号