Industrial Applications
Due to the harsh conditions and the presence of significant electrical noise, industrial environments pose unique challenges for digital isolators. It is critical to address these challenges to guarantee the efficiency and dependability of industrial systems.
Designing for Harsh Environments
Robustness Against Environmental Factors: Extreme temperatures, dust, corrosive substances, and humidity are often involved in industrial settings. In such environments, digital isolators must be robust, with enclosures designed to safeguard against these factors. Using materials capable of withstanding corrosive elements and temperature extremes is essential.
Mechanical Stress Resistance: In industrial applications, equipment can be subject to vibrations and mechanical shocks. In these settings, digital isolators need to be mechanically strong, with elements securely mounted and soldered to combat such situations.
Thermal Management: Effective thermal management solutions are mandatory for digital isolators as high temperatures are common in industrial environments. Thermal vias, heat sinks, and ensuring adequate air circulation for heat dissipation are included in this.
Enhanced Insulation and Sealing: Digital isolators should have improved insulation and sealing to safeguard against environmental contaminants such as moisture and dust. To protect the electronic elements, this may involve potting or conformal coating.
Managing Interference and Disturbances
EMI/RFI Shielding: In industrial environments, electromagnetic and radio-frequency interference are often rampant. In such settings, digital isolators must feature effective EMI/RFI shielding to prevent signal corruption. To achieve this, metal enclosures, ferrite cores on cables, and grounding techniques are required.
Surge and Transient Protection: Power surges and transient voltages, which can damage electronic components, are frequently experienced in industrial settings. To protect against these occurrences, it is necessary to incorporate surge protection devices and transient voltage suppressors in the isolation design.
Noise Filtering: To manage the high levels of electrical noise in industrial environments, implementing noise filtering techniques is crucial. Using bypass and decoupling capacitors, line filters, and differential signaling is part of this approach to improve noise immunity.
Robust Signal Isolation: In an electrically noisy environment, ensuring robust signal isolation is vital. To maintain signal integrity, this might entail selecting digital isolators with higher isolation ratings and superior common-mode transient immunity.
Medical Applications
The design of digital isolators needs strict adherence to medical device standards and strict attention to patient safety and equipment reliability in medical applications.
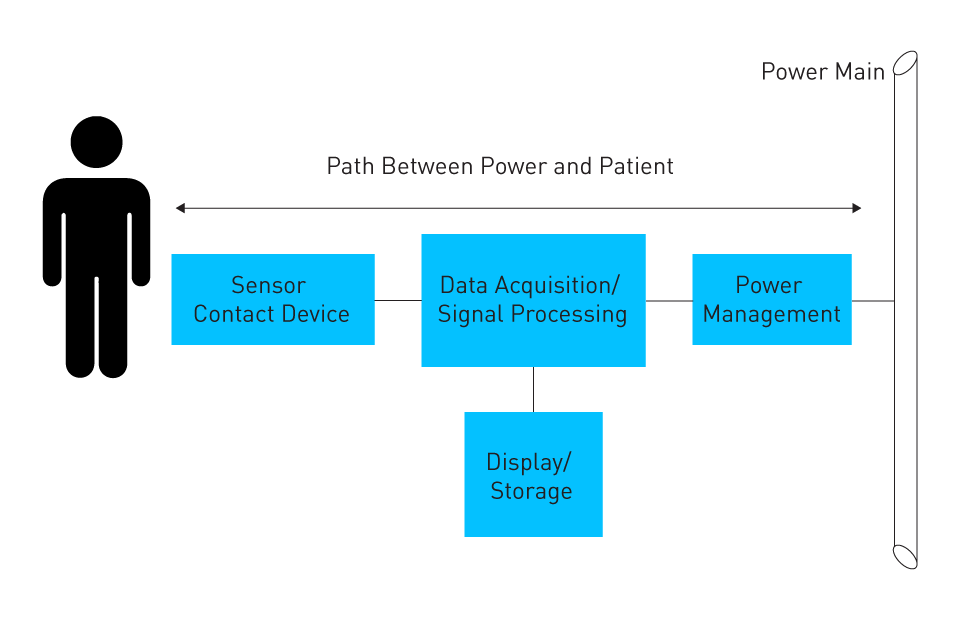
Figure 1: Isolation is Required to Break the Path between AC Mains and Patients
Ensuring Patient Safety and Equipment Reliability
High Reliability Standards: The necessity for medical equipment to possess exceptionally high reliability stems from its profound influence on patient well-being. In ensuring consistent performance, even under continuous operation, digital isolators in these applications must maintain low failure rates.
Biocompatibility and Safety: To prevent adverse reactions when in close proximity to patients, components utilized in medical devices, such as digital isolators, must adhere to biocompatibility standards. This involves the utilization of materials that are hypoallergenic and non-toxic.
Robust Isolation and Protection: Digital isolators must offer robust electrical isolation to safeguard patients from electric shocks, given the sensitive nature of medical procedures. To reduce leakage currents, this entails effective shielding and grounding along with high isolation voltage ratings.
Error Detection and Fail-Safe Mechanisms: To immediately address any malfunction, prevent potential harm to patients, and ensure the uninterrupted operation of medical equipment, it is crucial to implement error detection and fail-safe mechanisms.
Adherence to Medical Device Standards
Compliance with Regulatory Standards: Compliance with stringent regulatory standards, like those set by the FDA, International Organization for Standardization (ISO), and International Electrotechnical Commission (IEC) is necessary for digital isolators employed in medical devices. For medical electrical equipment safety, standards like IEC 60601 are included in this.
Certification Processes: Thorough testing and validation of the isolators to prove their efficacy and safety in medical applications are required to attain certification from relevant authorities. Clinical trials, quality assurance measures, and extensive documentation are frequently involved in this process.
Design for Electromagnetic Compatibility (EMC): To avert interference with other medical tools, medical equipment must fulfill stringent EMC standards. Designing digital isolators that can both combat external electromagnetic disturbances and restrict their own electromagnetic emissions is involved in this.
Traceability and Quality Control: To fulfill the high standards needed in medical applications, it is mandatory to maintain the traceability of elements and strict quality control throughout the manufacturing process. Ensuring that each digital isolator fulfills the mandatory specifications and functions reliably in a medical setting is essential.
直接登录
创建新帐号