Introduction to BMS in EVs
The proliferation of electrification has expanded the scope of Battery Management Systems (BMS) beyond electric automobiles, encompassing a wide spectrum of transportation modes. This includes everything from two-wheelers like bicycles and scooters to airborne drones and even the ambitious frontier of electric aircraft. While we place particular emphasis on road vehicles due to their current prevalence in this section, we also cast a spotlight on the broader landscape.
Significance of BMS in Transportation Systems
In every domain of electric transportation, the battery functions as a vital life force. Its management as a result assumes a crucial role in shaping the safety, performance, and longevity of the vehicle. More specifically:
Road Vehicles (Cars, Trucks, Bikes): In this context, the BMS serves as the primary guarantor of secure operations across diverse conditions. It optimizes vehicle performance by maintaining battery health and prolongs the battery's life by preventing overcharging, deep discharging, and exposure to extreme thermal conditions.
Drones: Aerial vehicles like drones require battery systems that are both lightweight and potent. The BMS designed for drones places a premium on weight efficiency while simultaneously guarding against the rapid discharge rates often encountered during flight.
Electric Planes: Electric aviation is an emerging frontier, and it presents challenges in weight management, high power demands, and the extremities of operating conditions. In this sphere, the BMS goes beyond mere management; it embodies innovation in battery technology itself.
Challenges Across Different Transportation Systems
Although a BMS's fundamental concepts stay constant, the particular difficulties change depending on the mode of transportation:
Diverse Operating Conditions: This is particularly true for road vehicles, which travel across environments ranging from hot deserts to freezing mountains. In these situations, BMS must manage batteries under various heat conditions.
High Power and Energy Density: These are necessary for everyone, however on different scales. Drones and aircraft need bursts of power rather than constant power, especially during takeoff.
Integration Complexity: Road cars frequently require communication between their BMS and a number of different subsystems, such as the vehicle control unit (VCU) or the thermal management system. In contrast, electric planes with avionics and drones may prioritize communication with flight control systems.
Consumer Expectations: Everyone wants devices with a greater range and faster charging times. A drone operator on the other hand could need even faster turnaround times than a car driver, who might be happy with a 30-minute rapid charge.
Safety Protocols: Different battery failures have different effects. A car fault could leave you stranded, but a drone or plane malfunction might have disastrous results. As a result, BMSs in aerial vehicles require strict safety regulations.
The significance of the BMS will only increase as electrification spreads to other modes of transportation. It serves as a showcase for engineering prowess, ensuring that we progress safely and effectively toward a cleaner future.
Integration with Vehicle Management System
The seamless integration of a Battery Management System (BMS) with the Vehicle Control Unit (VCU) is crucial as electric vehicles (EVs) continue to develop. As the brain of an EV, the VCU manages a number of systems, including the drive unit, the braking system, and others. In this situation, the BMS is crucial in notifying the VCU about the battery's health and enabling optimum vehicle performance.
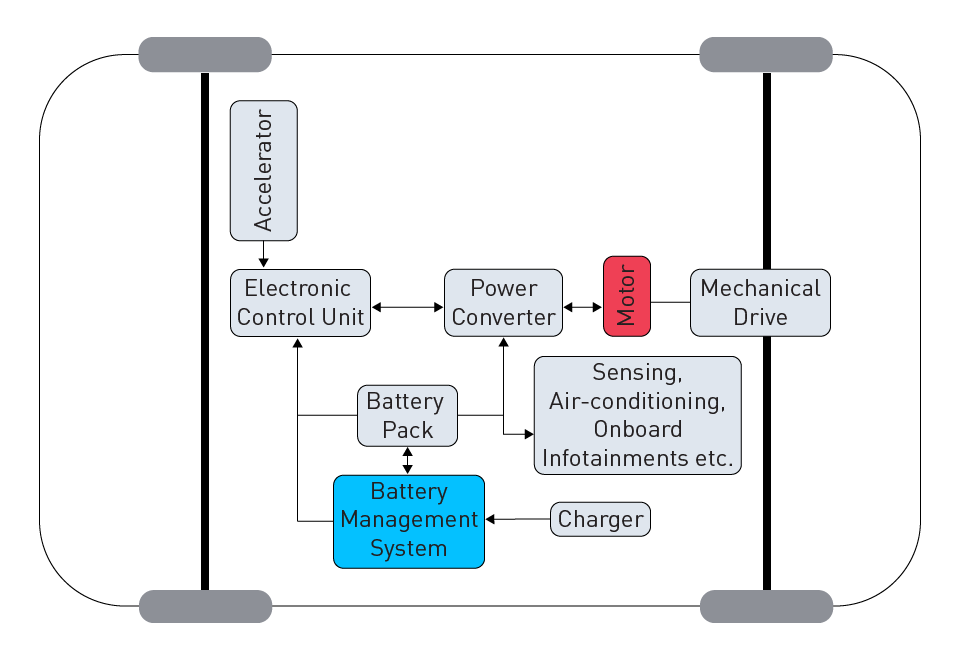
Figure 1: BMS for electric vehicle
Data Communication between BMS and Vehicle Control Unit (VCU)
The coordination between the Battery Management System (BMS) and the Vehicle Control Unit (VCU) is typically accomplished through a data communication protocol, this is mostly a Controller Area Network (CAN) or similar networking technologies. These high-speed networks are engineered to enable real-time control and facilitate data exchange among diverse vehicle subsystems.
The BMS furnishes essential data to the VCU, encompassing metrics such as the battery's state of charge (SOC), state of health (SoH), current, voltage, and temperature. Leveraging this information, the VCU makes pivotal determinations concerning available power for propulsion, regenerative braking capabilities, and when to disengage the battery for protective measures, among other considerations. Hence, ensuring effective data communication between these two systems becomes indispensable for maintaining the seamless operation of the vehicle.
Role of BMS in Vehicle Dynamics and Performance
The Battery Management System (BMS) plays a crucial role in shaping the dynamics and overall performance of an electric vehicle (EV). In one aspect, it has a significant impact on the driving range, a vital parameter for EVs. By overseeing the State of Charge (SOC) and regulating the discharge rates, the BMS can optimize the energy utilization from the battery, thereby increasing the distance the vehicle can travel.
Moreover, the BMS directly influences the vehicle's acceleration performance. It determines the safe rate at which energy can be drawn from the battery pack (power limit) based on the current battery conditions. Consequently, the BMS affects the amount of power that can be delivered to the drivetrain, which, in turn, influences the vehicle's acceleration capabilities.
During the process of regenerative braking, the BMS also plays a role in deciding the battery's charge acceptance rate. If the battery is nearing its full capacity or if the temperatures are outside the recommended range, the BMS may restrict or halt energy recovery. This limitation can impact the vehicle's braking performance and overall energy efficiency.
Thermal Management in EVs
As we take a deeper look into the intricacies of Battery Management Systems (BMS) in electric vehicles (EVs), the subject of thermal management emerges as a pivotal area of concern. The temperature of the battery is a crucial factor that not only impacts the performance of an EV but also affects the safety and longevity of the battery pack.
Importance of Temperature Control in EV Batteries
The battery cells within an EV produce heat as a result of charging and discharging, which is primarily due to the internal resistances. Excessive heat or extreme cold can however have detrimental effects on the battery's well-being. Elevated temperatures accelerate chemical reactions within the battery cells, leading to quicker degradation. Conversely, low temperatures can result in increased internal resistance and a reduction in available capacity. Thus, maintaining the battery within an optimal temperature range is of paramount importance.
In this context, the BMS assumes a critical role by monitoring the temperatures of the battery cells and implementing strategies to keep them within safe and operational limits. This proactive approach ensures optimal performance, mitigates the risk of thermal runaway (a situation where a temperature increase triggers conditions that cause further temperature elevation), and extends the overall lifespan of the battery.
Cooling Techniques and Technologies
To ensure that the battery remains within the recommended temperature range, various cooling methods and technologies have been employed.
Passive cooling, the simplest method relies on natural conduction and convection. However, it may prove inefficient for larger battery packs that generate a substantial amount of heat.
On the other hand, active cooling techniques utilize mechanical devices to disperse heat. These methods encompass air cooling, liquid cooling, and phase change material (PCM) cooling. Air cooling entails the use of fans to blow air across the battery pack, while liquid cooling involves the circulation of a coolant through tubes integrated into the battery pack. PCM cooling involves encasing battery cells within a material that absorbs heat as it undergoes a phase change.
The choice of the cooling method is contingent upon factors such as the battery's size, the type of vehicle, and specific design requirements.
Impact on Battery Performance and Lifespan
Temperature regulation plays a substantial role in influencing the performance and lifespan of an electric vehicle's (EV) battery. Excessive heat can diminish the battery's capacity, affecting the vehicle's driving range and potentially leading to hazardous situations like thermal runaways, which could result in fires. Conversely, extremely low temperatures can elevate the internal resistance of the battery cells, leading to reduced power output and slower charging rates.
Therefore, effective thermal management is not a mere auxiliary function but a fundamental necessity for the secure, efficient, and enduring operation of EVs. The Battery Management System (BMS), in conjunction with the chosen cooling methods, ensures that the battery cells maintain operation within their ideal temperature range, thus safeguarding performance and extending the battery's lifespan. Consequently, thermal management exemplifies one of the numerous pivotal roles that a BMS fulfills in ensuring the successful operation of electric vehicles.
Fast Charging Technologies
Fast charging has become a pivotal feature in promoting the widespread adoption of electric vehicles (EVs). The ability to rapidly recharge a battery's capacity can match or even surpass the convenience of refueling traditional internal combustion engine vehicles, thereby alleviating concerns about limited driving range, a significant obstacle to EV acceptance.
Introduction to Fast Charging
Fast charging refers to the capability of replenishing the charge of EV batteries in significantly reduced timeframes compared to conventional charging methods. Fast charging systems employ direct current (DC) rather than the alternating current (AC) used in standard chargers. These high-power DC chargers can deliver substantially higher currents to the battery, facilitating faster charging.
The charging rate, which determines the speed at which a battery can be charged (or discharged) without causing damage or reducing its lifespan, is often measured in "C." A charging rate of 1C indicates that the current will fully charge the battery in one hour. Fast charging typically operates at rates exceeding 1C.
Challenges in Fast Charging
Although fast charging offers appealing advantages, it presents a range of challenges. A primary concern is the heat generated during the rapid charging process. The higher the charging rate, the greater the heat produced due to increased resistive losses. Without effective cooling measures, this can lead to hazardous conditions such as thermal runaway and gradual battery degradation.
Another challenge revolves around the requirement for advanced Battery Management Systems (BMSs) capable of monitoring and regulating the fast charging process. This is necessary because the State of Charge (SOC) and the battery's health must be meticulously managed to prevent overcharging and ensure uniform charging across all cells within the battery pack.
Finally is the infrastructure challenge: fast charging demands high-power DC charging stations, which are more costly and complex to install and maintain compared to their AC counterparts. This implies that the widespread establishment of fast-charging infrastructure presents logistical and financial obstacles.
Role of BMS in Safe and Efficient Fast Charging
Fast charging relies heavily on a BMS to maintain the procedure's efficiency and safety. During charging, the BMS keeps a close eye on battery characteristics like the voltage, current, and temperature. To protect the battery, the BMS can change the charging rate or halt the operation entirely if any of these metrics go above their safe limits.
An efficient charging strategy that a BMS can use is constant current-constant voltage (CC-CV), in which the charging current is maintained until the battery reaches a particular voltage, at which point the voltage is maintained constant and the current is gradually decreased. With the use of this technique, charging speed can be maximized while heat production and battery deterioration are reduced.
Additionally, in order to negotiate the best charging current based on the battery's capacity and state-of-charge, the BMS communicates with the charging station.
BMS for Space Applications
In the realm of space exploration, batteries are essential for powering satellites, space probes, and potentially manned missions. Due to the distinctive challenges posed by the space environment, Battery Management Systems (BMSs) assume an even more crucial role in this context:
Extremes and Radiation: High amounts of cosmic and solar radiation are paired with huge temperature variations, from the cold of deep space to extreme solar heat, necessitating the use of BMSs that are both radiation and temperature-resistant.
Demanding Lifespans: Space missions, in contrast to terrestrial applications, may run for decades without maintenance, necessitating BMSs that guarantee flawless battery longevity and health over extended periods.
Operational Constraints: Passive cooling techniques used on Earth do not work in space due to the microgravity environment, which alters battery behavior. BMSs with integrated temperature systems and mechanisms capable of handling anomalies without human intervention are necessary for this.
Efficiency Imperative: BMSs must exceptionally optimize battery utilization, especially in deep space when recharging sources like sunlight are scarce.
In essence, BMSs make sure our cutting-edge space technology is fueled and protected in the great expanse as we push the bounds of exploration.
直接登录
创建新帐号