Introduction to LED Technology
In the past few decades, Light Emitting Diodes (LEDs) have seen a huge surge in their application within the automotive industry. When a voltage is applied, semiconductor diodes emit light through electroluminescence, which is the operating principle of LEDs. They are especially suitable for vehicular applications due to their small size, longevity, and efficiency.
Construction of an LED
The LED assembly typically comprises the LED chip, which is the silicon p-n junction responsible for light emission, connected via soldering to the Cathode terminal. To collect and concentrate the light in a specific location, the chip is surrounded by a reflective cavity. The anode side of the LED chip is wire-bonded to the Anode terminal of the LED to complete the circuit. Making the lens of the LED as well as protecting the structure from the environment, the internal structure is covered with epoxy or silicon.
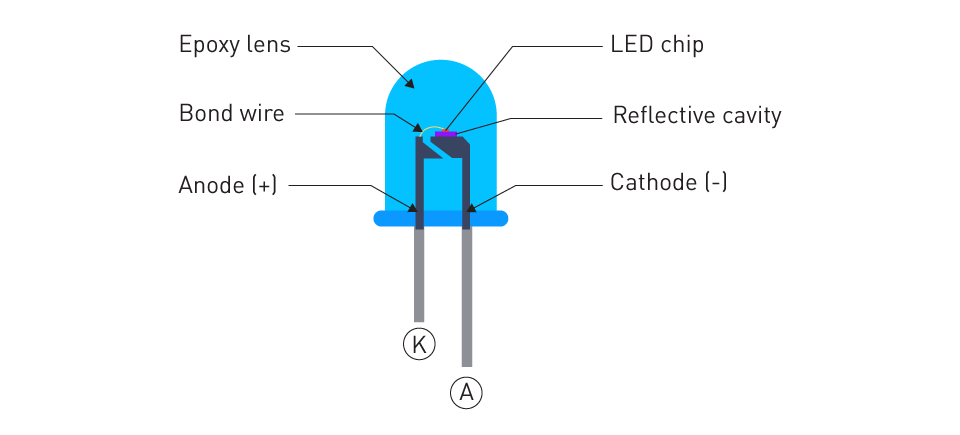
Figure 1: Construction of an LED
Working Principle
LED lights are like a p-n junction diode, with two regions in silicon. Excess electrons (negative charge carriers) are present in the n-type region, and excess holes (positive charge carriers) are in the p-type region. When the light emitting diode is forward-biased, it emits light. In the presence of a forward-biased voltage across the junction, current flows akin to any typical p-n junction scenario. Electrons originating from the n-type region and holes from the p-type region migrate towards the junction, where they undergo recombination, functioning similarly to a conventional diode and facilitating the flow of current. The working principle is very similar to a p-n junction diode. The silicon is consisting of two regions. The n-type region has electron (negative charge carrier) excess, and the p-type region that has hole (positive charge carrier) excess. The light emitting diode emits light when it is forward biased. When a voltage is applied across the junction to make it forward biased, current flows as in the case of any p-n junction. Holes from the p-type region and electrons from the n-type region enter the junction and recombine like a normal diode to enable the current to flow. As recombination is taking place, the electrons are returnin to a lower energy state called Valence band, and energy is released in the form of light.
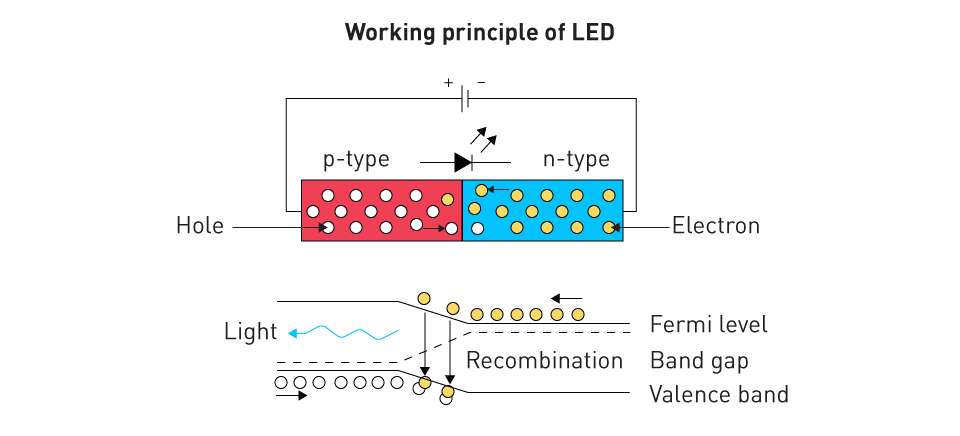
Figure 2: Working Principle of the LED
Benefits of LEDs in Automotive Applications
Efficiency: As compared to conventional lighting solutions, LEDs typically convert a higher percentage of electrical energy into light, making them more energy efficient. In the realm of vehicles, particularly electric ones, maximizing efficiency becomes paramount, emphasizing the significance of saving every watt-hour of battery power.
Longevity: Far higher than the life of halogen or HID lights, LEDs can last up to 25,000 hours or more. Such an approach diminishes the necessity for frequent replacements, resulting in both cost reductions and a decrease in waste generation.
Compactness: LEDs provide designers with more flexibility because of their small size. The advancement has opened avenues for creative and stylish automotive lighting concepts while upholding optimal performance standards.
Quick Response Time: The instantaneous illumination of LEDs proves crucial, particularly for brake lights, where even the slightest fraction of a second can impact reaction times for trailing drivers.
Durability: LEDs are solid-state lights not like filament-based bulbs. Such resilience renders them capable of enduring the jolts and vibrations commonly encountered in vehicular settings, making them more robust.
LEDs are sensitive to humidity, and this is the only drawback. Yet, through implementing sufficient measures in the casing design, this risk can be effectively eradicated.
LED vs. Halogen and HID Lighting
Halogen Lights
- Functioning: The operation of halogen bulbs involves passing an electric current through a tungsten filament enclosed within halogen gas. Assisted by the gas, the redeposition of tungsten onto the filament occurs, thereby marginally prolonging its lifespan.
- Comparison with LED: A greater amount of heat is produced by halogen bulbs than light, which makes them less efficient than LEDs. They are larger and have a shorter lifespan. Despite this, they generally come at a lower cost and have remained the conventional choice for automotive lighting over numerous years.
High-Intensity Discharge (HID) Lights
- Functioning: Due to the gas HIDs use, which generate light by producing an arc between two electrodes, it is frequently referred to as xenon lights. This arc then produces bright light because of the ignition of the xenon has and metallic salts within the bulb.
- Comparison with LED: While HID lights boast superior brightness and energy efficiency compared to halogens, they still fall short of the efficiency levels achieved by LEDs. Requiring several seconds to achieve full brightness, HID lights have a longer startup time compared to other options. As compared to both LEDs and halogens, they are usually more expensive.
To conclude, although halogen and HID lights have been strong in the automotive sector for years, the multitude of benefits offered by LEDs is rapidly establishing them as the preferred option for contemporary vehicles. Transitioning to LED technology signifies more than just a passing fad; it underscores the ongoing evolution of automotive engineering toward sustainability, efficiency, and performance.
LED Drivers
Regulating the necessary power for an LED or a group of LEDs, an LED driver serves as a self-contained power supply unit. LEDs necessitate drivers primarily due to their diode characteristics, permitting current to flow exclusively in one direction. This segment explores the essential elements of LED drivers, covering the differentiation between constant current and constant voltage drivers, their dimming mechanisms, and their functionality.
Function and Importance of LED Drivers
Unlike traditional lighting solutions, LEDs are unique in their power requirements. While incandescent bulbs autonomously regulate their current, LEDs control their current with the assistance of an external mechanism. Let’s explore the reasons why LED drivers come into the picture:
Regulating Current: The sensitivity of LEDs correlates significantly with the level of current passing through them. Minor fluctuations in current can impact their performance and lead to a substantial decrease in their lifespan. By guaranteeing a steady supply of current, LED drivers uphold uniform brightness levels and safeguard the integrity of the LED.
Protection from Voltage Fluctuations: High-voltage spikes pose a threat to the LEDs. Serving as a dedicated buffer, the driver shields the LED against potential damage caused by voltage fluctuations originating from the battery supply lines.
Optimizing Performance: Throughout their lifespan, drivers can enhance the light output of LEDs and offer advanced functionalities such as dimming capabilities.
Constant-Current vs. Constant-Voltage Drivers
The selection between constant voltage (CV) and constant current (CC) drivers hinges on the specific application of the LED:
Constant-Current (CC) Drivers: Providing a consistent current to the LED, these drivers typically achieve this by monitoring the voltage across a resistance in series with the LED string. They prove advantageous for numerous LED applications, particularly in scenarios where parallel configurations might lead to current discrepancies. CC drivers ensure uniform brightness by ensuring each LED receives a consistent current.
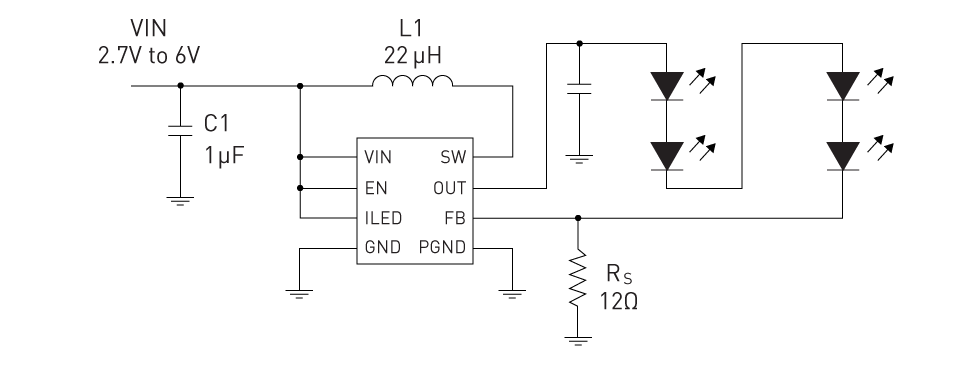
Figure 3: Simple Topology for Constant-Current Driver
Constant-Voltage (CV) Drivers: A consistent voltage is maintained by the CV drivers. Their typical usage involves scenarios where the LED's necessary current is managed directly by the LED or in setups where LEDs are interconnected in parallel, employing shunt resistors for current regulation in each branch. In strip lighting applications, CV drivers are common.
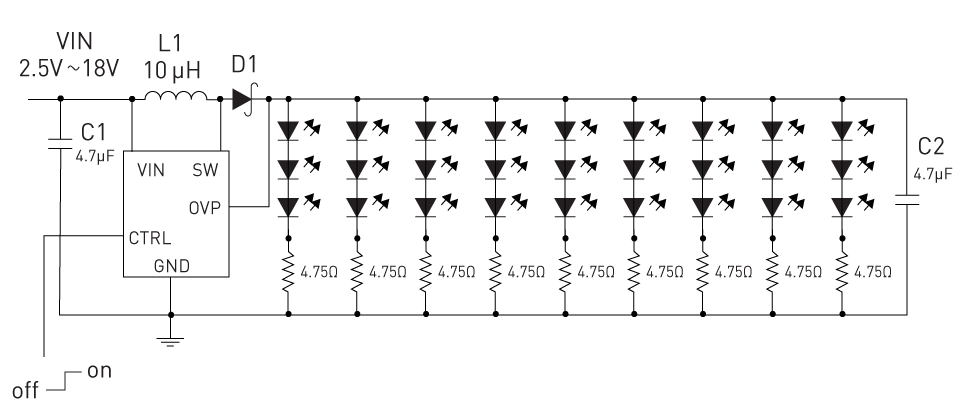
Figure 4: Simple Topology for Constant-Voltage Driver
Dimming Control for LED Drivers
Pulse-Width Modulation (PWM): This technique reduces the average current delivered to the LED which involves turning the LED on and off at a very fast rate. The brightness of the LED is determined by the duration the LED stays on. Due to its efficiency and consistent color temperature during dimming, it has become a popular method.
Analog Dimming: The continuous current flowing through the LED is reduced by this method. This method may result in color inconsistency when operating at lower brightness levels, less complex than PWM.
In the realm of LED operation, drivers serve as essential components, integral to maintaining optimal functionality and protecting against potential electrical irregularities, thereby guaranteeing consistent performance. The LED’s output and longevity are directly impacted by the appropriate dimming mechanisms along with the choice of driver, be it constant current or constant voltage.
Power Management in Lighting Systems
While considering the integration of sophisticated technologies such as LEDs, effective power management in lighting systems is of greatest importance. The subsequent section will explore these three vital aspects of power management within LED lighting systems.
Energy Efficiency Considerations
Due to growing environmental concerns and increasing energy costs, energy efficiency in lighting systems has become a prime focus. Let's examine how LED lighting systems enhance energy efficiency:
Lower Energy Consumption: As compared to conventional incandescent or halogen bulbs, LEDs, by design, consume significantly less power. This in turn contributes to lesser energy costs and a smaller carbon footprint.
Optimized Light Distribution: Unlike incandescent bulbs which radiate light (and heat) in all directions, LEDs are directional light sources, meaning they emit light in a particular direction. This guarantees efficient utilization of light in necessary areas, thereby reducing waste.
Minimal Wasted Energy: A process that produces very little heat is known as electroluminescence, which is used by LEDs to generate light. In contrast, a large amount of energy is wasted by traditional bulbs through heat.
Reliability and Lifetime Considerations
The operating conditions and power management of LED is directly influencing its reliability and longevity:
Temperature Management: The LED’s lifespan can be shortened by the prolonged exposure to high temperatures. To guarantee a longer functional life, efficient heat management is critical. A typical LED current derating curve is mentioned below. It's evident that there exists a continuous maximum permissible current (in this instance, 70mA) that must not be surpassed at any temperature. Upon reaching the threshold temperature of 60°C, the LED junction approaches its maximum allowable temperature of 100°C. Consequently, it becomes necessary to systematically decrease the load on the LED. The LED shall be turned off above 100°C ambient.
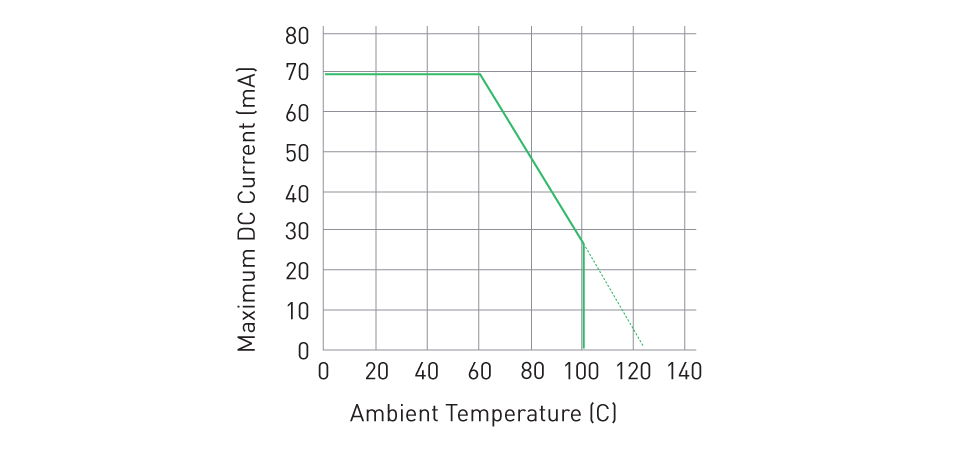
Figure 5: LED Current Derating Curve
Protection from Over-Voltage and Over-Current Conditions: The role of LED drivers is pivotal in safeguarding LEDs against potential factors contributing to premature failure, such as voltage spikes in the noisy battery supply feed or excessive current.
Robust Housing: Especially in automotive applications, the external environment can be challenging. Moisture, dust, and physical impacts pose greater risks to LEDs compared to other electronic components, particularly when the LED bulb is crafted from silicone, which exhibits higher humidity permeability than epoxy. This characteristic can result in the entrapment of moisture and other gases within, leading to corrosion of the LED's metal components. Employing durable seals and housing can effectively shield the LED from such external influences.
The performance and lifespan of LEDs are intricately tied to the efficiency of their power supply and management, despite their numerous benefits. Serving as the cornerstone of an efficient LED lighting system, energy preservation, thermal regulation, and guaranteeing a prolonged, dependable operational lifespan are all dependent on the fundamental power management strategies and technologies.
Advanced LED Technologies
In lighting technology, significant transformations have occurred, notably with sophisticated LED technologies. These advancements offer not only enhanced efficiency but also innovative applications, particularly within the automotive industry. In this regard two notable advancements are Laser Lights, and Organic Light Emitting Diodes (OLEDs), both heralding futuristic vehicle designs and improved functionality.
OLEDs in Automotive Applications
A breakthrough in lighting technology is represented by Organic Light Emitting Diodes or OLEDs. In contrast to traditional LEDs, which emit light from a single point, OLEDs serve as light sources distributed across the surface. Numerous unique benefits are offered by this distinction:
Flexible Design: OLEDs possess characteristics such as thin, light, and inherently flexible. Such attributes enable their integration into various shapes and forms, thereby unlocking innovative possibilities in vehicle design, such as bendable tail lights or intricately shaped interior lighting.
Homogeneous Illumination: OLEDs generate a uniformly luminous surface, since they are surface emitters. Enhancing aesthetic appeal and mitigating the glare commonly linked with point light sources, this feature offers notable advantages.
Layered Structures: Between two conductors, an OLED consists of numerous layers of organic compounds. A bright light is emitted when an electrical current is applied. To generate different colors and levels of brightness, these layers can be fine-tuned.
Challenges: Although holding promise, OLEDs present challenges, notably regarding their lifespan and susceptibility to moisture and oxygen. Nonetheless, ongoing research endeavors are advancing towards the development of more stable and durable OLEDs.
Laser Lights
In the realm of automotive lighting, laser lights are an emergent technology, positioning themselves as a game-changer:
Intensity and Range: Laser lights exhibit remarkable intensity, boasting a range that can nearly double that of traditional LEDs. For high-beam applications, this ensures superior visibility.
Compactness: With remarkably compact components, laser light systems offer automakers increased design flexibility and placement options.
Energy Efficiency: Despite emitting immensely bright light, laser lights demonstrate power consumption comparable to, if not lower than, LEDs.
Conversion Process: Lasers don’t directly illuminate the road in automotive applications. Rather than directly emitting light, the blue laser light is projected onto a phosphor plate. This plate subsequently emits a profoundly bright white light that is both safe and suitable for automotive lighting purposes.
Safety and Regulations: Due to their intensity, the utilization of laser lights is subject to regulatory considerations, aimed at preventing potential hazards to other road users.
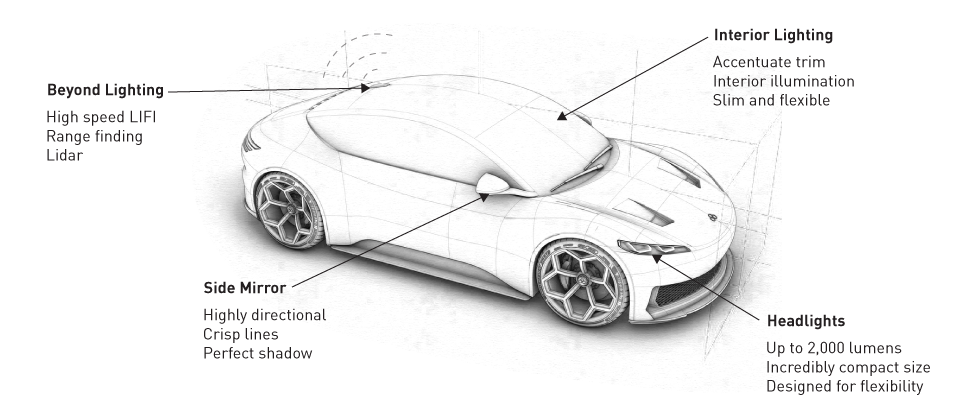
Figure 6: Different Laser Light Applications
To summarize, incorporating advanced LED technologies like OLEDs and laser lights into the automotive sector marks a significant stride toward vehicles that excel not only in aesthetics but also in functionality. With ongoing research and the maturation of these technologies, they hold the potential to revolutionize the landscape of automotive lighting, pushing the boundaries to new horizons.
直接登录
创建新帐号