Introduction to Stepper Motors
Basic Concept and Operational Principles
The capacity of stepper motors, which are a type of electric motor, to transform electrical pulses into discrete mechanical movements is one of their signature characteristics. Because of this property, stepper motors are an excellent option for applications that require regulated movement since they allow for precise control of the motor's position, speed, and acceleration. In contrast to conventional alternating current (AC) and direct current (DC) motors, which rotate continuously when voltage is supplied, stepper motors move in steps. Each pulse from the controller moves the rotor a particular increment, or step, which enables direct control over the rotation angle without the requirement for feedback devices.
Stepper motors are powered by electromagnets that are organized in a circular pattern around a central rotor. This is the fundamental idea of stepper motors. It is possible for the rotor to be constructed out of a magnetically soft material (in the case of variable reluctance motors) or to incorporate permanent magnets (in the case of hybrid and permanent magnet designs). A magnetic field is produced when these electromagnets are energized in a sequential pattern. This field causes the rotor to rotate in steps, which is the desired effect. The order in which the electromagnets are triggered can be used to control the direction of movement, and the rate at which the electromagnets are powered is what determines the speed at which the rotation occurs. In the following illustration of a two-phase bipolar type motor with a simple wave stepping mode, the operating principle is demonstrated:
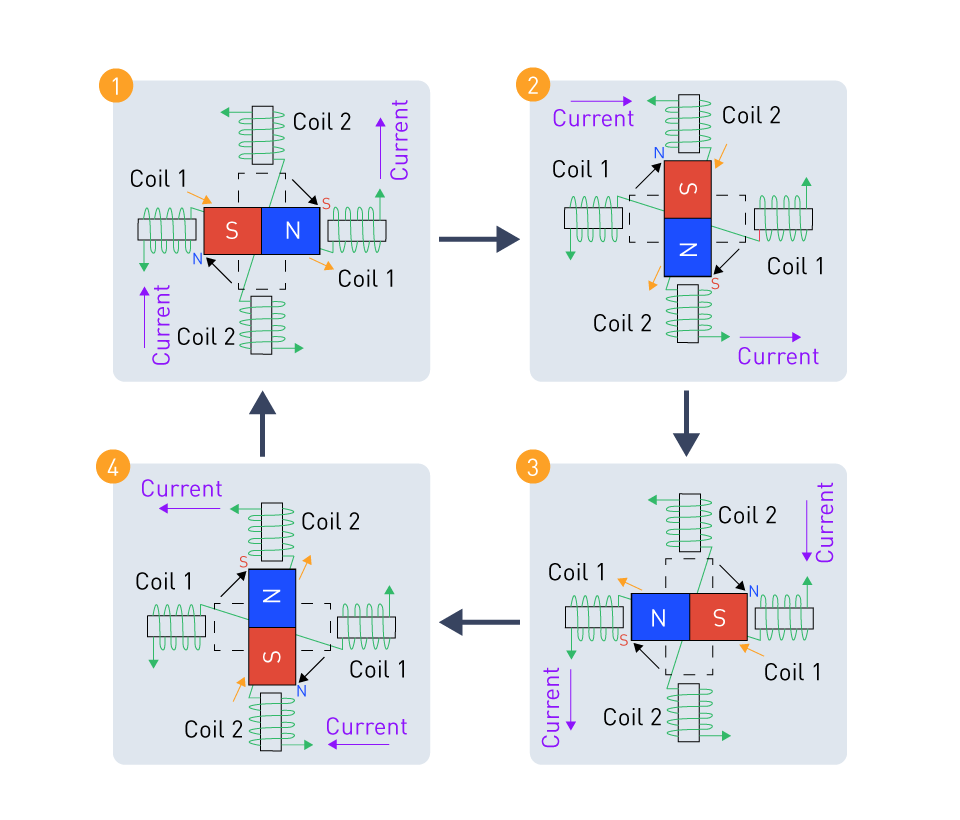
Figure 1: Basic Operation Principles of the Stepping Motor
In the illustration, we can see that the operation is broken down into four distinct parts. Coil 1 and Coil 2 are the two coils that are present. Every single coil is divided into two sections that are oriented in the opposite direction. At the beginning of the process, Coil 1 is ignited, and the flow of current will be from left to right. There is a magnetic field that is created between the two segments of Coil 1, and the permanent magnet rotor will turn in the direction of this magnetic field. This magnetic field is oriented in a particular direction, which is defined by the direction of the current. In the second stage, instead of Coil 1, the current is now passed via Coil 2, which results in the formation of a magnetic field for the rotor, which causes the rotor to revolve in the direction of the magnetic field. The third and fourth steps include repeating this operation, but this time with the currents flowing in the other direction. The four steps cover a full rotation of the rotor, and each step causes the rotor to turn through a full 90 degrees.
Historical Development and Evolution
Stepper motors have been around since the early 20th century, with substantial breakthroughs occurring in the middle of the 1900s as technology progressed to satisfy the growing demand for precise control mechanisms in areas like manufacturing, aircraft, and automation. Stepper motors have existed since the beginning of the 20th century. The introduction of digital computers and the accompanying requirement for accurate positioning in computer peripherals, such as printers and disk drives, were additional factors that contributed to the development of stepper motor technology.
The developments that have been made in materials science, magnetic theory, and electronic control systems over the course of several decades have been beneficial to stepper motors. These advancements have led to gains in efficiency, dependability, and performance. A significant improvement in the capabilities of stepper motors has been brought about by the development of controllers that are based on microprocessors. This has made it possible to implement more complex control techniques and integrate them into more complicated systems.
Stepper motors have undergone a process of evolution that has resulted in their diversification into several forms. These types include hybrid stepper motors, variable-reluctance stepper motors, and permanent magnet stepper motors. Each of these types of stepper motors has distinct advantages and is suited to specific applications. Stepper motors have become more compact, powerful, and cost-effective as a result of advancements in design and manufacturing techniques, thereby expanding the range of applications for which they may be used.
With the advancement of technology, stepper motors have become indispensable components in a wide variety of applications, ranging from robotics and precision instrumentation to consumer electronics and automotive systems. Continuous research is being conducted with the goal of improving their performance, reducing their size and energy consumption, and integrating them into developing technologies. Their capacity to give precise control in a straightforward and cost-effective manner continues to be the driving force behind their popularity and growth.
Types of Stepper Motors
Permanent Magnet, Variable Reluctance, and Hybrid Stepper Motors
Permanent Magnet (PM) Stepper Motors: PM stepper motors are characterized by the incorporation of permanent magnets within the rotor, which results in the generation of a magnetic field that is constant. The stator, which is made up of a number of windings, is electrified in a sequential manner, which either allows it to attract or repel the magnetic field of the rotor, which in turn causes it to step. Because of their strong torque at low speeds and outstanding holding torque, PM stepper motors are ideally suited for applications in which the load is maintained at a constant level.
Variable Reluctance (VR) Stepper Motors: Reluctance stepper motors, often known as VR stepper motors, are distinct from permanent magnet stepper motors in that they do not make use of permanent magnets. In its place, the rotor is constructed out of soft iron and features teeth that protrude from its surface. When the windings of the stator are electrified in a sequential manner, they magnetically attract the teeth of the rotor, which in turn causes the rotor to turn in distinct steps. This is a possibility due to the fact that the soft iron has a lower reluctance than the air that surrounds it. Because of this difference in reluctance, also known as magnetic resistance, a force is generated that causes the rotor teeth to revolve in order to align themselves in the center of the activated stator coil. This allows the magnetic field to locate the path with the lowest reluctance. Virtual reality stepper motors are chosen in applications that demand precise positioning across a wide range of speeds while requiring less torque. These motors offer better step resolutions than other types of steppers.
Hybrid Stepper Motors: Stepper Motors That Combine the Principles of PM and VR Stepper Motors Hybrid stepper motors combine the principles of PM and VR stepper motors with a rotor that contains teeth as well as permanent magnets. With this design, the magnetic route and interaction between the stator and rotor are optimized, which results in greater performance in terms of torque, efficiency, and step precision. In demanding applications that require both high torque and precise control, hybrid stepper motors are employed in a significant number of applications.
Characteristics and Suitability of Each Type
PM Stepper Motors: PM stepper motors are characterized by their robust performance at low speeds. They are therefore particularly well-suited for applications in which compact size and reliable holding torque are of the utmost importance. They perform exceptionally well in consumer electronics, automotive applications such as dashboard gauges, and small-scale automation projects where the demand for ultra-high precision is less important than the necessity for cost-effectiveness and simplicity with regard to the project.
Variable Reluctance (VR) Stepper Motors: These motors are distinguished by their outstanding precision and better step resolution, which makes them perfect for applications where complex control of movement is of the utmost importance. Because they do not contain any permanent magnets, they have a lower holding torque, which makes them the best option for applications such as high-speed scanning equipment, precise calibration instruments, and some types of printers. These are all applications in which speed and accuracy are more important than torque.
Hybrid Stepper Motors: The design of the hybrid stepper motor delivers the best of both worlds, combining strong torque with exceptional precision and efficiency. This is in contrast to the design of the conventional stepper motor. This makes them very well-suited for a wide range of industrial applications, including computer numerical control (CNC) machines, robotics, and complex automation systems, all of which have high requirements for both power and precision. They are especially suitable for specialist equipment in the field of laboratory instrumentation and medical devices because of their ability to retain performance across a wide range of speeds and loads.
直接登录
创建新帐号