Heat Generation and Dissipation
Efficient thermal management is crucial for maintaining the reliability and efficiency of isolated solutions. Having a grasp on the origins of heat and employing strategies to efficiently disperse it are vital aspects of this procedure.
Sources of Heat in Isolated Solutions
Electronic Component Heat Generation: During operation, electronic components are the main source of heat in isolated solutions. Electronic applications commonly use these components, especially when they need to handle significant currents or operate at high frequencies.
Losses in Power Conversion: Power conversion processes in isolators such as DC-DC converters generate heat due to inefficiencies, which can result in losses. These losses can be classified as conductive losses in the semiconductor material and switching losses during the transition of semiconductor devices between on and off states.
Thermal Runaway Risks: Some components, such as transistors and silicon diodes, can be susceptible to thermal runaway. This occurs when the temperature rises, causing an increase in resistance, which in turn raises the temperature even more in a continuous loop.
Environmental Factors: External factors in the environment such as hot temperatures and inadequate ventilation can make heat buildup worse in enclosed solutions. Compact or tightly packed areas can impede airflow, which hampers the natural cooling process.
Techniques for Effective Heat Dissipation
Heat Sinks and Thermal Pads: Heat sinks and thermal pads are frequently employed to improve heat dissipation. They enhance the surface area in contact with the air and commonly work in tandem with thermal pads or thermal paste to improve heat transfer from the component to the heat sink.
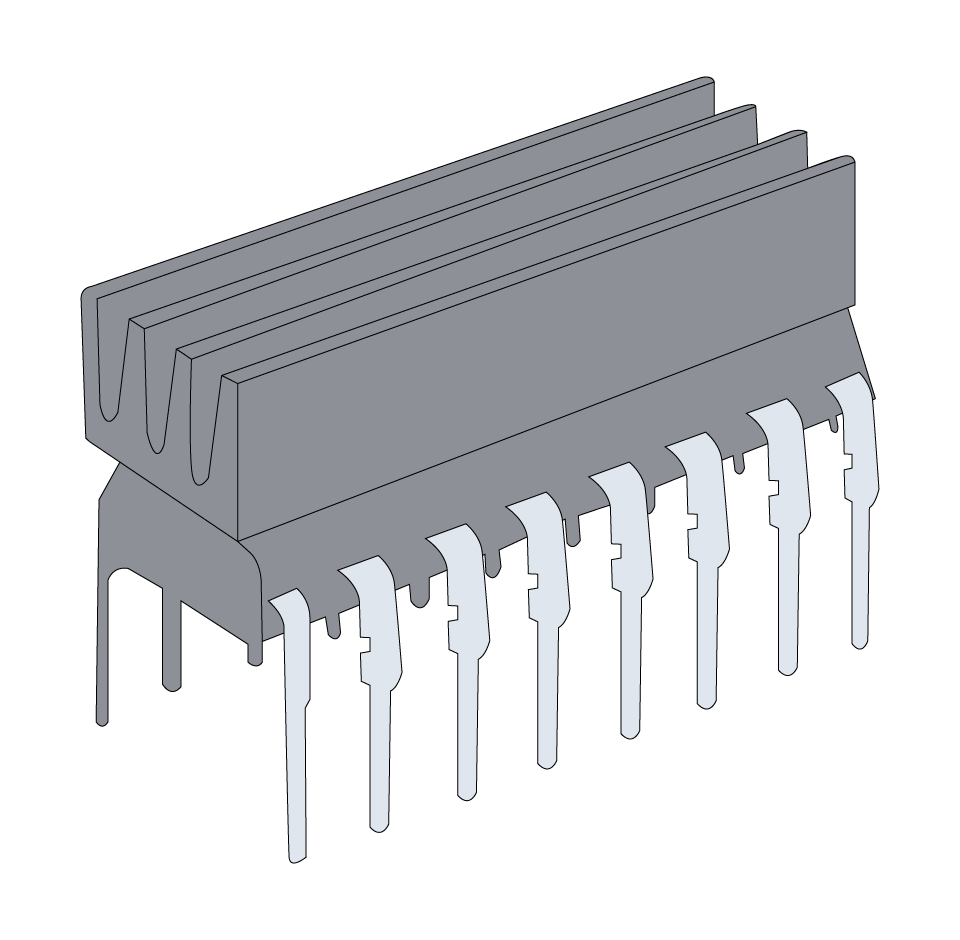
Figure 1: Integrated Circuit (IC) with Heat Sink on Top
Forced Air Cooling: When passive cooling methods such as heat sinks are not enough, one can turn to forced-air cooling options like fans or blowers. This method efficiently moves air around components, aiding in the removal of heat.
Optimized PCB Layout: The arrangement of the printed circuit board (PCB) is crucial for effective thermal management. Organizing components that generate heat in a way that promotes efficient heat flow and prevents heat concentration can help address thermal concerns.
Thermal Vias: Using thermal vias in PCB design aids in dissipating heat from areas of high temperature. These small plated-through holes in the PCB facilitate the connection between different layers, enhancing heat dissipation.
Conductive and Convective Heat Transfer Enhancement: Enhancing conductive and convective heat transfer is absolutely crucial, as it greatly impacts overall efficiency. This involves utilizing materials that have excellent thermal conductivity for PCBs and ensuring that there is sufficient spacing between components to allow for proper air circulation.
Thermal Isolation: In certain designs, it is crucial to separate certain components from others in terms of temperature, especially when there are components that are sensitive to heat or generate excessive heat.
Cooling Solutions
When it comes to managing the thermal aspects of isolated solutions, the proper implementation of cooling solutions is crucial. Having knowledge of both active and passive cooling techniques and knowing how to choose and implement them correctly is crucial for ensuring long-term functionality and durability.
Overview of Active and Passive Cooling Techniques
Passive Cooling Techniques
Passive cooling utilizes natural heat dissipation methods without relying on external energy sources. Passive cooling solutions are commonly used in various applications.
Heat Sinks: Heat sinks are metallic blocks or fins that increase surface area in contact with air, which helps to improve heat dissipation.
Conductive Plates: By evenly distributing heat across a surface, conductive plates effectively reduce the occurrence of hot spots on the PCB.
Thermal Conduction Paths: Efficiently transferring heat to cooler areas or out of the device is an important consideration when designing PCBs.
Active Cooling Techniques
Active cooling techniques focus on utilizing external energy to improve the process of heat dissipation. Some of the main active cooling methods are:
Forced Air Cooling: Utilizing fans or blowers to enhance air circulation over components that generate heat.
Liquid Cooling Systems: Utilizing coolants circulated through a system to absorb and eliminate heat, liquid cooling systems are highly effective. This method is commonly employed in applications that require significant power or density.
Thermoelectric Coolers (TECs): Thermoelectric coolers (TECs) are designed to provide targeted cooling by utilizing Peltier devices. These devices create a temperature gradient electronically, allowing for efficient cooling.
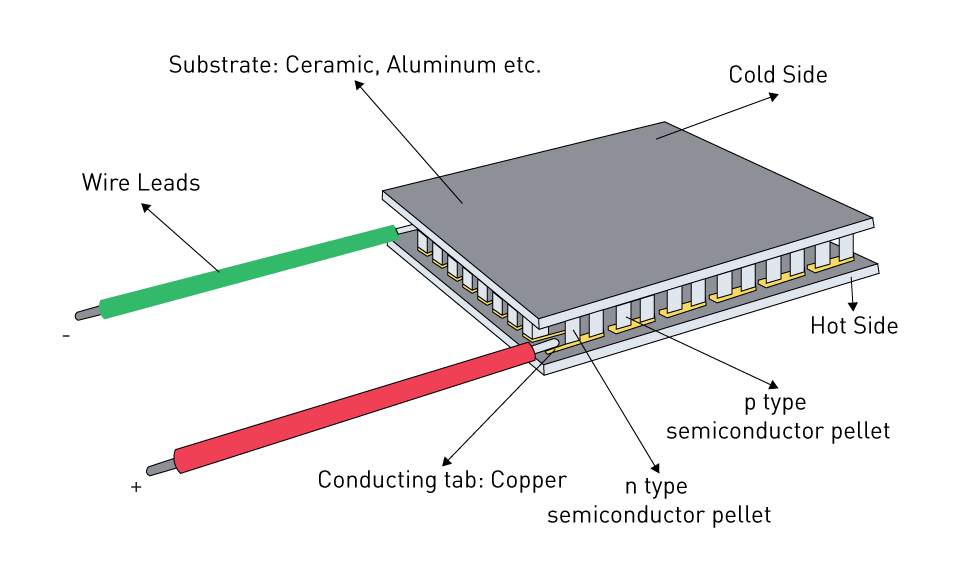
Figure 2: Thermoelectric Cooler
Selection and Implementation of Optimal Cooling Solutions
Analyzing Thermal Load: The choice of cooling solutions begins with a comprehensive evaluation of the thermal load. Understanding the heat generation characteristics of each component and the overall system under various operational conditions is crucial.
Environment Considerations: The surrounding environment is an important factor to consider when choosing a cooling solution. In environments with high ambient temperatures or limited ventilation, it is important to have cooling solutions that can handle the demands.
Space and Weight Constraints: When dealing with systems that have limited space and weight, such as in portable or aerospace applications, the effectiveness of passive cooling solutions becomes crucial. Active cooling solutions can be effective, but they often take up more space and increase the overall weight.
Noise and Energy Consumption: Concerns may arise in certain applications regarding the noise generated by fans or the increased energy consumption associated with active cooling methods. In these situations, it is crucial to focus on optimizing passive cooling or utilizing energy-efficient fans that produce minimal noise.
Integration with System Design: Seamless integration with the overall system design is crucial for cooling solutions. One must take into account the effects on airflow, mechanical stability, and other system components.
Reliability and Maintenance: Considering the longevity of cooling solutions and their maintenance requirements is crucial when choosing the right option. Passive solutions generally provide greater reliability and require less maintenance when compared to active solutions.
Monitoring and Feedback: Thermal Sensors and Shutdown Mechanisms
Monitoring and feedback mechanisms, such as thermal sensors and shutdown systems, play a crucial role in ensuring effective thermal management in isolated solutions. These technologies are essential for preventing overheating and ensuring the secure operation of electronic devices.
Thermal Sensors
Role of Thermal Sensors: Thermal sensors constantly monitor the temperature of important components or areas within a system. They offer up-to-the-minute information on thermal conditions, allowing for quick action to avoid overheating.
Types of Thermal Sensors: Different types of thermal sensors are thermistors, thermocouples, and infrared sensors. Every type has its own distinct characteristics and is suitable for various applications.
- Thermistors: Thermistors are resistors whose inheritance depends on temperature. They are commonly used due to their sensitivity and compact size, making them perfect for monitoring specific components or confined spaces.
- Thermocouples: A thermocouple is an electrical device that consists of two different electrical conductors that are connected at an electrical junction. The junction generates a voltage that varies with temperature. Thermocouples are well-suited for dynamic environments due to their wide temperature range and rapid response time.
- Infrared Sensors: Infrared sensors offer the convenience of measuring temperature without the need for physical integration into the circuit, making them ideal for monitoring the overall system temperature.
Placement Considerations: The placement of thermal sensors greatly affects their effectiveness. It is important to position them in close proximity to crucial components or areas of high temperature in order to provide an accurate representation of the system's thermal condition.
Shutdown Mechanisms
Automated Thermal Shutdown: If the temperature exceeds safe levels, the system will automatically shut down to avoid any potential damage. Usually, these systems react when temperatures exceed predetermined limits.
Integration with System Control: Thermal shutdown mechanisms are commonly incorporated into the system's control architecture. This integration enables coordinated responses to minimize power usage, fine-tune performance settings, or activate cooling mechanisms prior to a full shutdown.
Fail-Safe Design: Thermal shutdown mechanisms are meticulously designed to activate consistently, even in the event of component or system failures. This design philosophy emphasizes the importance of prioritizing system protection to ensure the safety of the system and its environment.
User Notifications and Diagnostics: These systems commonly provide notifications and diagnostic outputs, in addition to the shutdown function. These alerts notify users or maintenance personnel about thermal events, enabling quick intervention and resolution.
Redundancy and Reliability: Ensuring reliability is crucial for critical systems, which may include redundant thermal sensors and shutdown mechanisms. Having redundancy in place adds an extra layer of protection, ensuring that a single sensor or shutdown circuit failure does not lead to any issues.
Designing for Challenging Thermal Environments
Creating electronic systems that can function optimally in demanding thermal conditions, such as extreme heat or confined spaces, necessitates a meticulous approach to thermal management principles. These environments present specific challenges that need to be tackled in order to guarantee the dependability and durability of the systems.
High Ambient Temperatures
Enhanced Cooling Requirements: In environments with elevated ambient temperatures, typical cooling solutions may not be adequate. Improved cooling methods such as increasing the capacity of heat sinks or using more efficient active cooling systems might be required.
Component Selection and Rating: It is important to choose components that can handle higher operating temperatures. One important aspect to consider is selecting components that have higher temperature ratings and taking into account how high ambient temperatures can affect the performance of these components.
Thermal Margin Analysis: This is an essential step in evaluating the temperature difference between the operating temperature and the maximum rated temperature of the components. Maintaining reliability in high-temperature environments requires a strong focus on ensuring a sufficient thermal margin.
Enclosed Spaces
Airflow Management: Managing airflow can be quite challenging in enclosed or cramped spaces. Optimizing the positioning of vents, fans, or ducts can effectively enhance airflow and mitigate the formation of hot spots.
Heat Transfer Optimization: Utilizing thermal conduction techniques to efficiently transfer heat to the enclosure or an external heat sink can yield positive results. One possible approach is to utilize thermal interface materials, conductive paths, or heat pipes.
Miniaturization and Power Density: Miniaturization and maximizing power density can effectively address heat generation in confined areas. Achieving the desired outcome involves carefully managing the system's thermal and electrical needs.
General Considerations
Insulation and Isolation: In certain situations, it can be advantageous to protect sensitive components from external heat sources or separate heat-generating components. This could include the use of physical barriers, thermal insulating materials, or compartmentalization in the design.
Environmental Sealing: It is crucial to shield the system from harsh external elements such as dust, moisture, or chemicals. Sealed enclosures may be necessary, but it's crucial to consider heat dissipation during the design process.
Material Choices: The selection of materials is of utmost importance in the development of the system. Materials that have a high thermal conductivity are useful for efficiently distributing heat, while insulating materials are effective at safeguarding delicate components.
Long-Term Stability and Aging: Components in challenging thermal environments may experience faster degradation over time. Having a deep understanding of the long-term stability and aging characteristics of materials and components under thermal stress is crucial for ensuring reliable design.
Material Considerations for Thermal Management
The selection of materials is crucial in the context of thermal management for electronic systems. Material choices have a direct impact on thermal performance, affecting heat conduction, dissipation, and the overall stability of the system.
Impact of Material Choices on Thermal Performance
Conductivity and Heat Transfer: Efficient heat transfer relies on materials that have high thermal conductivity. Heat sinks and heat spreaders frequently choose copper and aluminum due to their exceptional heat conductivity.
Material Thickness and Surface Area: The thickness and surface area of materials also play a role in determining thermal performance. Thicker materials have the ability to absorb and dissipate a greater amount of heat. However, it is important to consider that they also contribute to the overall weight and size of the system. Maximizing surface area, particularly in heat sinks, improves the efficiency of heat dissipation into the surrounding environment.
Thermal Interface Materials (TIMs): Thermal Interface Materials (TIMs) are essential for enhancing the thermal contact between heat sources, such as ICs, and heat sinks. TIMs, including thermal pastes, pads, and adhesives, play a crucial role in optimizing heat transfer. They help to minimize air gaps and microscopic irregularities, which in turn lowers thermal resistance.
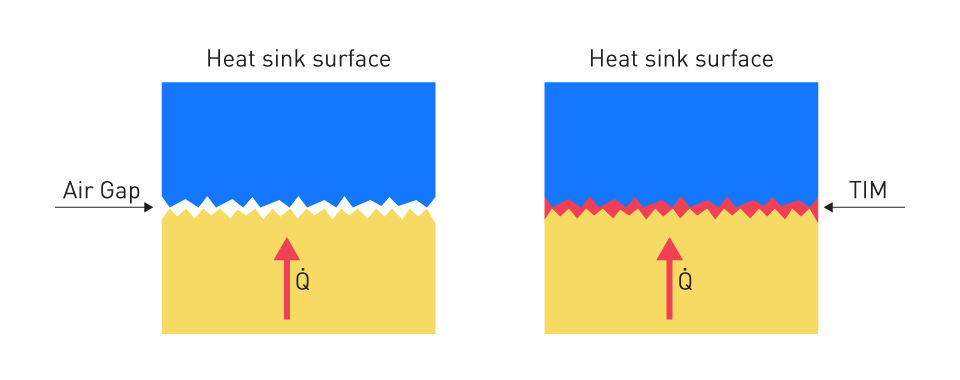
Figure 3: Direct Contact vs. using TIMs
Insulation Properties: Certain applications may necessitate the use of materials that possess excellent insulation properties in order to effectively inhibit heat transfer to vulnerable sections of the system. It is crucial to consider this aspect, especially in multi-layer PCBs and systems that have heat-sensitive components.
Selection of Materials for Enhanced Thermal Management
Performance vs. Cost: When considering performance and cost, it's important to note that certain materials, such as copper, provide superior thermal capabilities but come at a higher price. Striking the right balance between performance and cost is of utmost importance, particularly in the realm of consumer electronics, where price sensitivity plays a major role.
Weight Considerations: Weight is a crucial factor to consider in portable or aerospace applications, where the use of lightweight materials is essential. Optimal choices for materials with good thermal performance include lightweight options like aluminum or composite materials.
Environmental and Mechanical Properties: When choosing materials, it is important to consider not only their thermal properties but also their environmental and mechanical stability. These factors are important to take into account, such as the ability to resist corrosion, maintain strength, and withstand thermal cycling.
Compatibility with Manufacturing Processes: It is crucial to ensure that the selected materials align seamlessly with standard manufacturing processes without causing any unnecessary complications or expenses in the production line.
Sustainability and Regulations: It is important to consider sustainability and regulations, with a growing emphasis on using environmentally friendly materials and complying with regulations such as the Restriction of Hazardous Substances (RoHS). Choosing materials that are both efficient for thermal management and environmentally friendly is crucial.
Thermal Simulation and Analysis
Understanding heat behavior within electronic systems is essential for effective thermal management. Thermal simulation and analysis play a critical role in this process, providing valuable insights. These tools and methods are useful for predicting thermal performance and confirming the validity of thermal design choices.
Tools and Methods for Thermal Analysis
Computational Fluid Dynamics (CFD): Thermal analysis widely employs computational fluid dynamics (CFD) simulation tools. These tools simulate the flow of heat and air (or other coolants) around electronic components, offering a comprehensive view of temperature distribution and heat transfer in the system.
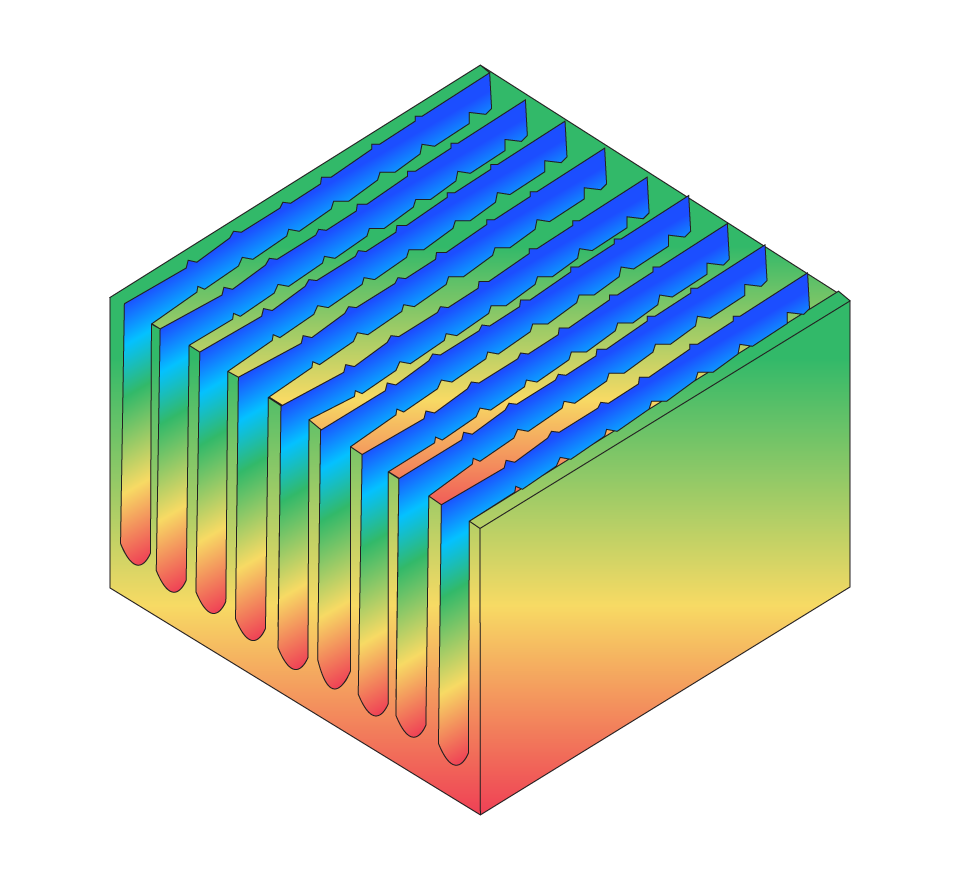
Figure 4: CFD Analysis of Heat Transfer Enhancement in a Heat Sink Design
Finite Element Analysis (FEA): Finite Element Analysis (FEA) is used to simulate and analyze thermal stresses and heat dissipation in various materials and structures. This method is extremely valuable for gaining insights into thermal behavior in intricate geometries.
Thermal Circuit Modeling: Just like electrical circuit analysis, thermal circuit modeling uses an equivalent circuit approach to represent heat flow. This method simplifies intricate thermal systems into networks of thermal resistances and capacitances.
Empirical Testing and Model Calibration: Simulations often work in tandem with real-world empirical testing to refine and validate the models. Using thermal cameras, thermocouples, or infrared thermography is necessary for measuring temperatures and validating simulation predictions.
Validation of Thermal Design through Simulation
Predicting Hot Spots and Temperature Gradients: Simulations are used to forecast regions with intense heat accumulation and variations in temperature within the system. Recognizing these areas is essential for implementing specific thermal management interventions.
Optimizing Heat Sink and Cooling System Design: Thermal simulations are instrumental in fine-tuning the design of heat sinks and cooling systems. Designers have the freedom to explore various configurations, materials, and sizes in order to achieve optimal heat dissipation.
Impact of Environmental Conditions: Simulations have the ability to accurately predict how different environmental conditions, like temperature and airflow will affect the thermal performance of a system. This is crucial for creating systems that can function dependably in various situations.
Design Iterations and Improvements: Through simulation results, designers have the opportunity to iterate and enhance their thermal designs. This process requires fine-tuning the placement of components, making adjustments to materials, or modifying the cooling architecture.
Reducing Prototyping Costs and Time: Simulation validation of thermal designs minimizes the need for extensive physical prototyping, resulting in cost and time savings. This not only helps in reducing expenses and saving time, but also allows for faster development cycles.
直接登录
创建新帐号